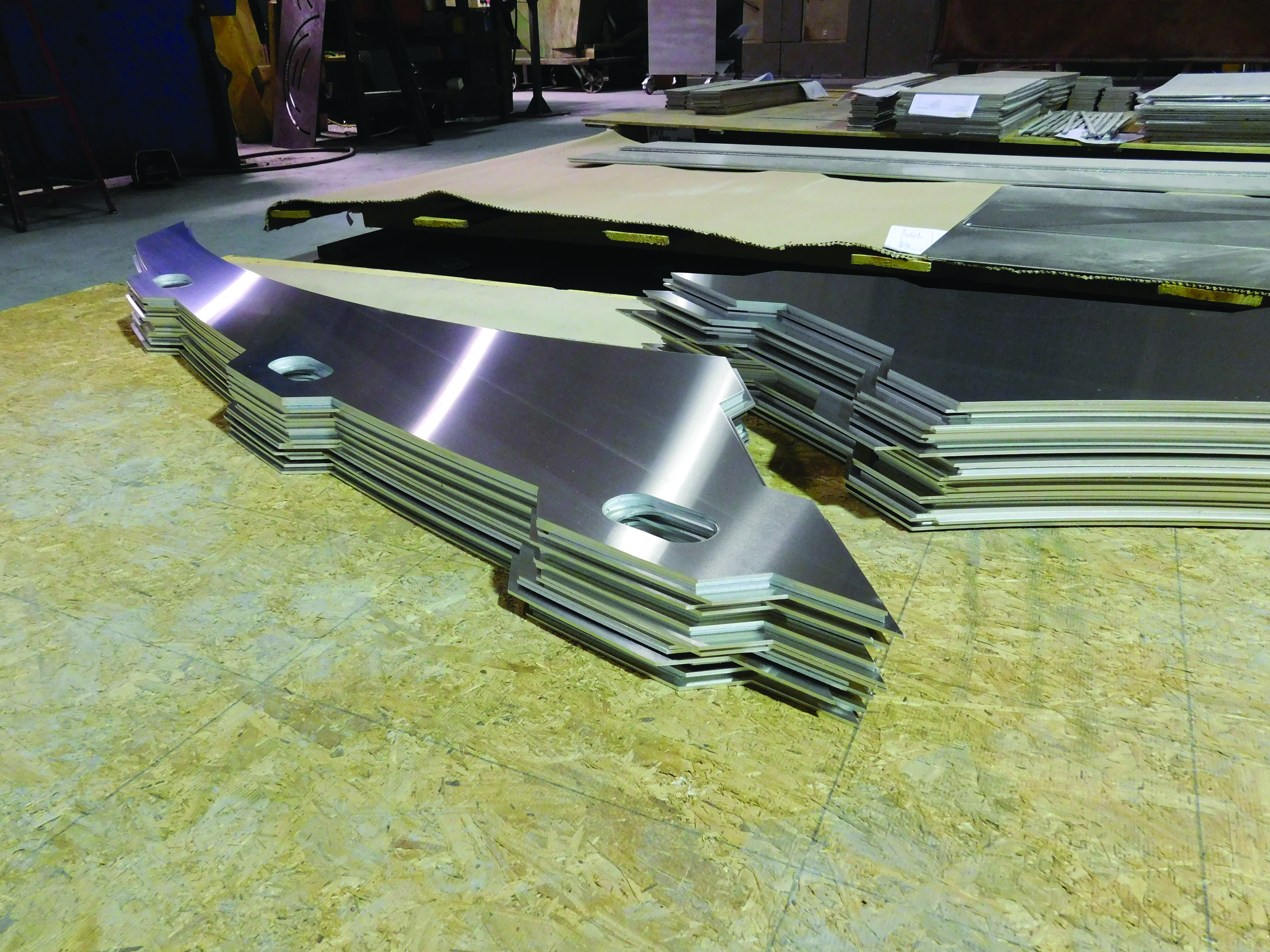
Continuous improvement has always been the goal at Tindle Construction Inc. (TCI) where industry expertise and the implementation of efficiency-boosting technologies has helped the company create high-quality products since 1994.
