“Huge.” That’s probably the first word that springs to mind when thinking of horizontal boring mills (HBMs). At their largest, the massive machine tools can have a work envelope with a length of more than 50 ' (15.24m), dominating a huge chunk of floor space. However, gigantic floor-type HBMs aren’t the only option. Smaller ones with rotary tables add versatility to a shop while using considerably less floor space than their bulkier brethren.
“The smallest one we offer is a table-type machine with a footprint of 3m × 3m (9.84 '×9.84 '), with a travel of about 1.2m (3.94 '),” said Joe Vidmar, service manager for machine tool builder Toshiba Machine Co. Canada Ltd., Markham, Ontario. “A lot of our customers are job shops, and whatever comes through their doors goes on a boring mill at some point in the manufacturing process.”
More Than Boring
A horizontal boring mill, despite the name, is capable of more than just boring. According to Bob Connors, vice president of sales and marketing for United Precision Services, a Cincinnati-based distributor of Union machine tools, a range of HBMs are available, including table, planer and floor types.
Table-type models typically include a rotary table. A compound slide is used to move the rotary table in the X and Z axes. Once X-axis travel needs exceed 100 " (2.54m), Union moves to a planer-type design, which has a full bed under the X-axis.
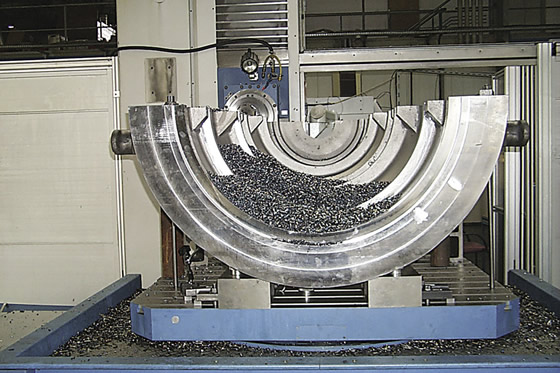
A valve component is machined on a Union T&K table-type horizontal boring mill.
“With planer-type machines, if you’ve got 10 ' of X travel, you’ve got a bed that’s 10 ' long to support the table as it moves,” Connors explained. “To achieve Z-axis movement, planer-types move the column rather than the table. That’s a more robust design, because you don’t have the compound slide, which is limiting.”
On a traditional table-type HBM, the saddle—and hence travel—is usually limited to the size of the bed. By eschewing the rotary table, planer designs typically travel about 4m (13.12 '). Beyond that, floor-type designs use a moving column for all axial travel.
Because of the nature of the design, all small horizontal boring mills are table-type, Connors noted, because the limitations of the table are outweighed by the flexibility it offers when machining small parts. This flexibility allows a table-type HBM to function like a horizontal machining center.
“If you look at HMCs, you’ll see a standard 630mm pallet, then an 800mm pallet, then a 1,000mm pallet,” he said. “Our boring mills pick up where the HMC leaves off. Applications would be similar—typically prismatic parts—but boring mills are outfitted with an integrated rotary table, similar to an HMC, which gives you access to four sides of the part.”
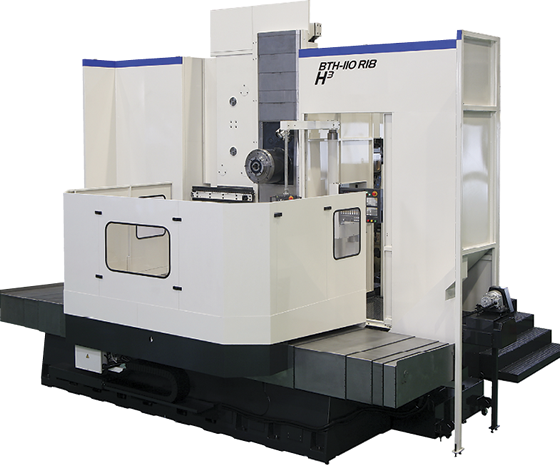
Toshiba offers a full range of table-type boring mills for various applications, including the BTH-110.R18, developed to provide machining center flexibility, according to the company.
Many United customers run machining center-style parts on an HBM because of its larger work envelope, he continued, although the unique capability of an HBM is the W-axis—an extendable quill, or spindle bar. The quill diameter determines the size of the work envelope, with the smallest machine United sells being the Union T-110, which has a 110mm (4.331 ") spindle bar. The machine’s work envelope is 80 "×63 "×60 " (2.032m × 1.600m × 1.524m), with 22 " (0.559m) of Z-axis spindle travel.
