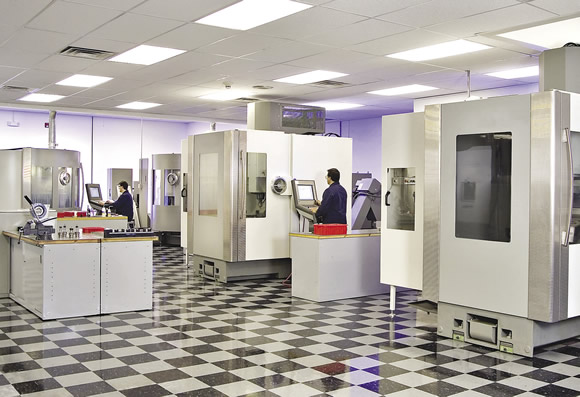
Courtesy of Oberg Medical
Oberg Medical performs multiaxis machining to produce a variety of medical devices.
Cobalt-chrome alloys are a good fit for medical and dental parts, but machining them can be a headache.
Manufacturers of medical and dental parts face an array of challenging workpiece materials, but cobalt-chrome alloys might take the cake.
“It ranks at the top in terms of difficulty,” said Steve Storlie, vice president of business development for Mendell Machine and Manufacturing Inc. The Lake-ville, Minn., medical parts manufacturer specializes in implants, surgical instruments and diagnostic equipment, as well as serving the defense and aerospace industries. It is no stranger to tough jobs. “We do all kinds of titanium,” he added. “We do titanium every day.”
In addition to cobalt and chromium, the metals used in the medical industry contain various alloying elements with desirable wear- and corrosion-resistance properties for implants, such as shoulder, knee and hip replacements. For example, CoCr28Mo6 ASTM F75 contains 58.9 to 69.5 percent cobalt, 27.0 to 30.0 percent chromium, 5.0 to 7.0 percent molybdenum, up to 1.0 percent manganese, silicon and nickel, up to 0.75 percent iron and up to 0.35 percent carbon. Cobalt chrome is stronger than stainless steel, but weighs twice as much as stainless and is brittle under impact loading. Hardness ranges from 40 to 50 HRC or higher.
“Cobalt chrome is extremely challenging to machine,” concurred Russ Moser, machining manager for medical parts manufacturer Judson A. Smith Co., Boyertown, Pa. Although the material has a tendency to workharden, he said cobalt chrome’s high hardness causes the shop more problems. “It becomes even more difficult once the hardness gets up in the 50-HRC range.”
Moser noted the company tends to apply uncoated carbide ballnose and other endmills to cut cobalt chrome, with some tools having a titanium-nitride coating for enhanced wear resistance. When the metal’s hardness makes it too much of a pain to mill or turn, or part features are too small or delicate for those machines, the shop will wire or sinker EDM it. “That way you don’t have to worry about a very small cutting tool that just wants to ping right off once it touches the part,” he said.
In the Cut
The challenge of cutting cobalt chrome is compounded when the workpiece has hard, abrasive intermetallic compounds in its microstructure. “The hard spots are about 58 HRC,” said Matt Dahms, founder and president of Oak View Tool Co. LLC. “That’s the problem.”
To enhance efficiency when cutting medical-grade cobalt chrome, the Columbia City, Ind.-based toolmaker developed the Ortho-Cut “CC” series of endmills. Oak View Tool also makes CC specials, such as keyway, form and dovetail cutters. “The series is designed for cobalt chrome and those types of tough materials that workharden and tear up a typical tool,” Dahms said.
Because cobalt chrome can workharden, CC tools have an edge prep combined with an effective shear angle, Dahms explained. “It’s so tough of a material, you have to hit it with the best of both worlds.”
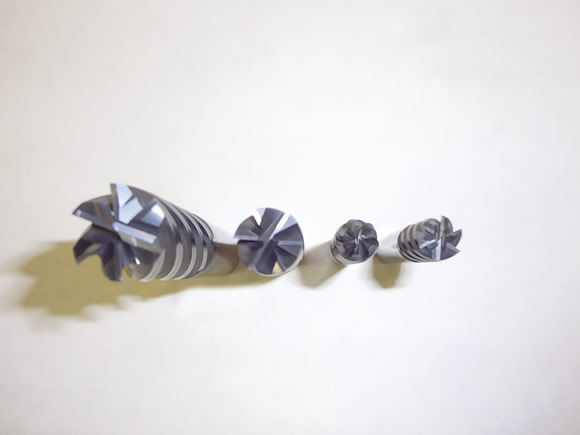
Courtesy of Oak View Tool
Oak View Tool designed its Ortho-Cut “CC” series endmills for machining medical-grade cobalt chrome. They are available with corner radii for added rigidity or for matching the size of the part feature.
