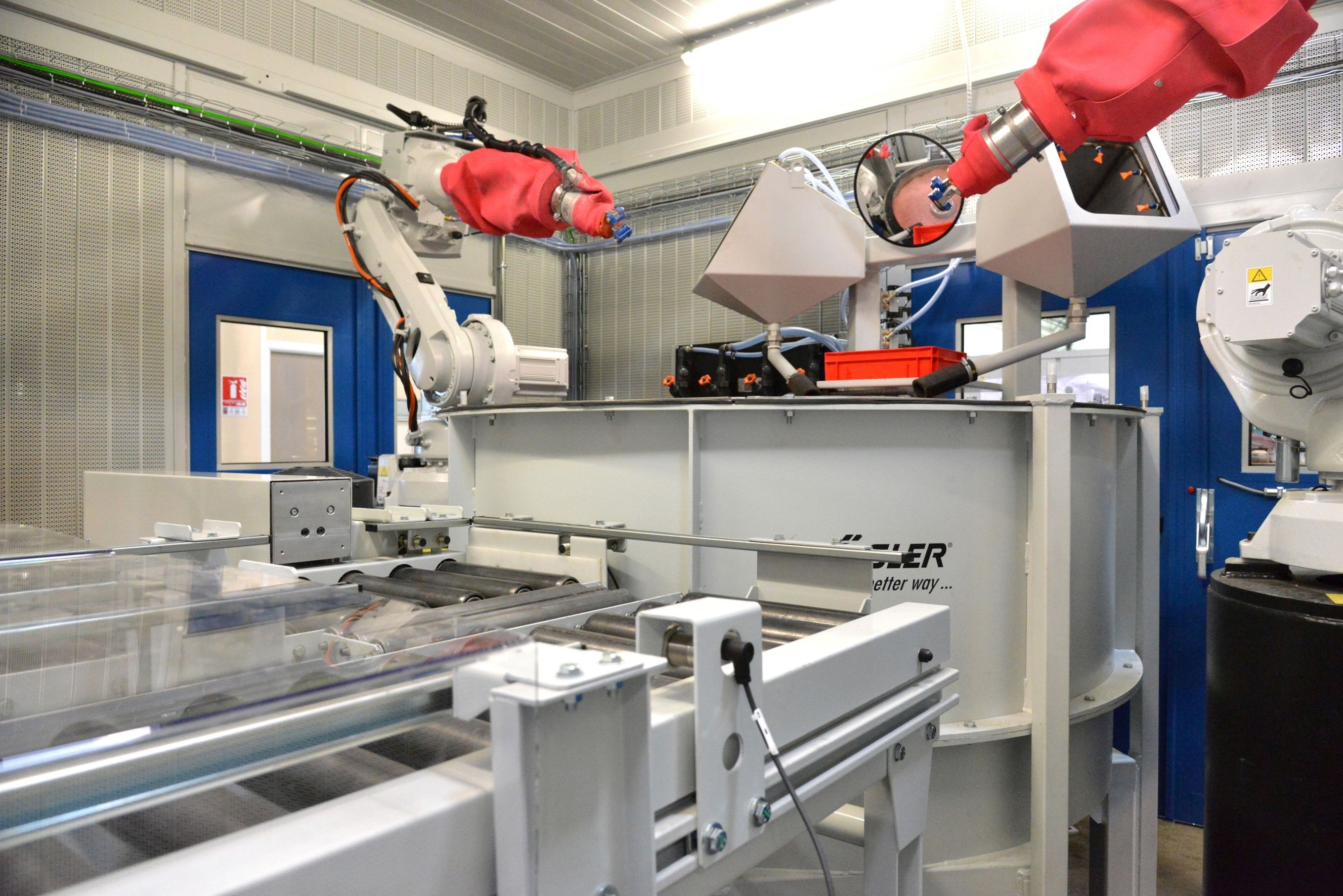
For today’s manufacturers of precision components, there’s no getting around deburring, rounding and polishing. These production steps are often seen as a necessary evil due to the high costs associated with them in some cases. Use of the right technology permits reliable processing at reduced costs.
