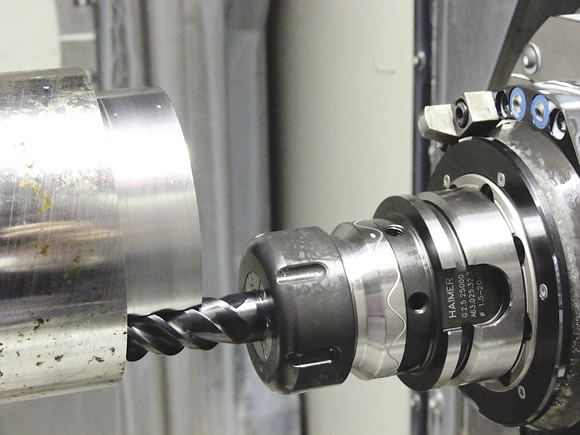
Courtesy of Haimer USA
Hogging 6061-T6 aluminum on a horizontal machining center using a Haimer Safe-Lock-equipped HSK collet chuck.
Antipullout toolholders reduce scrap, increase tool life and eliminate anxiety while milling.
In the winter of 1918, Carl A. Bergstrom opened the Weldon Tool Co. in Cleveland. Working from his shop atop the Blackstone Building, he developed a new kind of endmill, one with a 30° helical flute. The thing cut like crazy. Yet Bergstrom quickly realized that his toolholder lacked the gripping power to hang onto his cutting-edge endmill, as the darned thing kept spinning right out of the holder. In a fury, he grabbed that newfangled tool and ground a flat spot on its side, giving the toolholder’s clamping screw a place to bite into. Bergstrom had invented the Weldon shank.
The old toolmaker has long since turned to dust, but his invention lives on. For decades, the Weldon shank has taken first place in the contest for raw gripping force. Until now, that is. Brendt Holden, president of tooling provider Haimer USA LLC, Villa Park, Ill., aims to retire Bergstrom’s brainchild to a well-deserved place in the milling hall of fame with the development of Safe-Lock, a system that utilizes a no-fail clamping technique.
“Weldon-style endmill holders by their very nature push the cutter off center,” Holden said. This creates runout and drastically reduces tool life. Worse, even the rugged Weldon flat is prone to failure under modern cutting conditions—people weren’t hogging huge blocks of titanium in Bergstrom’s day or machining aluminum at 600 ipm and 20,000 rpm.
But hold on. The Weldon flat may not be history. Other toolholder manufacturers, including Iscar Metals and Rego-Fix Tool, have developed hydraulic and press-fit toolholders that use new technology, in conjunction with the Weldon flat, to provide antipullout characteristics. While suppliers may debate the benefits of each system, machine shops have a growing list of choices for securing their endmills when performing extreme milling.
An Expensive Problem
For Haimer, the road to pullout prevention began in 2006. “A big aerospace company came to us for help,” Holden explained. “They were machining aluminum wing spars worth $40,000 apiece and had problems with their high-helix endmills pulling out of the holder when going around the corners.” The company tried everything: shrink-fit and hydraulic holders, high-end collet chucks, and even press-fit systems. Nothing worked.
“They had these holders with tremendous gripping force, but still the tools were pulling out,” Holden said. “They settled for a side-lock holder with a Weldon-style endmill, but tool life decreased dramatically compared to the shrink-fit or hydraulic systems. And even then the screw on one of their Weldon holders backed out while roughing a $100,000 block of titanium and scrapped the workpiece. They challenged us to come up with a toolholder that ensured the tool would stay put.”
The aerospace company had other requirements as well. Minimal runout was an obvious one, but they also needed to adjust the tool’s gage length. “They have these big 3-spindle gantry mills, and each spindle has to be at the same Z-axis height,” Holden said.