The endmills also have unequal index geometry to minimize vibration and corresponding chatter. They have a carbide substrate with at least 10 percent cobalt to enhance tool toughness. The tools can be coated with aluminum titanium nitride or ordered uncoated if the orthopedic company has not yet validated the toolmaker’s coating, Dahms noted. He added that the coating, however, can extend tool life at least 30 percent. “The substrate, coating, geometry and edge prep are key,” he said. “If you’ve got those four things figured out, you can make the tools work really well.”
Jim Hoffman, director of manufacturing for Oberg Medical, Freeport, Pa., emphasized the importance of a tool’s corner radius. “You’re not going to go in there with a sharp-corner tool,” he said. “It just breaks down too quickly.”
To minimize workhardening and the damage it can cause to even a properly designed cutting tool, the tool must be kept loaded and continue to shear the workpiece rather than rub it, according to Hoffman. “You have to bite into the material, but you cannot sit there and dwell,” he said. “You have to stay in the cut.”
After machining a few parts for a job, Oberg has captured enough data to understand the process, making it a predictable job, Hoffman pointed out. Operators can then access the tool-life management data and change tools as needed based on the number of parts or minutes a previous tool lasted.
Hoffman noted cobalt chrome’s abrasiveness dulls cutting edges, but doesn’t typically cause them to chip or break. A degraded surface finish is the telltale sign of a worn tool, he explained, adding that most implants require a 20 µin. Ra finish off the machine to allow polishing to a 2 µin. Ra finish if required by the customer. Oberg regrinds worn tools, but to ensure quality, the company doesn’t use them to machine other implants.
The types of tool wear typically seen include abrasive, crater and notch, according to Judson A. Smith’s Moser. Abrasive wear is primarily the result of hard particles in the workpiece rubbing or grinding the cutting edge. Crater wear occurs when hard-particle grinding removes tool material from the chip face, and can be remedied by selecting a positive geometry and reducing the speed to lower the temperature in the cut. Notch wear is concentrated at a tool’s DOC and generates burrs.
Compared to other difficult-to-cut materials, such as 17-4 precipitation-hardened stainless steel, Hoffman said Oberg might cut surgical implant-grade cobalt chrome 40 to 50 percent slower because it’s more challenging. Generally, the surface speed is about 200 sfm and the feed rate from 0.0004 to 0.005 ipt, depending on the DOC, when applying a 3- or 4-flute endmill.
Hold On
Cobalt-chrome alloys are available as bar stock and can be cast into complex near-net shapes. The cast blank requires less material removal, but has a tough skin to get through or an inconsistent composition throughout the casting or both, noted Oak View Tool’s Dahms.
“Bar stock is like butter compared to castings,” Dahms said. “The castings seem to vary, and when it’s that tough of a material, just a little difference makes a big difference.” He added that the tools used for a cast application have stronger edge prep.
