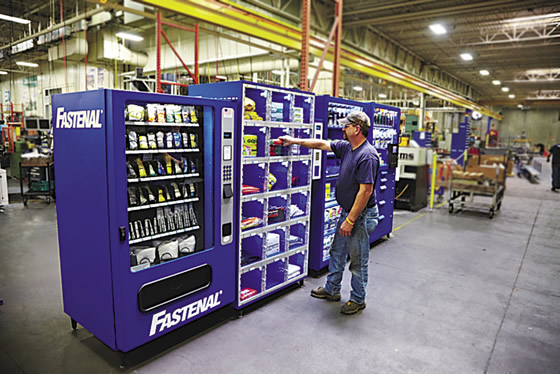
Courtesy of Fastenal
Fastenal has added a drawer unit to its FAST 10000SL series. The seven drawers have 168 total bins equipped with weight-based sensing technology.
The parts a job shop machines might be considered high industrial art—functional models of beauty—but its toolcrib can be a “messterpiece.” It’s often littered with sticky notes, cluttered with obsolete inventory and suffers from inefficiency, waste and manual, repetitive intervention without user accountability. Outside the crib, some machinists hoard cutting tools at their workstations to make sure they have an adequate supply or, in a worst-case scenario, take them to their garage shops for side jobs.
Many part manufacturers know they are working without structure and wasting money when searching for tools, according to Alexander Zoller, CEO of E. Zoller GmbH & Co. KG, Einstell- und Messgeräte, Germany, which offers TMS Tool Management Solutions. “The toolcrib is often one of the few areas where, [in many plants], no optimization has taken place so far.” (Zoller Inc., the company’s North American subsidiary, is based in Ann Arbor, Mich.)
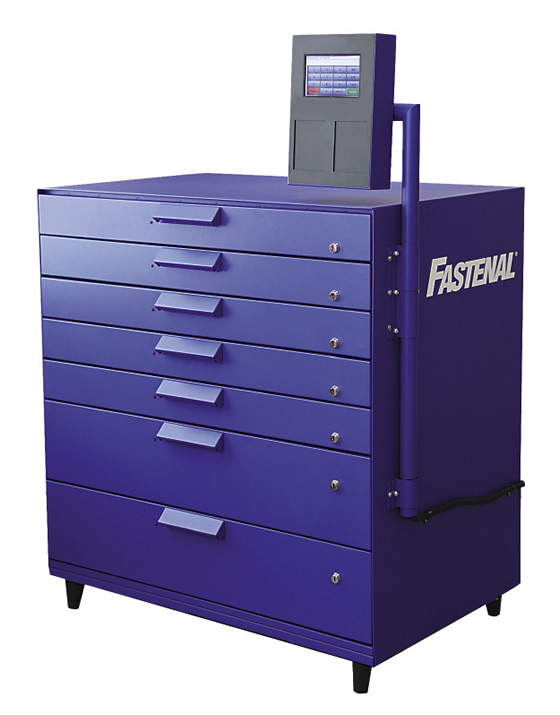
Courtesy of Fastenal
A machine shop uses Fastenal vending machines as part of its inventory management system.
An effective tool inventory management system changes that scenario, enabling part manufacturers to see what they’ve been missing. “They can see who uses a specific product and for what purpose the product is being used for, such as a job number. Then, by utilizing the usage data, customers can chose to set machine-enforced limits on the products and quantities used for further consumption reduction,” said Tim Albrecht, technology solutions manager for Fastenal. The Winona, Minn., distributor of manufacturing products provides numerous services, including toolcrib inventory and industrial vending machine management.
He added that manufacturers using the system can have the tailored information automatically e-mailed to those who need it, telling them what’s happening even if they don’t generate reports. This level of automation includes alerts to indicate when specific events occur. For example, if a vending machine contains a first-aid kit, the person in charge of safety receives a text message when someone dispenses it. “You can set up certain conditions to proactively notify [the appropriate person] when they take place,” Albrecht said.