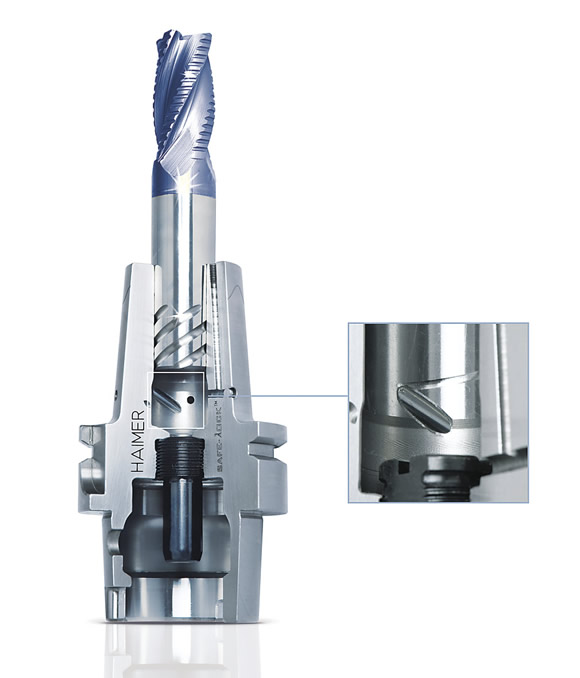
Courtesy of Haimer USA
Cutaway view of Haimer’s Safe-Lock clamping system.
Since Haimer was already producing shrink-fit toolholders, it started by modifying one of its standard shrink-fit chucks, adding a pair of angular rods immediately behind the clamping area. These rods engage a pair of precision-ground helical grooves on the endmill shank to securely hold the tool during high-feed milling. Because the helical locating grooves on a Safe-Lock endmill run in the same direction as the cutter’s helix angle, rotational forces can only drive the endmill into the holder, not force it out.
To satisfy the requirement for Z-axis length adjustment, Haimer designed the system to allow about 12mm of length adjustment, and then placed an adjusting screw in the bottom of the holder. This butts up against the endmill, preventing axial movement. The Safe-Lock system was born.
“We brought it to back to that aerospace company and it solved their problem,” Holden said. “Runout was less than 0.0001 " at a distance 3 times diameter from the chuck face. Tool life increased five to seven times compared to Weldon shank holders. They were very happy.”
Haimer then brought its invention to other aerospace shops, which experienced similar results. The company expanded its product line to include mechanical toolholders, accommodating those shops that do not have shrink-fit machines.
Partner Up
There was a problem, however—Haimer doesn’t make cutting tools. Its new system was unlikely to take off if Haimer couldn’t provide the modified endmills needed to use it. As a result, Haimer licensed the system to several toolmakers, including Kennametal Inc., Latrobe, Pa. Global Product Manager Ron West said Safe-Lock is one of the most innovative locking systems he’s seen in a long time. “It seems like the more torque you apply to the tool, the tighter it holds.”
West agreed the Safe-Lock system solves the laundry list of problems cited by Holden, but went one step further. Because Safe-Lock tends to send cutting forces toward the spindle, rigidity is improved compared to conventional toolholders. “Anytime you have a high radial load,” West said, “you’re pushing perpendicular to the spindle. It’s hard on the spindle bearings and can lead to wear and tear on the machine. Because tools in a Safe-Lock holder push straight upward in the Z-axis, the machine should be able to better absorb that energy into the spindle.”
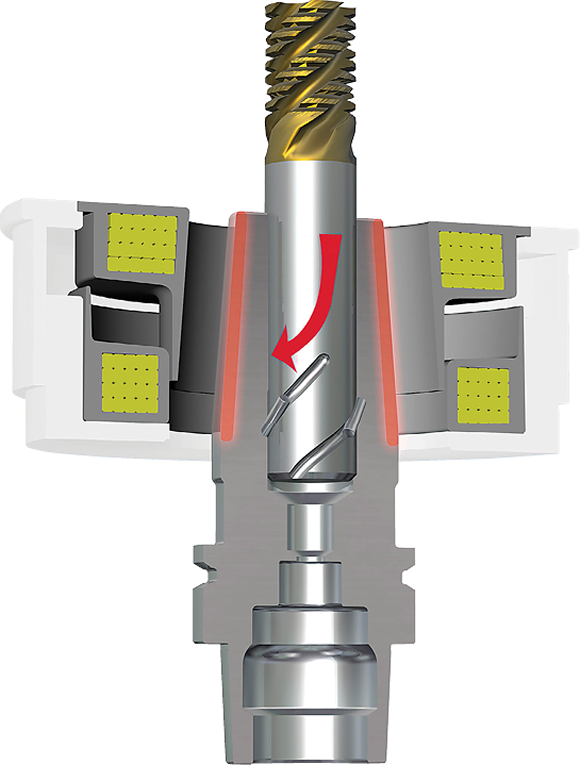
Courtesy of Haimer USA
Cutting forces are directed into the Safe-Lock chuck.