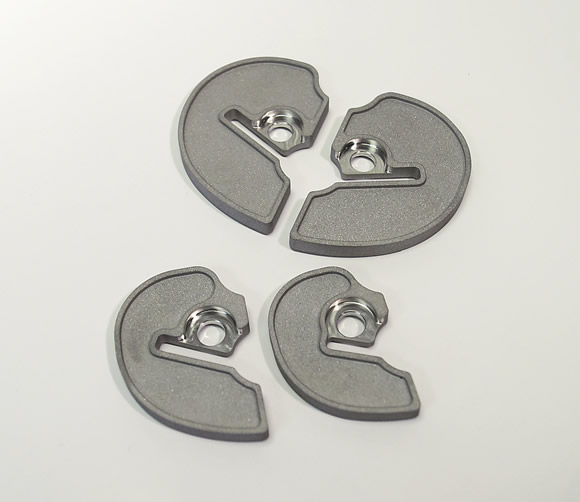
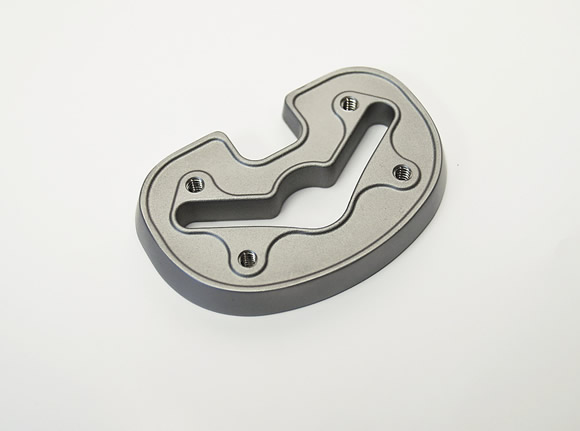
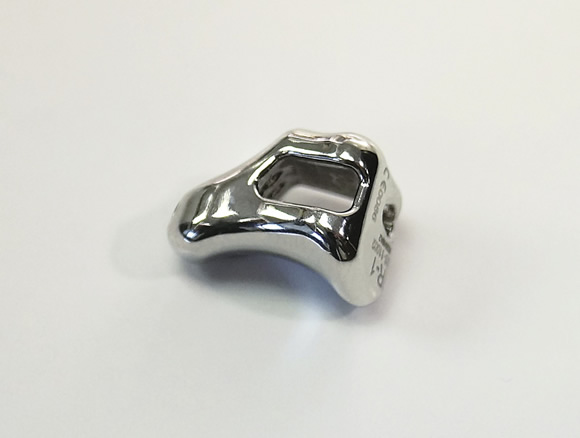
Courtesy of Oberg Medical
Oberg Medical produces an array of cobalt-chrome medical parts. From top to bottom: tibial augments used in knee replacements, a full tibial augment primarily used in total knee-revision surgery, and a trapezium implant used in the hand to replace the joint that controls thumb movement.
Oberg machines cobalt-chrome bar stock and castings and one challenge the company faces is securely holding the castings during machining. The near-net shapes have complex contours and typically there is no flat surface to grasp, Hoffman explained. As a result, the company spends a good deal of time designing and building fixtures to enable rigid workholding.
“At the end of the day, everybody has access to the machines, everybody has access to the cutting tools, but what makes or breaks your approach is the process itself and the workholding,” he said.
Hoffman added that Oberg creates the datum structure in the parts so the features that are held are held consistently throughout every step of the operation, including when a part moves from one machine to another. Therefore, variability is not introduced into the process.
Going a step further to ensure repeatability when machining cobalt-chrome and other parts, Moser said Judson A. Smith uses workholding receivers, including ones from Hirschmann, Erowa and System 3R. The receivers can be transferred from machine to machine, such as from a milling machine to a wire EDM, without removing the part from the fixture. “You also have the ease of knowing where your datums are and not having to try to find a datum,” he said.
When holding the cutting tool itself, Dahms recommends toolholders that minimize total indicator runout when machining cobalt chrome. “Shrink fit is the perfect world,” he said, adding that high-quality milling chucks are suitable. “Those chucks are much better than the standard Weldon-flat, slip-fit holders. That’s out and old school.” With the correct tool geometry, tool pullout is not an issue, according to Dahms.
Hoffman agreed that shrink-fit holders work well when cutting cobalt chrome. “Everything we machine from the medical side is HSK 63, all Haimer shrink fit,” he said. “This allows us to maintain a 0.0001 " TIR on our cutting tools, which is vital for achieving fine surface finishes and improved tool life when cutting cobalt chrome.”
Chipping Away
After a cobalt-chrome chip is produced, it’s critical to evacuate it from the tool so the heat in the chip doesn’t penetrate the tool, Moser pointed out. He added that he judges if the process is creating proper chips by their color and looks for a tan to bluish-black shade.
To control chips, Dahms recommends the radial chip thinning technique, especially when applying Oak View Tool’s CC series endmills, which have at least six shallow-depth flutes.
