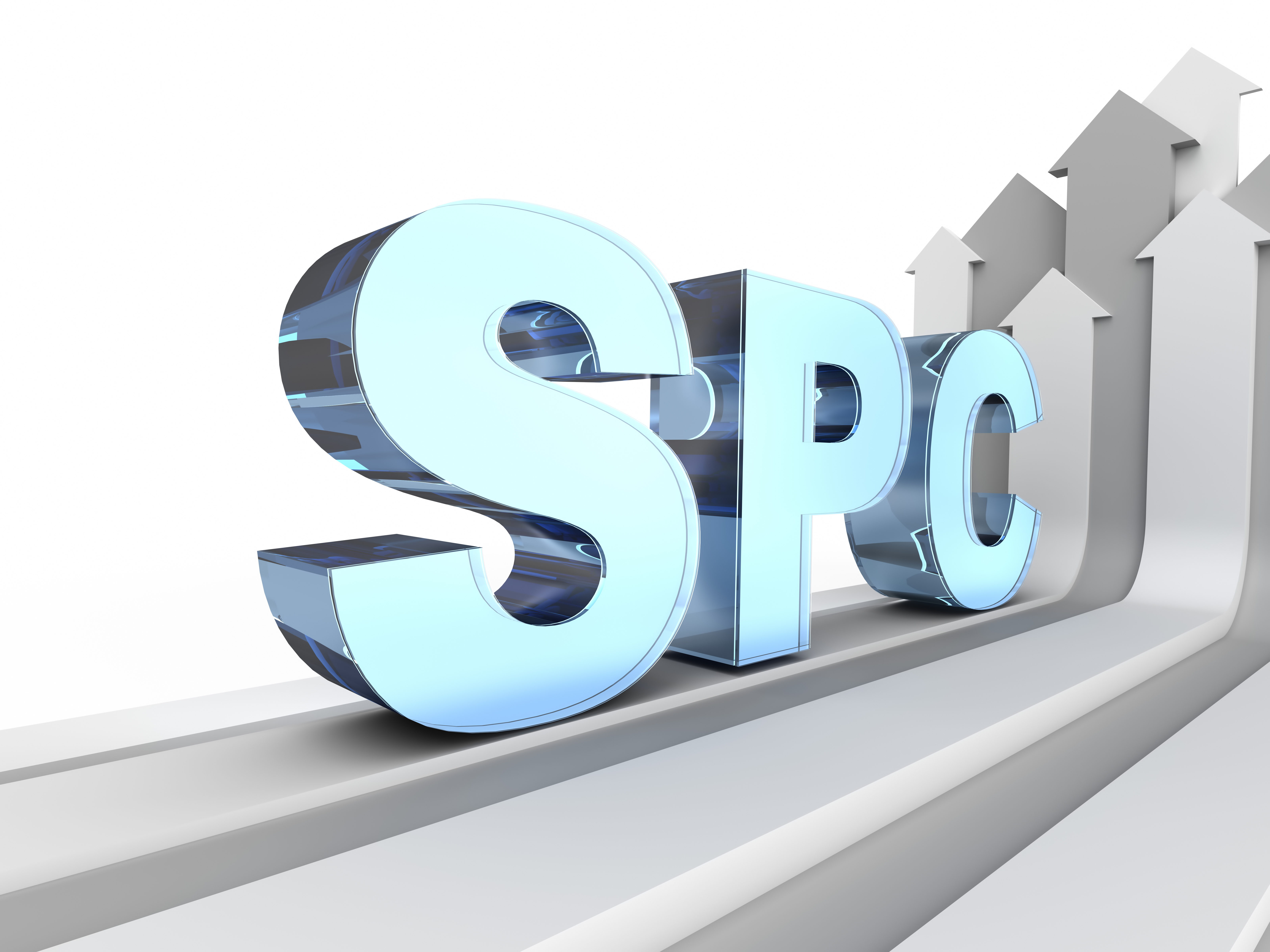
Statistical process control is a methodology aimed at improving the manufacturing process by using statistical means to measure and control quality. The goal is to reduce waste and ensure the highest level of quality in the production of discrete parts. This pertains to any process that a manufacturer follows to transform raw material into a finished product, such as the use of mills, lathes, grinding machines or stamping.