In addition to Safe-Lock-compliant endmills, Kennametal also makes a line of shrink-fit toolholders outfitted with Haimer’s patented antipullout technology. West said, “This system basically eliminates pullout. I’m a firm believer.”
Don’t Cheap Out
The up-front investment needed for any shrink-fit system can be a hurdle, and the Safe-Lock is no different. Dropping $20,000 for a machine to heat and cool toolholders makes most shop owners think twice. West offered the following argument: “An antipullout toolholding system offers many benefits. Productivity is improved because the feed rate and depth of cut are no longer limited by potential tool creep. This means less scrap and lost production due to unexpected pullout. The cutter will literally break before it comes out of the holder. Improved concentricity means better tool life and higher speed, again increasing throughput. And because shrink-fit endmills don’t have a flat on the side as with a Weldon shank, tool balance is better, reducing vibration.”
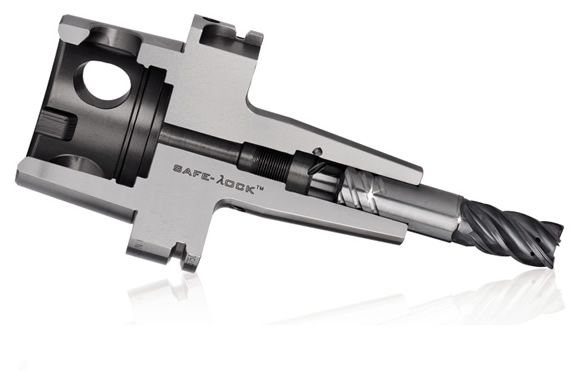
Courtesy of Kennametal
Cutaway view of a Kennametal shrink-fit HSK Safe-Lock toolholder.
Critics of shrink-fit technology point to the potential for metal fatigue. After all, repeated heating and cooling can turn even the toughest of metals into Silly Putty. To silence these naysayers, Haimer tested the typical shrink/heat thermal cycle more than 2,000 times against four sizes of toolholders, quickly bringing them up to 426° C, then chilling them down again to room temperature in less than 2 minutes. The results showed no loss of accuracy, gripping torque or metallurgical properties.
Another toolmaker embracing Safe-Lock technology is Seco Tools Inc. Bob Winegard, application support analyst for the Troy, Mich.-based company, said Seco is planning to roll out its own version of antipullout toolholders this fall. “Customers making aerospace, energy and medical parts cut a lot of Inconel, titanium, cobalt chrome, nitronic and high-strength duplex and super-duplex stainless steels, such as Ferralium and Zeron 100.” These alloys give toolholders a run for their money. “With precision components, even a few thousandths pullout will scrap the part. That’s why it’s critical to entirely eliminate all movement,” Winegard said.
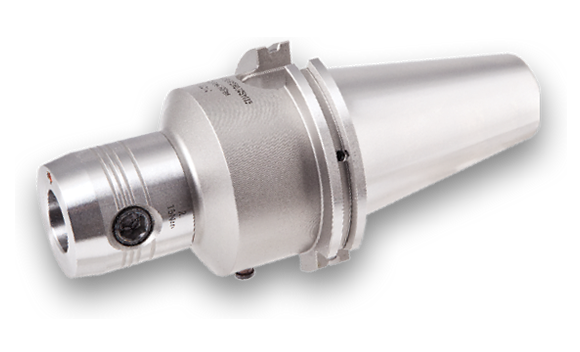

Images courtesy of Iscar Metals
An Iscar HYDRO-SURE sidelock hydraulic toolholder.
