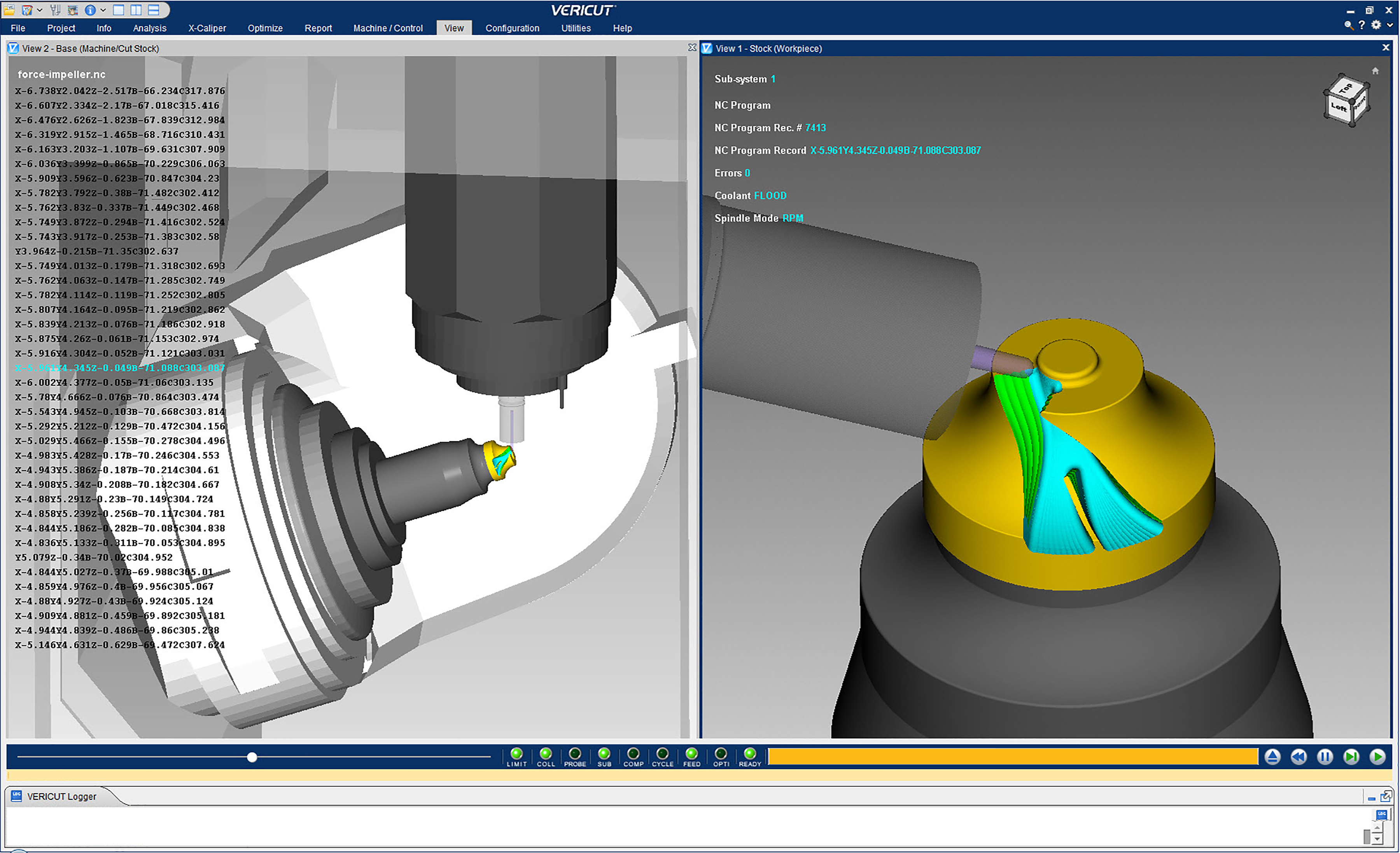
Irvine, CA - CGTech Technical Support Engineers will be on hand at the National Leadership and Skills Conference (NLSC) in Louisville, KY, June 25-27. Each year, CGTech staff proctor multiple SkillsUSA/NIMS competitions related to Computer Numeric Control (CNC) machining. In addition to grading competitions, CGTech will run its latest version of VERICUT CNC simulation software, in Booth S145.
The weeklong event is expected to draw more than 18,000 participants including students, teachers, and business partners. The event is designed to help prepare students for the workforce.
“This is a great opportunity for students to help prepare students for employment in CNC programming, and also see where their skill level is compared to their peers,” said Steve Arteman, CGTech Technical Support Engineer.
Participants will be graded by CGTech in two categories: CNC Milling and CNC Lathe machine operations. Each category will be evaluated to measure the contestant’s level of understanding and preparation of CNC programs. The contest assesses real world scenarios such as the ability to write CNC programs, interpret prints, and measure/gage parts. Participants will also demonstrate theoretical knowledge of CNC machine configuration, setup, and operations.
VERICUT software will be used to evaluate the accuracy of the participant’s NC programs created, while ensuring their programs run without violating safety standards or damaging machines. After each student’s NC program has been simulated, the virtual workpiece will be compared to the original design model.
CGTech’s VERICUT machine simulation software detects collisions and near-misses between all machine tool components such as axis slides, heads, turrets, rotary tables, spindles, tool changers, fixtures, workpieces, cutting tools, and other user-defined objects.
Contact Details
Related Glossary Terms
- computer numerical control ( CNC)
computer numerical control ( CNC)
Microprocessor-based controller dedicated to a machine tool that permits the creation or modification of parts. Programmed numerical control activates the machine’s servos and spindle drives and controls the various machining operations. See DNC, direct numerical control; NC, numerical control.
- gang cutting ( milling)
gang cutting ( milling)
Machining with several cutters mounted on a single arbor, generally for simultaneous cutting.
- lathe
lathe
Turning machine capable of sawing, milling, grinding, gear-cutting, drilling, reaming, boring, threading, facing, chamfering, grooving, knurling, spinning, parting, necking, taper-cutting, and cam- and eccentric-cutting, as well as step- and straight-turning. Comes in a variety of forms, ranging from manual to semiautomatic to fully automatic, with major types being engine lathes, turning and contouring lathes, turret lathes and numerical-control lathes. The engine lathe consists of a headstock and spindle, tailstock, bed, carriage (complete with apron) and cross slides. Features include gear- (speed) and feed-selector levers, toolpost, compound rest, lead screw and reversing lead screw, threading dial and rapid-traverse lever. Special lathe types include through-the-spindle, camshaft and crankshaft, brake drum and rotor, spinning and gun-barrel machines. Toolroom and bench lathes are used for precision work; the former for tool-and-die work and similar tasks, the latter for small workpieces (instruments, watches), normally without a power feed. Models are typically designated according to their “swing,” or the largest-diameter workpiece that can be rotated; bed length, or the distance between centers; and horsepower generated. See turning machine.
- milling
milling
Machining operation in which metal or other material is removed by applying power to a rotating cutter. In vertical milling, the cutting tool is mounted vertically on the spindle. In horizontal milling, the cutting tool is mounted horizontally, either directly on the spindle or on an arbor. Horizontal milling is further broken down into conventional milling, where the cutter rotates opposite the direction of feed, or “up” into the workpiece; and climb milling, where the cutter rotates in the direction of feed, or “down” into the workpiece. Milling operations include plane or surface milling, endmilling, facemilling, angle milling, form milling and profiling.
- numerical control ( NC)
numerical control ( NC)
Any controlled equipment that allows an operator to program its movement by entering a series of coded numbers and symbols. See CNC, computer numerical control; DNC, direct numerical control.