Courtesy of Tru-Cut Saw
A TiCN-coated cermet-tipped saw from Tru-Cut Saw.
Production and application of cermet-tipped circular saw blades continues to grow, eating into carbide’s market share.
Cermet is well established in metalworking—the first cermet patent was issued in 1930. However, many shops aren’t fully aware of the cutting tool material’s advantages compared to carbide when circular sawing metal, especially low-carbon steel. That’s changing, however, as more U.S. saw makers introduce cermet-tipped saws and end users learn about cermet saws’ long life and their ability to achieve a high level of squareness and impart a fine surface finish while providing high process reliability, abrasion and oxidation resistance, chemical stability and high hardness at high temperature.
Cermet is a composite material composed of ceramics, such as titanium carbide, titanium nitride and titanium carbonitride, and metals, such as molybdenum carbide and tungsten carbide, which are bonded with cobalt and nickel. Cermet is usually recognized as an intermediate material between cemented carbide and ceramic. “The recipe is unique to each manufacturer,” said Chris Mckenna, product manager for Ceratizit (Mamer) Luxembourg S.àr.l., a manufacturer of cermet and tungsten-carbide saw teeth and metalcutting tools.
Around a decade ago, cermet circular saws were developed in Japan, where manufacturers produced a thin-kerf, disposable design and collaborated with Japanese saw machine builders to enhance and control cutting performance. “To this day, Japanese manufacturers continue to innovate in this field with new materials and designs,” Mckenna said, “but with many new producers now entering this interesting and demanding application segment.”
Although Japanese-made cermet saws still dominate the market, U.S. saw makers have not sat on the sidelines since then as cermet saws’ market share continues to grow. “The cermet saws are replacing carbide saws and are able to run on the same machines,” said Warren Caltabiano, carbide division manager for Vollmer of America Corp., Carnegie, Pa., a builder of grinding machines, including ones designed for grinding cermet saw tips.
Grinding Cermet
According to Richard Otter, vice president of sales for Tru-Cut Saw Inc./ICO Surface Coatings Inc., the Brunswick, Ohio-based saw manufacturer and tool coating services provider noticed a need for a U.S. manufacturer of cermet-tipped saws in the late ’90s when U.S. forging companies were installing Japanese sawing machines to cut steel bars for automakers and indicated they could only buy cermet circular saw blades from Japanese suppliers. Entry into the market, however, isn’t for the faint of heart—or the budget minded.
“We had to invest over $2 million in research and development on this project with the installation of new grinding equipment and inspection stations just to produce cermet-tipped saws,” Otter said. “Our R&D team worked from 1998 to 2000 to achieve a product equal to the Japanese-style ‘throwaway’ saw to compete with them in the marketplace.”
Tru-Cut produces a standard line of cermet saws from 250mm to 630mm in diameter with 50 to 240 teeth and kerf thicknesses from 1.5mm to 3.2mm for automatic sawing machines manufactured by Tsune, Nishijimax, Amada, Kasto, Kaltenbach and Hydromat, and can make specials for cutting ferrous and nonferrous materials on any type of circular sawing equipment. “The maximum cermet-tipped saw that we can produce at this time is 1,250mm in diameter,” Otter said, but noted that the higher cost of cermet saws compared to carbide ones severely limits demand for ones larger than 630mm in diameter.
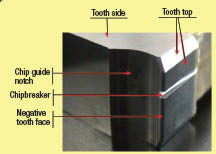
Courtesy of Vollmer
The cutting edge geometries of a cermet tip.
A cermet saw costs about 30 percent more than a comparable carbide one, according to Jim Holland, vice president of Pro-Mark Sales Ltd., Eastlake, Ohio, a distributor of saws, sawing machines and related products and a provider of cut-off sawing services. “But if I get 50 percent more blade life,” he added, “it’s a savings.”