The quill diameter determines work envelope size because the rigidity of the quill determines how far it can be extended, according to Toshiba Machine’s Vidmar.
“On the 110mm boring mill, the quill extends up to 0.5m and not much more, because performance decreases drastically past that point,” he explained. “The larger the quill diameter, the longer it can extend, but also the more chance of it causing interference from the extra bulk.”
The advantage of a quill is that it gives a machine more reach by bringing the tool closer to the part without relying on tool extenders, Vidmar continued. On an HBM, it is easy for the tool to reach whatever workpiece faces are closest to the edge of the rotary table, but it can be hard to access features closer to the table’s center. “The quill gives up a little bit of rigidity in the tool, but you gain flexibility in terms of the parts you can make,” he said.
Flexible Flyer
That flexibility allows job shops like Superior Machining Ltd., Concord, Ontario, to perform a range of work on one machine. Superior has several HBMs, including a Toshiba BTD-200QF table-type mill, which has a 1m × 1m (3.28 '×3.28 ') rotary table. The shop uses the mill to drill, tap, high-feed mill, endmill and, of course, bore, according to President Dan Boaretto.
“The smaller machine is extremely useful because you can reach the center of the table quite easily,” he explained. “If you put a small part on one of our larger tables, it becomes very difficult to reach some of the features—the table size will actually interfere with the Z-axis movement.”
A smaller rotary table, Boaretto continued, allows a part to be placed on the table and reached on all sides, while the quill allows the tool to reach internal faces by extending the W-axis. “You can stack up tooling on a machining center, but when you have a quill, that’s about as rigid as you can get for those applications. It’s just a solid bar that lets you reach farther from your spindle face.”
Pretty much anything that will fit on the table can be machined, Toshiba Machine’s Vidmar said. “Mold shops are a great example,” he said. “They will use a boring mill to rough mold cavities, complete side work, like mounting holes and waterlines, and drill, tap and square up the mold. Virtually everything but high-speed finishing operations can be done on a boring mill.”
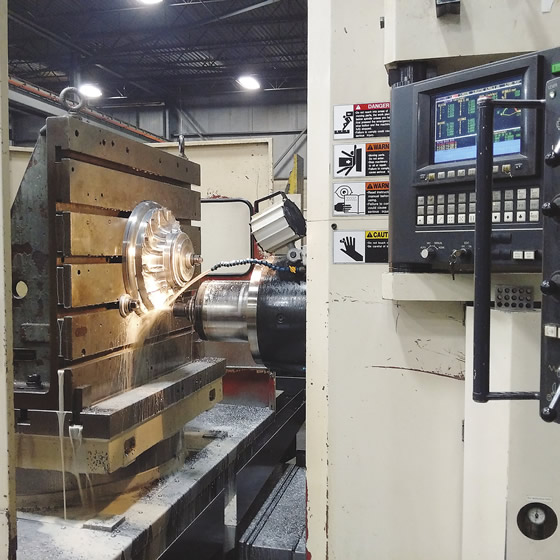
A Toshiba BTD-200QF HBM mills an inlet wall for a turbo compressor.
Granted, a vertical machining center might technically be able to perform more tasks in a smaller footprint than a table-type HBM, but machining large parts on a VMC presents issues, according to Dale Hedberg, Feeler product manager for Methods Machine Tools Inc., Sudbury, Mass.
“Methods’ Feeler boring mills feature ultrahigh precision when machining large workpieces, and 4-axis capability for work on multiple part surfaces,” he said. “You can probably machine all four sides in one setup by rotating the part to one side and machining the front and back faces. It’s a very efficient way to machine a part.” In addition, a substantial quill diameter and table capability for boring operations enables reaching into areas which are not accessible with typical spindles, allowing the machines to work with large, awkward workpieces.
Hedberg added that HBMs are typically more effective than VMCs when boring and drilling, as chip evacuation is more efficient with an HBM because it is not working against gravity to pull chips out of the cut.
“A table-type boring mill gives you a smaller footprint and a little more accuracy versus floor-type HBMs, but the work envelope is limited by the table size,” he explained. “However, you have the ability to do deep boring and drilling.”
Perfect Parallelism
While they are versatile, a key benefit of table-type HBMs is their ability to perform specific tasks not easily done otherwise.
“The name, of course, indicates boring,” said United’s Connors. “They can do much more than that, but they excel at a process called line boring, which involves machining two bores in perfect parallelism. In years past, and sometimes today, this was typically done on a HBM with a line bar that had a cutter on it and moved along the Z-axis.”
