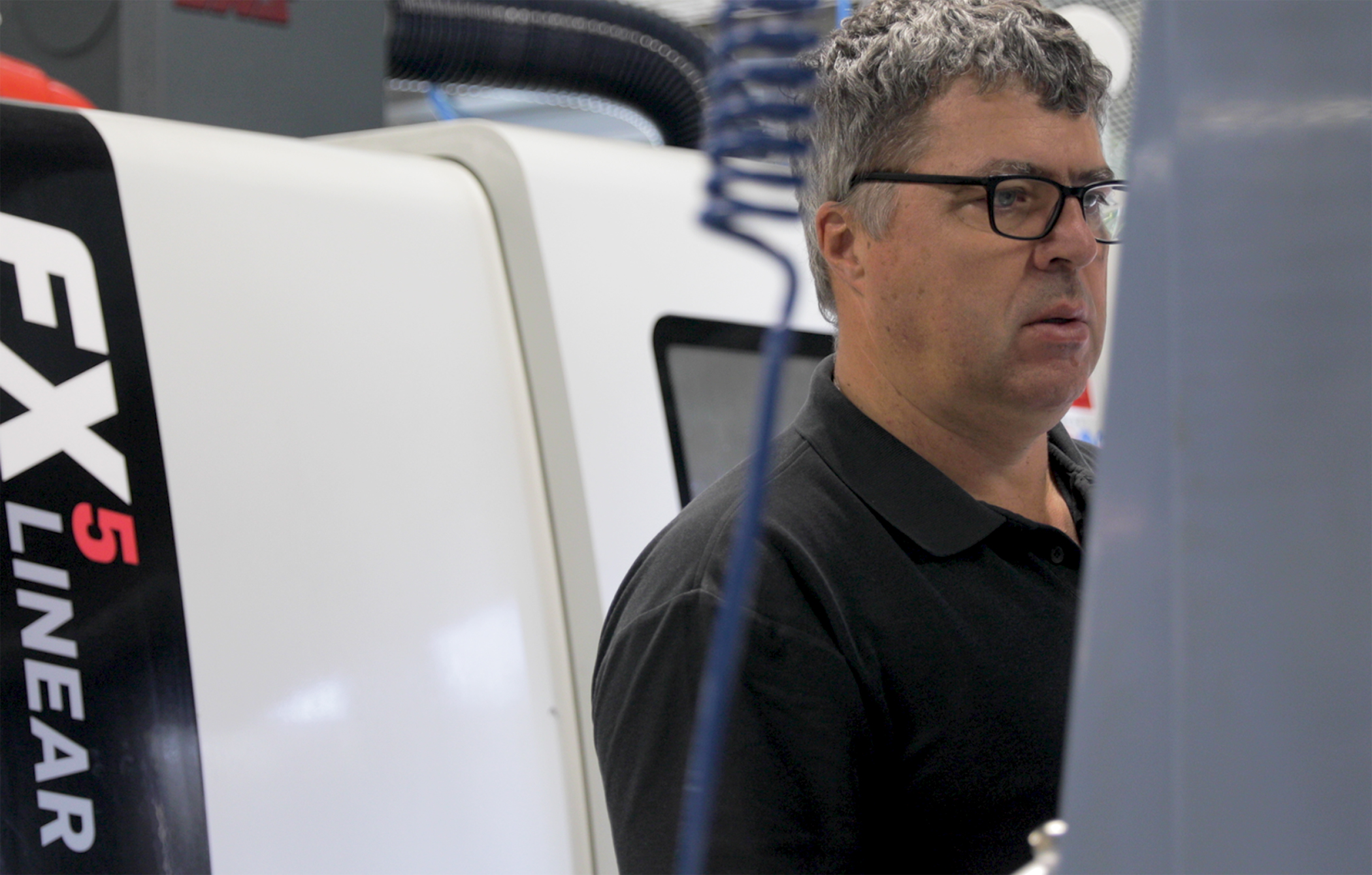
Loïc Jacot, a 5th generation family member of F.O. Select, said, “Our business was founded in 1886 by my great-great-grandfather when he started manufacturing razor blades. At the beginning of the 20th century, the multinational company Gillette entered the European market and Arnold Schumacher decided to diversify the production with different cutting tools.”
