In many machine shops, the daily grind is brightened up by the stellar results they get from their jig grinding machines. The jig grinders in these shops are used to produce round holes and other shapes that meet the most stringent requirements for accuracy and finish. Jig grinders can be either computer controlled or manual, but CNC versions with advanced features are gaining in popularity as older manual machines are retired.
When it comes to position, form and finish accuracy, jig grinding takes things to another level compared to milling, according to Ian Slaughter, technical marketing manager for glass molding at Moore Nanotechnology Systems LLC, a manufacturer of jig grinders and other machine tools based in Swanzey, New Hampshire. “Milling is great for removing large stock quantities and gives an accuracy of 2 µm to 5 µm depending on your machines,” Slaughter said. “With jig grinding, you’re typically working from 2 µm down to 0.5 µm.”
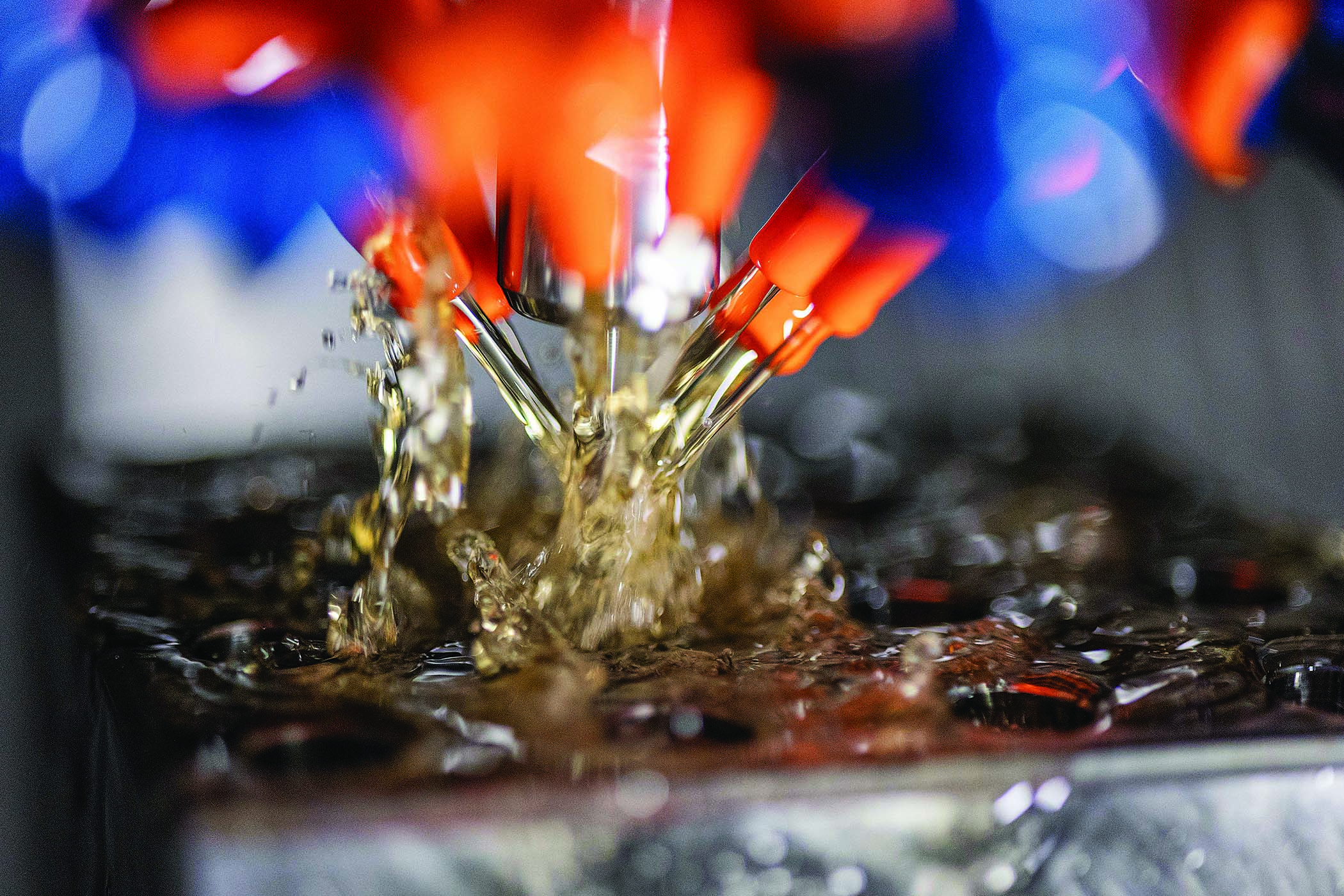
In many cases, Slaughter noted, jig grinders are used by the mold and tool industry to produce the forms needed to turn out accurate product shapes. In addition, he said, the machines are grinding components for the aerospace customers and others with high precision requirements.
