Founded in 2011 by Nathan Byman as a contract machine shop, Wolfram Manufacturing Technologies has morphed into a production technology laboratory, which is both a machine shop and a technology consulting firm that helps original equipment manufacturers with tools like adaptive machining, according to the company.
“We were basically going to build the company around the best technology that was available and try to figure out how to reduce defects and make a simpler way to machine,” said Byman, president of the Austin, Texas-based company.
Wolfram employs about 20 people and operates eight machine tools at its 557-sq-m (6,000-sq.-ft.) shop.
“Though about half of those people are dedicated to taking the technology and software that we work with and helping other machine shops,” Byman said.
He said the Tool Monitoring Adaptive Control system from Caron Engineering Inc. in Wells, Maine, was one of the core technologies that Wolfram integrated into its machining operation from the get-go. The system uses sensors, a dedicated high-speed data processor and an intuitive human-machine interface to measure tool wear and provide real-time control over cutting operations.
“I have run some really large facilities in the past with hundreds of machine tools, and it’s where I learned about TMAC,” Byman said. “I would not run a shop without it.”
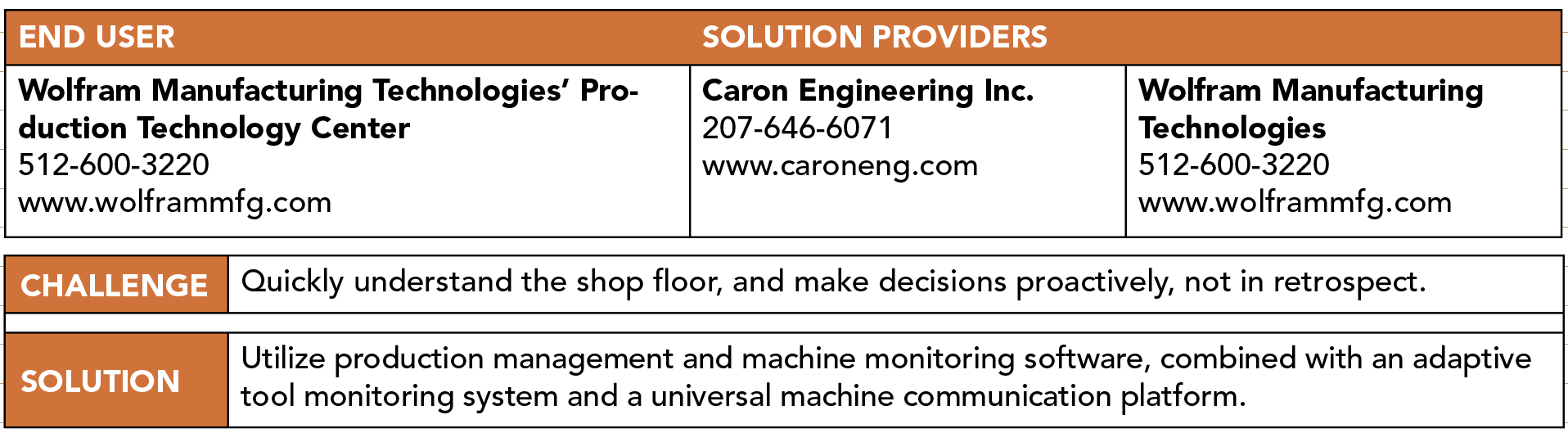
He said Wolfram also needed a shop monitoring tool, but after trying a variety of products from major developers, he determined that none provided the overall shop perspective that he wanted. As a result, Wolfram began development on its OnTakt production management and machine monitoring software about three years ago.
“The idea was it was going to show us what was going on with the shop, just whether the machines were running or not, whether they were producing parts,” Byman said. “But then what we realized is it would be incredibly powerful for tracking our tool consumption. And so we started making sure that it could register and track all the tool changes for all the tools in the shop and tie them to parts.”
With OnTakt, he said Wolfram can set targets for cutting tool life. For example, if a tool is under its target on several occasions, the software automatically captures that information and notifies the company via Microsoft Teams or Slack that there’s a tool issue.
“We are fixing things and recovering from them while other people still think everything is fine,” Byman said.
To bolster Wolfram’s ability to talk with other machine tools, he said the company purchased XMC in September, which is a universal machine communication platform that connects supervisory control and data acquisition, HMI, manufacturing intelligence and custom applications to diverse shop floor machines and devices.
“What XMC brings to the table is they’ve been in business for a long time and they have some of the very initial patents in this space for talking to machine tools,” Byman said. “What we got is this incredible knowledge about working with all kinds of additional machine tools and their direct connections to different systems.”
A big benefit of having OnTakt powered by XMC and integrated in TMAC is the reduced time to troubleshoot an issue. While at his desk or even remotely from his phone, if there is a problem, he said he can see exactly which tool caused it.
“I can see what that tool looked like when it was in the cut, its horsepower signature,” Byman said. “I can see what the same tool looked like on the prior part to see what was going on. I can see what that tool feature looked like 200 parts ago or two weeks ago to see what has changed.”
He said the result is straightforward conversations about what happened and how to fix it.
“So less speculation and quicker decision making about how to improve the process,” Byman said.
With the technologies, he said Wolfram also is able to push its cutting tools harder, faster and longer — and safer — than shops without them. For example, if an endmill lasts for 300 parts 9 out of 10 times, with the outlier lasting for 100 parts, shops generally set a tool life target of 100 parts to avoid scrapping expensive parts and potential machine downtime.
“Basically,” Byman said, “everyone handicaps their tools down farther than they need to based on the technology they’re using.”
That’s not the scenario at Wolfram.
“We have absolutely brilliant views of how long our tools are lasting, and we can push them right up to the limit, so we would set our limit at 300,” Byman said about the example. “Now, when we hit that 1-in-10 tool that has a shorter life, TMAC is going to stop it safely.”
In addition, he said Wolfram runs its machines around the clock, including weekends, whether attended or unattended.
Other parts manufacturers can purchase OnTakt and XMC from Wolfram, as well as TMAC from Caron Engineering. Byman said there has been “immense interest” in OnTakt since Wolfram began marketing it.
“Almost everyone who comes to our facility to take a look ends up leaving with it in their road map for deployment,” he said. “Seeing the tools working together is really compelling.”
Contact Details
Related Glossary Terms
- endmill
endmill
Milling cutter held by its shank that cuts on its periphery and, if so configured, on its free end. Takes a variety of shapes (single- and double-end, roughing, ballnose and cup-end) and sizes (stub, medium, long and extra-long). Also comes with differing numbers of flutes.