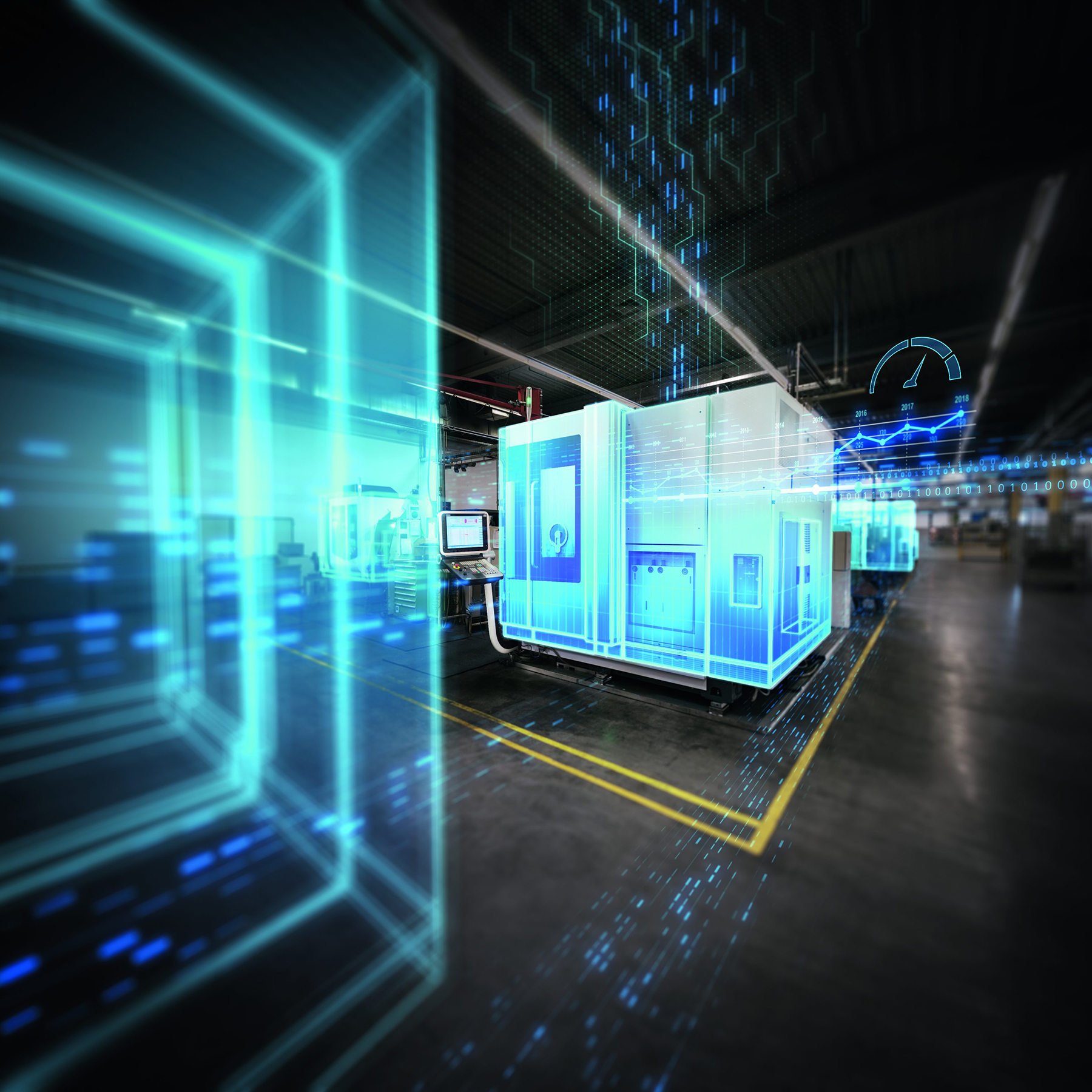
Today’s machine tool builder has read many articles and technical papers about the emerging concept of digitization. Here are three ways OEM engineering and management teams can view this technology and its impact, as it shapes the production and sales process of the future. They are: 1) Seeing digitization as a viable means of building a more effective, more reliable and more predictable machine from the outset of the design phase; 2) Realizing that digitization adds definable value, as it allows the machine tool builder better ways to present their value proposition to their customers; and 3) Utilizing digitization, builders can fashion new business models for the use of machine tools, as digitization demonstrates to the customers what they can do with the data and also how better to position the machine’s value to customers to sell more services, optimize machine uptime and track the performance of equipment in the field, all of which lead to improving the customer experience with your machines.