That assurance comes at a cost. While Winegard wouldn’t speculate on the price of Seco’s new system, both Winegard and Holden indicated Safe-Lock holders cost 10 to 15 percent more than standard shrink-fit tooling. They also require high-quality, modified endmills. “You’re doing yourself a disservice in terms of productivity and tool life if you buy on price alone,” he said.
The quality of the shank is at least as important as the business end of the cutter, Winegard said. Because of this, Seco recommends an H6 or better, which for a ½ "-dia. endmill means a shank tolerance of +0.00000 "/-0.00043 ". “If you don’t hold those tolerances, the shrink fit may not transmit enough torque and you can get vibration or runout.”
Not the Only Game in Town
Iscar Metals Inc. offers an alternative to shrink-fit and Safe-Lock holders. Its HYDRO-SURE hydraulic holder has 0.003mm concentricity and 360° clamping with a patent-pending locking system, according to Iscar. “It provides the security of a Weldon shank and the accuracy of a hydraulic holder, but without the high investment costs of shrink fit,” said Tom Edler, national product manager for Arlington, Texas-based Iscar. “The only additional equipment needed to tighten a HYDRO-SURE is an Allen wrench.”
Despite this advantage, he admitted to one shortcoming shared by most hydraulic holders. “The accuracy of the two systems is comparable, but shrink-fit holders do have nearly twice the gripping force,” Edler said. “For example, a 0.750 "-dia. shrink-fit holder exerts roughly 370 in./lbs. of torque, whereas the same size hydraulic holder has only 200 in./lbs. or so.”
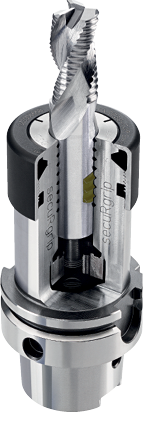
Courtesy of Rego-Fix Tool
Cutaway view of Rego-Fix’s antipullout secuRgrip toolholder. Note the threaded nose, which keeps the press-fit collet in place during heavy-duty milling.
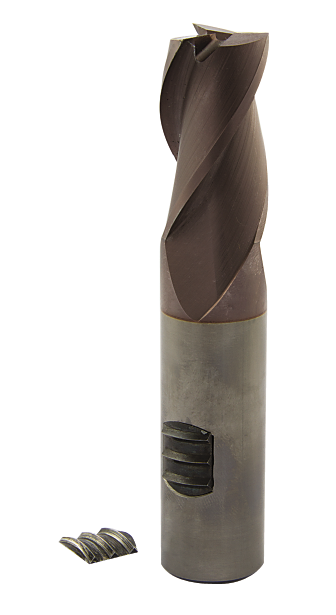
Courtesy of Rego-Fix Tool
In the Rego-Fix secuRgrip system, a threaded insert fits into the Weldon flat on the tool, locking it securely into place.
According to Iscar, its new system gets around this problem by incorporating a Weldon-style side-lock screw into the toolholder. “[Lower clamping force] is a moot point, as there is no way for it to rotate or pull out,” Edler said.
Like the systems discussed previously, an accurate tool shank is critical to gripping force. Edler also recommends H6 or better. And despite Iscar’s different approach to toolholding, Edler has no arguments about the affect of runout on tool life. “We prepared a case study, which established a baseline of 0.0004 " runout equal to 100 percent tool life. We found that increasing runout by just 0.0002 " cuts tool life by nearly 20 percent, while reducing runout by the same amount improves tool life by 30 percent.”
Edler said this is one area where most shops can see dramatic improvement with a reasonable investment: The cost of Iscar’s antipullout toolholder is around 15 percent more than its standard hydraulic one. “For a few bucks more,” he said, “I could literally come in, change the holder and provide better tool life and worry-free performance, regardless of whose cutter you’re using.”