Alternative Processes
As an alternative to jig grinding, Slaughter pointed out that similar results can sometimes be achieved by milling combined with a secondary operation. For example, a shop could mill and then polish to achieve similar surface finishes, he noted, but the entire process would be much more time-consuming than jig grinding.
Moreover, it would be “very difficult” to achieve comparable accuracy, he added. “Once you put in a manual operation, you will start to lose form very quickly. So customers looking to produce round holes or forms to sub-1 µm (accuracy) would be looking at a process such as jig grinding.”
Then there’s jig boring, which Slaughter described as a process done by a similar-looking machine that uses traditional cutting tools instead of a grinding wheel. Therefore, he said, jig boring can’t achieve the same levels of accuracy and surface finish as jig grinding. He also noted that a jig bore would only be used to produce round holes, whereas a jig grinder will produce other forms and contours.
Jig boring machines are very accurate when drilling, reaming and boring holes that need to be in a precise location, according to Andy White, president of White Jig Grinding Inc., a shop in South Elgin, Illinois, that offers a variety of jig grinding services. By contrast, White explained, jig grinders use a grinding wheel to finish existing holes or contour shapes with minimal stock to be removed. “Our customers usually leave a few thousandths of an inch of material to be removed to get the finished size,” he said.
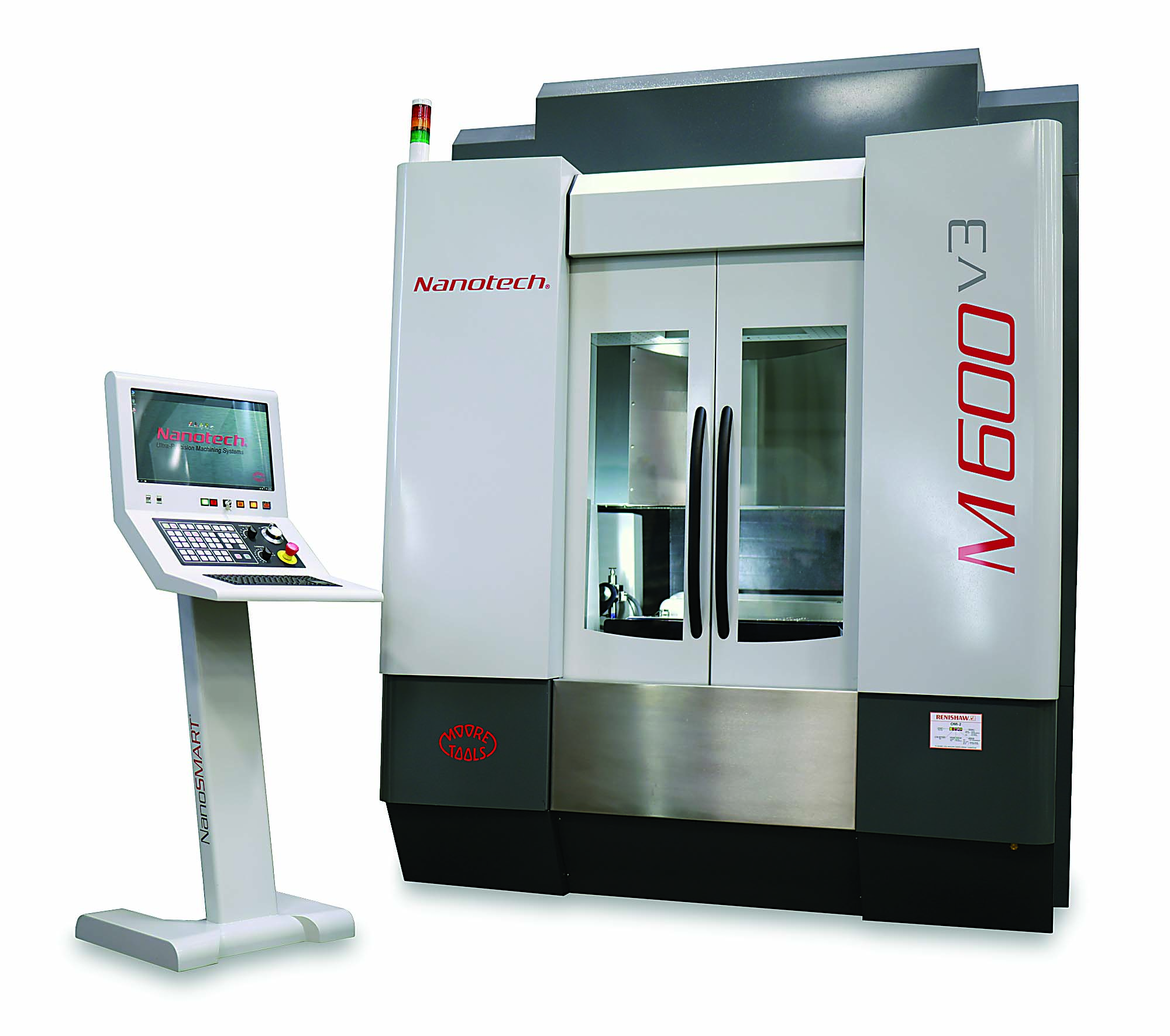
Image courtesy of Moore Nanotechnology Systems
