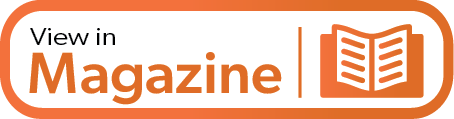

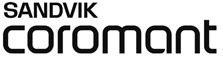
David Goulbourne, responsible for Sandvik Coromant’s solid round tools business unit, uses an interactive touchscreen presentation to introduce manufacturing wellness concepts aimed at optimizing production processes. The presentation addresses identifying bottlenecks, adopting new technology, committing to sustainability, reducing waste, improving data utilization, forming partnerships to ensure quality machining, and bolstering training with artificial intelligence.
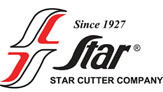
The Star Cutter Co. features the new FLX versatile five-axis tool and cutter grinder designed for high-volume production of 1" diameter tools up to 8" in length. Discover the machine’s two spindle options, including a 15-kilowatt, 20-horsepower spindle for endmill and drill manufacturing, and explore its advanced automation package. The video also highlights the TRU TECH T93XM centerless grinder, specialty tools for the automotive and medical industries, as well as custom products from H.B. Carbide.
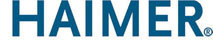
HAIMER USA’s Tod Petrik offers an exclusive tour of the company’s newest tools and technologies. In this video, he takes viewers through each featured product, sharing insights on innovations designed for precision, durability and versatility in machining applications. From the HAIMER Mill Series to the powerful Panther Mill, get an insider look at how these tools are pushing the boundaries of high-performance machining.
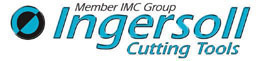
William Fiorenza from Ingersoll Cutting Tools highlights the company’s CeraSFeed silicon nitride high-feed ceramic insert launched in 2021 for applications in the aerospace, energy and medical industries. The insert efficiently machines cobalt and nickel-based materials without coolant. In addition, Fiorenza showcases Ingersoll’s IAbsorber dampening system for the Innofit product line. Ingersoll also presented its MaxSFeed series tangential milling products that feature a dovetail pocket design and expanded sizes.
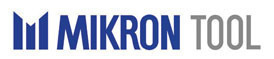
Mikron Tool, a U.S. distributor of NS Tool Co., demonstrates advanced surface finishing of a bone plate made of titanium alloy 6AL-4V using a three-flute ball endmill from NS Tool. The demo highlights high-speed operations for excellent finishes, new milling geometries and specialized tooling for medical applications. Innovative solutions also mentioned include chatterfree finishes and a new product line of through tool coolant mills for medical and firearm industries.
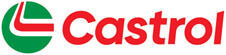
Dave Gannon, marketing manager at Castrol Industrial Solutions, introduces key members of the team: Tim Stiers, manager of technical services; Britney Palmer, key account manager; and Chasity Brewer, area sales manager. In this video, they discuss Castrol’s cutting-edge industrial solutions, focusing on the company’s advanced cutting fluids and the technical support provided by the team.
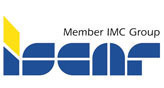
Explore the latest advancements in 3D printing technologies for cutting tools, including parting, grooving, milling, and turning tools — all featured at the Iscar booth during IMTS 2024. Innovative designs optimize coolant flow, enhancing tool life and performance. Discover versatile drilling technologies like the SUMOCHAM hole making line, and how computational fluid dynamics improves chip flow and evacuation.
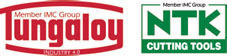
Tungaloy-NTK Chief Technical Officer Kedar Bhagath shares insights on the company’s advancements in turning technology, including its AddMultiTurn six-corner inserts for front turning, back turning, profiling and face turning. He next highlights the company’s new grooving product, the AddForceCut, which features a self-clamping design. Bhagath also discussed the company’s miniature cutting technology, ceramics innovations, and drilling solutions like its DrillMeister product.
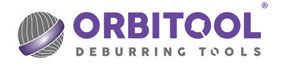
Designed for cross holes in both manual and CNC applications, Orbitool deburring tools from J.W. Done feature a flexible shank and protective disc, allowing for selective material removal at intersecting edges. J.W. Done General Manager Stanley Kroll demonstrates how Orbitool is shown to effectively deburr complex contours and surfaces, particularly for brass parts. Custom tools also are available.
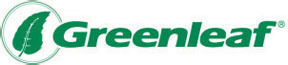
Martin Dillaman, global manager at Greenleaf Corp., presents innovative tooling solutions for hardened steel. Key highlights include the WG-600 ceramic insert, designed for high-speed, coolant-free operations, and the versatile Excelerator milling tools. Live demonstrations underscore the efficiency of ceramic inserts, cutting process times from 30 minutes to mere seconds.
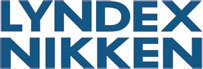
Tom Dang, vice president of Lyndex-Nikken, introduces a new workholding product aimed at improving shop throughput. The presentation highlights its zero point system, known for its compact design and high repeatability. The video also showcases reversible jaws for different workpieces and a userfriendly tombstone automation system. The insights emphasize incremental investment in automation, allowing one operator to efficiently manage multiple machines.