It’s practically impossible to fully avoid the occurrence of burrs when using any of the traditional metalworking processes. Due to the fact that these manufacturing or processing remnants represent a risk from both a functional and an ergonomic standpoint, they have to be removed. As was also the case in days of old, this is not infrequently still done manually. Quite apart from the fact that the necessary process reliability and reproducibility is not assured, this manual work results in high costs and often leads to time-consuming rework – in both cases at the expense of economic efficiency and the company’s competitive edge. And thus it’s no wonder that deburring, rounding and polishing are often seen as a necessary and costly evil.
Process Reliability and Costs – a Question of the Process
More and more demanding requirements for process reliability in production and product quality, as well as cost pressure in global competition, necessitate more economic efficiency for the manufacturing steps of deburring, rounding and polishing. At the same time, uniform high quality must be assured in a reproducible manner. Various processes have established themselves to this end, for example automated brush deburring, deburring with special tooling which is integrated into the machining centres, barrel finishing and high-pressure water jets. Many of these processes have been further developed in recent years, and new technologies have been introduced to the market as well.
A New Dimension of Barrel Finishing
Various developments such as drag finishing and so-called surf, or stream, finishing make reliable and economical lot processing by means of barrel finishing possible for parts which are sensitive to damage and could previously only be deburred, ground, polished or smoothed by means of a costly, nonreproducible manual procedure or at great expense with the help of a machine.
In the case of drag finishing, the parts are clamped to workpiece carriers which are then dragged through a barrel with abrasive particles or a polishing medium. Uniform flow of the abrasive particles or polishing medium around all sides of the workpieces results in effective but nevertheless gentle processing. Even in the case of workpieces with complex geometries, ideal, reproducible processing results of “handmade quality” can be achieved within a relatively short period of time.
Surf finishing goes one step further. A robot immerses the workpiece at a precisely defined position into the rotating bowl which is filled with grinding medium, and accurately guides it. This makes it possible to selectively process certain areas, or different radii can be achieved by variously positioning the robot arm. High grinding pressure is generated by rotating the bowl while the component is surfing in the grinding medium. This results in intensive, reliable processing with short cycle times and a surface finish which complies with the specified requirement.
Reliably Removing Thousands of Burrs in a Matter of Just Seconds
Not every burr on a geometrically complex workpiece is easy to reach. Thermal energy machining (TEM) makes it possible to remove burrs reliably, efficiently and with consistently high quality where mechanical processing would be either uneconomical or not possible at all. It’s suitable for components made of nearly all metallic materials and thermoplastics from which internal as well as external burrs need to be removed – even from very difficult to access places.
The parts are positioned inside a bell-shaped chamber for the deburring process, which is hermetically sealed. A precisely defined mixture of gases (e.g. oxygen and methane) is fed to the chamber by means of a gas metering system. It flows through the entire component, or the complete batch. Upon ignition of the gas mixture, burning ensues resulting in temperatures ranging from 2,500 to 3,300 degrees C. The burrs reach ignition temperature and react with the excess oxygen. This causes complete combustion of all burrs within approximately 20 ms, and their roots are also sealed as a result. Because the process lasts just a few milliseconds, the workpieces are only heated up insignificantly. No material is removed from the surface. Overall cycle time is usually less than 2 minutes.
TEM makes it possible to achieve “sharp-edged/burr-free” deburring quality. Depending on the material, slight rounding of the edges is also possible. Use of this process is limited by the size of the part, as well as in the event that targeted edge rounding needs to be achieved during deburring.
