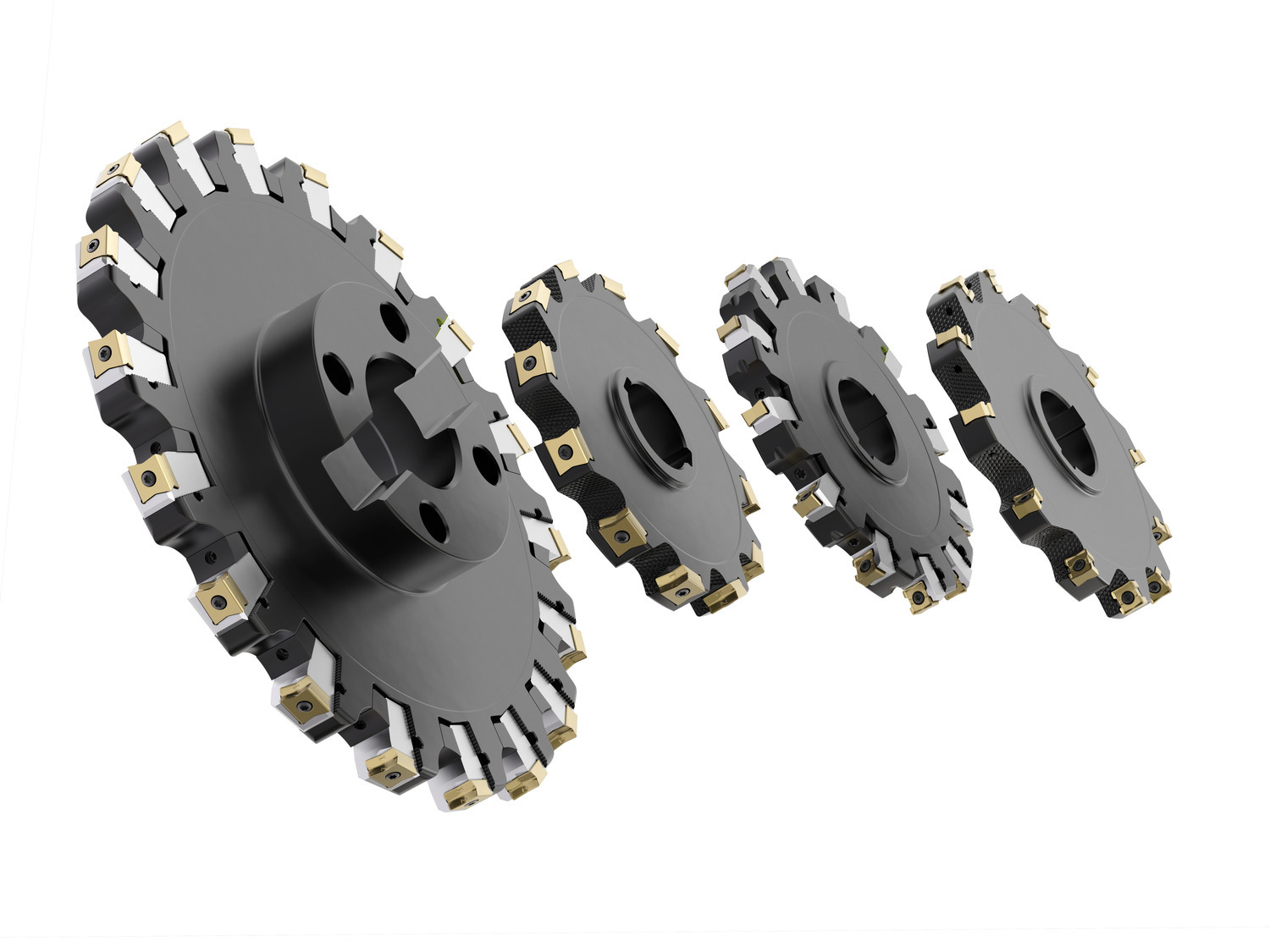
The new Seco 335.98 Disc Milling Cutter system, which was designed specifically for cost reductions, achieves the lowest cost per part in half-side and face disc milling operations, according to Seco executives.
The system’s combination of cutter body and insert geometries further enhances performance through a strong interface, free-cutting design and minimization of cutting forces.
Seco 335.98 disc milling cutters use dedicated inserts with eight usable cutting edges. The unique geometries of the inserts yield up to 60% longer life in left-hand and right-hand side disc milling operations.
"The 335.98 disc milling cutter achieves the best possible performance and excels in high-volume production applications, especially those involving components with right-hand and left-hand side milling operations," said Seco product manager Benjamin Michelet. "Not only will manufacturers, such as those in the automotive industry, increase their productivity, but they will also significantly reduce their tooling costs
through decreased insert consumption."