For holding very tight tolerances, White said, wire EDM is often chosen as a faster and less expensive alternative to jig grinding, despite the fact that the wire will often leave a start/finish line on parts. There are no such flaws with jig grinding, he continued, noting that the process can generate a better surface finish because of the high speed (3,000 to 60,000 rpm) of the grinding head. “And with the many grinding wheel options, we are able to generate the surface finishes required for a specific job regardless of the type of material being worked on.”
Newer Machines
For shops that are tackling the jig grinding process, the latest machines are designed to deliver top-notch results while also making the job easier. One example is the M600, a state-of-the-art jig grinder co-developed by Moore Nanotechnology Systems and its sister firm, Moore Tool Co. Inc. in Bridgeport, Connecticut.
Officially introduced last year, the most recent version of the M600 includes a number of design elements aimed at boosting accuracy, repeatability and surface finish. According to Slaughter, these include increased rigidity at the wheel point where grinding takes place. Also new is a “counterbalance” for the machine’s Z axis. Thanks to this feature, “as the spindle motor, accelerates, decelerates and reverses in its reciprocation stroke, we have zero inertia, effectively putting no forces through the machine and giving us that ability to achieve greater accuracy and better surface finish,” he explained.
Slaughter also pointed out that the frame of the latest M600 is a granite monolithic structure, setting it apart from machines with frames made of cast components. This change is meant to improve accuracy by eliminating thermal expansion and contraction.