Cermet costs more because it is harder than carbide and therefore requires grinding with diamond wheels at reduced parameters to avoid generating microcracks in the cermet. “Cermet inserts are very brittle, so we must slow our grinding process by 30 percent compared to grinding carbide inserts,” Otter said, adding that the high price of grinding wheels, coolant and cermet inserts also increases the cost.
Pasan Wanigarathne, technical director for The M. K. Morse Co., concurred that grinding cermet is challenging and said it takes 50 to 100 percent longer to grind a cermet saw with the same number of teeth as a carbide variety. The Canton, Ohio, saw blade manufacturer began offering cermet saws about 2 years ago, starting with Revolution, a 360mm disposable thin-kerf saw blade.
In addition, the tolerances are tighter for thin-kerf, ferrous-cutting cermet and carbide saw blades than for a traditional carbide saw blade, which is typically wider. Aaron Overstreet, sharpening specialist for Tsune America LLC, Columbus, Ind., noted that the Japan-headquartered company holds tighter than a 0.001 " tolerance for its thin-kerf blades whereas the tolerance for traditional carbide saws is greater than 0.002 ". (Tsune is one of the rare companies that manufactures cutting tools and builds machine tools.)
Tsune charges the same price for its cermet and carbide saws regardless of whether the customer has a Tsune sawing machine. About 80 percent of the saws Tsune makes for its machines are cermet with the remainder being carbide, so the company has significant economies of scale, according to Mike Riebl, managing partner for Tsune America.
Fine Filtration
Overstreet emphasized the importance of properly filtering the grinding oil when producing cermet wheels because of cermet’s lower density compared to carbide, which causes cermet fines to float in the oil and takes longer to filter. “We recommend around 1-micron filtration,” he said.
Mckenna pointed out that a conventional carbide grade has a density of 14 to 15 g/cm3 vs. cermet’s 6 to 7 g/cm3 range. “If you recycle the fine particles through the process, you tend to load them back onto the grinding wheel and get a problem with heat buildup,” he said, noting that 2- to 3-micron filtration of grinding sludge particles is typical.
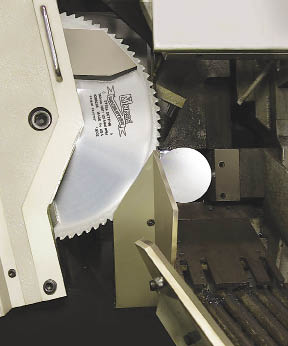
Courtesy of M.K. Morse
M.K. Morse’s Revolution cermet-tipped saw cuts a solid steel bar.
To prevent the wheel, which is usually a specialized resin-bond wheel that has an increased 240- to 300-mesh size, from becoming clogged, proper wheel dressing is critical. An element in cermet’s composition makes it more susceptible to clogging. “Nickel, when it gets hot, gets very sticky, and that nickel tends to smear between the wheel’s diamond particles,” Mckenna said. “Then, the diamond is not free cutting.” That means the wheel is rubbing more than grinding, causing friction that generates heat that, in turn, produces microcracking.
Mckenna added that to minimize the risk of microcracking and the amount of grinding after a saw maker brazes cermet tips to the saw body—which must be rigid, extremely flat and well tensioned—the tips are pressed to a near-net shape. “There is still quite a lot of grinding,” he said. Mckenna noted that to minimize heat when brazing, special braze alloys are used, sometimes with a high-silver content, with a lower melt temperature of 670° to 690° C.
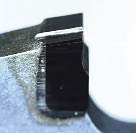
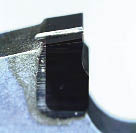
Courtesy of Tsune
A cermet tip (left) and a carbide one show geometric similarities and differences.
Tip Top
Minimizing the amount of heat when creating the edge preparation on a cermet tip also benefits saw life. Rather than using a diamond or other type of brush to generate a hone and increase edge strength, Mckenna recommends waterjetting it. “It takes a bit longer, but it gives a very uniform radius,” he said, suggesting a 0.5μm to 1.5μm edge hone.