How SPC Helps
When using SPC throughout a manufacturing process, part measurements are acquired and then plotted on a chart to visualize if inconsistencies are present. For instance, are you trending out of tolerance, either up or down? Is a part becoming less round or rougher over time? Is the position of the part changing?
In addition to identifying inconsistencies, statistics themselves become part of an equation that takes into account all measurement data and then outputs a scorecard. This allows you to set a threshold regarding the level of quality and Cpk that you need to have as a manufacturer, whether determined internally or by the requirement of a customer. The scorecard tells you how close you are to meeting that threshold.
In this way, SPC metrics enable manufacturers to decide if action is needed for a problematic machine or process. For example, say you have a Cpk threshold of 1 and you are running a process with a current Cpk of 0.9. You can leverage SPC data to identify where the problem lies, whether investigating the Cpk of each machine or looking into the data of specific operators, shifts or other variables to recognize and solve the root cause.
This allows you to fix issues in real time. If you are making 1,000 parts a day and part dimensions become larger or smaller over the course of that day because a cutting tool is wearing out, SPC graphical data will show that. Knowing this information as it happens permits you to immediately change the cutting tool so parts quickly return to being produced at the correct size. This reduces waste and saves money, given you are not waiting until the end of the day to make the discovery.
Minimizing Variation
In any machining process, measurement variation will occur. Natural or expected variation in part production, like that caused by machine vibration, is referred to as common cause variation. Unexpected variation is called special cause variation, in which it can be traced to an assignable cause.
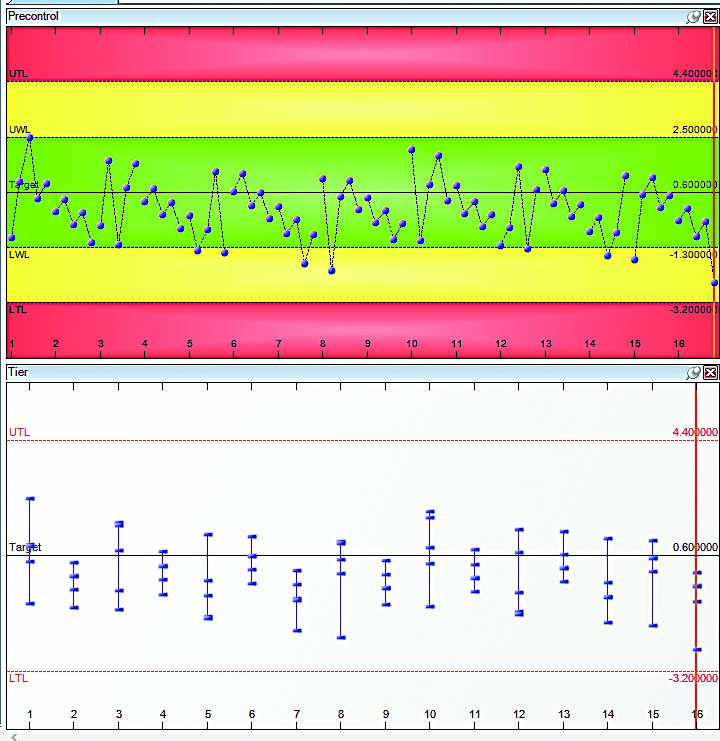
The magnitude to which manufacturers experience common cause variation is based on the quality of the machine, the production environment and the machine operator skill level. What causes this type of variation is not always easy to identify, but the resulting deviations, if centered on the target dimension, should remain within tolerance. Conversely, special cause variations can be tied to specific causes, such as operator error, machine malfunction, faulty part material or insufficient cutting tool fluids.
Use of SPC likely will reduce most variations, save for occasional special cause cases. This means that production should more consistently remain within tolerance and control measures.
Manual Processes
SPC can be used in both automatic and manual manufacturing processes. This is helpful for smaller shops that rely on manual machining and measuring devices. For example, at a shop with different levels of automation and therefore different variations, you could have someone turn the dials on a manual mill to remove material or you could use a CNC machine where someone loads a part, but the automated machine accomplishes the milling. In either case, you might have an operator manually inspecting while data collection is automated through digital tools. Here, SPC still can help improve quality control and measurement by using statistical means to consolidate and evaluate data.
