Contrary to popular belief, material thickness is only one factor in selecting the proper plate rolling machine capacity as well as the most effective process parameters. In addition to size, a plate’s material composition along with tensile and yield strength play equally critical roles in the decision-making process.
Tensile and yield are essentially how hard a material is. Yield strength means how much a material will bend when forces are applied, and tensile is the breaking point of the material.
The higher the yield, the tougher the material and more strength/power needed to roll it.
With that said, a mild steel like A36 with a yield strength of 40 ksi to 48 ksi for instance, will roll a lot easier than would stainless steel or AR plate that is harder with a yield strength of 90 ksi to 120 ksi.
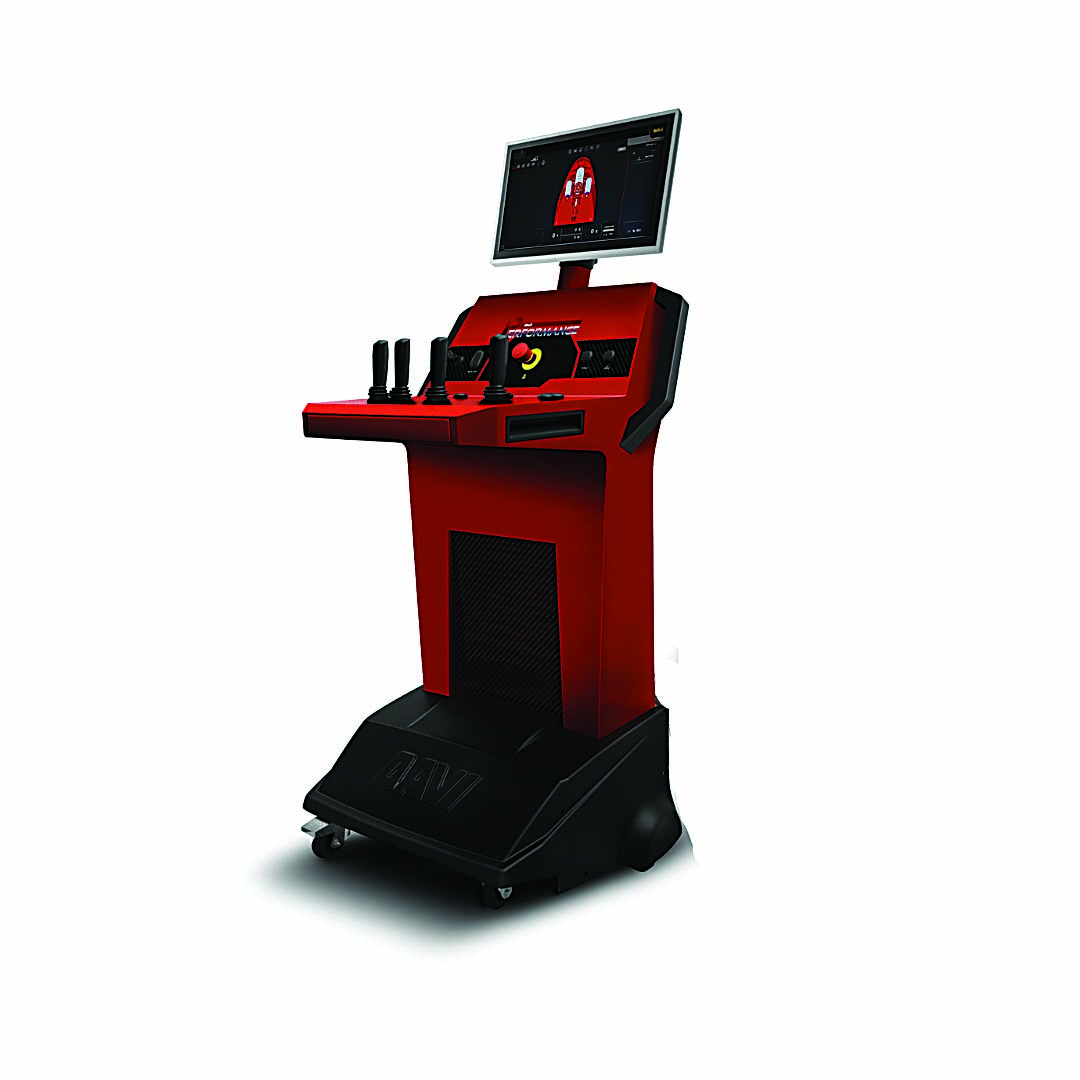
When it comes to determining proper rolling parameters, today’s plate rolling machine CNC controls make it easier based on the material being processed. For instance, these advanced machine controls will prompt operators to enter four key pieces of data. Those are type of material (yield and tensile strength), thickness, width and desired rolling diameter. From this, the CNC calculates the program along with presets for the required pressure and side rolls movement – how far they need to rise to achieve a certain radius along with all other necessary parameters.