Radial chip thinning is the effect of taking a radial WOC less than 25 percent of the milling tool’s diameter. The chip thickness based on the calculated feed per tooth will diminish as the radial width decreases, resulting in a lighter actual feed per tooth. This causes the tool to rub the workpiece rather than cut it, so the feed needs to be increased as the radial depth decreases. The result is a lower temperature at the tool/workpiece interface, a decrease in cycle times and longer tool life.
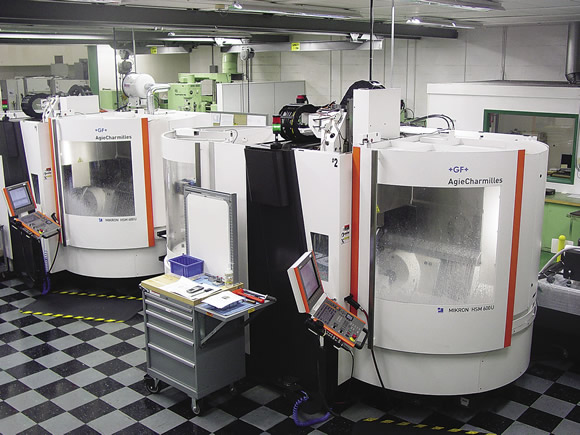
Courtesy of Oberg Medical
Oberg Medical uses high-speed machines from GF AgieCharmilles to produce some of its cobalt-chrome medical parts.
“We do light step-overs with full-flute depths to try to buzz the material off quickly,” Dahms said. “It gets the surface footage back up to where the heat is right for the coating. Also, we get a high enough feed rate to make parts fast enough, so everybody is excited.”
In addition, Dahms promotes using the full-flute length when machining cobalt chrome, and noted Oak View Tool designed the CC series tools to handle that type of cutting. “A lot of people do surfacing where they’ll use Z-level depths to remove material,” he said. “We want to get in and out quickly, because every time you use a Z-level depth, you’re putting more heat into the part and getting workhardening.”
Regardless of the machining methods, cobalt chrome’s high cost makes scrap unacceptable, and up-front process design is critical to producing good parts, according to Oberg’s Hoffman. What shouldn’t be considered an unnecessary expense is the cost premium for high-performance cutting tools to effectively cut the metal.
“You can try to cut tool costs but you’ll lose money in scrap and just induce more risk in terms of more tool changes and tool adjustments, tool breakage, poor surface finishes and rework. We’ve seen all of that happen if not using the right cutting tool,” Hoffman said. “I tell my guys all the time: Don’t step over a dollar to pick up a dime.”
Mendell Machine’s Storlie also understands the value of the right high-quality tool for the job. “Getting the proper tool is so critical because, if you don’t have it, you might only last 20 parts,” he said. “With the proper tool, you might get a few hundred parts.”
Nonetheless, tool selection is only one piece of the machining system puzzle. “What is most important to be successful is to have a robust process that incorporates effective workholding, a solid machining approach and the latest in cutting tool technology,” Hoffman emphasized. CTE
About the Author: Alan Richter is editor of CTE. He joined the publication in 2000. Contact him at (847) 714-0175 or [email protected].
Strategies for milling dental restorations
When milling understructures for dental restorations, titanium is often the workpiece of choice, but cobalt chrome is another option that offers advantages, according to Felix S. Chung, president/owner of Imagine Milling Technologies LLC, a Reston, Va.-based dental milling center.
Compared to titanium, cobalt chrome infuses more effectively with other materials, such as a ceramic or composites, which covers the understructure and makes the restoration look more aesthetically pleasing. “You mimic the natural tooth color,” Chung said. “Titanium doesn’t have very good bonding with porcelain, so some people stay away from using it.”
According to Chung, cobalt chrome is also not as challenging to machine as titanium because titanium chips don’t effectively absorb and transport heat away from the tool/workpiece interface. This means coolant is typically required. Cobalt chrome, on the other hand, can be machined dry, he pointed out, adding that the company applies a silicone-based cooling agent when producing titanium restorations on its Datron dental milling machine. “There’s not a lot of water mixture with it,” Chung said, “and that [cooling agent] can get very messy.”
The majority of the cutting tools used by Imagine for machining cobalt chrome are coated, 2-flute, ballnose endmills, ranging in diameter from 0.5mm to 3mm, with neck lengths from 4mm to 14mm. Spindle speeds range from 15,000 to 35,000 rpm, depending on tool diameter.