As Slaugther sees it, however, the main enhancement offered by the new M600 is the integration of the NanoSMART operating system used by all of the company’s other machines. As a former operator of conventional jig grinders, he believes the conversational and customizable NanoSMART system will be a welcome change for current operators who have long been dealing with specialized and difficult-to-master jig grinding controllers. “It’s a big step forward in ensuring that the machine is operator-friendly and attractive to users who are familiar with other machine tool types,” he said.
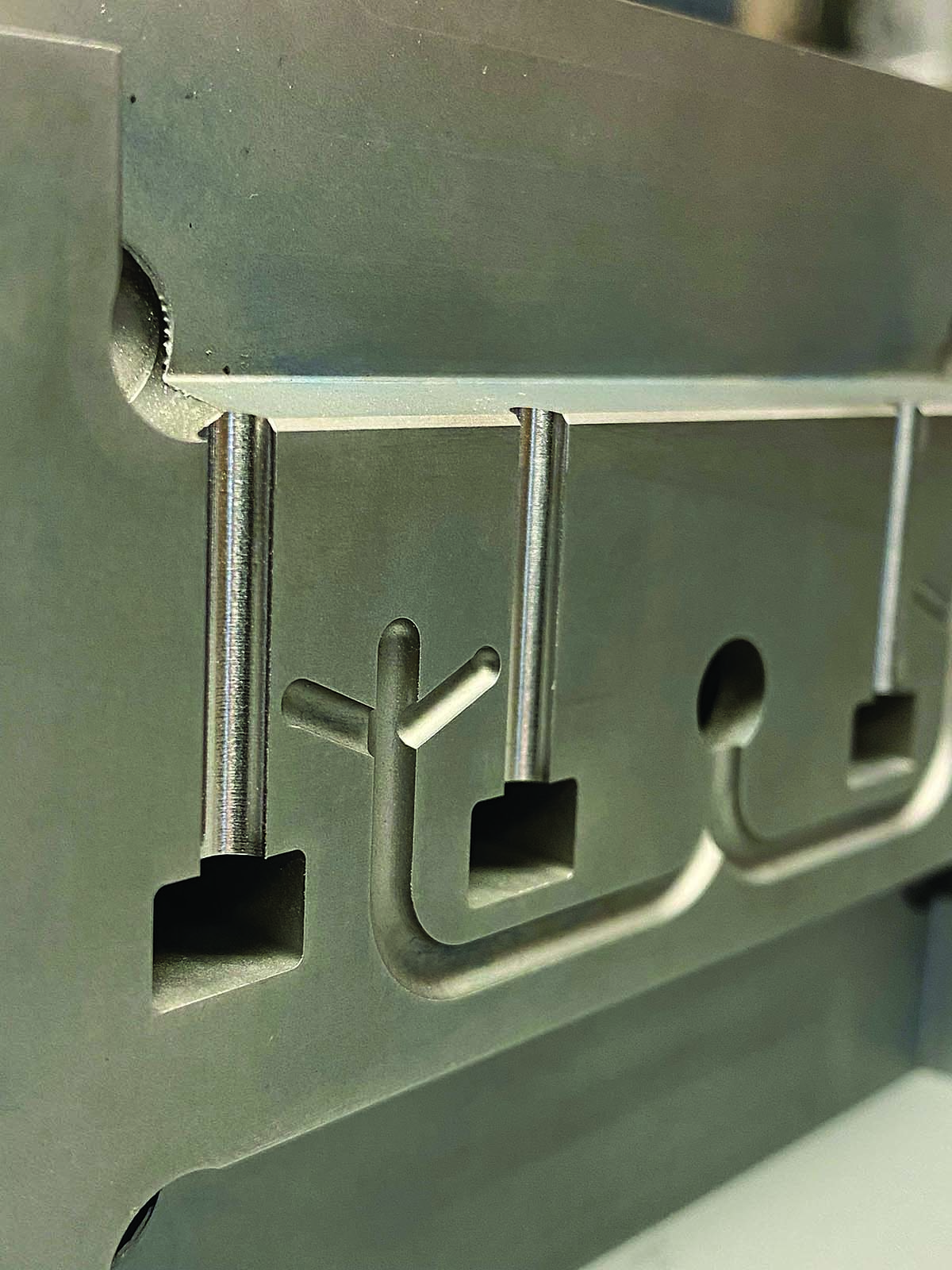
Chris Marsilius, Moore Tool’s chief marketing officer, said M600 users will also appreciate the fact that the machine can repeatably achieve sub-0.5 µm form and positioning accuracy in an unattended process. “Jig grinder operators traditionally have been very skilled at what they do. We’ve taken a lot of that (knowledge) and built it into the machine.” As a result, he said, “an operator is able to walk away and the machine will finish the part to that submicron level.”
Another modern CNC contender in the jig grinder market is the J350G from Mitsui Seiki USA Inc. in Franklin Lakes, New Jersey. The J350G, according to the company, offers the largest grinding infeed stroke available among competing machines, with a U-axis range of -3 mm to 50 mm relative to the spindle center. Mitsui Seiki says this allows the machine to grind both small- and large-diameter holes, as well as multiple features, using a single wheel in a continuous automatic mode.
The J350G’s Fanuc 31i-B control includes a 15" touch-panel LCD screen and is preloaded with G-MAPS conversational-style programming software. In addition, the control allows easy manual programming using graphic icons, data entry or conventional methods, the company notes.
Mitsui Seiki also touts the machine’s 3m2 footprint, which is said to be 50% smaller than that of its predecessor. Hand scraping and custom-designed Heidenhain scales contribute to ±0.0007 mm accuracy along the X, Y and Z axes, according to the company.