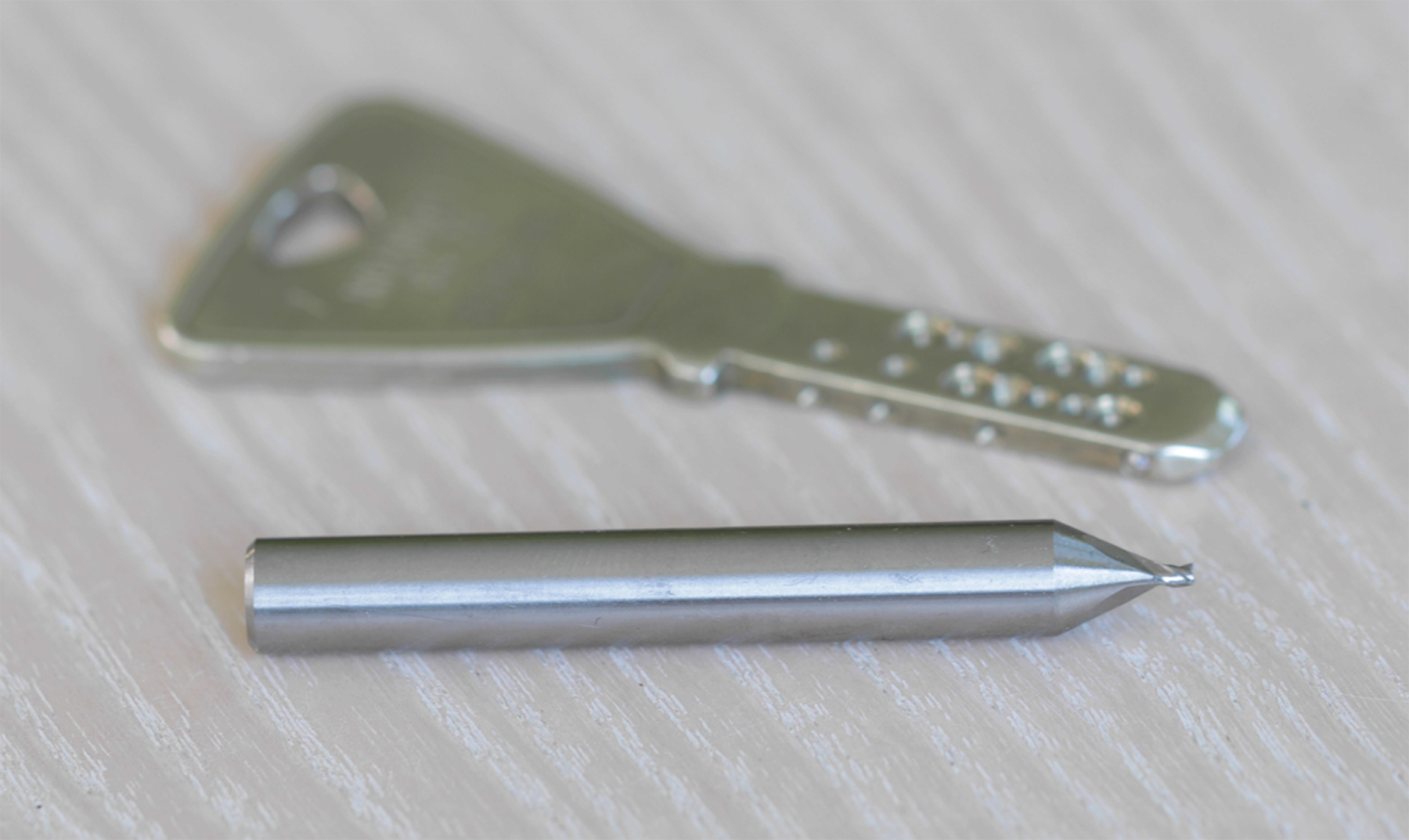
“Our customers like the fact that we are still a family business,” said Jacot. “We have 130 years of experience in the production of tools. In general, we can say that we work with all the main key cutting machine producers on the market. Since all people in the world use keys you need to cut millions and millions of keys every day. The market is niche but worldwide.”
