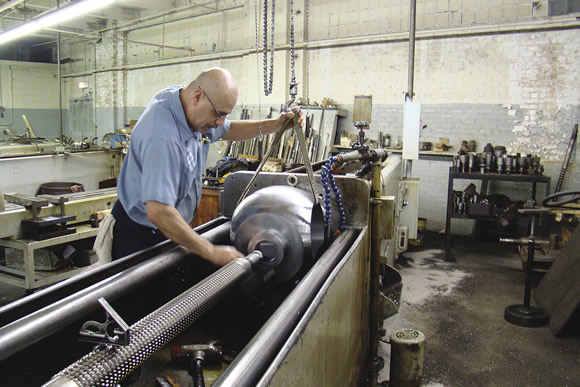
Operator Salvador Leanos at V W Broaching Service sets up a ball valve to broach an internal spline.
In many ways, one cannot think about the future of a broaching company like V W Broaching Service Inc. without thinking about its past. Broaches stored along a wall, hundreds of them, new and old, are visual reminders of countless jobs, of past challenges, of literally the blood, sweat and tears of a family, the Roschman family.
Patriarch George Roschman started V W Broaching nearly 60 years ago, and his family lineage can be seen today. His son Russell Roschman serves as president, and grandson Steve Hanna as vice president, with other family members working in the front office.
The business began in 1955 in a rented basement, and, by 1959, had moved into its current 54,000-sq.-ft. facility, located next to the elevated railway tracks that run along Chicago’s Lake Street.
While much of the company has remained constant over the years—its location, leadership and many of its employees—that doesn’t mean the company stands still. Acquisitions and investments in new technology have increased capacity and capabilities.
Over the years, the company has produced just about anything and everything, from farm equipment to medical device components, parts for rockets and knobs for consumer electronics. Diversification, Roschman said, is the key to the future, as it was to its past.
In the 1960s and 1970s, the company flew high on sales to the automotive industry, literally by keeping passengers from flying out of their seats. The company produced millions of seat belt components. Eventually, that business faded.
“I miss the old days of having jobs like broaching 11.5 million seat belt pins that held seat belts into a carriage,” Roschman said. “Those were wonderful days, when the customer would literally back up the truck with broaching jobs for us.”
Today, the company compensates for the loss of high-volume orders by serving a wider range of clients, with more than 2,000 active customers around the world, according to Roschman.
One of its biggest current projects harkens back to broaching’s roots in rifle making. The company has a major contract to broach rifle stock and create the well that holds ammunition magazines on the AR-15 semiautomatic rifle. In the 1800s, job shops often broached, or rifled, weapons with broaching tools not too dissimilar to today’s cutters.
Tooling ExperienceJust as in the 1800s, and in the 1950s when the business began, the quality of the cutting tool is the key to effective broaching. V W Broaching has an expert broach maker in Tooling Manager Brian Gillund, who brings more than 30 years of experience to the task. Preferring his practiced touch and simple grinders over automated methods to make and maintain the tools, Gillund can often be found hunched over a broach, measuring and fine-tuning tools.
Broaching, in the main, is not a difficult concept, but the devil is in the details, such as a finely honed edge and the pitch of a cutting tooth. A broach combines roughing and finishing in one operation, and often in one pass, where the broaching tool is pulled through the workpiece. The tool consists of a series of teeth, with each tooth removing a small amount of stock, and the teeth are gathered into three distinct cutting sections. The first set is the largest and does the rough cut, the second set semifinishes, and the last set, with the fewest teeth, imparts a fine finish.
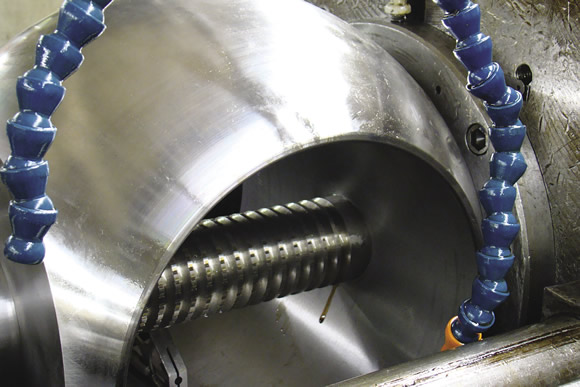
V W Broaching used a horizontal broaching machine (above) to cut an internal spline on this 24"-dia. ball valve. Below: In a few seconds, this spline was broached.