Chung emphasized the importance of keeping tool wear to a minimum when milling dental implants, which have tolerances as tight as 20µm.
In addition to machining titanium and cobalt chrome, Imagine also makes zirconia understructures, which require minimal material to be added because zirconia is similar to ceramic. Regardless of the workpiece material, each understructure has its own unique, organic shape to match the patient.
—A. Richter
Contributors
Core3dcentres USA
(888) 750-9204
www.core3dcentres.com
DMG Vertriebs und Service GmbH Deckel Maho Gildemeister
+49 8363 89 3140
www.gildemeister.com
Imagine Milling Technologies LLC
(888) 776-1119
www.imilling.com
Judson A. Smith Co.
(610) 367-2021
www.judsonsmith.com
Mendell Machine and Manufacturing Inc.
(952) 469-5500
www.mendell.com
Oak View Tool Co. LLC
(260) 244-7677
www.oakviewtool.com
Oberg Medical
(724) 295-2121
www.obergmedical.com
Ultrasonic machining for demanding dental applications
Las Vegas-based Core3dcentres USA is located near the Las Vegas Institute for Advanced Dental Studies, where restorative and cosmetic dental techniques are taught to practicing dentists and laboratory technicians.
At its facility, Core3dcentres prepares CAD files developed from data typically gathered with an iTero oral scanning wand or CAD files from scans of conventional dental impressions from a patient’s mouth, which are then digitally captured in a dental scanner. Software is used to image the impression, beginning the process of creating a crown, bridge, abutment, coping, implant or full denture restoration.
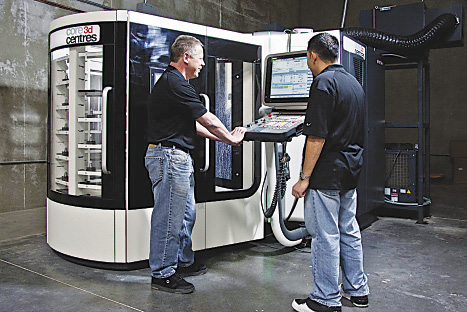
Courtesy of Core3dcentres USA
The DMG Sauer 20 ultrasonic machine with a robot loader at Core3dcentres has a Siemens Sinumerik 840D sl CNC. The CNC recognizes the workpiece pallet, which is coded by patient name to reportedly eliminate error.
The next step is translation of the digital impression to a RenShape mold, using conventional machine tools. Usually, the required structures are simultaneously designed, and then the mold with coping is sent to the DMG Sauer ultrasonic dental machine for preparation of the final structures. This is where Core3dcentres processes advanced and expensive substrates, such as cobalt chrome, ceramics, lithium disilicate and zirconia.
Tim McKimson, the company’s worldwide director of engineering, explained that the decision to cut ultrasonically rather than use other techniques was relatively easy, given the inherent wear conditions and high cost of conventional cutting tools. In the ultrasonic process, a combination of electrolysis and fluid lubrication act in concert to create an ionic attraction of particles, removing material in a predictable and accurate way, without the mechanical stress implicit in conventional machining.
“The process is more or less a grinding process,” said Dr. Uli Sutor, senior account manager for DMG Vertriebs und Service GmbH Deckel Maho Gildemeister, Pfronten, Germany. He added that the ultrasonic tools move 2µm to 4µm about 50,000 times a second and only remove material that’s sintered or harder than 62 HRC. “It is not possible in material like titanium.”
Blanks of material are loaded into the ultrasonic machine’s 66-position feeder station and delivered to the work zone by a Motoman robotic arm with Schunk pressure grippers.
According to Sutor, most of DMG’s ultrasonic machines are automated with either a robot or a linear magazine. “For the dental industry, complete 24/7 automation is available,” he said.
In detailing the accuracy of ultrasonic machining, McKimson noted each ultrasonic tool is obtained from a 25-position toolchanger and a Renishaw probe monitors its position. Technicians often load three sets of the tools needed for the 66-piece runs, ensuring virtually 24/7 unattended operation. According to McKimson, accuracies are from 2µm to 4µm, and process reliability has significantly reduced scrap.
When considering an ultrasonic machine, Sutor emphasized looking at the advantages of the equipment, such as extended tool life, high surface quality and accuracy. “If these points are interesting for you, the ultrasonic technology is a step forward for your company.”