Prior to CNCs, the plate rolling process required extremely skilled and experienced operators with an understanding of metallurgy along with some trial and error. When rolling a new and different material, these individuals would work out the best parameters, which took time, then manually record/list them in notebooks — or in their mind — for future reference.
Such material databases are now part of a machine’s control, which speeds the process immensely. For example, Davi’s two higher-end plate rolling machine CNCs – the iRoll eXtreme and iRoll Performance – contain internal material libraries, and once a material is selected, the control already knows the material’s characteristics.
These controls also allow shops to edit the material libraries, so they can further fine-tune the rolling process for their particular material types. This is especially helpful when material tensile and yield strength varies from batch to batch or from one supplier to the next.
Thanks to CNC technology, an inexperienced individual could successfully program and operate a plate rolling machine. Icons guide users through the programming process, starting with desired shape and on to the four key pieces of data. It is this ease of use that is helping shops combat the skilled labor shortage as experience operators age out of the industry. In fact, the vast majority of eligible Davi machines currently purchased are those with CNC controls.
Because CNCs are so beneficial to the plate rolling process, many shops with existing manual machines will opt for control retrofits. The only style of plate rolling machine that can be retrofitted with a true CNC is a four-roll type. This is because the CNC needs to know where the plate is during the entire rolling process, and this requires a bottom/pinch roll. Once the pinch roll and top roll clamp the material, encoders on each roll relay the position back to the CNC. By design, a three-roll machine lacks such capability.
However, those shops wishing to retrofit CNCs need to keep in mind that the cost of doing so, in some instances, can exceed the value of the machine itself. Machine age and the amount of effort required for the retrofit will strongly influence the cost. For example, a bare bones four-roll machine purchased in 1982, although it is possible, would most likely not be a good candidate for a CNC retrofit. The main reason for this is that older machines often lack the encoders, electronics, precision valves and other key components needed.
When a shop is ready to add advanced plate rolling technology such as machines with CNC controls, both tensile and yield strength are once again key to selecting the proper machine size/capacity (what the machine is rated for). For instance, the machine capacity a shop rolling quarter-inch, 10-foot sheets of A36 steel needs will differ from the one a shop working with that same size sheet and thickness but in AR steel. That latter application would call for a much bigger, stronger machine with more tonnage and capacity.
There’s always a sweet spot in terms of machine size for each shop. While there is some flexibility in terms of thickness with each machine, that level of flexibility is limited when plate thickness increases dramatically. Such changes in thickness would warrant a larger sized machine with more rolling capacity.
To accurately determine machine size sweet spots, Davi uses special internally developed simulation software to calculate necessary machine tonnage, then conducts performance tests for customers based on their material application. Without such software, rolling machine OEMs must rely on old capacity charts that can be hit or miss in some instances. Simulation software ensures a shop doesn’t invest in a machine with too much or too little capacity.
Much like CNCs take the educated guess work out of determining proper machine capacity and rolling process parameters, so too does in-process measurement for real time adjustments and corrections during actual rolling. Such systems include Davi’s patent pending iVision that the company showcased at Fabtech on its new e-POWER all-electric plate rolling machine, but it is available on both hydraulic and electric machines.
Davi's fully electric e-POWER plate rolling machine embodies the highest levels of precision, productivity, ease of maintenance and energy efficiency all within a quiet, compact machine that ensures hassle-free installation.
When it comes to plate rolling, it’s all about application. The material type and size along with tensile and yield strength that a shop wishes to roll will not only dictate effective process parameters but also the proper machine capacity. To eliminate the guesswork and the need for highly skilled operators, plate rolling OEMs offer advanced CNCs, material databases and other technologies like in-process measuring that take plate rolling ease of use to new levels.
Related Glossary Terms
- computer numerical control ( CNC)
computer numerical control ( CNC)
Microprocessor-based controller dedicated to a machine tool that permits the creation or modification of parts. Programmed numerical control activates the machine’s servos and spindle drives and controls the various machining operations. See DNC, direct numerical control; NC, numerical control.
- yield strength
yield strength
Stress at which a material exhibits a specified deviation from proportionality of stress and strain. An offset of 0.2 percent is used for many metals. Compare with tensile strength.