F.O. Select specializes in the manufacture of key cutters, cutter wheels and fine-tooth cutters. Their dynamism and expertise have led the business to strive constantly for innovative performance and quality assurance. Production-wise, the company has leading-edge technology that combines traditional craftsmanship with today’s modern manufacturing methods.
“We produce all our products in-house so we have a control over the whole production process,” said Jacot. “We produce about 100,000 pieces a year and export our products to 75 different countries with a very short lead time of 48 hours. Keys are becoming more complex because people want more security. Since the market is shifting towards precision we needed more precise machines to manufacture the keys.”
“In Switzerland, if we want to be competitive, we have to be automated, because in Switzerland everything is very expensive,” said Jacot. “We looked for the best solution for our production needs, understanding that cost reduction could be achieved with better efficiency and productivity. Investing in capital equipment is expensive and we needed to calculate if we should buy new machinery. We looked at how the ANCA FX5 grinding machine would help us in the production process in terms of productivity through automated solutions. Quality is also very important to our business.”
Lights-out production
“We have achieved these savings by investing in equipment that can run without human intervention, or ‘lights out.’ This means they can run, producing tools, after office hours – during the night and weekends unattended.”
“Since we installed our FX5 ANCA grinding machine we have been working 24 hours seven days a week.”
“New technology is very important because they bring efficiency, reliability, and precision. Our new ANCA machine is very precise, automated; and thanks to the laser we can measure the pieces on the machine and the machine will, by itself, change the software to make the measurement correct. This is crucial when working unmanned during the night or weekend.”
“The ANCA machine is easy to set up because the software is user-friendly. We had no experience in how to set up grinding machines producing endmills before our first ANCA machine. And now we have two and in the future maybe more.”
“We received training from ANCA to help set up the machine correctly. The robot is very easy to set up, so in a few minutes, you can change the diameter or you can change the table and the machine will be ready for production. And the good thing also is, I mean, the machine is more compact. I mean in comparison -- if we compare our old ANCA machine and the new one, the new one is maybe 30% smaller.”
“We have a bright future because we have modern machines, precise ones, automated. And since we control the whole production process we developed our know-how and we produce more precise and more durable tools,” Jacot said.
Contact Details
Related Glossary Terms
- grinding
grinding
Machining operation in which material is removed from the workpiece by a powered abrasive wheel, stone, belt, paste, sheet, compound, slurry, etc. Takes various forms: surface grinding (creates flat and/or squared surfaces); cylindrical grinding (for external cylindrical and tapered shapes, fillets, undercuts, etc.); centerless grinding; chamfering; thread and form grinding; tool and cutter grinding; offhand grinding; lapping and polishing (grinding with extremely fine grits to create ultrasmooth surfaces); honing; and disc grinding.
- grinding machine
grinding machine
Powers a grinding wheel or other abrasive tool for the purpose of removing metal and finishing workpieces to close tolerances. Provides smooth, square, parallel and accurate workpiece surfaces. When ultrasmooth surfaces and finishes on the order of microns are required, lapping and honing machines (precision grinders that run abrasives with extremely fine, uniform grits) are used. In its “finishing” role, the grinder is perhaps the most widely used machine tool. Various styles are available: bench and pedestal grinders for sharpening lathe bits and drills; surface grinders for producing square, parallel, smooth and accurate parts; cylindrical and centerless grinders; center-hole grinders; form grinders; facemill and endmill grinders; gear-cutting grinders; jig grinders; abrasive belt (backstand, swing-frame, belt-roll) grinders; tool and cutter grinders for sharpening and resharpening cutting tools; carbide grinders; hand-held die grinders; and abrasive cutoff saws.
- quality assurance ( quality control)
quality assurance ( quality control)
Terms denoting a formal program for monitoring product quality. The denotations are the same, but QC typically connotes a more traditional postmachining inspection system, while QA implies a more comprehensive approach, with emphasis on “total quality,” broad quality principles, statistical process control and other statistical methods.