Shops can realize benefits from an inventory management system without even taking the time to review the information that’s automatically distributed. “At the end of the day, the mere presence of the machine, and the fact that somebody has to self-identify prior to taking something, sets the tone that, ‘listen, we want everybody to be accountable,’ ” Albrecht added. “We have customers who never look at reports. All they really try to do is make people accountable and reduce waste.”
Crib Crawl
The process of creating an effective tool management system begins with an assessment of an end user’s inventory management needs to find opportunities for improvement, often focusing on the top 20 percent of the most critical tooling at a facility. “It’s not just about putting a vending machine into a customer’s facility,” said Bill Welch, director of vending systems for MSC Industrial Supply Co., Wood Dale, Ill. “When we go through an assessment, we’re looking at every aspect of our customer’s supply chain to understand how we can help our customer apply a solution that will have the greatest impact.”
Next, Welch emphasized the importance of collaborating with customers to understand which cutting tools and related tooling are being used and which ones are the most critical to their production operations. “We work closely with them to develop the key information we need to help them put an inventory management solution in place and make it successful,” he said, adding that the information includes item descriptions and access privileges.
In addition, it’s critical that manufacturers view inventory management as an extension of their supply chain and buinsess. “It’s not just a service somebody else is providing them,” Welch said, noting that they must integrate it into their day-to-day operations.
Another equally important element, according to Welch, is that shops should work with a partner that understands cutting tools and employs experienced machinists to help optimize tool utilization beyond just managing inventory.
After conducting an on-site evaluation to determine an end user’s requirement. Zoller recommends a tool management system to optimize the workflow of tools and other toolcrib resources during their life cycles, which can be expanded. When selecting the specific modules available in tool management software, he emphasized the need to consider if a system can expand as business needs change.
In addition, Zoller noted the company’s system queries remaining life from the machine tools, generates tool demand for the next shift and communicates with tool dispensing systems to deliver information about needed tools. “The presetting and inspection machine is working on the same database and knows which tools have to be measured next,” Zoller said. “And the measurement itself is only a click of a button, after which tool data is be transferred to the machine tools.”
Time to Save
Once in place, a tool management system starts to realize savings for the parts manufacturer, with the biggest savings being time. In the TMS system, “CAM programmers don’t have to search for or draw tools,” Zoller said. “They just query the database and start working. Toolcrib employees don’t have to search for tools anymore. Instead, they get displays of where to go and their lift and cabinet systems are triggered to automatically check out tools.” The database also includes other items that would have previously required searches, such as fixtures, gages and NC programs.
Because many inventory management systems are near the point of use, time is saved by minimizing the number of footsteps to get a tool even when its location is known. A machinist no longer has to walk through a manufacturing facility to go to the toolcrib and collect a tool, MSC’s Welch said.
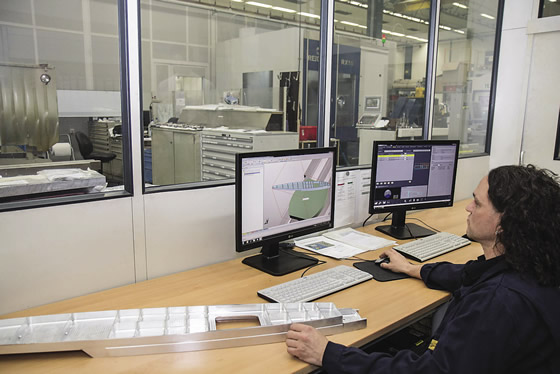
Courtesy of Zoller
With Zoller TMS Tool Management Solutions, consistent cutting tool data travels from the CAM system to the machine tool.
In addition, money is saved by reducing product consumption. According to Fastenal’s Albrecht, it’s not uncommon for usage to drop 30 percent over time when a manufacturer implements inventory management with vending machines. If hoarding has already taken place, he said Fastenal frequently sees little immediate usage because operators are consuming tools out of their individual stockpiles.