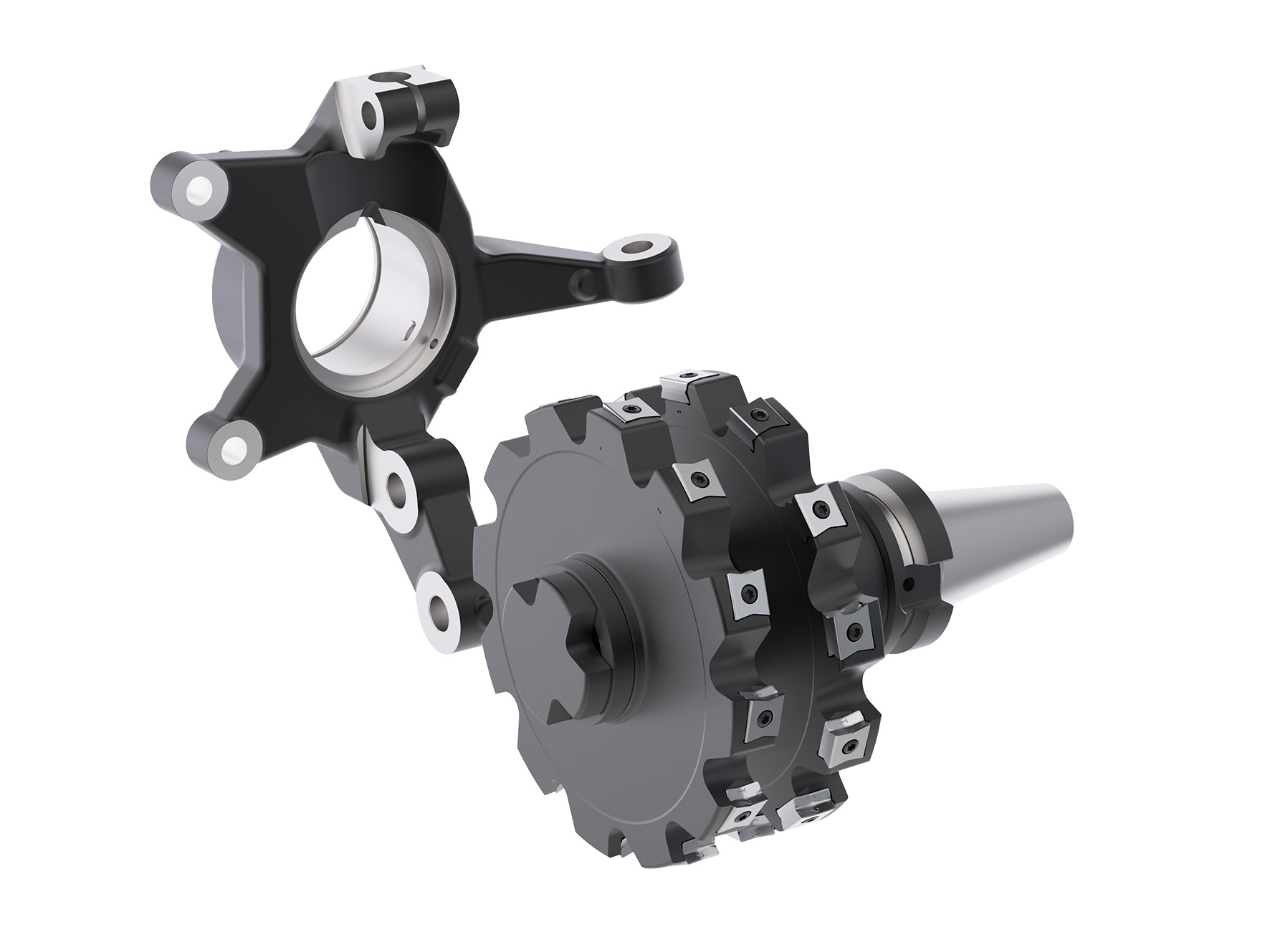
Seco 335.98 disc milling cutter bodies are also available with optional insert cassettes. According to Michelet, the cassettes increase flexibility through quick, easy insert changes, and they significantly reduce repair costs if a pocket is damaged, as only the cassette needs replacing.
Increased process security and flexibility
The Seco 335.98 disc milling system offers a strong, reliable interface between cutter body and insert to maximize stability. Furthermore, this unique interface simplifies insert setup and indexing by preventing mounting mistakes. The free-cutting design of the inserts optimizes chip flow to avoid potential jams, while also minimizing cutting forces to eliminate vibration and increase part quality.
Inserts are available in two standard sizes with a broad range of grade and corner radii options. This enables the flexibility to apply the system to a broad range of material types and applications. For high-volume applications, the Seco custom tools department provides on-demand customization to further optimize performance.
Contact Details
Related Glossary Terms
- gang cutting ( milling)
gang cutting ( milling)
Machining with several cutters mounted on a single arbor, generally for simultaneous cutting.
- milling
milling
Machining operation in which metal or other material is removed by applying power to a rotating cutter. In vertical milling, the cutting tool is mounted vertically on the spindle. In horizontal milling, the cutting tool is mounted horizontally, either directly on the spindle or on an arbor. Horizontal milling is further broken down into conventional milling, where the cutter rotates opposite the direction of feed, or “up” into the workpiece; and climb milling, where the cutter rotates in the direction of feed, or “down” into the workpiece. Milling operations include plane or surface milling, endmilling, facemilling, angle milling, form milling and profiling.
- milling cutter
milling cutter
Loosely, any milling tool. Horizontal cutters take the form of plain milling cutters, plain spiral-tooth cutters, helical cutters, side-milling cutters, staggered-tooth side-milling cutters, facemilling cutters, angular cutters, double-angle cutters, convex and concave form-milling cutters, straddle-sprocket cutters, spur-gear cutters, corner-rounding cutters and slitting saws. Vertical cutters use shank-mounted cutting tools, including endmills, T-slot cutters, Woodruff keyseat cutters and dovetail cutters; these may also be used on horizontal mills. See milling.