Moraine Park Technical College in West Bend, Wisconsin, and Siemens are working together to train workers in the manufacturing sector.
With an emphasis on CNC, tool & die design, and tool & die making, the AMTC trains students on state-of-the-industry equipment, controls, and software.
Opened in August 2002, the AMTC is home to the CNC Programmer/Operator track of the Machining Technician program as well as the Tool & Die Designer program of MPTC.
The facility also supports the Tool & Die Making track of the program, housed in another part of the campus.
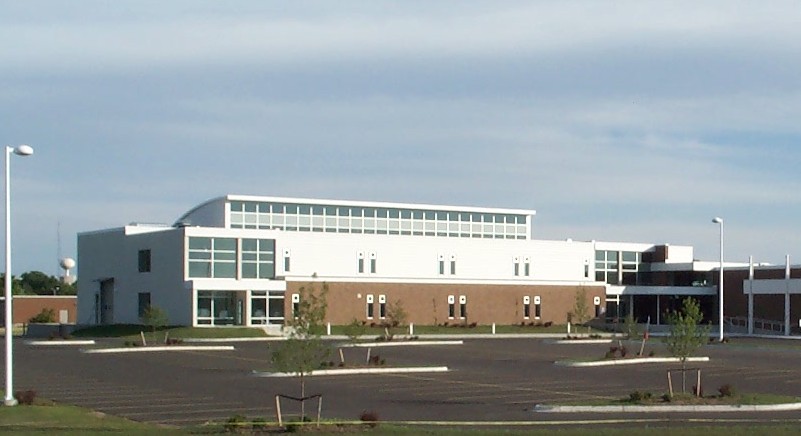
The AMTC is a 42,000-square-foot facility, comprising a 6,000-square-foot facility CNC lab, three computer labs for CNC, tool & die design, and an industry OEM partner lab, as well as other classrooms, conference areas, and an auditorium.
The students in this program comprise displaced workers coming back for retraining, new program participants, and the local industry.
Moraine Park Technical College provides a two-year technical diploma in its Machining Technician program, which includes a track in CNC programming and operations, among others. MPTC’s two-year associate degree in tool & die design is the only one of its kind in the state of Wisconsin.
The AMTC CNC programmer/operator lab has a horizontal machining center with pallet changer and tool selection carousel, wire EDM, CNC CMM, and six vertical machining centers and four lathes.
The tool & die lab contains four VMCs, two wire EDMs, two sinker EDMs, two benchtop CMMs (coordinate measuring machines), seven lathes, seven 6-18 grinders, three 12-24 wet grinders, a 100-ton punch press with servo auto-feed, 90-ton plastic injection molding press, 20 2-D conversational manual milling machines and two power feed drill presses.
An important aspect of all machine training today is the control technology onboard. On two of the VMCs in the CNC lab, each a Hardinge 600II with 8000 RPM spindles, there are Siemens SINUMERIK 810D CNCs with the proprietary Siemens ShopMill software suite.
“The Siemens CNC is an intelligent control with excellent flexibility,” said Jim Hokenson, CNC instructor of the AMTC. “ShopMill is a very productive package, especially when doing shop floor programming. The graphic user interface is very helpful to novice programmers and operators. The 3D solid graphic verification is exemplary. The file management system is easily followed and understood. The fact that normal G-code can be intermixed with ShopMill code is a great feature. We’ve undergone three software upgrades and the transition has been seamless.”
Students here normally start on 6061 aluminum, because it machines faster, as well as 1018 tool steel. After the basic concept is mastered, the students move on to other steels such as O-1, D-2, S-7, 4140, 410SS, P-20, and H-13, plus composite plastics, brass, and hardened tool steels. Typically, the parts produced here resemble fittings, valves, valve bodies, stamping die punches, die blocks, mold die cores, and cavities, plus various components for personal machinists’ tools.
On the Hardinge VMCs, Siemens controls are used for axis movement and spindle control. Communication on the AMTC’s machine tools is primarily wireless Ethernet, though a fully-wired RS232 network is also present and is taught to students.
Jim Hokenson said that the Siemens control was easy to navigate and, since the file manager is Windows-based, the students have no trouble creating, saving, moving, and editing programs.
Learning production steps
Typically, the student uses an edge finder to locate their part zero. After they set up the edge finder in the tool library, they can set the offset. The position screen is checked for configuration.
Next, the tool offsets are established. The tool length measure mode is enabled, then the student will tell the machine to put the proper tool into the spindle via the S, T, M mode. The tool is then brought down to its 1.0000 touch-off block. The 1.0000 valves are checked on the tool length measure page and then the length measure key is pressed.
Tools and offsets are now set. The Z-axis is set to the home position, using the axis zero return button. The program is now ready to be written at the machine or loaded offline. If it’s written on the machine, the student will create a program using Siemens ShopMill and verify it with the graphics software. If the program is to be loaded offline, the student will navigate to the program through the local net 1,2, or 3 channels. The program is then transferred to the CNC memory and executed.”
Contact Details
Related Glossary Terms
- 2-D
2-D
Way of displaying real-world objects on a flat surface, showing only height and width. This system uses only the X and Y axes.
- centers
centers
Cone-shaped pins that support a workpiece by one or two ends during machining. The centers fit into holes drilled in the workpiece ends. Centers that turn with the workpiece are called “live” centers; those that do not are called “dead” centers.
- computer numerical control ( CNC)
computer numerical control ( CNC)
Microprocessor-based controller dedicated to a machine tool that permits the creation or modification of parts. Programmed numerical control activates the machine’s servos and spindle drives and controls the various machining operations. See DNC, direct numerical control; NC, numerical control.
- edge finder
edge finder
Gage mounted in the spindle of a vertical mill and used, while rotating, to find the center of a part relative to the toolholder.
- electrical-discharge machining ( EDM)
electrical-discharge machining ( EDM)
Process that vaporizes conductive materials by controlled application of pulsed electrical current that flows between a workpiece and electrode (tool) in a dielectric fluid. Permits machining shapes to tight accuracies without the internal stresses conventional machining often generates. Useful in diemaking.
- feed
feed
Rate of change of position of the tool as a whole, relative to the workpiece while cutting.
- gang cutting ( milling)
gang cutting ( milling)
Machining with several cutters mounted on a single arbor, generally for simultaneous cutting.
- machining center
machining center
CNC machine tool capable of drilling, reaming, tapping, milling and boring. Normally comes with an automatic toolchanger. See automatic toolchanger.
- milling
milling
Machining operation in which metal or other material is removed by applying power to a rotating cutter. In vertical milling, the cutting tool is mounted vertically on the spindle. In horizontal milling, the cutting tool is mounted horizontally, either directly on the spindle or on an arbor. Horizontal milling is further broken down into conventional milling, where the cutter rotates opposite the direction of feed, or “up” into the workpiece; and climb milling, where the cutter rotates in the direction of feed, or “down” into the workpiece. Milling operations include plane or surface milling, endmilling, facemilling, angle milling, form milling and profiling.
- tool steels
tool steels
Group of alloy steels which, after proper heat treatment, provide the combination of properties required for cutting tool and die applications. The American Iron and Steel Institute divides tool steels into six major categories: water hardening, shock resisting, cold work, hot work, special purpose and high speed.
- wire EDM
wire EDM
Process similar to ram electrical-discharge machining except a small-diameter copper or brass wire is used as a traveling electrode. Usually used in conjunction with a CNC and only works when a part is to be cut completely through. A common analogy is wire electrical-discharge machining is like an ultraprecise, electrical, contour-sawing operation.