Another company looking to keep the Weldon flat alive and kicking is Rego-Fix Tool Corp., Indianapolis. As Vice President of Sales Bill Obras explained, Rego-Fix leverages the Weldon flat as a way to guarantee zero pullout and high accuracy and does so with a mechanical clamping method.
“We began development of our system in 2002,” he said. “We observed problems with hydraulics in that you have a fluid chamber that can flex within the toolholder. And shrink-fit has issues with longevity due to heating and cooling, especially at diameters of ¼ " and below. We wanted to have a solid toolholder, one with the clamping force of a Weldon toolholder but without the associated runout.”
The result was the powRgrip, a press-fit system that uses a 100:1 taper and a matching collet. The tool is mounted in a collet, and, using a tabletop press that exerts more than 9 tons of force, the collet is pressed into the holder. Rego-Fix claims runout better than 0.0001 " at 3 times diameter with a service life in excess of 20,000 cycles at all diameters.
In spite of the powRgrip’s success, Rego-Fix observed that in some extreme cases pullout might occur. This is no different from any system without a positive lock. And, in today’s world of high-value aerospace and medical components, customers are unwilling to take the chance of scrapping an expensive workpiece.
Obras said: “Even with the tremendous clamping force generated by many systems, there’s a limit in very aggressive machining applications. The vibration and extreme radial load work to loosen the tool no matter how hard you clamp it. You have to have some sort of positive lock on that tool shank.”
The solution was to take that old Weldon flat and make it new again. Rego-Fix developed the secuRgrip toolholder, an antipullout version of its proven hydraulic system. The secuRgrip has several components, the first one being a standard hydraulic collet modified with an internal thread running the length of the bore. The second is a threaded insert that fits into a Weldon flat (see photos on page 56 and 57). Drop the insert into place, screw the endmill with its two pieces together into the collet, and then press the collet/endmill assembly into the tool holder like any powRgrip system. Lastly, a threaded cap screws over the top of the collet, locking it all together.
“We worked for a number of years on the secuRgrip system,” Obras said. “There’s no way for the tool to pull out of the collet, and the collet can’t pull out of the holder. The only failure mechanism is if the endmill breaks.”
Are you still using old-fashioned side-lock endmill holders and ER-style collet chucks? For a few hundred bucks, you can buy an endmill holder that can be pushed harder than Rocky Balboa in the 15th round. Whatever system you go with, all are sure to provide gripping power and accuracy far greater than their less capable counterparts. So stop griping, and start gripping. CTE
Machine tools have a dog in this fight
When it comes to extreme milling, there’s more to the story than keeping the tool securely in the holder. Michael Minton, national application engineering manager for machine tool supplier Methods Machine Tools Inc., Sudbury, Mass., said high-end tooling, antipullout or not, is kinder and gentler on equipment.
“Anytime you utilize precision toolholders and premium cutting tools, you will certainly improve part quality and productivity, but you’ll also be doing your machine tool a favor,” he said.
Minton explained that vibration is reduced as a tool is held more rigidly and concentrically. This improves surface finish and allows for correct and efficient acceleration of the tool through the workpiece. And an optimized tooling setup generates lower cutting forces. Not only can users push the tools harder, increasing throughput, they can also extend tool life.
This ultimately means less wear and tear on machine components, especially the spindle. “The machine tool and the spindle bearings should be designed for the majority of the work you’re going to do,” Minton observed. “That said, this isn’t always possible in a job shop. You might be machining aluminum one day and titanium the next. Many machine spindles work better when the cutting forces are directed upward in the Z-axis. This is especially true on light-duty equipment and machines with spindles that are not equipped to use dual-contact tooling, such as HSK or BIG-PLUS, since double-face contact spindles absorb radial forces better than taper contact-only tooling.
“Ideally, a machine tool should be purchased for the type of work you’re planning on doing on it,” Minton continued. “You will require a significantly different machine tool structure for machining titanium than you would for high-speed machining of aluminum. In either case, buying the best toolholders and cutters you can afford will maximize your machining success as well as your return on investment.”
—K. Hanson
Contributors
Haimer USA LLC
(866) 837-3265
www.haimer-usa.com
Iscar Metals Inc.