Other tip geometries play significant roles and are determined by a host of factors, including type of machine, sawing parameters, coolant application and the type of workpiece material. Using a special diamond wheel for grinding cermet to create the geometries, a cermet saw’s basic tooth angles are the triple-chip grind, the alternate top bevel grind and the notch grind, according to Otter. The triple-chip grind has a high tooth called a raker tooth, which is 0.006 " to 0.015 " higher than the low tooth, and has 45° bevels that help the tooth cut through metal. The ATB grind, which is for cutting thin-wall tubing, has 45° bevels on every other tooth, but the tops are ground equal. The tops are also ground equal on the notch grind, but they have a chipbreaker on the tooth face. The latter is suitable for sawing solid bars or tubing. “The notch grind is for high-performance machines running at high speeds and feeds,” he said. “For the most part, the angles stay the same whether the customer is cutting with a carbide- or cermet-inserted saw blade.”
Workpiece Considerations
Similar to how nickel bonds to a diamond wheel when grinding cermet, cermet has an affinity for nickel in workpiece materials. That causes nickel to bond to cermet teeth, causing tooth galling and reducing tool life when sawing stainless steel and nickel-base superalloys. “When cutting stainless, we recommend using a carbide-tipped blade rather than a cermet-tipped blade,” said Tsune’s Overstreet.
According to M.K. Morse’s Wanigarathne, however, cermet material advances have made sawing stainless with cermet more appropriate. Those advances include reducing the material’s grain size, improving the saw blade manufacturing process and changing the material’s properties by adding tantalum, molybdenum and other alloying elements. “People thought at the beginning that machining stainless steel was not a suitable application for cermet, but now you can do it,” he said.
On the other hand, a cermet saw is highly suitable for cutting low-carbon steel. “The customer will see optimal cutting life when sawing carbon and alloy steels with less than 0.40 percent carbon content,” Tru-Cut Saw’s Otter said.
A cermet saw lasts about twice as long as a carbide one for those applications, according to Tsune’s Riebl. “If somebody cuts 1018 steel, we say use a cermet blade.” However, he noted that carbide is a better choice when there’s interrupted cuts, such as when sawing tubing.
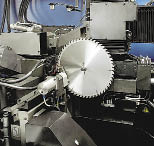
Courtesy of Vollmer
A cermet-tipped saw is ground in a Vollmer CHF 270 dual-side grinding machine.
Regardless of the type of workpiece material, it needs to be firmly clamped when sawing to eliminate vibration and avoid chipping the cermet. For example, Pro-Mark Sales’ Holland indicated that the Amada CM-100 circular sawing machine the company uses for its cermet saw cutoff services clamps the workpiece from both sides and has a vertical clamp that comes down from the top onto the material being cut. In addition, the machine provides a large guide for both sides of a blade.
“When you have a thin-kerf blade, you must have a nice guide system so there’s no flexing in that blade whatsoever,” Holland said. That helps ensure a high level of squareness in the cut.
Time for a Change
As a saw blade starts to wear, the cut will begin to lose squareness and the blade imparts a rougher surface finish. Some end users determine when a blade is near the end of its life based on a machine’s ammeter reading or the number of square inches it has cut, but Holland said he uses sight, touch and sound to know when it’s time to switch blades. “It will start to spark a little, the parts won’t be as cool and will start to feel warm to the touch and there will be a deeper sound with a bit of a grumble as the blade is on its last legs,” he explained.
As previously noted, a cermet-tipped blade was initially intended to be thrown away at the end of its life, and end users, typically at high-volume, automated operations, run the blades until they’re basically destroyed. “But being very expensive, the end user searched for a means to have them resharpened, so that’s where the market is going now,” Vollmer’s Caltabiano said. “The problem is, typically, the end user runs the bejeebers out of the saws till they won’t cut anymore and then they’ve damaged them, so they’re hard to resharpen.”