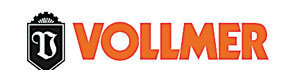
Arndt Hauger, innovation manager at Vollmer, introduces the VLaser 370 — a high-precision machine crafted for PCD tool production with a focus on the automotive and aerospace sectors. The VLaser utilizes a unique kinematic design that enables fast and efficient laser machining of complex profiles. It offers exceptional dimensional accuracy and is supported by a flexible loading system that accommodates various tool placements.
Related Glossary Terms
- ceramics
ceramics
Cutting tool materials based on aluminum oxide and silicon nitride. Ceramic tools can withstand higher cutting speeds than cemented carbide tools when machining hardened steels, cast irons and high-temperature alloys.
- computer numerical control ( CNC)
computer numerical control ( CNC)
Microprocessor-based controller dedicated to a machine tool that permits the creation or modification of parts. Programmed numerical control activates the machine’s servos and spindle drives and controls the various machining operations. See DNC, direct numerical control; NC, numerical control.
- coolant
coolant
Fluid that reduces temperature buildup at the tool/workpiece interface during machining. Normally takes the form of a liquid such as soluble or chemical mixtures (semisynthetic, synthetic) but can be pressurized air or other gas. Because of water’s ability to absorb great quantities of heat, it is widely used as a coolant and vehicle for various cutting compounds, with the water-to-compound ratio varying with the machining task. See cutting fluid; semisynthetic cutting fluid; soluble-oil cutting fluid; synthetic cutting fluid.
- endmill
endmill
Milling cutter held by its shank that cuts on its periphery and, if so configured, on its free end. Takes a variety of shapes (single- and double-end, roughing, ballnose and cup-end) and sizes (stub, medium, long and extra-long). Also comes with differing numbers of flutes.
- gang cutting ( milling)
gang cutting ( milling)
Machining with several cutters mounted on a single arbor, generally for simultaneous cutting.
- grooving
grooving
Machining grooves and shallow channels. Example: grooving ball-bearing raceways. Typically performed by tools that are capable of light cuts at high feed rates. Imparts high-quality finish.
- laser machining
laser machining
Intensified, pulsed beams of light generated by lasers—typically carbon dioxide or neodium-doped yttrium aluminum garnet (Nd:YAG)—that drill, weld, engrave, mark, slit and caseharden. Usually under CNC, often at both high cutting rates (100 linear in./sec.) and high power (5kW or more). Lasers also are used in conjunction with in-process quality-control monitoring systems allowing measuring accuracies of 0.00001".
- milling
milling
Machining operation in which metal or other material is removed by applying power to a rotating cutter. In vertical milling, the cutting tool is mounted vertically on the spindle. In horizontal milling, the cutting tool is mounted horizontally, either directly on the spindle or on an arbor. Horizontal milling is further broken down into conventional milling, where the cutter rotates opposite the direction of feed, or “up” into the workpiece; and climb milling, where the cutter rotates in the direction of feed, or “down” into the workpiece. Milling operations include plane or surface milling, endmilling, facemilling, angle milling, form milling and profiling.
- milling machine ( mill)
milling machine ( mill)
Runs endmills and arbor-mounted milling cutters. Features include a head with a spindle that drives the cutters; a column, knee and table that provide motion in the three Cartesian axes; and a base that supports the components and houses the cutting-fluid pump and reservoir. The work is mounted on the table and fed into the rotating cutter or endmill to accomplish the milling steps; vertical milling machines also feed endmills into the work by means of a spindle-mounted quill. Models range from small manual machines to big bed-type and duplex mills. All take one of three basic forms: vertical, horizontal or convertible horizontal/vertical. Vertical machines may be knee-type (the table is mounted on a knee that can be elevated) or bed-type (the table is securely supported and only moves horizontally). In general, horizontal machines are bigger and more powerful, while vertical machines are lighter but more versatile and easier to set up and operate.
- parting
parting
When used in lathe or screw-machine operations, this process separates a completed part from chuck-held or collet-fed stock by means of a very narrow, flat-end cutting, or parting, tool.
- polycrystalline diamond ( PCD)
polycrystalline diamond ( PCD)
Cutting tool material consisting of natural or synthetic diamond crystals bonded together under high pressure at elevated temperatures. PCD is available as a tip brazed to a carbide insert carrier. Used for machining nonferrous alloys and nonmetallic materials at high cutting speeds.
- profiling
profiling
Machining vertical edges of workpieces having irregular contours; normally performed with an endmill in a vertical spindle on a milling machine or with a profiler, following a pattern. See mill, milling machine.
- shank
shank
Main body of a tool; the portion of a drill or similar end-held tool that fits into a collet, chuck or similar mounting device.
- turning
turning
Workpiece is held in a chuck, mounted on a face plate or secured between centers and rotated while a cutting tool, normally a single-point tool, is fed into it along its periphery or across its end or face. Takes the form of straight turning (cutting along the periphery of the workpiece); taper turning (creating a taper); step turning (turning different-size diameters on the same work); chamfering (beveling an edge or shoulder); facing (cutting on an end); turning threads (usually external but can be internal); roughing (high-volume metal removal); and finishing (final light cuts). Performed on lathes, turning centers, chucking machines, automatic screw machines and similar machines.