(877) BY-ISCAR
www.iscarmetals.com
Kennametal Inc.
(800) 446-7738
www.kennametal.com
Methods Machine Tools Inc.
(877) 668-4262
www.methodsmachine.com
Rego-Fix Tool Corp.
(317) 870-5959
www.rego-fix.com
Seco Tools Inc.
(248) 528-5200
www.secotools.com
Related Glossary Terms
- alloys
alloys
Substances having metallic properties and being composed of two or more chemical elements of which at least one is a metal.
- chuck
chuck
Workholding device that affixes to a mill, lathe or drill-press spindle. It holds a tool or workpiece by one end, allowing it to be rotated. May also be fitted to the machine table to hold a workpiece. Two or more adjustable jaws actually hold the tool or part. May be actuated manually, pneumatically, hydraulically or electrically. See collet.
- collet
collet
Flexible-sided device that secures a tool or workpiece. Similar in function to a chuck, but can accommodate only a narrow size range. Typically provides greater gripping force and precision than a chuck. See chuck.
- depth of cut
depth of cut
Distance between the bottom of the cut and the uncut surface of the workpiece, measured in a direction at right angles to the machined surface of the workpiece.
- endmill
endmill
Milling cutter held by its shank that cuts on its periphery and, if so configured, on its free end. Takes a variety of shapes (single- and double-end, roughing, ballnose and cup-end) and sizes (stub, medium, long and extra-long). Also comes with differing numbers of flutes.
- fatigue
fatigue
Phenomenon leading to fracture under repeated or fluctuating stresses having a maximum value less than the tensile strength of the material. Fatigue fractures are progressive, beginning as minute cracks that grow under the action of the fluctuating stress.
- feed
feed
Rate of change of position of the tool as a whole, relative to the workpiece while cutting.
- flat ( screw flat)
flat ( screw flat)
Flat surface machined into the shank of a cutting tool for enhanced holding of the tool.
- gang cutting ( milling)
gang cutting ( milling)
Machining with several cutters mounted on a single arbor, generally for simultaneous cutting.
- helix angle
helix angle
Angle that the tool’s leading edge makes with the plane of its centerline.
- inches per minute ( ipm)
inches per minute ( ipm)
Value that refers to how far the workpiece or cutter advances linearly in 1 minute, defined as: ipm = ipt 5 number of effective teeth 5 rpm. Also known as the table feed or machine feed.
- machining center
machining center
CNC machine tool capable of drilling, reaming, tapping, milling and boring. Normally comes with an automatic toolchanger. See automatic toolchanger.
- milling
milling
Machining operation in which metal or other material is removed by applying power to a rotating cutter. In vertical milling, the cutting tool is mounted vertically on the spindle. In horizontal milling, the cutting tool is mounted horizontally, either directly on the spindle or on an arbor. Horizontal milling is further broken down into conventional milling, where the cutter rotates opposite the direction of feed, or “up” into the workpiece; and climb milling, where the cutter rotates in the direction of feed, or “down” into the workpiece. Milling operations include plane or surface milling, endmilling, facemilling, angle milling, form milling and profiling.
- shank
shank
Main body of a tool; the portion of a drill or similar end-held tool that fits into a collet, chuck or similar mounting device.
- stainless steels
stainless steels
Stainless steels possess high strength, heat resistance, excellent workability and erosion resistance. Four general classes have been developed to cover a range of mechanical and physical properties for particular applications. The four classes are: the austenitic types of the chromium-nickel-manganese 200 series and the chromium-nickel 300 series; the martensitic types of the chromium, hardenable 400 series; the chromium, nonhardenable 400-series ferritic types; and the precipitation-hardening type of chromium-nickel alloys with additional elements that are hardenable by solution treating and aging.
- tolerance
tolerance
Minimum and maximum amount a workpiece dimension is allowed to vary from a set standard and still be acceptable.
- toolholder
toolholder
Secures a cutting tool during a machining operation. Basic types include block, cartridge, chuck, collet, fixed, modular, quick-change and rotating.