Edward A. Bissell, president of Union Grove (N.C.) Saw & Knife Inc., a cermet saw resharpener that does light manufacturing of cermet tips, concurred that end users often use cermet saws too long before sharpening them. “That really cuts down on the overall life of the blade,” he said. “If they would remove that blade before it gets spent, then they could get more sharpenings and the blade would hold its tension and level a lot better.”
To know when a blade needs resharpening and avoid costly unscheduled blade changes, Bissell recommends monitoring the quality of the blade’s cutting performance. Union Grove Saw & Knife primarily resharpens 100-tooth, 460mm-dia. blades with a 2.7mm kerf.
As long as a cermet saw’s teeth aren’t chipped, cracked or missing, the blade can usually be resharpened twice. “When it starts cracking, you’ll definitely know it,” Bissell said. “It doesn’t decrease life; it usually stops life.”
Bissell noted that, depending on the application, a cermet saw that’s resharpened once or twice can have a run time as long as a new blade. “The new cost is $300 to $500 where resharpening is from $60 to $95,” he said.
According to Overstreet at Tsune, which resharpens its own blades as well as competitors’, a resharpened blade has 80 to 90 percent the life of a new one. Tsune charges $1.50 per tooth for resharpening. Riebl noted that the cost of a new blade depends on its diameter and number of teeth, whereas the cost of resharpening only depends on the number of teeth. “The sharpening cost changes with the diameter from 50 to 20 percent,” he said. “Therefore, the economics of sharpening 250mm-dia. blades is very different than sharpening blades 500mm to 600mm in diameter.”
A thin-kerf cermet or carbide saw also takes longer to resharpen than a traditional carbide one. Including the time to resharpen the teeth and inspect them under a microscope to be sure the geometries are correct and symmetrical so out-of-square cutting does not occur, Tsune spends 90 minutes to service a thin-kerf blade—twice the time it takes for a traditional carbide blade, according to Riebl.
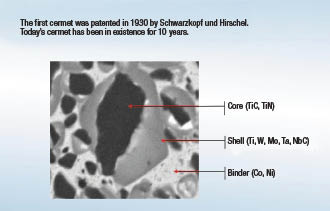
Courtesy of Vollmer
Cermet’s microstructure showing a core of titanium carbide and titanium nitride, a shell of titanium carbide, tungsten carbide, molybdenum carbide, tantalum carbide and niobium carbide and a cobalt and nickel binder.
Others feel cermet saws remain a purely disposable tool. “We participate only in the disposable market with our thin-kerf blades,” said Kevin Burgess, director of engineering for M.K. Morse. “We don’t recommend that people resharpen them. This is because typical use of these blades causes damage to the tips and plates, which can go undetected and ultimately damage the work and machine. In addition, the level of precision required to make these blades cannot easily be replicated at a typical resharpening shop, such as matching the same cermet grade.”
Tru-Cut Saw’s Otter agrees. “Metalcutting cermet saws are intended to run until the operator feels he is not getting the surface finish required or the saw is cutting out of tolerance,” he said. “It is best to pull the saw before you have a complete failure as this reduces damage to your machine. Cermet saws are called ‘throwaway saws’ for this reason. After the operator changes the blade, it is best to put the used blade in the scrap bin.”
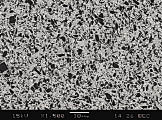
Courtesy of Ceratizit
A photomicrograph of cermet.
Otter added that after the initial use, the cermet has small hairline cracks caused by the heat created during sawing, and regrinding the blade would not remove those cracks and may cause harm to the operator or machine. The alternative is to replace all the cermet inserts, which likely would cost more than buying new and can cause another problem. “When you apply heat to cermet inserts to remove them, the steel plate looses its tension and causes the saw blade to cut out of tolerance,” he said.
However, if an end user does want to resharpen them, Otter instructed that a resharpening service must have rigid grinding machines, apply wheels and grinding oil designed for cermet, have the equipment, such as a high-magnification camera, to inspect for hairline cracks before and after sharpening and tension and straighten blades before and after servicing them.