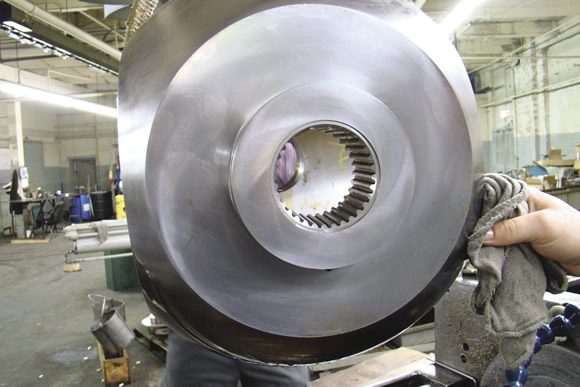
The secret to a fine finish, said Tim Espy, production manager, is in the gradual increase of tooth height over the length of the tool. This rise per tooth determines the amount of material removed and chip size. The rule of thumb for rise per tooth is 0.0025", he added, but varies according to finish requirements.
As opposed to yesteryear’s relatively soft, ferrous tools, today’s broaches are made from HSS, heat treated and coated to increase the tool’s surface hardness, lubricity and wear resistance. The broaches are often made from PM-M4 HSS, hardened to 65 HRC.
In addition to the broaches it makes for the jobs it runs, V W Broaching also produces custom and stock broaches for customers who do their own broaching, and sharpens and reconditions the tools.
Broaches are designed with a proprietary CAD program or CAD files sent in by its customers. While most broaches start with a part drawing, V W can reverse engineer from an existing part.
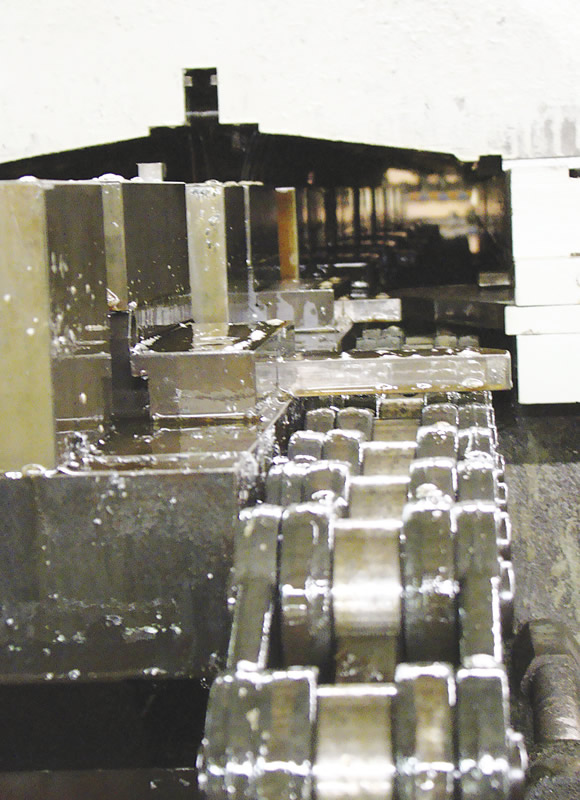
The chain on a continuous-chain broaching machine pulls parts through the work envelope (above), where multiple cutting tools remove stock. Below: A part before and after a slot is cut on the tip using a continuous-chain broaching machine.
