To ensure the optimal function of artificial hips in a patient’s body, certain surface areas on the hip stem must have different finishes. For example, the neck area of the stems requires a very smooth, polished surface.
Recently, a manufacturer of precision components replaced a combined manual grinding/electropolishing operation with a fully automated two-stage mass finishing process. The drag finisher R 4/700 SF from Rösler allows the simultaneous, precise finishing of twelve hip stems in one single operation.
This resulted not only in significant cost savings and lower cycle times but also in a drastically improved quality and consistent finishing results.
For 20 years, the MBN Präzisionstechnik GmbH, located in Pottendorf, Austria, has been specializing in the manufacture of machined precision components and assemblies. The company’s main focus is on the production of orthopedic implants and surgical instruments made from titanium and stainless steel.
MBN Präzisionstechnik, certified according to DIN 13485, is not only equipped with ultra-modern machinery, including laser marking systems but has also clean rooms for the coating and germ-free packaging of its products.
Surface areas on different hip stems
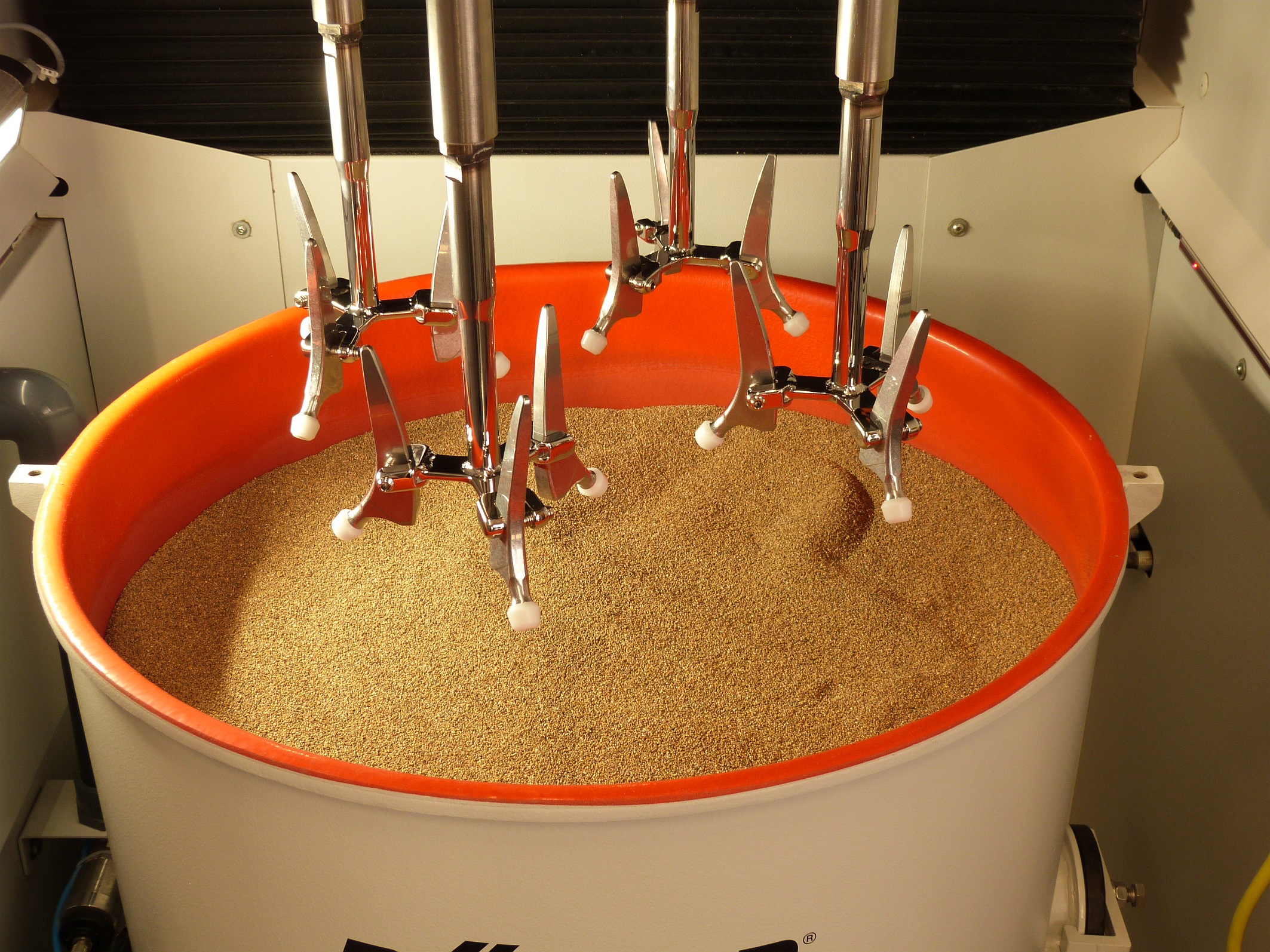
The production is to a large extent automated and allows tracing the entire manufacturing chain, from the raw material to the finished product. Until recently polishing of the neck area of the hip stems took place by a manual pre- and fine-grinding step, followed by an electropolishing process. This surface refinement operation was time-consuming, required a lot of manpower, and was very costly.