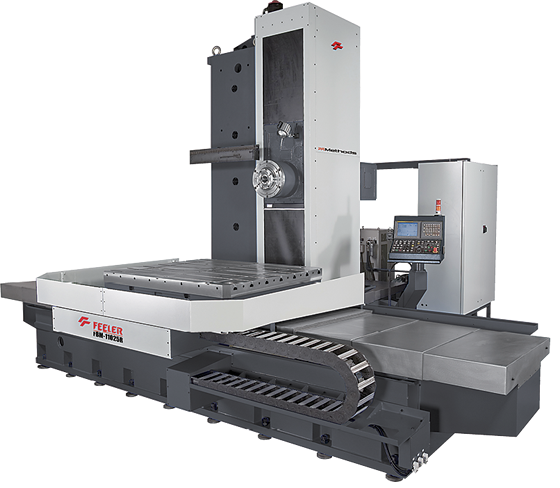
A Feeler table-type HBM from Methods Machine Tools has a rotary table and an extendable quill.
This operation aligns bores spaced a long distance apart, he explained, such as in a gearbox. While Connors has seen many shops bore one side on a machining center, then use an index table to line up the other side, index tables are still not completely exact, as each time an axis moves, inaccuracies are added.
“Granted, there are a lot of difficulties with line boring,” he admitted. “For example, when you’re extending the bar that far, gravity will take its toll and you have to support the end of the bar against its own weight. But sometimes you might have a journal in the center of a part—a gearbox is a good example again—and the difference between a machining center and a boring mill is that a boring mill will provide reach and rigidity to make sure everything is perfectly aligned.”
Shops machining parts for the oil and gas industry also use HBMs for specific machining operations, according to Methods’ Hedberg.
“Several manufacturers are doing wellhead parts, flanges, manifolds and fluid ends, and a very popular HBM attachment for those jobs is the U-drill,” Hedberg said, noting the specialized drill head makes repeated axial cuts. “With a U-drill, you automatically adjust the quill length, which forms different cutting radii in the workpiece. Cutting the desired radius is fully adjustable through the CNC program and allows you to perform machining operations in ways most standard machining centers can’t really manage.”
Custom Shop
Regarding options, table-type HBMs typically come standard with an automatic toolchanger and, obviously, a rotary table, but machine customization is virtually limitless.
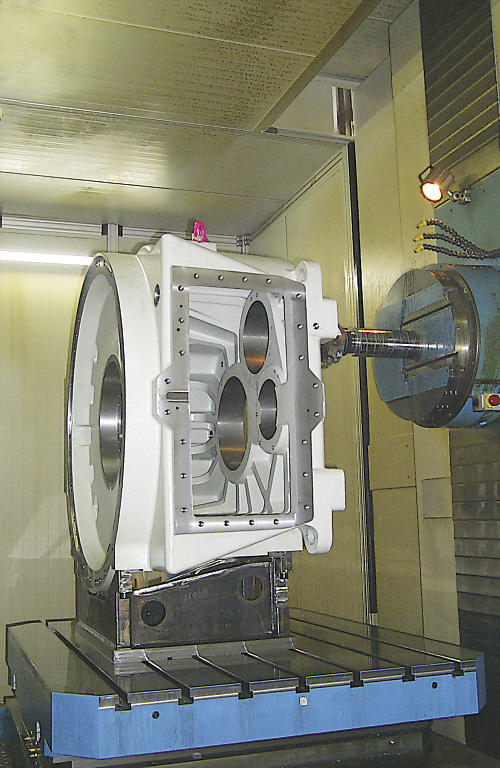
Gearbox manufacturers can make use of the HBM’s quill to ensure all internal and external bores are perfectly aligned.
“Automatic spindle probes and tool probes are common options, and pallet changers are not standard but are available and fairly common in production applications,” said United’s Connors. “Almost any automation capability that exists for a machining center can be applied to a horizontal boring mill.”
According to Boaretto, Superior was drawn to Toshiba Machine’s reputation for heavy-duty, dependable tools, and the ability to outfit its BTD-200QF table-type HBM with certain options.
“It’s got an automatic toolchanger, like most modern machines, but we also have some options on the control that help to reduce cycle times, like a high-feed machining option, Archimedes interpolation and a Shape function, which allows us to program a little more easily if we’re milling complex surfaces,” he said. “If you’re doing heavy work with difficult-to-cut materials, you aren’t going to be flying through the material, but those options do help increase productivity.” CTE
Contributors
Methods Machine Tools
(877) 668-4262
www.methodsmachine.com
Superior Machining Ltd.