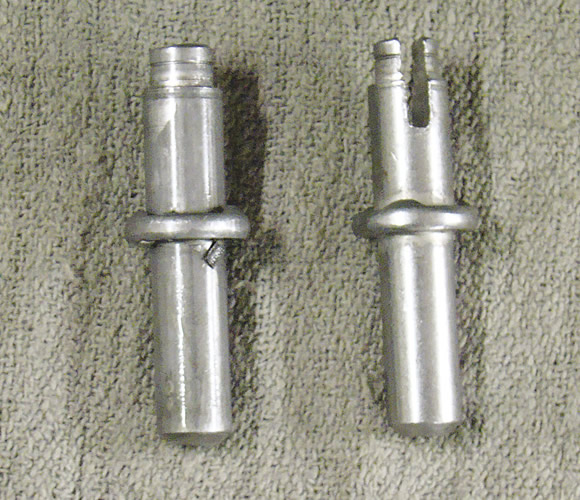
“Typically, the part to be reverse engineered will be something like a splined hub that connects a wheel to a shaft, and the customer comes in with a shaft or a hub and wants the mate,” Gillund said. “That’s a challenge, because we have to design a tool to figure out what the spline specs are through careful, multiple measurements, then design a tool to make the spline cut.”
Most broaches at V W Broaching are owned by customers, but left at V W’s plant. Keeping the broaches maintained and ready for use is a key issue, in part, because of the long lead times for new broaches. A broach in the 6"- to 7"-dia. range could take 8 to 10 weeks to produce and cost up to $25,000, Hanna said. If properly maintained, however, the broaches can last for years and drive down the cost per part to pennies, he added.
The tradeoff of this high cutting tool cost is the high cutting speeds and short cycle times broaching can achieve. Broaching speeds vary from 20 to 120 sfm, and cycle times are typically from 5 to 30 seconds. For example, the cycle time to broach the AR-15 well is about 5 seconds.
More than MillingBroaching’s lightning-fast speed has helped keep competing processes like CNC milling at bay. When broaching internal part features, for instance, “then it is no contest, broaching wins. It is simply too fast,” Roschman said.
Also, if the internal feature has a square-sided shape, it typically cannot be done with a CNC mill because the cutter has to spin, and that usually eliminates any job with such a feature. “Jobs with square-sided internal or external shapes can really only be done by broaching, wire EDMing, laser cutting and waterjetting,” Roschman said.
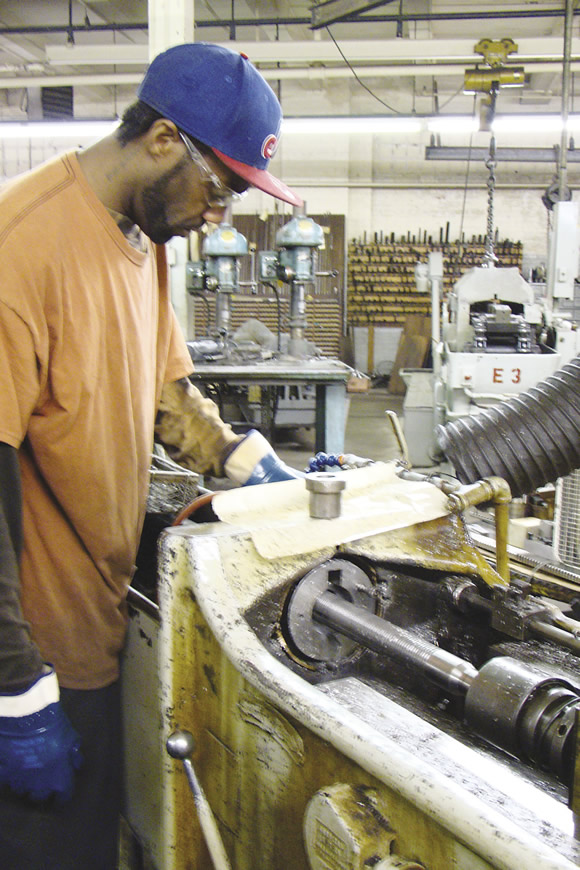
Operator Antoine Osby broaches a part.
When it comes to external part features, CNC milling can sometimes compete, unless the job calls for a simple slot or a series of slots and the piece can be magazine-loaded. In that case, “by the time the workpiece is loaded into and ejected from a CNC mill, broaching is already finished and moving to the next piece,” Roschman said.
V W Broaching Service has more than 60 horizontal, vertical and continuous-chain broaching machines. The company also utilizes vertical shapers and wire EDMs. With this capacity, the company can broach nearly any size part made of almost any material, Espy said.