Headquartered in Fredonia, Kansas, TCI is a family-owned, multi-divisional company is a premier metal fabricator and specialized industrial services company across the country. TCI employs 74 and operates two divisions, Industrial Services and Fabrication, working separately and in combination to produce superior products for a variety of customers. The company also offers design and planning services for projects that it manufactures.
“AWS certified and R-stamp welds, custom engineering on architectural parts, custom high-end finishes on copper, brass, stainless and carbon display products are some of the things that separate us from our competition,” said engineering manager Jesse McGinnis, who has been with TCI for 15 years.
A range of finished products
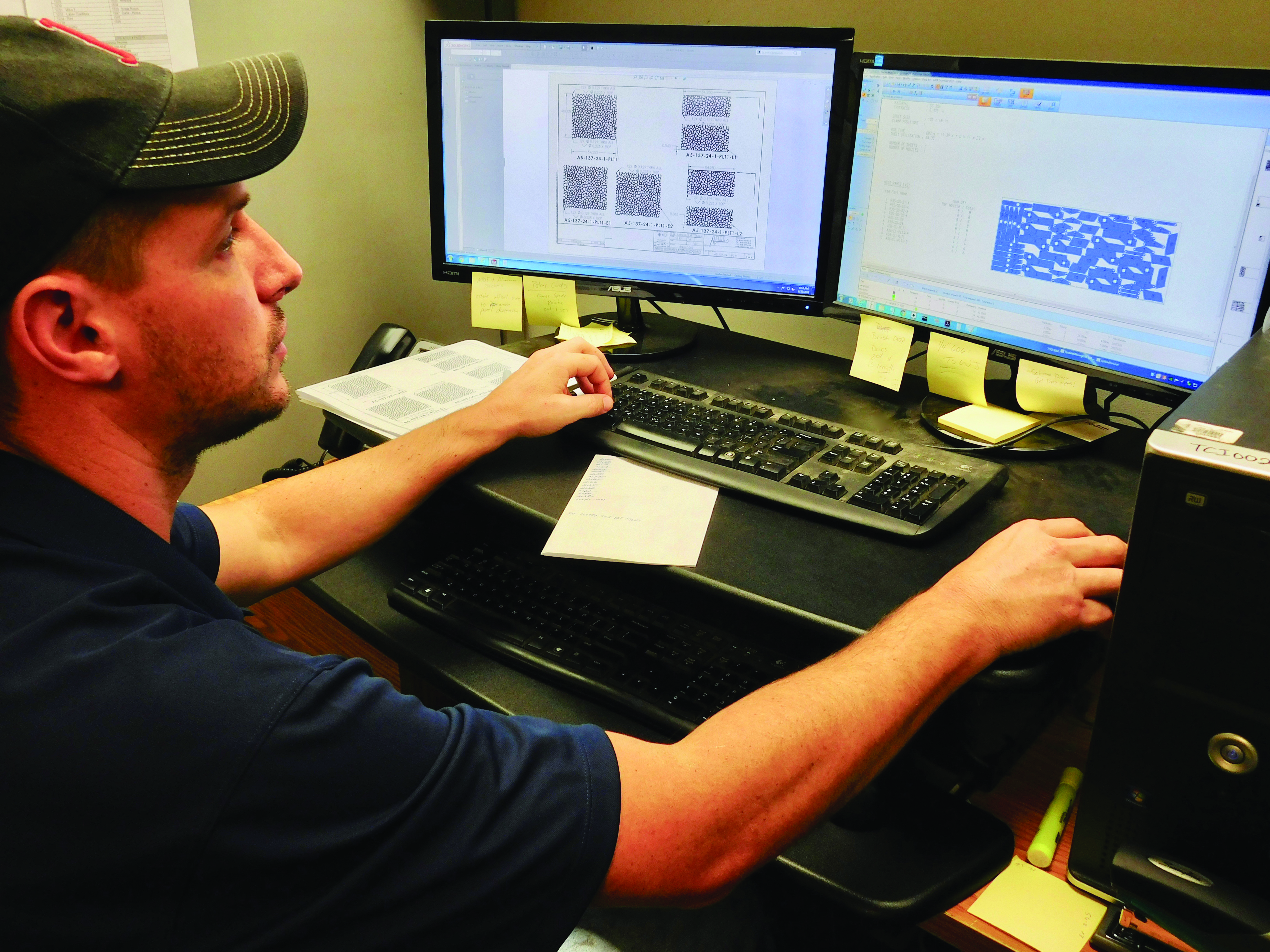
Ornamental and architectural metal products, signage and artwork, as well as sheet-metal products like wall panels, corner trims, and ceiling inserts are counted among TCI’s diverse range of fabrication capabilities. Sheet metal parts, weldments, structural steel, pressure vessels, and unique metal finishes are typical projects that make their way across the shop floor. Aluminum, carbon steel, stainless steel, brass, and copper are TCI’s most commonly used materials.