Applicable Industries
Although SPC has roots in the automotive industry, the method is used in varying degrees in a number of highly automated industries, including oil and gas, medical and aerospace. SPC is most common in high-volume, low-mix manufacturing in which only a few part numbers are being produced and machines can be automated to complete repetitive tasks.
However, in high-mix, low-volume situations, automating operations becomes more complex. Operators are vital in these conditions, but that increases the chance of human error. In this case, SPC serves an important function in identifying when human error comes into play and whether more operator training or improvements to the manufacturing process can make a difference by lessening the opportunity for mistakes.
Looking Ahead
For people torn regarding whether to move forward with SPC, ask yourself these questions: What is the cost of bad quality at my shop? What is trying to reduce rejection rates and scrap worth to me? What return on investment can I get from SPC?
In the end, it is about identifying root causes and finding ways to limit those issues so you can save money in the long run and not lose valuable time that could be spent on other business needs. If SPC looks to be one of the ways to accomplish those goals, it is worth considering.
While the adoption of automation in manufacturing continues accelerating, operators and other staff members will remain involved in the production process. SPC will play an important role because it helps identify patterns in both manual and automated practices that ultimately affect the quality of measurement and the final product.
Contact Details
Related Glossary Terms
- computer numerical control ( CNC)
computer numerical control ( CNC)
Microprocessor-based controller dedicated to a machine tool that permits the creation or modification of parts. Programmed numerical control activates the machine’s servos and spindle drives and controls the various machining operations. See DNC, direct numerical control; NC, numerical control.
- gang cutting ( milling)
gang cutting ( milling)
Machining with several cutters mounted on a single arbor, generally for simultaneous cutting.
- grinding
grinding
Machining operation in which material is removed from the workpiece by a powered abrasive wheel, stone, belt, paste, sheet, compound, slurry, etc. Takes various forms: surface grinding (creates flat and/or squared surfaces); cylindrical grinding (for external cylindrical and tapered shapes, fillets, undercuts, etc.); centerless grinding; chamfering; thread and form grinding; tool and cutter grinding; offhand grinding; lapping and polishing (grinding with extremely fine grits to create ultrasmooth surfaces); honing; and disc grinding.
- milling
milling
Machining operation in which metal or other material is removed by applying power to a rotating cutter. In vertical milling, the cutting tool is mounted vertically on the spindle. In horizontal milling, the cutting tool is mounted horizontally, either directly on the spindle or on an arbor. Horizontal milling is further broken down into conventional milling, where the cutter rotates opposite the direction of feed, or “up” into the workpiece; and climb milling, where the cutter rotates in the direction of feed, or “down” into the workpiece. Milling operations include plane or surface milling, endmilling, facemilling, angle milling, form milling and profiling.
- milling machine ( mill)
milling machine ( mill)
Runs endmills and arbor-mounted milling cutters. Features include a head with a spindle that drives the cutters; a column, knee and table that provide motion in the three Cartesian axes; and a base that supports the components and houses the cutting-fluid pump and reservoir. The work is mounted on the table and fed into the rotating cutter or endmill to accomplish the milling steps; vertical milling machines also feed endmills into the work by means of a spindle-mounted quill. Models range from small manual machines to big bed-type and duplex mills. All take one of three basic forms: vertical, horizontal or convertible horizontal/vertical. Vertical machines may be knee-type (the table is mounted on a knee that can be elevated) or bed-type (the table is securely supported and only moves horizontally). In general, horizontal machines are bigger and more powerful, while vertical machines are lighter but more versatile and easier to set up and operate.
- process control
process control
Method of monitoring a process. Relates to electronic hardware and instrumentation used in automated process control. See in-process gaging, inspection; SPC, statistical process control.
- quality assurance ( quality control)
quality assurance ( quality control)
Terms denoting a formal program for monitoring product quality. The denotations are the same, but QC typically connotes a more traditional postmachining inspection system, while QA implies a more comprehensive approach, with emphasis on “total quality,” broad quality principles, statistical process control and other statistical methods.
- statistical process control ( SPC)
statistical process control ( SPC)
Statistical techniques to measure and analyze the extent to which a process deviates from a set standard.
- statistical process control ( SPC)2
statistical process control ( SPC)
Statistical techniques to measure and analyze the extent to which a process deviates from a set standard.
- tolerance
tolerance
Minimum and maximum amount a workpiece dimension is allowed to vary from a set standard and still be acceptable.