He added that the company does high-volume production work as well as single-part runs. “We can create complex forms using modular tooling and multistage operations,” Espy said. While internal and external broaching are the company’s bread-and-butter, V W Broaching also does complex specialty broaching, such as spiral, blind-hole, straddle and pot broaching.
Horizontal broaching was the first broaching method developed and is still the most common way to cut internal shapes and forms, such as keyways. The company has several of these machines, each distinguished by its length of cut, which is a direct function of its total stroke and tonnage. In a typical horizontal broaching of an internal feature, the workpiece is fixtured to a base plate and the cutting tool is pulled through the piece. “We can cut up to 84" in length using one pass, with a maximum of 25 tons,” Hanna said.
On a recent project, Hanna and his team used an old Colonial horizontal machine to broach an internal spline on a 24"-dia. stainless steel ball valve. While this valve is large, the company can broach larger products, including a 48"-dia. valve that required removal of the machine’s front panel to set up the workpiece.
“The internal spline on that valve takes about 10 seconds to complete,” Hanna said. “If that were on a gear-shaping machine, it might take a couple hours.”
The company uses many different setups on its vertical broaching machines. Typically, the ram moves past the workpiece, carrying its broaching tools mounted in holders, and the part is secured in a fixture using hydraulic or mechanical clamps.
V W Broaching produces sprags, the clutch components that allow a flywheel to turn in one direction but not in the reverse direction. An operator of a vertical broaching machine, in a pull-down configuration, feeds bar stock into a broach, pulls down the ram and produces 24 sprags at a time in less than 4 seconds. In one shift, the company produces about 12,000 of these components.
A high-speed broaching method often employed at V W Broaching Service is continuous-chain broaching, which Espy refers to as “a train.” This train consists of a series of workpieces mounted to “cars” that enter an enclosed cutting envelope. The workpiece is chain-pulled past the cutters, each of which removes a small amount of stock. One recent job called for a deep slot to be cut into the tip of a part, reaching the required 3⁄8" depth with the help of 18 modular cutting tools.
This method is geared to high-volume production of external features and is extremely fast and efficient, Espy said. Another benefit is that it does not require a one-piece, solid broach; instead it uses smaller, modular cutting tools. “Instead of ordering a $10,000 broach and waiting weeks for it, we can make this tooling package in-house for a nominal fee and be up and running that day,” Espy said.
Modular tooling is appropriate for simple, external forms like slots and notches. However, when cutting complex internal forms such as irregular shapes and involute splines, the only option is a solid, one-piece broach.
Other MachinesThe company often looks for ways to save its customers money and decrease cycle times, Roschman said. Sometimes, grinding a broach is not cost-effective, he added. “If we are talking about onesies and twosies, and it has a straight-sided shape, we can do it with our vertical shapers,” Roschman said.
While many general machine shops no longer have vertical shapers, V W Broaching uses several of them as well as keyseaters, which generate about 15 percent of the company’s annual income. A shaper uses a single-point cutter to progressively remove material in multiple passes. “The vertical shaper is very versatile. It can do very large and heavy parts, and it can do very small parts. We don’t need to make an expensive broach to get the job done,” Hanna said.
For example, the company used a vertical shaper to generate an internal spline. The part was machined in two passes, a rough and a finish pass, and the tolerance was 0.008".
“We hold it to a plus, but never a minus tolerance,” Espy said.
The company also wire EDMs parts when the application is appropriate. V W’s EDMs are sequestered in a temperature- and humidity-controlled room. EDMed parts are designed using Esprit CAD software.
V W’s TomorrowThe wire EDM department is just part of V W’s plan to add machining capacity and expand into secondary operations, including, grudgingly, CNC milling. About 90 percent of all jobs are done without the need for subcontracting, but Roschman would like to improve on that figure.
It is no secret, he said, that these are challenging times for broaching companies, as margins are tighter, new technologies are entering the marketplace and engineers and part designers are creating products that do not require broaching. Because of that, Roschman said the company has to continue to increase market share and offer more capabilities.