(905) 669-4288
www.superiormachining.com
Toshiba Machine Co. Canada Ltd.
(905) 479-9111
www.toshibamachine.ca
United Precision Services
(513) 851-6900
www.unitedprecision services.com
Related Glossary Terms
- automatic toolchanger
automatic toolchanger
Mechanism typically included in a machining center that, on the appropriate command, removes one cutting tool from the spindle nose and replaces it with another. The changer restores the used tool to the magazine and selects and withdraws the next desired tool from the storage magazine. The changer is controlled by a set of prerecorded/predetermined instructions associated with the part(s) to be produced.
- boring
boring
Enlarging a hole that already has been drilled or cored. Generally, it is an operation of truing the previously drilled hole with a single-point, lathe-type tool. Boring is essentially internal turning, in that usually a single-point cutting tool forms the internal shape. Some tools are available with two cutting edges to balance cutting forces.
- centers
centers
Cone-shaped pins that support a workpiece by one or two ends during machining. The centers fit into holes drilled in the workpiece ends. Centers that turn with the workpiece are called “live” centers; those that do not are called “dead” centers.
- computer numerical control ( CNC)
computer numerical control ( CNC)
Microprocessor-based controller dedicated to a machine tool that permits the creation or modification of parts. Programmed numerical control activates the machine’s servos and spindle drives and controls the various machining operations. See DNC, direct numerical control; NC, numerical control.
- endmill
endmill
Milling cutter held by its shank that cuts on its periphery and, if so configured, on its free end. Takes a variety of shapes (single- and double-end, roughing, ballnose and cup-end) and sizes (stub, medium, long and extra-long). Also comes with differing numbers of flutes.
- gang cutting ( milling)
gang cutting ( milling)
Machining with several cutters mounted on a single arbor, generally for simultaneous cutting.
- interpolation
interpolation
Process of generating a sufficient number of positioning commands for the servomotors driving the machine tool so the path of the tool closely approximates the ideal path. See CNC, computer numerical control; NC, numerical control.
- machining center
machining center
CNC machine tool capable of drilling, reaming, tapping, milling and boring. Normally comes with an automatic toolchanger. See automatic toolchanger.
- milling
milling
Machining operation in which metal or other material is removed by applying power to a rotating cutter. In vertical milling, the cutting tool is mounted vertically on the spindle. In horizontal milling, the cutting tool is mounted horizontally, either directly on the spindle or on an arbor. Horizontal milling is further broken down into conventional milling, where the cutter rotates opposite the direction of feed, or “up” into the workpiece; and climb milling, where the cutter rotates in the direction of feed, or “down” into the workpiece. Milling operations include plane or surface milling, endmilling, facemilling, angle milling, form milling and profiling.
- milling machine ( mill)
milling machine ( mill)
Runs endmills and arbor-mounted milling cutters. Features include a head with a spindle that drives the cutters; a column, knee and table that provide motion in the three Cartesian axes; and a base that supports the components and houses the cutting-fluid pump and reservoir. The work is mounted on the table and fed into the rotating cutter or endmill to accomplish the milling steps; vertical milling machines also feed endmills into the work by means of a spindle-mounted quill. Models range from small manual machines to big bed-type and duplex mills. All take one of three basic forms: vertical, horizontal or convertible horizontal/vertical. Vertical machines may be knee-type (the table is mounted on a knee that can be elevated) or bed-type (the table is securely supported and only moves horizontally). In general, horizontal machines are bigger and more powerful, while vertical machines are lighter but more versatile and easier to set up and operate.
- planing machine ( planer)
planing machine ( planer)
Machines flat surfaces. Planers take a variety of forms: double-housing, open-side, convertible and adjustable open-side, double-cut and milling. Large multihead (milling, boring, drilling, etc.) planers and planer-type milling machines handle most planing work.
- tap
tap
Cylindrical tool that cuts internal threads and has flutes to remove chips and carry tapping fluid to the point of cut. Normally used on a drill press or tapping machine but also may be operated manually. See tapping.
- toolchanger
toolchanger
Carriage or drum attached to a machining center that holds tools until needed; when a tool is needed, the toolchanger inserts the tool into the machine spindle. See automatic toolchanger.
- work envelope
work envelope
Cube, sphere, cylinder or other physical space within which the cutting tool is capable of reaching.