Automating machine tools increases productivity and efficiency and helps ensure repeatable precision across multiple platforms and different operators. Automation of the machine’s supporting equipment also increases productivity. Tool presetters are a case in point.
Once a simple device that used a digital readout and an optical projector to determine the length and diameter of a cutting tool assembly, today’s tool presetters barely resemble their older counterparts. They’ve even outgrown the name “tool presetters.” Modern presetter systems collect hundreds of geometric features and measurements by scanning the cutting tool surface with a high-resolution CMOS video sensor. The presetter systems are one part measuring machine, one part inspection instrument and one part multifunction communication device.
More machine shops are requesting enhanced automation and additional inspection capabilities from tool measuring systems. Automating the mechanical system provides micropositioning of up to five independent axes of linear and rotational movement, while automation of the software routines that analyze the cutting tool gives operators a high degree of process control and micron-level repeatability of the resulting data. Software developers have recently made significant automation advancements.
For example, by automatically rotating the cutting tool assembly and simultaneously scanning the tool surface with a high-megapixel video sensor, Parlec’s software processes millions of points of data using thousands of algorithms. This produces measurements and geometries of interest to the machine tool control (if used to control the machining operation) or to connected applications (if used to support the tool data management process).
As this technology has evolved, operators have had to endure complicated user interfaces, the need to enter some tool data to identify the tool parameters and varying communication protocols to finally get the data where it needs to go. Manufacturer demand for greater simplicity led Parlec to develop the new SpeedScan measuring routine app for Parle-Vision CNC automated tool measuring and presetting software.
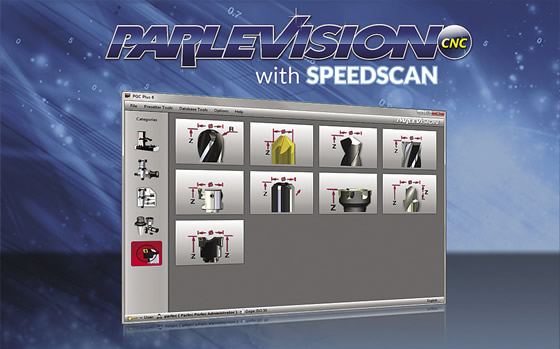
Courtesy of Parlec
Parlec has introduced the SpeedScan measuring routine app.
It starts with a tool presetter capable of total automation, including automatic tool positioning, focusing and indexing. These features, along with a standard library of automation routines and point-and-click creation of custom automation macros, combine to create a presetter system that can increase throughput of cutting tools up to 300 percent and ensure conformity and repeatability of the measuring and inspection process. By pressing one button, SpeedScan automates measurement of most standard tools without any data input. Efficiencies are increased by eliminating the risk of operator error.
Once data is collected and stored, the next step is to communicate this data where and when it’s needed. Here, tool presetters take advantage of Ethernet technology. Most tool presetters with a PC-based control come equipped for network and Internet communications. But it’s not enough to simply hook up to the network. Data comes in many languages and protocols, depending on the model of machine tool control, type of CAM software and tool management application.
Over the past few years, Parlec has spent considerable time developing and maintaining the capability to communicate with as many devices and applications as possible. Unfortunately, the machining industry is like the Tower of Babel. It seems like every control manufacturer has its own language and many idiosyncrasies when it comes to sending data.
To overcome this and incorporate the latest technology into its Parsetter TMM tool presetter systems, Parlec became involved in MTConnect from its inception. MTConnect is an open-source communication protocol that allows all devices and applications in the manufacturing environment to talk with one another. Parlec has incorporated MTConnect into the latest version of its tool data management software.
Therefore, using the term “tool presetter” simply won’t do anymore. You might just have to say “precision tool measuring and inspection and tool data communications and” … oh, never mind! CTE
Related Glossary Terms
- computer numerical control ( CNC)
computer numerical control ( CNC)
Microprocessor-based controller dedicated to a machine tool that permits the creation or modification of parts. Programmed numerical control activates the machine’s servos and spindle drives and controls the various machining operations. See DNC, direct numerical control; NC, numerical control.
- computer-aided manufacturing ( CAM)
computer-aided manufacturing ( CAM)
Use of computers to control machining and manufacturing processes.
- process control
process control
Method of monitoring a process. Relates to electronic hardware and instrumentation used in automated process control. See in-process gaging, inspection; SPC, statistical process control.