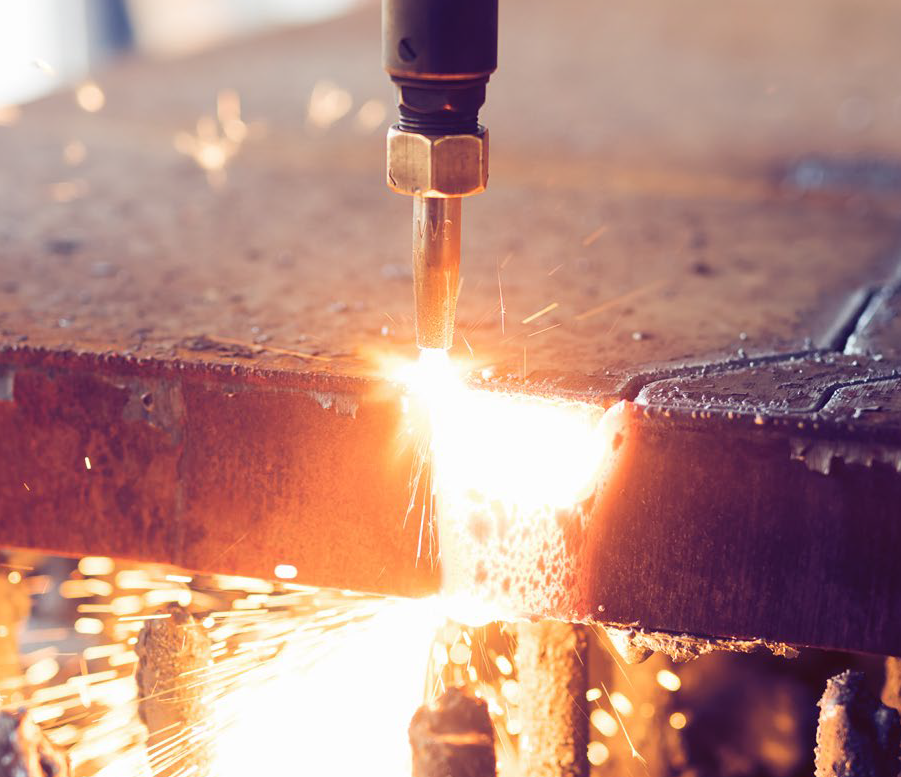
Today’s manufacturing customers expect fast turnaround times, competitive pricing, and on-time delivery of quality parts with every job. Achieving these outcomes requires a variety of capabilities called the “Great 8 of Manufacturing.”
In this whitepaper by Mike Melzer, VP of Operations & Service for Global Shop Solutions, the eight great ways that ERP can improve a manufacturer’s facility are discussed. If a manufacturer falls short in one of these areas, it can impact the ability to deliver what customers want.
These Great 8 elements are inextricably linked to each other, and low performance in one area negatively impacts all the others. The Great 8 ways to use ERP software to improve manufacturing and increase sales, are:
- Move parts through the shop quickly and efficiently.
- Schedule and deliver on time.
- Know your costs.
- Maintain accurate inventory.
- Control your labor costs.
- Get quality right.
- Serve your customers the way you want.
- Grow sales.
The ERP software provides a complete business management system designed to grow sales. When you schedule jobs more efficiently, it lowers setup and labor costs, improves throughput, maximizes capacity, and increases on-time delivery. These outcomes improve estimating and quoting so you can give customers the best possible price. Efficient scheduling also reduces the time spent putting out fires on the shop floor, allowing more time to focus on generating new business and increasing sales.
To get the complete whitepaper from Global Shop Solutions, click here.
To employ Great 8 method, call Global Shop Solutions at (800) 364-5958. To set up a demo online, click here.