Manufacturers also save money by streamlining the purchasing process. It might cost $60 to $80 to cut a purchase order at a large manufacturer, for instance, and a tool management system provides a predictable inventory with minimum and maximum levels that the distributor monitors electronically, Albrecht said. “Rather than having an emergency purchase, we keep the machines full and customers are getting an invoice for whatever we bring out in a given timeframe.”
Albrecht emphasized, however, that although tool management systems reduce consumption, it’s in distributors’ long-term interest to implement these systems. “This is not an investment for us in next month’s sales,” he said. “It’s an investment in the relationship, which in turn builds loyalty back to us in terms of driving cost savings. People are looking for partners who can help with that versus just supplying products.”
Focus on Optimization
After a manufacturer begins generating data for cutting tool optimization, this data enables the manufacturer and distributor to focus their efforts on reducing costs in areas that generate the biggest impact.
“Am I improving a process that will ultimately affect the total cost of the part versus attacking areas that aren’t going to provide much benefit?” Welch asked, adding that it’s important to discern whether an issue is related to tooling or something else, such as workpiece material, fixturing or the machine. “[Tool optimization] data gives you a clear path to understanding where to focus your improvement efforts to get the most out of them. The control and visibility you get starts to improve the way you apply your efforts.”
According to Welch, tool consumption information spotlights trends and enables data analysis so manufacturers can make sound business decisions and identify opportunities for improvement. “We can break that consumption data down so the customer can start to analyze it, turn it into action and drill into tool consumption by department, by job and by user, and paint a pathway for improvement.”
One action an inventory management system won’t generate is the elimination of toolcrib jobs. “We’re helping them manage their time to work on the things that aren’t repetitive,” Albrecht said. “We’re really looking for the high-transaction cutting tools, where the shop goes down if they run out of them. We’ve got that visibility built into our replenishment model to make sure we always have product on the shelf for them.”
Welch concurred that establishing a system allows toolcrib personnel to focus their energy on more value-added tasks rather than chasing a stock outage or going off-site for a needed item. “We see it as a complement to what a toolcrib management team does,” he said.
With a suite of solutions, including an e-commerce platform and vendor-managed inventory utilizing personnel at a customer’s site, an effective tool inventory management system doesn’t necessarily involve vending machines at MSC. “We place a significant amount of vending machines but we tend to look at it more from a business needs’ analysis, then apply the best solution,” Welch said.
Ultimately, end users want to save money and enhance efficiency and product utilization with a tool management system. “If we can put something in to alleviate costs and increase the visibility of products and what they’re using them for,” Albrecht said, “we certainly have an incentive to make that work.” CTE
Flexible technology for safe flying
A modern airplane is complex. The safety of passengers depends on its parts functioning without error, as does the cost effectiveness of an airline’s operations. This dependability is accomplished with technology onboard the plane—and behind the scenes.
Lufthansa Technik AG understands that expandable and flexible manufacturing systems and transparent manufacturing data are essential when producing high-quality parts for its commercial and government jet aircraft. More than 1,000 employees are involved in the business unit at the Lufthansa hangar in Hamburg, Germany.
A pool of about 2,000 different, complete tools is available for machining the parts, which have prismatic and free-form surfaces. Lufthansa Technik programs the elaborate NC programs for the parts’ complex geometries with Edgecam CAM software and uses the >>venturion 450<< CNC tool setting and measuring machine from Zoller. Lufthansa selected the Zoller machine after conducting a cost/benefit analysis, according to the company’s Planning Engineer Frank Pieterwas. “Decisive for us was the expandability and linking to the machine tools.”
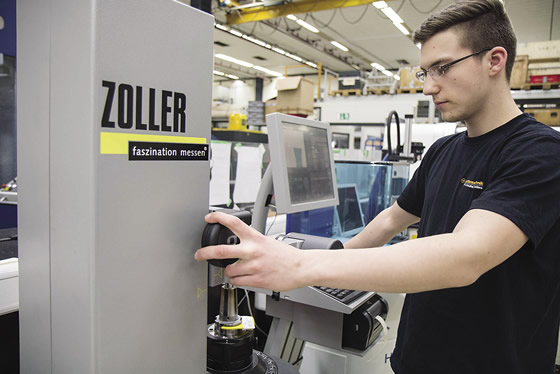
Courtesy of Zoller
Lufthansa Technik uses a Zoller >>venturion 450<< tool presetting and measuring machine (top photo) in connection with producing an array of components (below).