“We have a lot of different machines and a lot of different capabilities, and combining those is like playing chess,” said McGinnis . “It’s interesting to see what we can come up with to get the job done, and that’s definitely a challenge that I enjoy.”
TCI utilizes a laser, water jet, press brake, mandrel bender, CNC lathe, CNC mills, and manual lathes and mills. Part of McGinnis’s job is to decide which combinations of machinery will be most efficient and best suited to each unique job.
McGinnis was hired by TCI specifically for the fabrication side of the business and was tasked with hand-programming the company’s new laser, purchased in September of 2015. TCI eventually invested in a CNC programming solution for the laser, but over time found that the system was significantly limited in efficiency and flexibility.
Fast nesting
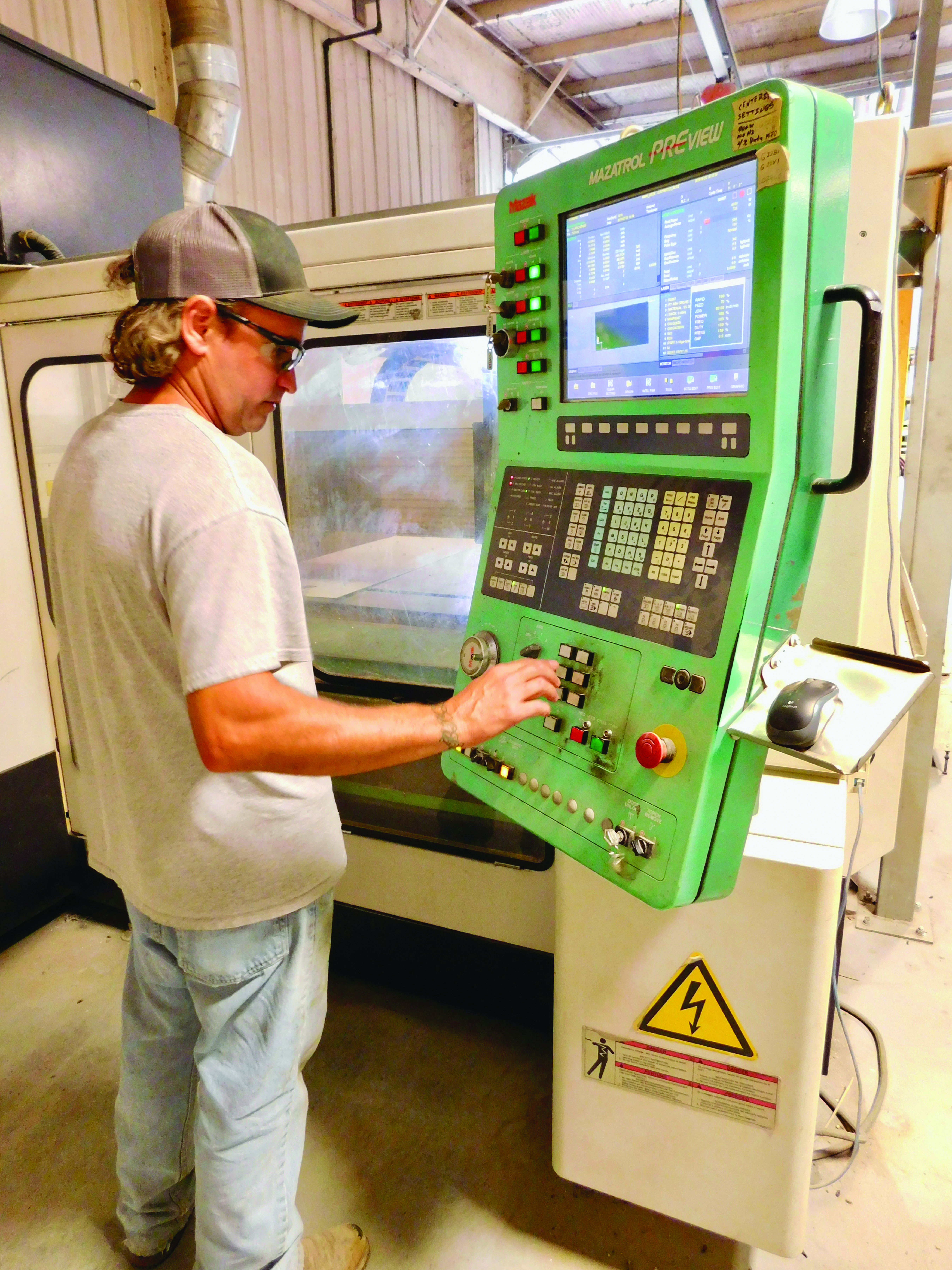
After investigating all options for implementing a new sheet-metal solution, TCI made the switch to RADAN in 2015. “I felt like RADAN was a better fit for us,” said McGinnis, who also uses RADAN to program TCI’s waterjet. “The providers of our previous solution were going to give us an upgrade and a patch for the new laser, but it became obvious when I saw how fast RADAN was with nesting that we needed to make the switch to a new solution.”
Prior to the implementation of RADAN, staff at TCI would begin the nesting process and then tackle other shop tasks while the nests were generated, as the process typically took hours to complete.
“RADAN can make a day’s worth of nests in a couple of minutes,” McGinnis says. “This is a huge difference to us in man hours alone. “