At the same time, the possibilities are both appealing and a bit challenging, so allow me to explain each briefly.
Advantages during design
Having a visual model of your CNC machine for commissioning alone makes the investment in digitization worthwhile to the builders of today’s machine tools. With the data and design concept in hand, you can use digitization tools available today, such as a mechatronics concept designer, which brings the physics of the world to your computer screen, so you can test the PLC, test the NC, run the motion control or load protocols including full machine kinematics and conduct overall system component integration, prior to the first manufacturing step of the build.
The available digitization tools provide highly accurate hardware in the loop emulation, transitioning from CAD to CAM to mechatronic concept designer, then finally to the virtual machine controller. Because the model is essentially mirroring the real hardware in operation under power, the simulations of machine motion and feedback are more precise than it would be with a pure simulation.
Specific customer challenges can be addressed at this stage and the results for the machine tool builder are faster resolution of design issues and less time to market with their machine.
Improved customer experience
On a functional level, the digital twin further integrates virtual and actual machine commissioning and production monitoring, so the machine tool builder can fashion new models in presenting their machines with enhanced, augmented reality monitoring, customizable apps for data prioritization and improved requirements and production data evaluation scenarios. This concept of data exchange represents a richer value proposition for the machine tool, as you present it to your customer. It also creates a closer touchpoint between builder and customer.
Better business models
New business models are also created by the machine tool builder’s ability to help their customers utilize digitization tools to improve their production. The virtual twin, based upon the virtual NC kernel (VNCK), allows various production, material handling and full motion control scenarios to be sampled in the design stage by the customer, while virtual training for programmers, operators and maintenance personnel is also possible. This digital twin is a high-value concept from a market appeal standpoint, plus the embedded software that permits the training can be positioned as a perceptible value-add for the machine builder to pass along to the end customer. Using a digital twin to support training and design helps the machine tool builder customers to save valuable machine uptime on the shopfloor
As machine tool builders become more capable of tracking the data on their CNC machines in the field, a dual benefit results for the end customer. Improvement in machine uptime is made possible, as the resolution of issues on the machine becomes a more streamlined process, plus current and rapidly emerging edge technology can add more precise analysis of the machine and the production process at the end customer.
The machine tool builder further benefits from studying component and overall machine performance in the field to improve the design and production process of his machine, even a global installed base, and making this data available to the end customer. The machine builder can then use the available data to track line productivity, machine-to-machine or facility-to-facility comparison, production schedule variance and other KPIs.
Digital twins are emerging as viable tools in the design and marketing of many CNC machine tools, a trend that will continue to grow.
Related Glossary Terms
- computer numerical control ( CNC)
computer numerical control ( CNC)
Microprocessor-based controller dedicated to a machine tool that permits the creation or modification of parts. Programmed numerical control activates the machine’s servos and spindle drives and controls the various machining operations. See DNC, direct numerical control; NC, numerical control.
- computer-aided design ( CAD)
computer-aided design ( CAD)
Product-design functions performed with the help of computers and special software.
- computer-aided manufacturing ( CAM)
computer-aided manufacturing ( CAM)
Use of computers to control machining and manufacturing processes.
- numerical control ( NC)
numerical control ( NC)
Any controlled equipment that allows an operator to program its movement by entering a series of coded numbers and symbols. See CNC, computer numerical control; DNC, direct numerical control.