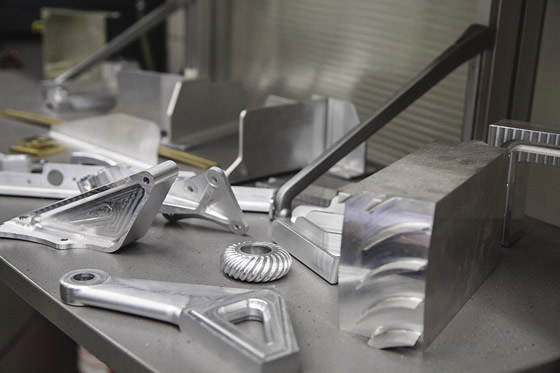
In addition to the potential of introducing a tool database that’s superimposed on the company’s machining system, application details favored the Zoller unit when Lufthansa compared machines from different vendors, said Jan Horn, CAM specialist at Lufthansa. “The graphic user interface for the otherwise laborious presetting of fine drilling tools, for example, or the fact that I can clearly view the cutting edge with the magnifying glass [are key advantages of the Zoller machine].”
However, the distribution of data from Edgecam to the Zoller system to the machine control resulted in redundant data management. This led to increased inefficiencies and contained potential error sources because of the need to manually reenter data.
As a result, Lufthansa added the Zoller TMS Tool Management Solutions system. “If a new tool is set up, it should be entered into the Zoller tool management database, so the name is correct, as well as the description and the magazine place number,” Horn said. “Thus, once entered, it can be consistently found and used by all employees in a standardized manner throughout the entire manufacturing process.”
With the interface from Edgecam to TMS already established, Lufthansa linked the tool memory of the CNC machines and the Zoller presetting and measuring machine via the Zoller database. This ensured data consistency from the CAM system to the machine tool. All data is saved in TMS and accessed by the CAM system. The measuring requirements are saved in the database directly next to the tool and are available on the measuring machine. Measurements are made at the push of a button and the tool data is transferred to a machine tool to ensure consistency and eliminate manual-entry errors and redundant tool data.
The tool data is available in the CAM system as a 3D model. The system then programs using real data and outputs the data of tools on which machining simulation was performed. These tools can be assembled on the machine in the same way they were simulated.
After the first 6 months of operation with the tool management system, errors were significantly reduced. “Everyone downloads their NC programs into the machine; the tools are included and have standardized descriptions,” Horn explained. “I use a single set of tool data. Once I have written a program in Edgecam, it applies to all machines. All I do is change the post-processor, send the NC program and the process is completed.”
Contributors
Fastenal
(877) 507-7555
www.fastenal.com
Lufthansa Technik AG
+49 40 5070-2524
www.lufthansa-technik.com
MSC Industrial Supply Co.
(800) 521-9520
www.mscdirect.com
Zoller Inc.
(734) 332-4851
www.zoller-usa.com
Related Glossary Terms
- arbor
arbor
Shaft used for rotary support in machining applications. In grinding, the spindle for mounting the wheel; in milling and other cutting operations, the shaft for mounting the cutter.
- computer numerical control ( CNC)
computer numerical control ( CNC)
Microprocessor-based controller dedicated to a machine tool that permits the creation or modification of parts. Programmed numerical control activates the machine’s servos and spindle drives and controls the various machining operations. See DNC, direct numerical control; NC, numerical control.
- computer-aided manufacturing ( CAM)
computer-aided manufacturing ( CAM)
Use of computers to control machining and manufacturing processes.
- numerical control ( NC)
numerical control ( NC)
Any controlled equipment that allows an operator to program its movement by entering a series of coded numbers and symbols. See CNC, computer numerical control; DNC, direct numerical control.