He said that the company has one employee who programs for half the day and spends the rest of the day working on engineering projects. “Because of what we’re able to do with RADAN, it’s not necessary to have a person generating nests full time anymore.”
Unlike many other solutions for sheet metal, RADAN also allows editing of its automatically-generated nests, ensuring that programming control remains in the hands of the user.
“The ability to edit nests was something that our old software could not give us, and we can do that with RADAN— edit the lead in lead, lead out, tooling, or just edit for cosmetic reasons,” McGinnis said. “That was another high point for RADAN.”
A planning solution
For TCI, RADAN’s ability to work with its Manufacturing Requirement Planning (MRP) solution is every bit as vital to efficiency as the solution’s nesting features. RADAN MRP Essentials is an MRP integration utility that enables nested projects to be automatically generated from a production schedule file.
While several MRP systems deliver the ability to generate a schedule-file report — including production information, such as part numbers, quantities, and material thickness — RADAN MRP Essentials can read scheduled files and construct nests automatically. The nests can also be automatically sorted by material type, gauge, and designated CNC machine.
“RADAN’s ability to work with our MRP is very critical for keeping track of the many things we have to keep track of on a daily basis,” says McGinnis, who notes that TCI had an ERP system up and running prior to the implementation of RADAN. That system tracks TCI’s purchasing, receiving, and shipping, and manages shop-floor time tickets and job scheduling.
