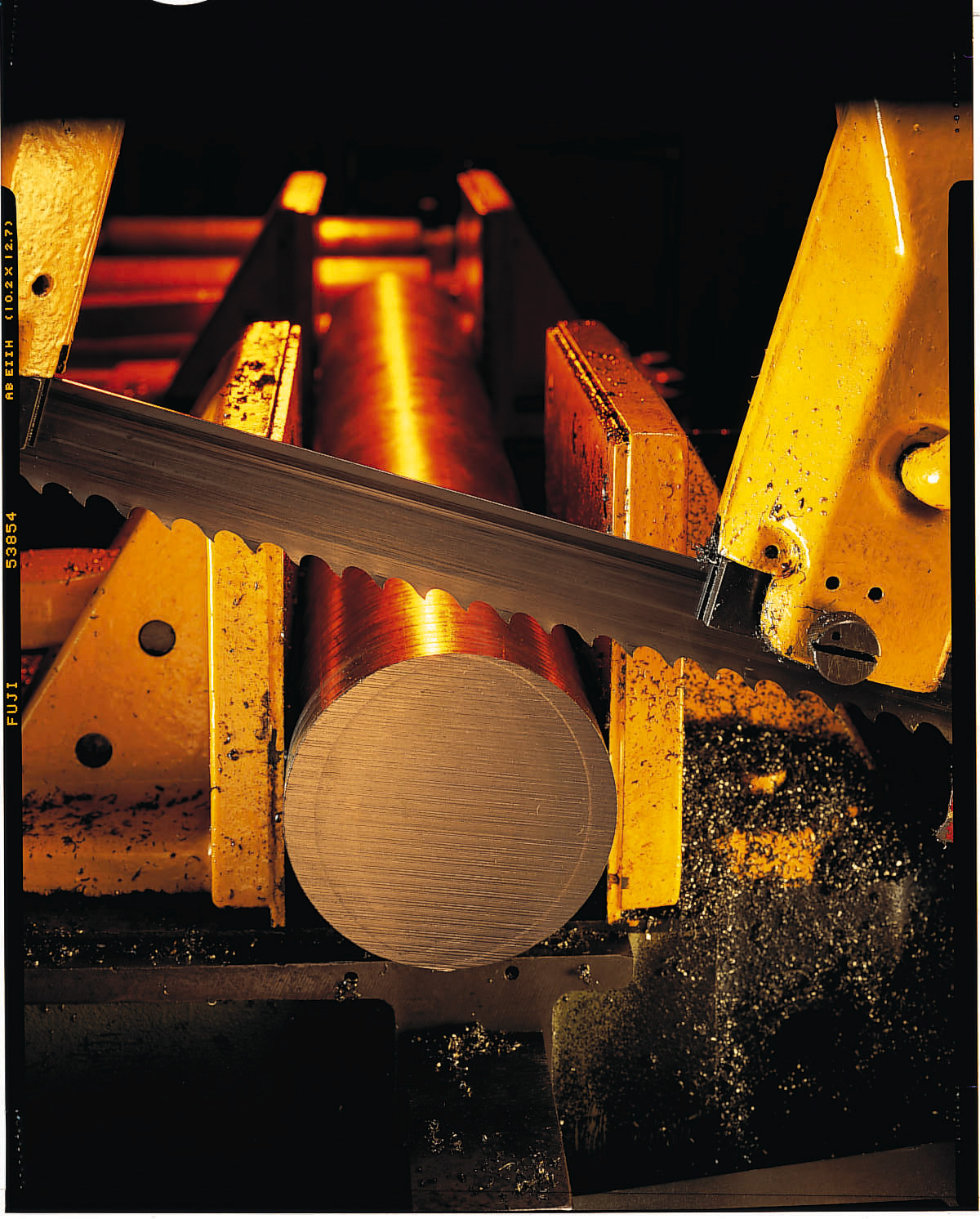
Burton Mill Solutions has acquired Oregon Industrial, based in Eugene, Oregon.
Oregon Industrial is a bandsaw blade weld center, specializing in precision tooth matching for nearly 90 years. This acquisition expands Burton Mill Solutions’ ability to continue pushing the boundaries of excellence in custom cutting tools.
The company said that thanks to this new team of expert welders, Burton will be able to supply metal cutting bands that meet the most stringent factory specifications for tough metals and abrasive surfaces. The continued use of the same state-of-the-art equipment and the same experienced Oregon Industrial professionals will ensure the same exceptional quality and service.
“We are delighted to join forces with Oregon Industrial Bandsaw. The addition of the narrow band welding service, and all the employees that have contributed to its success, will allow us to better serve the secondary markets in the U.S. West,” said senior vice president Chuck Wert.
As part of this transition, Oregon Industrial will be relocating to the Burton Mill Solutions facility across town in Springfield, Oregon, where it will be integrated into existing operations to the benefit of existing and future customers.
Related Glossary Terms
- abrasive
abrasive
Substance used for grinding, honing, lapping, superfinishing and polishing. Examples include garnet, emery, corundum, silicon carbide, cubic boron nitride and diamond in various grit sizes.
- bandsaw
bandsaw
Machine that utilizes an endless band, normally with serrated teeth, for cutoff or contour sawing. See saw, sawing machine.
- bandsaw blade ( band)
bandsaw blade ( band)
Endless band, normally with serrated teeth, that serves as the cutting tool for cutoff or contour band machines.
- bandsaw blade ( band)2
bandsaw blade ( band)
Endless band, normally with serrated teeth, that serves as the cutting tool for cutoff or contour band machines.
- chuck
chuck
Workholding device that affixes to a mill, lathe or drill-press spindle. It holds a tool or workpiece by one end, allowing it to be rotated. May also be fitted to the machine table to hold a workpiece. Two or more adjustable jaws actually hold the tool or part. May be actuated manually, pneumatically, hydraulically or electrically. See collet.
- milling machine ( mill)
milling machine ( mill)
Runs endmills and arbor-mounted milling cutters. Features include a head with a spindle that drives the cutters; a column, knee and table that provide motion in the three Cartesian axes; and a base that supports the components and houses the cutting-fluid pump and reservoir. The work is mounted on the table and fed into the rotating cutter or endmill to accomplish the milling steps; vertical milling machines also feed endmills into the work by means of a spindle-mounted quill. Models range from small manual machines to big bed-type and duplex mills. All take one of three basic forms: vertical, horizontal or convertible horizontal/vertical. Vertical machines may be knee-type (the table is mounted on a knee that can be elevated) or bed-type (the table is securely supported and only moves horizontally). In general, horizontal machines are bigger and more powerful, while vertical machines are lighter but more versatile and easier to set up and operate.