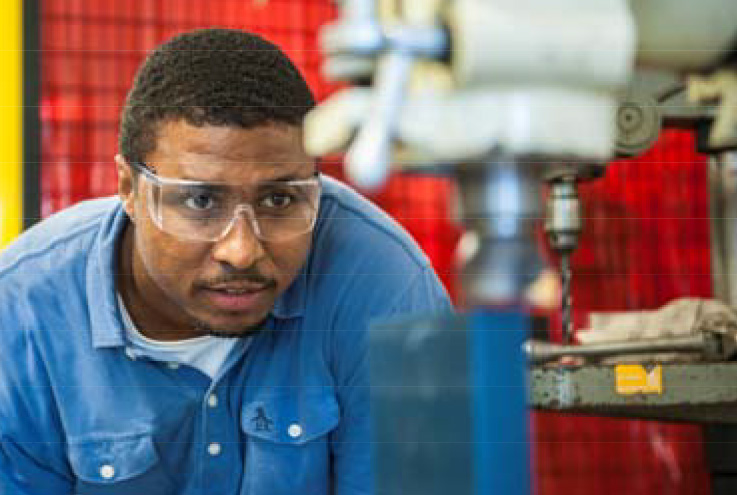
It’s no secret that many manufacturers are scrambling to attract skilled workers to fill openings. A host of training programs are available to provide job seekers with the skills needed to get hired, and one in my hometown of Chicago that caught my attention is the Jane Addams Resource Center.
I spoke with James Yoo, director of business and workforce services for JARC, to get a better idea about the types of programs the center offers and its approach to worker training. JARC started with a CNC machining program in 1985 to help local companies find prescreened, qualified, entry-level workers, he said. “Primarily, they were targeting the low-income adult population.”
The center, which serves about 100 trainees annually, also offers training for welders and anticipates restarting its press brake program later in the year, Yoo added.
He emphasized that the focus isn’t only on technical skills training. JARC also offers financial coaching, soft skills instruction and help with resume writing, and conducts mock interviews to prepare trainees for what manufacturers will require of them.
“We try to offer a wide range of services to make sure they are as successful as possible,” Yoo said.
That effort includes not giving trainees a pass when they behave in a less-than-professional manner. They must clock in, and attendance is mandatory, Yoo said. A trainee is docked a point for each missed day and terminated from the program after three such instances. “The whole point of the training is we want them to feel this is a real-life, work-simulator environment.”
Those who successfully complete the program for CNC milling and turning are NIMS-certified, Yoo noted, but their time isn’t only spent in a classroom. “It’s not just certification on paper, but it’s also to get them hands-on experience.”
The hands-on experience involves a couple hundred hours of machining, Yoo said, and the center has three Haas CNC machine tools: a lathe and two Mini Mills. The center takes a project-based approach to the machining portion of the program so trainees understand how to complete a task as efficiently and correctly as possible. “Metrology is a part of this, as well as shop math and blueprint reading.”
Yoo noted JARC works with foundations and receives public funds, so up to 100 percent of training costs can be covered. However, he added that the application process, which is open to the public, is rigorous. The process requires candidates to take a basic adult education test and achieve at least a ninth-grade level for math and reading. If that requirement isn’t met, the center offers a bridge program.
“You are in that bridge program,” Yoo said, “to basically skill up in math or reading and make sure you have the basic skills that you need to be an effective learner in either program.”
Related Glossary Terms
- computer numerical control ( CNC)
computer numerical control ( CNC)
Microprocessor-based controller dedicated to a machine tool that permits the creation or modification of parts. Programmed numerical control activates the machine’s servos and spindle drives and controls the various machining operations. See DNC, direct numerical control; NC, numerical control.
- gang cutting ( milling)
gang cutting ( milling)
Machining with several cutters mounted on a single arbor, generally for simultaneous cutting.
- lathe
lathe
Turning machine capable of sawing, milling, grinding, gear-cutting, drilling, reaming, boring, threading, facing, chamfering, grooving, knurling, spinning, parting, necking, taper-cutting, and cam- and eccentric-cutting, as well as step- and straight-turning. Comes in a variety of forms, ranging from manual to semiautomatic to fully automatic, with major types being engine lathes, turning and contouring lathes, turret lathes and numerical-control lathes. The engine lathe consists of a headstock and spindle, tailstock, bed, carriage (complete with apron) and cross slides. Features include gear- (speed) and feed-selector levers, toolpost, compound rest, lead screw and reversing lead screw, threading dial and rapid-traverse lever. Special lathe types include through-the-spindle, camshaft and crankshaft, brake drum and rotor, spinning and gun-barrel machines. Toolroom and bench lathes are used for precision work; the former for tool-and-die work and similar tasks, the latter for small workpieces (instruments, watches), normally without a power feed. Models are typically designated according to their “swing,” or the largest-diameter workpiece that can be rotated; bed length, or the distance between centers; and horsepower generated. See turning machine.
- milling
milling
Machining operation in which metal or other material is removed by applying power to a rotating cutter. In vertical milling, the cutting tool is mounted vertically on the spindle. In horizontal milling, the cutting tool is mounted horizontally, either directly on the spindle or on an arbor. Horizontal milling is further broken down into conventional milling, where the cutter rotates opposite the direction of feed, or “up” into the workpiece; and climb milling, where the cutter rotates in the direction of feed, or “down” into the workpiece. Milling operations include plane or surface milling, endmilling, facemilling, angle milling, form milling and profiling.
- turning
turning
Workpiece is held in a chuck, mounted on a face plate or secured between centers and rotated while a cutting tool, normally a single-point tool, is fed into it along its periphery or across its end or face. Takes the form of straight turning (cutting along the periphery of the workpiece); taper turning (creating a taper); step turning (turning different-size diameters on the same work); chamfering (beveling an edge or shoulder); facing (cutting on an end); turning threads (usually external but can be internal); roughing (high-volume metal removal); and finishing (final light cuts). Performed on lathes, turning centers, chucking machines, automatic screw machines and similar machines.