After a potential customer requests an estimate, TCI’s estimator will work with the company’s engineering staff to provide a “ballpark figure” that reflects man hours, materials, and other job details. If the job goes forward, an engineer will then use the company’s computer-aided-design (CAD) software to create a model.
“After we design it the way it will be built, the job gets routed in the ERP and we’ll get an outline of steps for how each piece will be made,” McGinnis says. “We’re very efficient: The ERP tracks every piece and where it’s purchased from, and each item has a drawing attached to it that is current. Once all of that is ready, the scheduler will take the order and purchasing can be verified.”
After purchasing verification, a separate job is created for each part to be manufactured, as well as for each assembly. Once materials are sorted, TCI’s RADAN operator receives a loading summary in text format for both the laser and waterjet, and that summary is loaded into MRP Essentials.
“MRP Essentials will look at that list to order parts and generate jobs,” McGinnis says. “It has basic job information, revision quantity, date, and any other important details. From there, RADAN will generate two lists, one for parts that are ready to be cut and one for jobs that have missing information. That’s how we keep from cutting things that we shouldn’t.”
Programs are then written based on the parts on the “approved” list, and those programs are sent to the shop floor with job numbers. The jobs with incomplete information are edited and run through the system again until they are glitch free.
“We wouldn’t be as efficient as we are without RADAN’s nesting and the ability of the system to do what we need it to do,” McGinnis says. “RADAN offered extensive help implementing MRP essentials to fit our needs working with our ERP. We worked with customer support to make custom reports to get the job information to the laser operator, and to track the revisions levels in our RADAN Symbol library. We are now able to track material certs for each part and mix different customer parts together on one program based on the material type.”
With the goal at TCI to continue to improve in efficiency and innovation, RADAN has proven to be a vital part of everyday production at TCI.
For more information on RADAN CAD/CAM software, visit www.radan.com.
Related Glossary Terms
- computer numerical control ( CNC)
computer numerical control ( CNC)
Microprocessor-based controller dedicated to a machine tool that permits the creation or modification of parts. Programmed numerical control activates the machine’s servos and spindle drives and controls the various machining operations. See DNC, direct numerical control; NC, numerical control.
- lathe
lathe
Turning machine capable of sawing, milling, grinding, gear-cutting, drilling, reaming, boring, threading, facing, chamfering, grooving, knurling, spinning, parting, necking, taper-cutting, and cam- and eccentric-cutting, as well as step- and straight-turning. Comes in a variety of forms, ranging from manual to semiautomatic to fully automatic, with major types being engine lathes, turning and contouring lathes, turret lathes and numerical-control lathes. The engine lathe consists of a headstock and spindle, tailstock, bed, carriage (complete with apron) and cross slides. Features include gear- (speed) and feed-selector levers, toolpost, compound rest, lead screw and reversing lead screw, threading dial and rapid-traverse lever. Special lathe types include through-the-spindle, camshaft and crankshaft, brake drum and rotor, spinning and gun-barrel machines. Toolroom and bench lathes are used for precision work; the former for tool-and-die work and similar tasks, the latter for small workpieces (instruments, watches), normally without a power feed. Models are typically designated according to their “swing,” or the largest-diameter workpiece that can be rotated; bed length, or the distance between centers; and horsepower generated. See turning machine.
- mandrel
mandrel
Workholder for turning that fits inside hollow workpieces. Types available include expanding, pin and threaded.
- sawing machine ( saw)
sawing machine ( saw)
Machine designed to use a serrated-tooth blade to cut metal or other material. Comes in a wide variety of styles but takes one of four basic forms: hacksaw (a simple, rugged machine that uses a reciprocating motion to part metal or other material); cold or circular saw (powers a circular blade that cuts structural materials); bandsaw (runs an endless band; the two basic types are cutoff and contour band machines, which cut intricate contours and shapes); and abrasive cutoff saw (similar in appearance to the cold saw, but uses an abrasive disc that rotates at high speeds rather than a blade with serrated teeth).