To Coat or Not
After Union Grove Saw resharpens a cermet saw, it sends the blade to a coating facility where a diamond-like carbon coating is deposited. That’s the case regardless of whether it was coated when new. “We always coat after resharpening,” Bissell said, adding that about a third of the new saws are coated.
In addition to DLC, coatings include aluminum titanium nitride, titanium nitride and titanium carbonitride, which Tru-Cut Saw determined was the most appropriate coating for its cermet grade, Otter noted.
Similar to the dispose vs. resharpen debate, some manufacturers say a cermet saw already contains the components most coating manufacturers deposit to create a hard, protective shell around carbide tools. “You don’t need a coating,” Ceratizit’s Mckenna said. “I don’t know of any major producers that put coatings on cermets.”
Cermet is tough enough and hard enough without a coating, according to M.K. Morse’s Wanigarathne. “If you coat it, you can get some advantage for a small period of time, but after that it’s going to work as a normal [uncoated] cermet blade,” he said.
That’s because aggressiveness of the sawing operations removes the coating on the cutting edge in the early stages of saw life, and the wear rate of most coatings are similar to the wear rate of cermets. Therefore, a coating on a cermet tip’s flank delays the onset of flank wear, which is the main failure mode for cermet saw blades, according to Wanigarathne. “My experience with cermet blades shows nothing to a 30 percent improvement in blade life with a coating,” he said, adding that secondary advantages of a coating include imparting a finer surface finish, enhancing chip flow, reducing heat effects on cermet and possibly increasing the production rate.
One aspect of cermet saws everyone agrees upon is that their share of the saw market is growing, driven by demand for fine surface finishes and reduced material removal. “Cermet’s share is increasing, for sure, but it’s nowhere near the volume of carbide,” Mckenna said. “There will always be a need for carbide saws, particularly for stainless steel.”
Bissell estimated that cermet has 10 to 15 percent of the saw blade market, but that’s rapidly changing. “I bet cermet will take 50 to 75 percent of the market in 5 years because of its unique properties,” he said. “The overall life of the cermet tool is where the huge gains are.”
Switching to cermet provides gains to blade manufacturers as well. “In carbides, you find a high percentage of cobalt and this can cause problems for saw blade manufacturers when it leaches out of the insert,” Otter said. “This alone can be a good reason for saw blade manufacturers to look at manufacturing saw blades with cermet instead of carbide.” CTE
About the Author: Alan Richter is editor of Cutting Tool Engineering, having joined the publication in 2000. Contact him at (847) 714-0175 or [email protected].

Courtesy of L.S. Starrett
Proper coolant mixture and flow maximizes bandsaw blade life.
Preventive maintenance is paramount for a bandsaw
Similar to other sawing methods, when preventive maintenance for a bandsaw is at an optimal level, sawing and blade performance tend to consistently mirror a similar high level. Presented here is a 15-point checklist that covers the gamut of practical machine care. • Condition and adjustment of band guides. If the guides are worn or loose, the result will be misaligned cuts and blade failure. Properly adjust the guides to the machine manufacturer’s recommendations and repair or replace them if needed.
• Band wheel and bearing conditions. Worn flanges and out-of-round wheels can cause blade stress, which in turn creates blade failure and poor cuts. Contact the machine manufacturer for service and replacement guidelines.
• Blade tension. Low tension speeds blade wear, while excessive tension not only can cause blade failure but can also damage the machine. Always tension the blade according to the manufacturer’s specifications.
• Blade alignment. Improper blade alignment to the vise or bed leads to blade fatigue and out-of-spec, crooked cuts. Square and adjust the blade to align it with the machine.
• Feed and speed calibration. Once the blade is properly guided, it is imperative that the feed and speed of the blade and saw are calculated to the manufacturer’s recommendations. This optimizes blade and—ultimately—machine performance.
• Hydraulic and transmission oil level. Proper levels ensure consistent feed rates and longer machine life. Fill to the proper level with the manufacturer’s recommended oils.