In addition, it was less than perfect with regard to the consistency of the finishing results and general sustainability. Therefore, Thomas Müllner, general manager at MBN Präzisionstechnik GmbH, had been looking for an automated alternative for quite some time.
”Since only, a precisely defined surface area must be polished, and a variety of different hip stem shafts must be processed, automating the surface finishing process turned out to be quite challenging,” he said.
“First, processing trials were undertaken by a supplier competing with Rösler. However, the results did not meet our quality standards.”
An application for the drag finishing technology
Based on the recommendation of one of MBN’s customer's further processing trials were conducted by the Rösler sales branch in Austria. This company is not only located nearby but also maintains a combined test and service center.
The Rösler experts decided to run the processing trials in a drag finisher. The unique mass finishing system allows the precise and targeted surface finishing of high-value work pieces with complex shapes. Once the process parameters have been established, the process runs without any variations, thus ensuring absolutely repeatable finishing results.
”Rösler’s comprehensive know-how and experience from the job shop operation helped to quickly develop a two-stage process with the drag finishing technology,” said Müllner. “The process, consisting of a wet grinding / pre-polishing step, followed by a dry polishing stage, produces a consistently high quality in surprisingly short cycle times.”
A feature of the Rösler drag finishing technology is the vibratory motor mounted below the processing bowl. ”The vibration of the processing bowl ensures the optimal mixing of the processing media. This results in the absolutely homogeneous finishing of all relevant surface areas on the hip stems,” said the general manager.
Drag finishing operation with two processing bowls
In the end, MBN Präzisionstechnik chose a compact drag finisher, model R 4/700 SF. The plug-and-play machine consists of a processing bowl with a diameter of 700 mm and a carousel with four rotating working spindles, each spindle allowing the mounting of three work pieces. The carousel and rotating spindles are equipped with separate drive systems so that the carousel and spindle speeds can be set independently from each other. The drag finishing machine is furnished with a second processing bowl. With a lift truck, the two bowls can be quickly exchanged.
Before the grinding operation, the surface areas on the hip stems requiring no finish are masked. Then the implants are manually mounted to special work piece fixtures. ”For this purpose we developed a clamping device that can be used for all stem types and sizes,” said Müllner. “The work piece fixtures with attached hip stems are then attached to the working spindles.”
After the respective processing program, stored in the programmable system controls, has started, the carousel is lowered so that the rotating spindles are immersed in the processing media. For the wet grinding process, a mix of plastic media with different geometric shapes and a special compound are utilized. Carousel and spindles are rotating at the pre-defined speed in opposite rotational directions.
After about half of the cycle time – amounting to less than one hour – the rotational direction is normally reversed. This ensures that the neck area of the hip stems receives an all-around perfect homogeneous finish. For cleaning the process water from the wet grinding process, MBN Präzisionstechnik purchased a semi-automatic Rösler centrifugal process water recycling system, model Z 800. Recycling the process water protects the environment and helps to significantly reduce the finishing costs.
For the polishing operation, a plant-based dry polishing media is utilized. For this process stage, requiring a cycle time of under 20 minutes, the processing bowl containing the finishing media is simply exchanged with the bowl filled with polishing media. Müllner said,” With the automatic drag finishing process we could significantly improve the quality and consistency of the finishing results. At the same time, compared to our previous finishing operation, the costs for grinding and polishing of the hip stem neck could be reduced by two thirds. Therefore, this investment will be amortized within three years.”
Contact Details
Related Glossary Terms
- grinding
grinding
Machining operation in which material is removed from the workpiece by a powered abrasive wheel, stone, belt, paste, sheet, compound, slurry, etc. Takes various forms: surface grinding (creates flat and/or squared surfaces); cylindrical grinding (for external cylindrical and tapered shapes, fillets, undercuts, etc.); centerless grinding; chamfering; thread and form grinding; tool and cutter grinding; offhand grinding; lapping and polishing (grinding with extremely fine grits to create ultrasmooth surfaces); honing; and disc grinding.
- polishing
polishing
Abrasive process that improves surface finish and blends contours. Abrasive particles attached to a flexible backing abrade the workpiece.