Within the last 10 years, the company acquired Broach and Fixture Renewal Service, Harvey, Ill., High Speed Broaching Co., Franklin Park, Ill., and Hennig Broach and Tool Co. Inc., Thornton, Ill., which brought into the company more experienced staff and equipment. The Hennig acquisition, which was the most recent, enables V W Broaching to provide an entire new line of stock keyway broaches. These acquired companies were renamed V W Broaching Service, and now operate under the corporate banner, helping to carry the company into the future. “There are not many broaching companies who make their own broaches on-site anymore,” Roschman said. “That is why the acquisitions were so important to the company.”
For more information about V W Broaching Service Inc., call (800) 966-6052 or visit www.vwbroach ing.com. CTE
Broaching’s bright future?
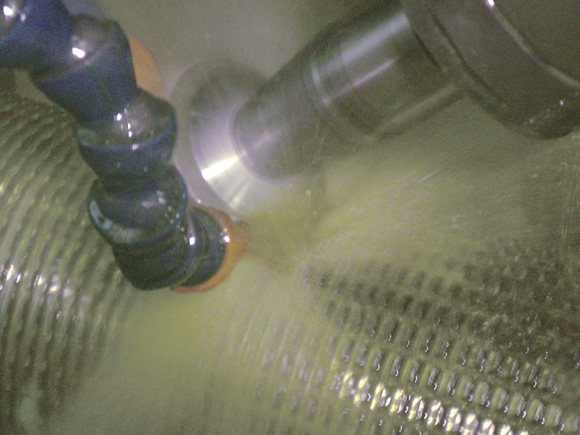
A broach is CNC-sharpened to help the tool produce parts with tight tolerances.
Related Glossary Terms
- blind-hole
blind-hole
Hole or cavity cut in a solid shape that does not connect with other holes or exit through the workpiece.
- broach
broach
Tapered tool, with a series of teeth of increasing length, that is pushed or pulled into a workpiece, successively removing small amounts of metal to enlarge a hole, slot or other opening to final size.
- broaching
broaching
Operation in which a cutter progressively enlarges a slot or hole or shapes a workpiece exterior. Low teeth start the cut, intermediate teeth remove the majority of the material and high teeth finish the task. Broaching can be a one-step operation, as opposed to milling and slotting, which require repeated passes. Typically, however, broaching also involves multiple passes.
- broaching machine
broaching machine
Machine designed specifically to run broaching tools. It is typically designated by operating characteristics (pull, push, rotary, continuous, blind-spline), type of power used (hydraulic, mechanical) and tonnage ratings. Broaching is also performed on arbor presses (manual and powered).
- chamfering
chamfering
Machining a bevel on a workpiece or tool; improves a tool’s entrance into the cut.
- computer numerical control ( CNC)
computer numerical control ( CNC)
Microprocessor-based controller dedicated to a machine tool that permits the creation or modification of parts. Programmed numerical control activates the machine’s servos and spindle drives and controls the various machining operations. See DNC, direct numerical control; NC, numerical control.
- computer-aided design ( CAD)
computer-aided design ( CAD)
Product-design functions performed with the help of computers and special software.
- electrical-discharge machining ( EDM)
electrical-discharge machining ( EDM)
Process that vaporizes conductive materials by controlled application of pulsed electrical current that flows between a workpiece and electrode (tool) in a dielectric fluid. Permits machining shapes to tight accuracies without the internal stresses conventional machining often generates. Useful in diemaking.
- fixture
fixture
Device, often made in-house, that holds a specific workpiece. See jig; modular fixturing.
- gang cutting ( milling)
gang cutting ( milling)
Machining with several cutters mounted on a single arbor, generally for simultaneous cutting.
- grinding
grinding
Machining operation in which material is removed from the workpiece by a powered abrasive wheel, stone, belt, paste, sheet, compound, slurry, etc. Takes various forms: surface grinding (creates flat and/or squared surfaces); cylindrical grinding (for external cylindrical and tapered shapes, fillets, undercuts, etc.); centerless grinding; chamfering; thread and form grinding; tool and cutter grinding; offhand grinding; lapping and polishing (grinding with extremely fine grits to create ultrasmooth surfaces); honing; and disc grinding.