Related Glossary Terms
- abrasive
abrasive
Substance used for grinding, honing, lapping, superfinishing and polishing. Examples include garnet, emery, corundum, silicon carbide, cubic boron nitride and diamond in various grit sizes.
- alloys
alloys
Substances having metallic properties and being composed of two or more chemical elements of which at least one is a metal.
- ceramics
ceramics
Cutting tool materials based on aluminum oxide and silicon nitride. Ceramic tools can withstand higher cutting speeds than cemented carbide tools when machining hardened steels, cast irons and high-temperature alloys.
- chatter
chatter
Condition of vibration involving the machine, workpiece and cutting tool. Once this condition arises, it is often self-sustaining until the problem is corrected. Chatter can be identified when lines or grooves appear at regular intervals in the workpiece. These lines or grooves are caused by the teeth of the cutter as they vibrate in and out of the workpiece and their spacing depends on the frequency of vibration.
- composites
composites
Materials composed of different elements, with one element normally embedded in another, held together by a compatible binder.
- computer numerical control ( CNC)
computer numerical control ( CNC)
Microprocessor-based controller dedicated to a machine tool that permits the creation or modification of parts. Programmed numerical control activates the machine’s servos and spindle drives and controls the various machining operations. See DNC, direct numerical control; NC, numerical control.
- computer-aided design ( CAD)
computer-aided design ( CAD)
Product-design functions performed with the help of computers and special software.
- coolant
coolant
Fluid that reduces temperature buildup at the tool/workpiece interface during machining. Normally takes the form of a liquid such as soluble or chemical mixtures (semisynthetic, synthetic) but can be pressurized air or other gas. Because of water’s ability to absorb great quantities of heat, it is widely used as a coolant and vehicle for various cutting compounds, with the water-to-compound ratio varying with the machining task. See cutting fluid; semisynthetic cutting fluid; soluble-oil cutting fluid; synthetic cutting fluid.
- electrical-discharge machining ( EDM)
electrical-discharge machining ( EDM)
Process that vaporizes conductive materials by controlled application of pulsed electrical current that flows between a workpiece and electrode (tool) in a dielectric fluid. Permits machining shapes to tight accuracies without the internal stresses conventional machining often generates. Useful in diemaking.
- endmill
endmill
Milling cutter held by its shank that cuts on its periphery and, if so configured, on its free end. Takes a variety of shapes (single- and double-end, roughing, ballnose and cup-end) and sizes (stub, medium, long and extra-long). Also comes with differing numbers of flutes.
- feed
feed
Rate of change of position of the tool as a whole, relative to the workpiece while cutting.
- fixture
fixture
Device, often made in-house, that holds a specific workpiece. See jig; modular fixturing.
- flat ( screw flat)
flat ( screw flat)
Flat surface machined into the shank of a cutting tool for enhanced holding of the tool.
- flutes
flutes
Grooves and spaces in the body of a tool that permit chip removal from, and cutting-fluid application to, the point of cut.
- gang cutting ( milling)
gang cutting ( milling)
Machining with several cutters mounted on a single arbor, generally for simultaneous cutting.
- grinding
grinding
Machining operation in which material is removed from the workpiece by a powered abrasive wheel, stone, belt, paste, sheet, compound, slurry, etc. Takes various forms: surface grinding (creates flat and/or squared surfaces); cylindrical grinding (for external cylindrical and tapered shapes, fillets, undercuts, etc.); centerless grinding; chamfering; thread and form grinding; tool and cutter grinding; offhand grinding; lapping and polishing (grinding with extremely fine grits to create ultrasmooth surfaces); honing; and disc grinding.
- hardness
hardness
Hardness is a measure of the resistance of a material to surface indentation or abrasion. There is no absolute scale for hardness. In order to express hardness quantitatively, each type of test has its own scale, which defines hardness. Indentation hardness obtained through static methods is measured by Brinell, Rockwell, Vickers and Knoop tests. Hardness without indentation is measured by a dynamic method, known as the Scleroscope test.
- inches per tooth ( ipt)
inches per tooth ( ipt)
Linear distance traveled by the cutter during the engagement of one tooth. Although the milling cutter is a multi-edge tool, it is the capacity of each individual cutting edge that sets the limit of the tool, defined as: ipt = ipm/number of effective teeth 5 rpm or ipt = ipr/number of effective teeth. Sometimes referred to as the chip load.
