END USER: Daystar Machining Technologies Inc., (828) 684-1316, www.daystarmachining.com.
CHALLENGE: Reduce setup and changeover time on lathes with live tooling.
SOLUTION: A modular quick-change collet system.
SOLUTION PROVIDER: Benz Inc., (866) 852-BENZ, www.benz-inc.com.
Performing quicker tool changes continues to be a priority at machine shops everywhere, because reducing machine setup by minutes or even seconds can add up to savings of hundreds of thousands of dollars annually. In addition to reducing setup and changeover times, flexible and stable quick-change system can cut tooling costs. Daystar Machining Technologies Inc., Fletcher, N.C., wanted to improve setup time when it purchased two Hurco lathes with live tooling last year. The shop previously didn’t have any live-tool machines.
Company President Jimmy Lytle noted the shop focuses on machining and fabrication with quick turnaround for short runs, prototypes and specialty parts. When Daystar personnel visited Hurco’s Indianapolis facility for a demonstration, they saw the lathes equipped with the Benz Solidfix modular quick-change collet system from Benz Inc., Charlotte, N.C.
With conventional tooling, when a shop finishes a run it has to remove the driven tools and then remove and clean the collet. This is a relatively cumbersome operation that requires the use of two hands and multiple tools, installation of the new tooling and taking offset measurements, according to Benz. Using Benz Solidfix, operators don’t have to remove the main tooling unit itself. Instead, they simply change the adapter, which holds a premeasured tool.
After seeing the demonstration, Lytle examined some other quick-change systems but determined Benz Solidfix was the best fit and purchased the quick-change system separately from the machine. “We are able to switch from a drill chuck to a collet chuck to a shell mill adapter to a solid endmill holder without having to change to a different live toolholder for each application,” he said. “Basically, anything you could think of to go on the end can be changed very rapidly.”
This means Daystar doesn’t have to buy as many live tools, which cost from $1,000 to $1,500 each, Lytle said. “Using this quick-change system, we have one somewhat-expensive toolholder and everything else is fairly inexpensive, costing a couple hundred dollars. This gives us a great deal of versatility without a major capital investment.”
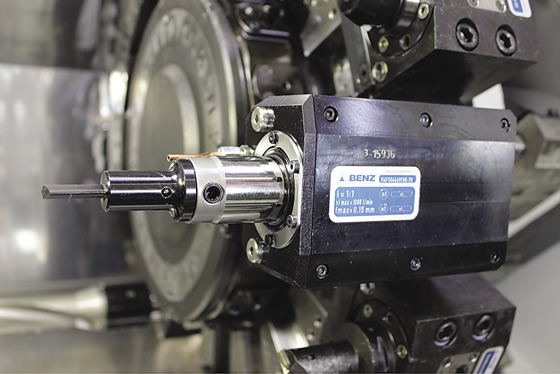
With the Benz Solidfix quick-change collet system, operators don’t have to remove the main tooling unit. Instead, they simply change the adapter, which holds a premeasured tool.
In developing the modular system, Benz reportedly simplified conventional quick-change technology. Instead of requiring an operator to spin on and tighten tooling in the holder using a wrench, the quick-change system requires only a turn of an Allen wrench. “Basically, turn a screw, pop a new head in, turn a screw and you’re done,” Lytle said.
In addition, in a conventional quick-change system, the operator has to remove the tool, install a new one and then touch off the tool to ensure the offset is correct. With the modular system, the operator can preset tools on a granite surface plate. When a cutting tool starts to wear or another type of tool is required, the operator inserts and secures the new tool.
Lytle said: “We have quick-change adapters on all the live tooling for those lathes. We can set the adapters out on the workbench and get everything ready for a setup. Then we are in and out of the machine very quickly.”
He noted the Benz Solidfix system reduces tool-change time from as much as 5 minutes to 10 to 15 seconds.
“Essentially, they’re putting the whole tool aggregate back in, and the repeatability is so accurate they can program in what they just measured off their height gage so they don’t have to go through that scenario of touching off the tool and then programming the offset,” explained Mike Starnes, sales application engineer for Benz. “It is really a plug-and-play system. Operators just switch out the soft tooling and they’re all set.”
He added that with Benz Solidfix, operators are performing a much simpler task, which usually can be done with one hand.
Lytle added that Daystar is planning to also use the quick-change system for right-angle heads on its machining centers.
Related Glossary Terms
- centers
centers
Cone-shaped pins that support a workpiece by one or two ends during machining. The centers fit into holes drilled in the workpiece ends. Centers that turn with the workpiece are called “live” centers; those that do not are called “dead” centers.
- chuck
chuck
Workholding device that affixes to a mill, lathe or drill-press spindle. It holds a tool or workpiece by one end, allowing it to be rotated. May also be fitted to the machine table to hold a workpiece. Two or more adjustable jaws actually hold the tool or part. May be actuated manually, pneumatically, hydraulically or electrically. See collet.
- collet
collet
Flexible-sided device that secures a tool or workpiece. Similar in function to a chuck, but can accommodate only a narrow size range. Typically provides greater gripping force and precision than a chuck. See chuck.
- endmill
endmill
Milling cutter held by its shank that cuts on its periphery and, if so configured, on its free end. Takes a variety of shapes (single- and double-end, roughing, ballnose and cup-end) and sizes (stub, medium, long and extra-long). Also comes with differing numbers of flutes.
- milling machine ( mill)
milling machine ( mill)
Runs endmills and arbor-mounted milling cutters. Features include a head with a spindle that drives the cutters; a column, knee and table that provide motion in the three Cartesian axes; and a base that supports the components and houses the cutting-fluid pump and reservoir. The work is mounted on the table and fed into the rotating cutter or endmill to accomplish the milling steps; vertical milling machines also feed endmills into the work by means of a spindle-mounted quill. Models range from small manual machines to big bed-type and duplex mills. All take one of three basic forms: vertical, horizontal or convertible horizontal/vertical. Vertical machines may be knee-type (the table is mounted on a knee that can be elevated) or bed-type (the table is securely supported and only moves horizontally). In general, horizontal machines are bigger and more powerful, while vertical machines are lighter but more versatile and easier to set up and operate.
- sawing machine ( saw)
sawing machine ( saw)
Machine designed to use a serrated-tooth blade to cut metal or other material. Comes in a wide variety of styles but takes one of four basic forms: hacksaw (a simple, rugged machine that uses a reciprocating motion to part metal or other material); cold or circular saw (powers a circular blade that cuts structural materials); bandsaw (runs an endless band; the two basic types are cutoff and contour band machines, which cut intricate contours and shapes); and abrasive cutoff saw (similar in appearance to the cold saw, but uses an abrasive disc that rotates at high speeds rather than a blade with serrated teeth).
- toolholder
toolholder
Secures a cutting tool during a machining operation. Basic types include block, cartridge, chuck, collet, fixed, modular, quick-change and rotating.