• Coolant quality, condition and flow. Proper coolant mixture and flow extend blade life and improves productivity.
• Belts and drives. Loose or worn drive belts can slip or break, resulting in reduced blade performance and loss of production. Be sure to tighten drive belts properly and check for wear.
• Guide arms in proper position and secured. Loose or improper guide arm position can result in misaligned cuts, increased guide wear and reduced blade life. Adjust the guide arms as close as possible to the material being cut.
• Calibrate work height and slow approach controls. Proper operation increases production and blade life. Inaccurate calibration can lead to blade damage and possibly injure the operator. Consult the machine recommendations or obtain the proper settings from the manufacturer.
• Lubrication. Use lubrication to ensure longer machine life and reduce downtime for repairs.
• Safety switches. They must be working properly to ensure operator safety and prevent possible damage to the machine.
• Sufficient vise holding. Parts must be held securely to prevent vibration and movement.
• Blade tracking and proper rotation. Improper blade tracking can shorten blade life. Rotation should be checked to make sure the blade is running in the proper direction, and adjust band wheels for proper blade tracking.
• Blade and wheel brushes. Brushes help remove chips from the blade to prevent them from re-entering the cut. Missing, worn or improperly adjusted brushes reduce blade performance and should be replaced or repaired as needed. —The L.S. Starrett Co.
Contributors
Ceratizit USA Inc.
(800) 783-2280
www.ceratizit.com
The L.S. Starrett Co.
(978) 249-3551
www.starrett.com
The M.K. Morse Co.
(330) 453-8187
www.mkmorse.com
Pro-Mark Sales Ltd.
(440) 602-7184
www.pmsaw.com
Tru-Cut Saw Inc./ ICO Surface Coatings Inc.
(330) 225-4090
www.trucutsaw.com & www.icosurfacecoatings.com
Tsune America LLC
(800) 264-5290
www.tsuneamerica.com
Union Grove Saw & Knife Inc.
(704) 539-4442
www.sawandknife.com
Vollmer of America Corp.
(412) 278-0655
www.vollmer-us.com
Related Glossary Terms
- alloy steels
alloy steels
Steel containing specified quantities of alloying elements (other than carbon and the commonly accepted amounts of manganese, sulfur and phosphorus) added to cause changes in the metal’s mechanical and/or physical properties. Principal alloying elements are nickel, chromium, molybdenum and silicon. Some grades of alloy steels contain one or more of these elements: vanadium, boron, lead and copper.
- alloys
alloys
Substances having metallic properties and being composed of two or more chemical elements of which at least one is a metal.
- bandsaw
bandsaw
Machine that utilizes an endless band, normally with serrated teeth, for cutoff or contour sawing. See saw, sawing machine.
- bandsaw blade ( band)
bandsaw blade ( band)
Endless band, normally with serrated teeth, that serves as the cutting tool for cutoff or contour band machines.
- bandsaw blade ( band)2
bandsaw blade ( band)
Endless band, normally with serrated teeth, that serves as the cutting tool for cutoff or contour band machines.
- calibration
calibration
Checking measuring instruments and devices against a master set to ensure that, over time, they have remained dimensionally stable and nominally accurate.
- ceramics
ceramics
Cutting tool materials based on aluminum oxide and silicon nitride. Ceramic tools can withstand higher cutting speeds than cemented carbide tools when machining hardened steels, cast irons and high-temperature alloys.
- cermets
cermets
Cutting tool materials based mostly on titanium carbonitride with nickel and/or cobalt binder. Cermets are characterized by high wear resistance due to their chemical and thermal stability. Cermets are able to hold a sharp edge at high cutting speeds and temperatures, which results in exceptional surface finish when machining most types of steels.
- chipbreaker
chipbreaker
Groove or other tool geometry that breaks chips into small fragments as they come off the workpiece. Designed to prevent chips from becoming so long that they are difficult to control, catch in turning parts and cause safety problems.