- microstructure
microstructure
Structure of a metal as revealed by microscopic examination of the etched surface of a polished specimen.
- milling
milling
Machining operation in which metal or other material is removed by applying power to a rotating cutter. In vertical milling, the cutting tool is mounted vertically on the spindle. In horizontal milling, the cutting tool is mounted horizontally, either directly on the spindle or on an arbor. Horizontal milling is further broken down into conventional milling, where the cutter rotates opposite the direction of feed, or “up” into the workpiece; and climb milling, where the cutter rotates in the direction of feed, or “down” into the workpiece. Milling operations include plane or surface milling, endmilling, facemilling, angle milling, form milling and profiling.
- milling machine ( mill)
milling machine ( mill)
Runs endmills and arbor-mounted milling cutters. Features include a head with a spindle that drives the cutters; a column, knee and table that provide motion in the three Cartesian axes; and a base that supports the components and houses the cutting-fluid pump and reservoir. The work is mounted on the table and fed into the rotating cutter or endmill to accomplish the milling steps; vertical milling machines also feed endmills into the work by means of a spindle-mounted quill. Models range from small manual machines to big bed-type and duplex mills. All take one of three basic forms: vertical, horizontal or convertible horizontal/vertical. Vertical machines may be knee-type (the table is mounted on a knee that can be elevated) or bed-type (the table is securely supported and only moves horizontally). In general, horizontal machines are bigger and more powerful, while vertical machines are lighter but more versatile and easier to set up and operate.
- milling machine ( mill)2
milling machine ( mill)
Runs endmills and arbor-mounted milling cutters. Features include a head with a spindle that drives the cutters; a column, knee and table that provide motion in the three Cartesian axes; and a base that supports the components and houses the cutting-fluid pump and reservoir. The work is mounted on the table and fed into the rotating cutter or endmill to accomplish the milling steps; vertical milling machines also feed endmills into the work by means of a spindle-mounted quill. Models range from small manual machines to big bed-type and duplex mills. All take one of three basic forms: vertical, horizontal or convertible horizontal/vertical. Vertical machines may be knee-type (the table is mounted on a knee that can be elevated) or bed-type (the table is securely supported and only moves horizontally). In general, horizontal machines are bigger and more powerful, while vertical machines are lighter but more versatile and easier to set up and operate.
- polishing
polishing
Abrasive process that improves surface finish and blends contours. Abrasive particles attached to a flexible backing abrade the workpiece.
- titanium nitride ( TiN)
titanium nitride ( TiN)
Added to titanium-carbide tooling to permit machining of hard metals at high speeds. Also used as a tool coating. See coated tools.
- toolchanger
toolchanger
Carriage or drum attached to a machining center that holds tools until needed; when a tool is needed, the toolchanger inserts the tool into the machine spindle. See automatic toolchanger.
- total indicator runout ( TIR)
total indicator runout ( TIR)
Combined variations of all dimensions of a workpiece, measured with an indicator, determined by rotating the part 360°.
- total indicator runout ( TIR)2
total indicator runout ( TIR)
Combined variations of all dimensions of a workpiece, measured with an indicator, determined by rotating the part 360°.
- ultrasonic machining
ultrasonic machining
Material-removal operation in which an abrasive slurry flows between a tool, vibrating at a high frequency, and a workpiece.
- wear resistance
wear resistance
Ability of the tool to withstand stresses that cause it to wear during cutting; an attribute linked to alloy composition, base material, thermal conditions, type of tooling and operation and other variables.
- wire EDM
wire EDM
Process similar to ram electrical-discharge machining except a small-diameter copper or brass wire is used as a traveling electrode. Usually used in conjunction with a CNC and only works when a part is to be cut completely through. A common analogy is wire electrical-discharge machining is like an ultraprecise, electrical, contour-sawing operation.
- workhardening
workhardening
Tendency of all metals to become harder when they are machined or subjected to other stresses and strains. This trait is particularly pronounced in soft, low-carbon steel or alloys containing nickel and manganese—nonmagnetic stainless steel, high-manganese steel and the superalloys Inconel and Monel.