TEM systems with rectangular deburring chambers are a new development. They are used, for example, to deburr die-cast zinc and aluminium parts as bulk goods. Parts handling is significantly simplified and accelerated as a result, because the loaded container can be transferred directly to a parts cleaning system after TEM deburring. Another possible application for systems with rectangular chambers is the deburring of aluminium cylinder heads.
Deburring with Additional Function
Contactless electrochemical machining (ECM) demonstrates its strengths in this respect. The process is based on the principle of electrolysis. A cathodic electrode used as a tool is connected to a source of direct current. The other electrode is the anodic workpiece itself. A charge exchange between the cathode and the workpiece takes place in an aqueous electrolyte solution and processes the workpiece in a targeted fashion. On the one hand, this makes it possible to reliably deburr difficult to access areas such as edges, undercuts, internal bore intersections and pockets at precisely defined location on the workpiece. Casting, press moulding and forging flash can also be removed. On the other hand, ECM also makes it possible to produce, for example, highly precise contours, ducts, slots and hollows in a reproducible manner without any thermal or mechanical stressing. And thus the ECM process fulfils the more and more frequently specified requirement for burr-free processing – with a high quality surface finish as well.
This is also one of the characteristics of abrasive flow machining, by means of which Ra values off less than 0.01 µm can be achieved. The process is used for economically efficient deburring, edge rounding and polishing of internal and external surfaces of demanding components from the automotive and aviation industries, turbine manufacturing, medical and fluid engineering, food processing, mould and toolmaking, general machinery manufacturing and other industry sectors. Processing is accomplished by means of abrasive particles, the type, size and concentration of which are matched to the respective task, and which are embedded in a polymer plastic mass of defined viscosity. This grinding medium is caused to flow through or over the area of the component to be deburred in alternating directions at a defined pressure level by means of hydraulically powered pistons.
Deburring, cleaning, rounding and hardening of the surface in a single step is made possible by the so-called Pinflow process. The workpieces to be processed are clamped in a part-specific fixture which is laid out as a container, is filled with a processing medium (small steel balls) and is located in the machine’s process chamber. Vibrators then cause the fixture to oscillate horizontally, thus resulting in relative motion between the workpiece and the deburring medium. The resultant kinetic energy of the steel balls is transferred to the workpiece in order to process its external and internal surfaces, and the deburring effect is also apparent in difficult to access places.
DeburringEXPO: Trade Fair for Deburring Technology and Precision Surface Finishing
Which processes ensure efficient deburring and surface finishing with good process reliability? Which new technologies are available for deburring, rounding and polishing? Which measures contribute to the reduced formation of burrs? Answers to these and many other questions are provided by DeburringEXPO. With its technical trade fair for deburring technologies and precision surface finishing, fairXperts GmbH & Co. KG has created a platform at which users from all industry sectors can gather comprehensive information about relevant technologies. The 2nd DeburringEXPO will take place at the Karlsruhe Exhibition Centre from the 10th through the 12th of October, 2017. The exhibition portfolio includes equipment, systems and tools for belt grinding, brushing, abrasive flow machining, vibratory grinding, blasting with solid and liquid media, abrasive water-jet blasting, magnetic-abrasive deburring, ultrasonic deburring, chemical bath deburring, electrochemical machining (ECM), electron beam machining, thermal energy machining (TEM), mechanical deburring, buffing, polish honing, electrolytic polishing, plasma polishing, laser polishing, immersion and brush polishing, as well as measuring, test and analysis systems, and technical literature. Further information is available at www.deburring-expo.de.
Related Glossary Terms
- abrasive
abrasive
Substance used for grinding, honing, lapping, superfinishing and polishing. Examples include garnet, emery, corundum, silicon carbide, cubic boron nitride and diamond in various grit sizes.
- abrasive flow machining
abrasive flow machining
Finishing and deburring operation for holes, inaccessible areas or restricted passages. Done by clamping the workpiece in a fixture, then extruding semisolid abrasive media through the passage. Often, multiple parts are loaded into a single fixture and finished simultaneously.