- hardness
hardness
Hardness is a measure of the resistance of a material to surface indentation or abrasion. There is no absolute scale for hardness. In order to express hardness quantitatively, each type of test has its own scale, which defines hardness. Indentation hardness obtained through static methods is measured by Brinell, Rockwell, Vickers and Knoop tests. Hardness without indentation is measured by a dynamic method, known as the Scleroscope test.
- high-speed steels ( HSS)
high-speed steels ( HSS)
Available in two major types: tungsten high-speed steels (designated by letter T having tungsten as the principal alloying element) and molybdenum high-speed steels (designated by letter M having molybdenum as the principal alloying element). The type T high-speed steels containing cobalt have higher wear resistance and greater red (hot) hardness, withstanding cutting temperature up to 1,100º F (590º C). The type T steels are used to fabricate metalcutting tools (milling cutters, drills, reamers and taps), woodworking tools, various types of punches and dies, ball and roller bearings. The type M steels are used for cutting tools and various types of dies.
- lubricity
lubricity
Measure of the relative efficiency with which a cutting fluid or lubricant reduces friction between surfaces.
- milling
milling
Machining operation in which metal or other material is removed by applying power to a rotating cutter. In vertical milling, the cutting tool is mounted vertically on the spindle. In horizontal milling, the cutting tool is mounted horizontally, either directly on the spindle or on an arbor. Horizontal milling is further broken down into conventional milling, where the cutter rotates opposite the direction of feed, or “up” into the workpiece; and climb milling, where the cutter rotates in the direction of feed, or “down” into the workpiece. Milling operations include plane or surface milling, endmilling, facemilling, angle milling, form milling and profiling.
- milling machine ( mill)
milling machine ( mill)
Runs endmills and arbor-mounted milling cutters. Features include a head with a spindle that drives the cutters; a column, knee and table that provide motion in the three Cartesian axes; and a base that supports the components and houses the cutting-fluid pump and reservoir. The work is mounted on the table and fed into the rotating cutter or endmill to accomplish the milling steps; vertical milling machines also feed endmills into the work by means of a spindle-mounted quill. Models range from small manual machines to big bed-type and duplex mills. All take one of three basic forms: vertical, horizontal or convertible horizontal/vertical. Vertical machines may be knee-type (the table is mounted on a knee that can be elevated) or bed-type (the table is securely supported and only moves horizontally). In general, horizontal machines are bigger and more powerful, while vertical machines are lighter but more versatile and easier to set up and operate.
- modular tooling
modular tooling
1. Tooling system comprised of standardized tools and toolholders. 2. Devices that allow rapid mounting and replacement of tools. Commonly used with carousel toolchangers and other computerized machining operations. See toolchanger; toolholder.
- outer diameter ( OD)
outer diameter ( OD)
Dimension that defines the exterior diameter of a cylindrical or round part. See ID, inner diameter.
- pitch
pitch
1. On a saw blade, the number of teeth per inch. 2. In threading, the number of threads per inch.
- slotting machine ( shaper)
slotting machine ( shaper)
Vertical or horizontal machine that accommodates single-point, reciprocating cutting tools to shape or slot a workpiece. Normally used for special (unusual/intricate shapes), low-volume runs typically performed by broaching or milling machines. See broaching machine; mill, milling machine.
- tolerance
tolerance
Minimum and maximum amount a workpiece dimension is allowed to vary from a set standard and still be acceptable.
- wear resistance
wear resistance
Ability of the tool to withstand stresses that cause it to wear during cutting; an attribute linked to alloy composition, base material, thermal conditions, type of tooling and operation and other variables.
- wire EDM
wire EDM
Process similar to ram electrical-discharge machining except a small-diameter copper or brass wire is used as a traveling electrode. Usually used in conjunction with a CNC and only works when a part is to be cut completely through. A common analogy is wire electrical-discharge machining is like an ultraprecise, electrical, contour-sawing operation.
- work envelope
work envelope
Cube, sphere, cylinder or other physical space within which the cutting tool is capable of reaching.