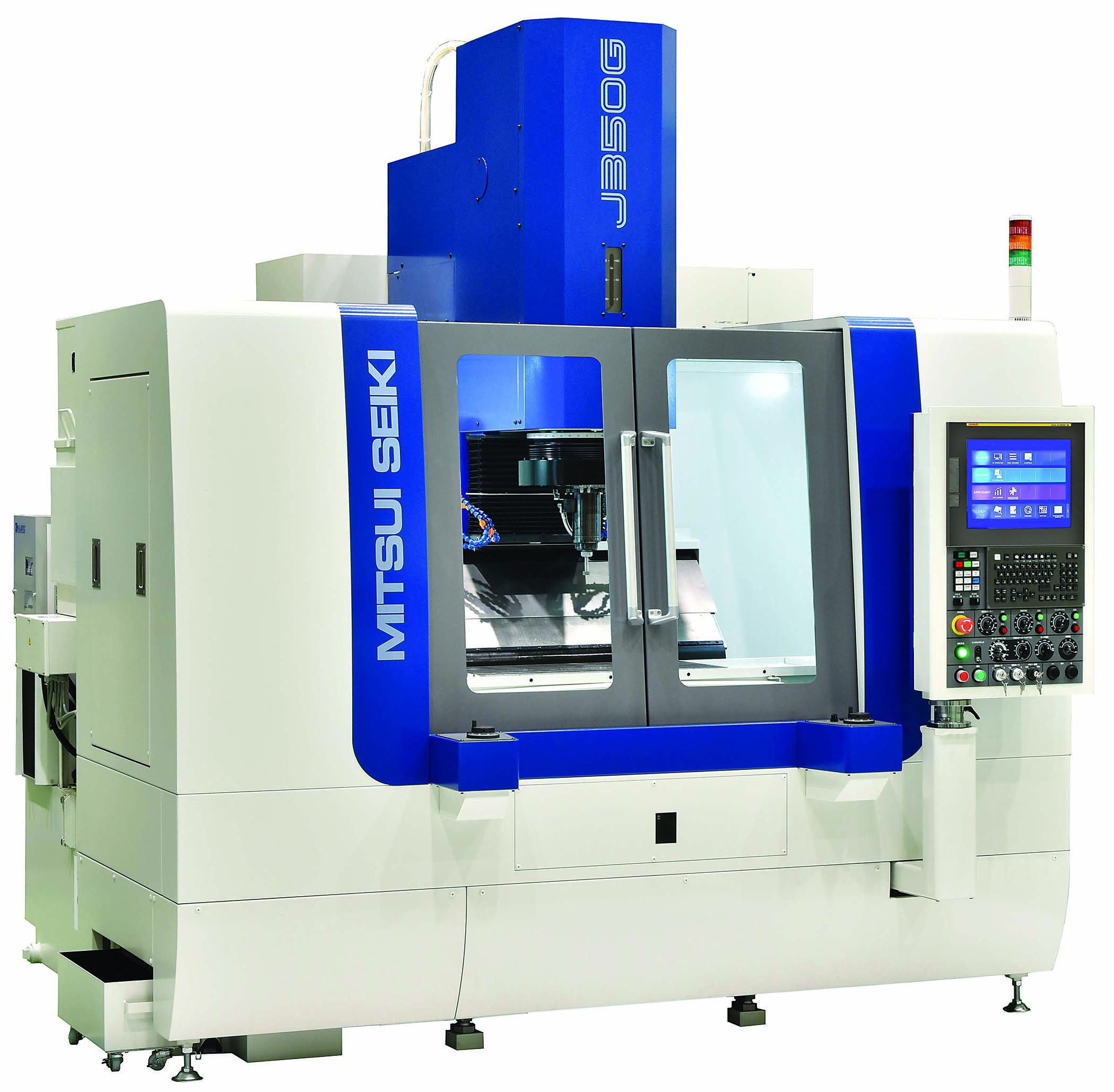
The space-saving footprint of the J350G jig grinder is 50% smaller than that of its predecessor. Image courtesy of Mitsui Seiki USA
Outsourcing Considerations
While some manufacturers purchase jig grinders strictly for their own work, Slaughter said others that own the machines have jig grinding departments that accept outside work as well as handling in-house needs. Manufacturers whose jig grinding needs don’t justify the capital investment in a machine can outsource the work to companies with these departments, as well as to specialist firms like White Jig Grinding. A third-generation family business dating back to 1970, White Jig Grinding buys its machines new and from a single source.
“There are companies that retrofit [old] jig grinders and modernize them with CNC control,” White said. “All ours are straight from the manufacturer, and we only use Moore jig grinders. Moore jig grinding machines are built with extreme accuracy that allows us to meet customer sizing, location and surface requirements.”
According to White, his jig grinding machines can repeatably grind holes and also contour profiles with a tolerance of ±0.0006". Different grinding wheels are used depending on the application material. He said solid borazon wheels, for example, are used to grind some harder materials. “And for the really tough stuff, which is carbide material, we use diamond wheels.”
White points to his company’s current experience as proof that strong demand continues for the services of jig grinding specialists. “As far as the little guy that’s doing this for a living, there’s not many of us out there,” he said. “But (judging by) our book of business, there‘s still a very big need for it.”
