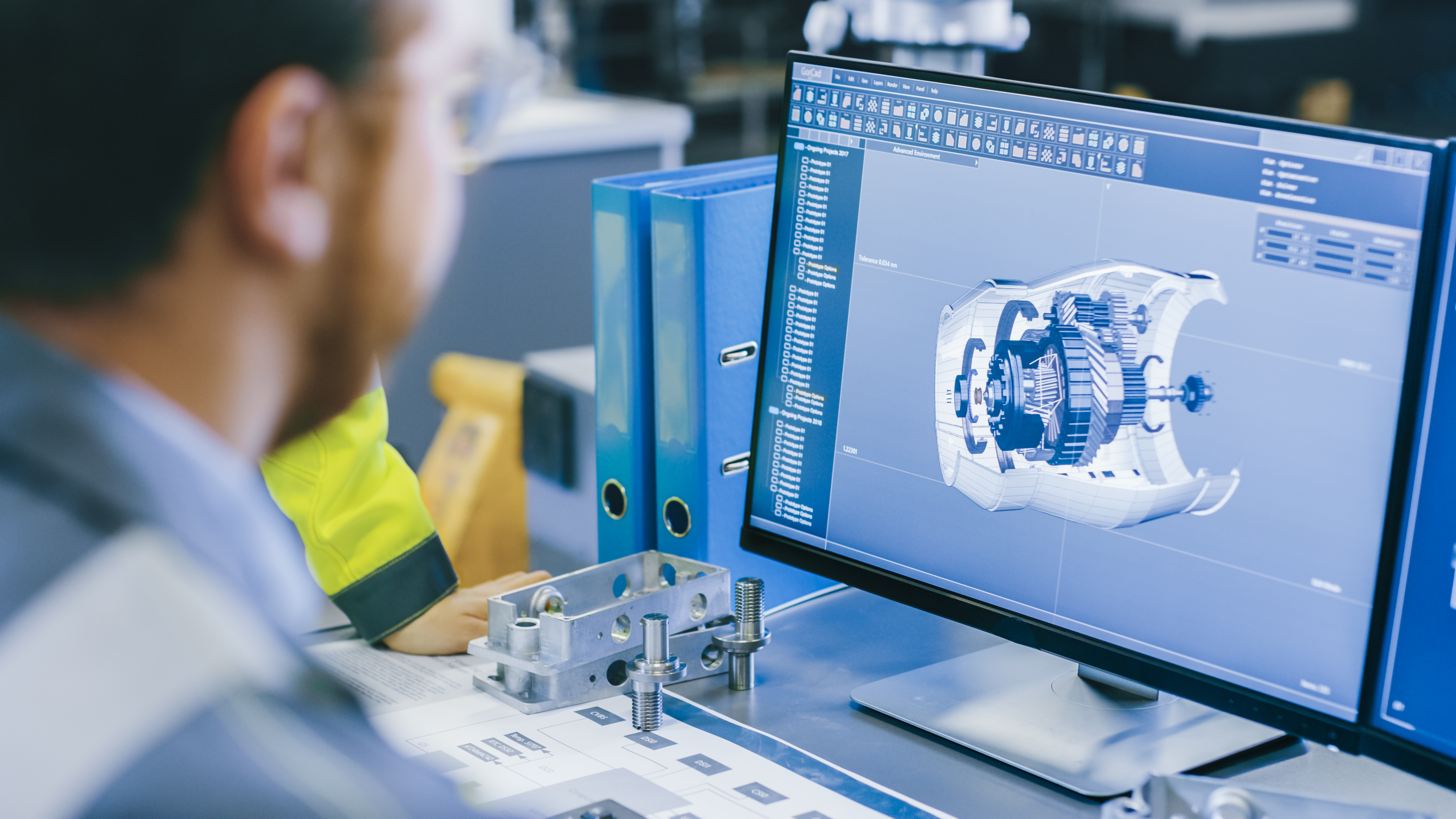
Article from NIMS
The National Institute for Metalworking Skills (NIMS) is now offering standardized CAM credentials, CAM Milling and Turning. “The CAM field continues to grow and is expected to create almost 100,000 new programmer, designer, and engineer jobs by 2024,” said NIMS Executive Director Montez King. “It is imperative that people entering the field are properly trained and capable, and these credentials show a potential employer that applicants are ready to program CNC machine tools. Further, employees already on the job may wish to secure an official, portable, industry-recognized certification.”
The new credentials are based on standards developed in partnership with and sponsored by Autodesk, a leader in 3D design and engineering software. Over 125 subject matter experts from organizations such as CNC Software, developer of Mastercam; Barefoot CNC; Arkansas State University Mid-South; CamInstructor, and custom machining technology leader, Rosenburger of North America, volunteered their insight during the rigorous development and piloting process of the standards.
Throughout the development process, field experts, within their technical work groups, identified the skills expected for entry-level CAM positions. As a result, these standards now define necessary competencies associated with job preparation, modeling, toolpath generation, documentation, written oral communication, machining mathematics, decision making and problem solving, social skills and personal qualities, engineering drawings and sketches, computer operations, and technologies.
“CAM is the first set of NIMS credentials to use our new Performance Measure (PM) Development Requirements for the hands-on component of the credential,” King said. “The new model will allow schools and employers to customize their credentialing experience by using their own projects to validate performance for NIMS credentials as long as they meet the minimum NIMS requirements.”
Manufacturing companies are expected to benefit greatly by having properly trained CAM programmers, designers and engineers. As cycle times decline, material waste and machining errors decrease, and the quality of parts increases with more capable personnel. It is predicted that individuals trained according to these standards will be in high demand in coming years.
Related Glossary Terms
- computer numerical control ( CNC)
computer numerical control ( CNC)
Microprocessor-based controller dedicated to a machine tool that permits the creation or modification of parts. Programmed numerical control activates the machine’s servos and spindle drives and controls the various machining operations. See DNC, direct numerical control; NC, numerical control.
- computer-aided manufacturing ( CAM)
computer-aided manufacturing ( CAM)
Use of computers to control machining and manufacturing processes.
- gang cutting ( milling)
gang cutting ( milling)
Machining with several cutters mounted on a single arbor, generally for simultaneous cutting.
- metalworking
metalworking
Any manufacturing process in which metal is processed or machined such that the workpiece is given a new shape. Broadly defined, the term includes processes such as design and layout, heat-treating, material handling and inspection.
- milling
milling
Machining operation in which metal or other material is removed by applying power to a rotating cutter. In vertical milling, the cutting tool is mounted vertically on the spindle. In horizontal milling, the cutting tool is mounted horizontally, either directly on the spindle or on an arbor. Horizontal milling is further broken down into conventional milling, where the cutter rotates opposite the direction of feed, or “up” into the workpiece; and climb milling, where the cutter rotates in the direction of feed, or “down” into the workpiece. Milling operations include plane or surface milling, endmilling, facemilling, angle milling, form milling and profiling.
- toolpath( cutter path)
toolpath( cutter path)
2-D or 3-D path generated by program code or a CAM system and followed by tool when machining a part.
- turning
turning
Workpiece is held in a chuck, mounted on a face plate or secured between centers and rotated while a cutting tool, normally a single-point tool, is fed into it along its periphery or across its end or face. Takes the form of straight turning (cutting along the periphery of the workpiece); taper turning (creating a taper); step turning (turning different-size diameters on the same work); chamfering (beveling an edge or shoulder); facing (cutting on an end); turning threads (usually external but can be internal); roughing (high-volume metal removal); and finishing (final light cuts). Performed on lathes, turning centers, chucking machines, automatic screw machines and similar machines.