- circular saw
circular saw
Cutoff machine utilizing a circular blade with serrated teeth. See saw, sawing machine.
- coolant
coolant
Fluid that reduces temperature buildup at the tool/workpiece interface during machining. Normally takes the form of a liquid such as soluble or chemical mixtures (semisynthetic, synthetic) but can be pressurized air or other gas. Because of water’s ability to absorb great quantities of heat, it is widely used as a coolant and vehicle for various cutting compounds, with the water-to-compound ratio varying with the machining task. See cutting fluid; semisynthetic cutting fluid; soluble-oil cutting fluid; synthetic cutting fluid.
- cutoff
cutoff
Step that prepares a slug, blank or other workpiece for machining or other processing by separating it from the original stock. Performed on lathes, chucking machines, automatic screw machines and other turning machines. Also performed on milling machines, machining centers with slitting saws and sawing machines with cold (circular) saws, hacksaws, bandsaws or abrasive cutoff saws. See saw, sawing machine; turning.
- dressing
dressing
Removal of undesirable materials from “loaded” grinding wheels using a single- or multi-point diamond or other tool. The process also exposes unused, sharp abrasive points. See loading; truing.
- edge preparation
edge preparation
Conditioning of the cutting edge, such as a honing or chamfering, to make it stronger and less susceptible to chipping. A chamfer is a bevel on the tool’s cutting edge; the angle is measured from the cutting face downward and generally varies from 25° to 45°. Honing is the process of rounding or blunting the cutting edge with abrasives, either manually or mechanically.
- fatigue
fatigue
Phenomenon leading to fracture under repeated or fluctuating stresses having a maximum value less than the tensile strength of the material. Fatigue fractures are progressive, beginning as minute cracks that grow under the action of the fluctuating stress.
- feed
feed
Rate of change of position of the tool as a whole, relative to the workpiece while cutting.
- flank wear
flank wear
Reduction in clearance on the tool’s flank caused by contact with the workpiece. Ultimately causes tool failure.
- flat ( screw flat)
flat ( screw flat)
Flat surface machined into the shank of a cutting tool for enhanced holding of the tool.
- galling
galling
Condition whereby excessive friction between high spots results in localized welding with subsequent spalling and further roughening of the rubbing surface(s) of one or both of two mating parts.
- grinding
grinding
Machining operation in which material is removed from the workpiece by a powered abrasive wheel, stone, belt, paste, sheet, compound, slurry, etc. Takes various forms: surface grinding (creates flat and/or squared surfaces); cylindrical grinding (for external cylindrical and tapered shapes, fillets, undercuts, etc.); centerless grinding; chamfering; thread and form grinding; tool and cutter grinding; offhand grinding; lapping and polishing (grinding with extremely fine grits to create ultrasmooth surfaces); honing; and disc grinding.
- grinding machine
grinding machine
Powers a grinding wheel or other abrasive tool for the purpose of removing metal and finishing workpieces to close tolerances. Provides smooth, square, parallel and accurate workpiece surfaces. When ultrasmooth surfaces and finishes on the order of microns are required, lapping and honing machines (precision grinders that run abrasives with extremely fine, uniform grits) are used. In its “finishing” role, the grinder is perhaps the most widely used machine tool. Various styles are available: bench and pedestal grinders for sharpening lathe bits and drills; surface grinders for producing square, parallel, smooth and accurate parts; cylindrical and centerless grinders; center-hole grinders; form grinders; facemill and endmill grinders; gear-cutting grinders; jig grinders; abrasive belt (backstand, swing-frame, belt-roll) grinders; tool and cutter grinders for sharpening and resharpening cutting tools; carbide grinders; hand-held die grinders; and abrasive cutoff saws.
- grinding wheel
grinding wheel
Wheel formed from abrasive material mixed in a suitable matrix. Takes a variety of shapes but falls into two basic categories: one that cuts on its periphery, as in reciprocating grinding, and one that cuts on its side or face, as in tool and cutter grinding.