Contact Details
Related Glossary Terms
- boring
boring
Enlarging a hole that already has been drilled or cored. Generally, it is an operation of truing the previously drilled hole with a single-point, lathe-type tool. Boring is essentially internal turning, in that usually a single-point cutting tool forms the internal shape. Some tools are available with two cutting edges to balance cutting forces.
- computer numerical control ( CNC)
computer numerical control ( CNC)
Microprocessor-based controller dedicated to a machine tool that permits the creation or modification of parts. Programmed numerical control activates the machine’s servos and spindle drives and controls the various machining operations. See DNC, direct numerical control; NC, numerical control.
- electrical-discharge machining ( EDM)
electrical-discharge machining ( EDM)
Process that vaporizes conductive materials by controlled application of pulsed electrical current that flows between a workpiece and electrode (tool) in a dielectric fluid. Permits machining shapes to tight accuracies without the internal stresses conventional machining often generates. Useful in diemaking.
- gang cutting ( milling)
gang cutting ( milling)
Machining with several cutters mounted on a single arbor, generally for simultaneous cutting.
- grinding
grinding
Machining operation in which material is removed from the workpiece by a powered abrasive wheel, stone, belt, paste, sheet, compound, slurry, etc. Takes various forms: surface grinding (creates flat and/or squared surfaces); cylindrical grinding (for external cylindrical and tapered shapes, fillets, undercuts, etc.); centerless grinding; chamfering; thread and form grinding; tool and cutter grinding; offhand grinding; lapping and polishing (grinding with extremely fine grits to create ultrasmooth surfaces); honing; and disc grinding.
- grinding wheel
grinding wheel
Wheel formed from abrasive material mixed in a suitable matrix. Takes a variety of shapes but falls into two basic categories: one that cuts on its periphery, as in reciprocating grinding, and one that cuts on its side or face, as in tool and cutter grinding.
- jig
jig
Tooling usually considered to be a stationary apparatus. A jig assists in the assembly or manufacture of a part or device. It holds the workpiece while guiding the cutting tool with a bushing. A jig used in subassembly or final assembly might provide assembly aids such as alignments and adjustments. See fixture.
- jig boring
jig boring
High-precision machining (a sophisticated form of milling) that originally pertained to jig and fixture manufacturing. Basic jig-boring processes include centering, drilling, reaming, through and step boring, counterboring and contouring.
- jig grinder
jig grinder
Machine for grinding molds and dies where the positioning, shaping and finishing of holes and other surfaces are needed.
- milling
milling
Machining operation in which metal or other material is removed by applying power to a rotating cutter. In vertical milling, the cutting tool is mounted vertically on the spindle. In horizontal milling, the cutting tool is mounted horizontally, either directly on the spindle or on an arbor. Horizontal milling is further broken down into conventional milling, where the cutter rotates opposite the direction of feed, or “up” into the workpiece; and climb milling, where the cutter rotates in the direction of feed, or “down” into the workpiece. Milling operations include plane or surface milling, endmilling, facemilling, angle milling, form milling and profiling.
- milling machine ( mill)
milling machine ( mill)
Runs endmills and arbor-mounted milling cutters. Features include a head with a spindle that drives the cutters; a column, knee and table that provide motion in the three Cartesian axes; and a base that supports the components and houses the cutting-fluid pump and reservoir. The work is mounted on the table and fed into the rotating cutter or endmill to accomplish the milling steps; vertical milling machines also feed endmills into the work by means of a spindle-mounted quill. Models range from small manual machines to big bed-type and duplex mills. All take one of three basic forms: vertical, horizontal or convertible horizontal/vertical. Vertical machines may be knee-type (the table is mounted on a knee that can be elevated) or bed-type (the table is securely supported and only moves horizontally). In general, horizontal machines are bigger and more powerful, while vertical machines are lighter but more versatile and easier to set up and operate.
- tolerance
tolerance
Minimum and maximum amount a workpiece dimension is allowed to vary from a set standard and still be acceptable.
- wire EDM
wire EDM
Process similar to ram electrical-discharge machining except a small-diameter copper or brass wire is used as a traveling electrode. Usually used in conjunction with a CNC and only works when a part is to be cut completely through. A common analogy is wire electrical-discharge machining is like an ultraprecise, electrical, contour-sawing operation.
Contributors
Moore Nanotechnology Systems LLC
603-352-3030
https://nanotechsys.com
Moore Tool Co. Inc.
203-366-3224
https://mooretool.com
White Jig Grinding Inc.
847-888-2260
www.whitejiggrinding.com