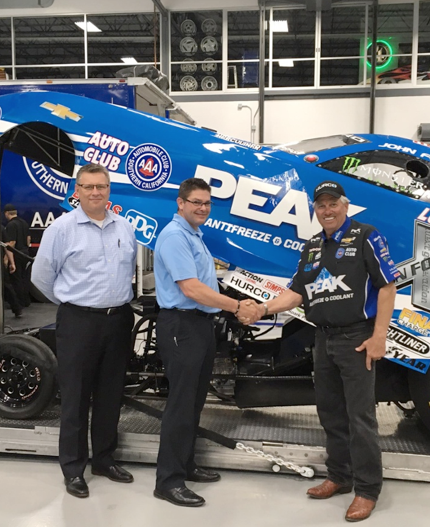
CEO of John Force Racing Inc. and 16-time NHRA Funny Car champion John Force along with Cory Miller, General Manager of Hurco North America, announced an initial 5-year agreement between the Indianapolis area based companies that will continue to enhance the development and production capabilities of JFR and its Force American Made (FAM) machining company. FAM will be adding Hurco’s latest product technology with six state-of-the-art CNC machining and turning centers, plus all support equipment to the machine shop area.
“I am excited about this agreement with Hurco because having technology like these machines will translate to wins on the racetrack and take us to the next level. Not only are we getting high quality machines but we are also getting the experts to help us run them and train our engineers. It was great to work out this deal with Cory and I know all the guys in the shop are excited to get these machines in here and start putting them to work,” said John Force.
“We are looking forward to entertaining customers here at our shop as well as working with them at the IMTS and PRI shows. We are also going to be using our FAM shop as a showcase and training facility for their products,” added Force.
Hurco is an Indianapolis-based company with global reach. It has divisions throughout North America, Europe, and Asia. Their corporate offices have been located in Indianapolis, Indiana since the company's founding in 1968. Hurco engineers will be assisting John Force Racing with the set-up and training of all the new Hurco products. With more than 60 active patents, Hurco is focused on continuous innovation that makes machinists more productive and machine shops more profitable.
“John Force Racing is a legendary brand in the world of NHRA and Hurco is proud to partner with them. We often say the world of racing and machining are a lot alike because the name of the game is speed, power, and precision. The JFR team and their facility, which is just down the road from Hurco’s international headquarters, are top notch and the ability to showcase our CNC machine technology at JFR’s Force American Made machine shop will be very beneficial. I know the sophisticated technology of the Hurco CNC machines will serve JFR well,” said Cory Miller, General Manager of Hurco North America.
Hurco is installing the most technologically sophisticated CNC machines at JFR’s FAM shop, including the 5-axis VMX42SRTi and the TMX10MYSi slant-bed lathe with live tooling and sub-spindle in addition to other CNC machines from the VMX Performance Series. All of the Hurco CNC machining centers are equipped with UltiMotion, which is the motion system Hurco invented that significantly reduces cycle time as well as machine jerk while improving surface finish quality of parts. All of the HUrco CNC machines are equipped with the integrated MAX5 control powered by WinMax software, considered the most versatile in the industry as it has intuitive conversational programming, Industry Standard NC, and Hurco’s NC/Conversational Merge that blends both programming methods for increased productivity.
Contact Details
Related Glossary Terms
- centers
centers
Cone-shaped pins that support a workpiece by one or two ends during machining. The centers fit into holes drilled in the workpiece ends. Centers that turn with the workpiece are called “live” centers; those that do not are called “dead” centers.
- computer numerical control ( CNC)
computer numerical control ( CNC)
Microprocessor-based controller dedicated to a machine tool that permits the creation or modification of parts. Programmed numerical control activates the machine’s servos and spindle drives and controls the various machining operations. See DNC, direct numerical control; NC, numerical control.
- conversational programming
conversational programming
Method for using plain English to produce G-code file without knowing G-code in order to program CNC machines.
- lathe
lathe
Turning machine capable of sawing, milling, grinding, gear-cutting, drilling, reaming, boring, threading, facing, chamfering, grooving, knurling, spinning, parting, necking, taper-cutting, and cam- and eccentric-cutting, as well as step- and straight-turning. Comes in a variety of forms, ranging from manual to semiautomatic to fully automatic, with major types being engine lathes, turning and contouring lathes, turret lathes and numerical-control lathes. The engine lathe consists of a headstock and spindle, tailstock, bed, carriage (complete with apron) and cross slides. Features include gear- (speed) and feed-selector levers, toolpost, compound rest, lead screw and reversing lead screw, threading dial and rapid-traverse lever. Special lathe types include through-the-spindle, camshaft and crankshaft, brake drum and rotor, spinning and gun-barrel machines. Toolroom and bench lathes are used for precision work; the former for tool-and-die work and similar tasks, the latter for small workpieces (instruments, watches), normally without a power feed. Models are typically designated according to their “swing,” or the largest-diameter workpiece that can be rotated; bed length, or the distance between centers; and horsepower generated. See turning machine.
- numerical control ( NC)
numerical control ( NC)
Any controlled equipment that allows an operator to program its movement by entering a series of coded numbers and symbols. See CNC, computer numerical control; DNC, direct numerical control.
- turning
turning
Workpiece is held in a chuck, mounted on a face plate or secured between centers and rotated while a cutting tool, normally a single-point tool, is fed into it along its periphery or across its end or face. Takes the form of straight turning (cutting along the periphery of the workpiece); taper turning (creating a taper); step turning (turning different-size diameters on the same work); chamfering (beveling an edge or shoulder); facing (cutting on an end); turning threads (usually external but can be internal); roughing (high-volume metal removal); and finishing (final light cuts). Performed on lathes, turning centers, chucking machines, automatic screw machines and similar machines.