- hardness
hardness
Hardness is a measure of the resistance of a material to surface indentation or abrasion. There is no absolute scale for hardness. In order to express hardness quantitatively, each type of test has its own scale, which defines hardness. Indentation hardness obtained through static methods is measured by Brinell, Rockwell, Vickers and Knoop tests. Hardness without indentation is measured by a dynamic method, known as the Scleroscope test.
- kerf
kerf
Width of cut left after a blade or tool makes a pass.
- metalcutting ( material cutting)
metalcutting ( material cutting)
Any machining process used to part metal or other material or give a workpiece a new configuration. Conventionally applies to machining operations in which a cutting tool mechanically removes material in the form of chips; applies to any process in which metal or material is removed to create new shapes. See metalforming.
- microstructure
microstructure
Structure of a metal as revealed by microscopic examination of the etched surface of a polished specimen.
- sawing
sawing
Machining operation in which a powered machine, usually equipped with a blade having milled or ground teeth, is used to part material (cutoff) or give it a new shape (contour bandsawing, band machining). Four basic types of sawing operations are: hacksawing (power or manual operation in which the blade moves back and forth through the work, cutting on one of the strokes); cold or circular sawing (a rotating, circular, toothed blade parts the material much as a workshop table saw or radial-arm saw cuts wood); bandsawing (a flexible, toothed blade rides on wheels under tension and is guided through the work); and abrasive sawing (abrasive points attached to a fiber or metal backing part stock, could be considered a grinding operation).
- sawing machine ( saw)
sawing machine ( saw)
Machine designed to use a serrated-tooth blade to cut metal or other material. Comes in a wide variety of styles but takes one of four basic forms: hacksaw (a simple, rugged machine that uses a reciprocating motion to part metal or other material); cold or circular saw (powers a circular blade that cuts structural materials); bandsaw (runs an endless band; the two basic types are cutoff and contour band machines, which cut intricate contours and shapes); and abrasive cutoff saw (similar in appearance to the cold saw, but uses an abrasive disc that rotates at high speeds rather than a blade with serrated teeth).
- sawing machine ( saw)2
sawing machine ( saw)
Machine designed to use a serrated-tooth blade to cut metal or other material. Comes in a wide variety of styles but takes one of four basic forms: hacksaw (a simple, rugged machine that uses a reciprocating motion to part metal or other material); cold or circular saw (powers a circular blade that cuts structural materials); bandsaw (runs an endless band; the two basic types are cutoff and contour band machines, which cut intricate contours and shapes); and abrasive cutoff saw (similar in appearance to the cold saw, but uses an abrasive disc that rotates at high speeds rather than a blade with serrated teeth).
- superalloys
superalloys
Tough, difficult-to-machine alloys; includes Hastelloy, Inconel and Monel. Many are nickel-base metals.
- titanium carbide ( TiC)
titanium carbide ( TiC)
Extremely hard material added to tungsten carbide to reduce cratering and built-up edge. Also used as a tool coating. See coated tools.
- titanium carbonitride ( TiCN)
titanium carbonitride ( TiCN)
Often used as a tool coating. See coated tools.
- titanium nitride ( TiN)
titanium nitride ( TiN)
Added to titanium-carbide tooling to permit machining of hard metals at high speeds. Also used as a tool coating. See coated tools.
- tolerance
tolerance
Minimum and maximum amount a workpiece dimension is allowed to vary from a set standard and still be acceptable.
- tungsten carbide ( WC)
tungsten carbide ( WC)
Intermetallic compound consisting of equal parts, by atomic weight, of tungsten and carbon. Sometimes tungsten carbide is used in reference to the cemented tungsten carbide material with cobalt added and/or with titanium carbide or tantalum carbide added. Thus, the tungsten carbide may be used to refer to pure tungsten carbide as well as co-bonded tungsten carbide, which may or may not contain added titanium carbide and/or tantalum carbide.