- barrel finishing
barrel finishing
Mass finishing process that involves low-pressure abrasion resulting from tumbling workpieces in a barrel (usually of hexagonal or octagonal cross section) together with an abrasive slurry. See finishing.
- brushing
brushing
Generic term for a curve whose shape is controlled by a combination of its control points and knots (parameter values). The placement of the control points is controlled by an application-specific combination of order, tangency constraints and curvature requirements. See NURBS, nonuniform rational B-splines.
- buffing
buffing
Use of rapidly spinning wires or fibers to effectively and economically remove burrs, scratches and similar mechanical imperfections from precision and highly stressed components. The greatest application is in the manufacture of gears and bearing races where the removal of sharp edges and stress risers by power methods has increased the speed of the operation.
- burning
burning
Rotary tool that removes hard or soft materials similar to a rotary file. A bur’s teeth, or flutes, have a negative rake.
- burr
burr
Stringy portions of material formed on workpiece edges during machining. Often sharp. Can be removed with hand files, abrasive wheels or belts, wire wheels, abrasive-fiber brushes, waterjet equipment or other methods.
- electrochemical machining ( ECM)
electrochemical machining ( ECM)
Operation in which electrical current flows between a workpiece and conductive tool through an electrolyte. Initiates a chemical reaction that dissolves metal from the workpiece at a controlled rate. Unlike with traditional cutting methods, workpiece hardness is not a factor, making ECM suitable for difficult-to-machine materials. Takes such forms as electrochemical grinding, electrochemical honing and electrochemical turning.
- electrochemical machining ( ECM)2
electrochemical machining ( ECM)
Operation in which electrical current flows between a workpiece and conductive tool through an electrolyte. Initiates a chemical reaction that dissolves metal from the workpiece at a controlled rate. Unlike with traditional cutting methods, workpiece hardness is not a factor, making ECM suitable for difficult-to-machine materials. Takes such forms as electrochemical grinding, electrochemical honing and electrochemical turning.
- fixture
fixture
Device, often made in-house, that holds a specific workpiece. See jig; modular fixturing.
- flash
flash
Thin web or film of metal on a casting that occurs at die partings and around air vents and movable cores. This excess metal is due to necessary working and operating clearances in a die. Flash also is the excess material squeezed out of the cavity as a compression mold closes or as pressure is applied to the cavity.
- grinding
grinding
Machining operation in which material is removed from the workpiece by a powered abrasive wheel, stone, belt, paste, sheet, compound, slurry, etc. Takes various forms: surface grinding (creates flat and/or squared surfaces); cylindrical grinding (for external cylindrical and tapered shapes, fillets, undercuts, etc.); centerless grinding; chamfering; thread and form grinding; tool and cutter grinding; offhand grinding; lapping and polishing (grinding with extremely fine grits to create ultrasmooth surfaces); honing; and disc grinding.
- hardening
hardening
Process of increasing the surface hardness of a part. It is accomplished by heating a piece of steel to a temperature within or above its critical range and then cooling (or quenching) it rapidly. In any heat-treatment operation, the rate of heating is important. Heat flows from the exterior to the interior of steel at a definite rate. If the steel is heated too quickly, the outside becomes hotter than the inside and the desired uniform structure cannot be obtained. If a piece is irregular in shape, a slow heating rate is essential to prevent warping and cracking. The heavier the section, the longer the heating time must be to achieve uniform results. Even after the correct temperature has been reached, the piece should be held at the temperature for a sufficient period of time to permit its thickest section to attain a uniform temperature. See workhardening.
- metalworking
metalworking
Any manufacturing process in which metal is processed or machined such that the workpiece is given a new shape. Broadly defined, the term includes processes such as design and layout, heat-treating, material handling and inspection.
- polishing
polishing
Abrasive process that improves surface finish and blends contours. Abrasive particles attached to a flexible backing abrade the workpiece.