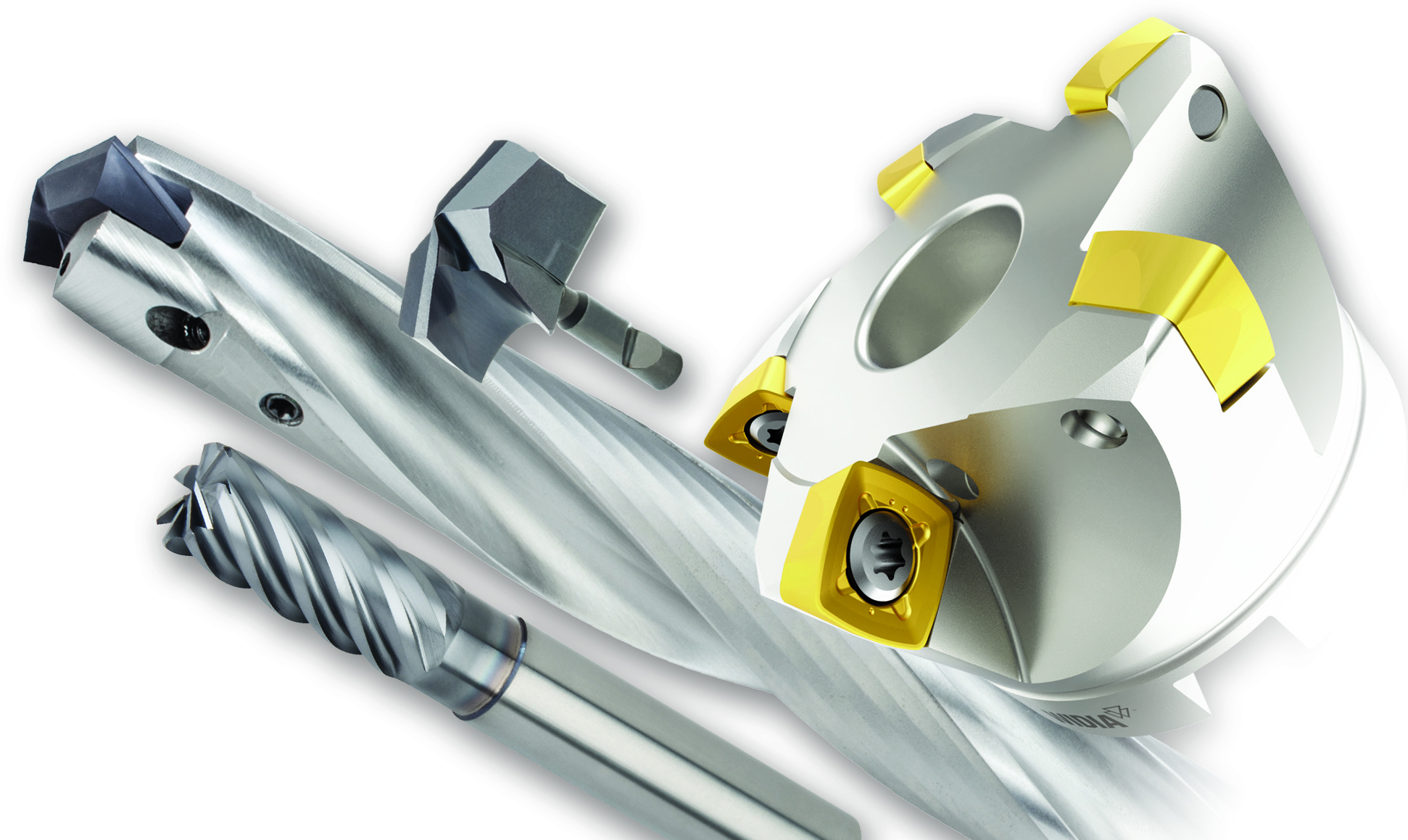
IBC announces that WIDIA Products Group, Latrobe, Pennsylvania, has joined the IBC industrial buying group as a preferred supplier. WIDIA is a leading manufacturer of precision metalcutting tools utilized in CNC machining operations. Products include endmills, drills, taps, indexable milling cutters, turning tools, threading tools and toolholders. Authorized independent distributors within the IBC buying group now have access to WIDIA’s complete portfolio of precision engineered products and services to offer end users in the U.S. plus parts of Canada, Mexico and the Caribbean.
“WIDIA is a global brand of innovative, performance cutting tools and is a significant addition to the IBC’s metalworking portfolio,” stated Mark R. Higgins, IBC business development, relations and recruitment. “WIDIA is led by Jeff Kraez, an industry veteran, who has assembled an outstanding team to assist IBC members. Our ability to provide ‘world class’ solutions for end-user customers has increased exponentially with WIDIA’s joining IBC.”
”WIDIA is excited about the opportunity to join forces with IBC and its members to help promote and grow the WIDIA brand,” said Jeff Kraez, general manager of WIDIA Americas. “Our position with current IBC distributors is already significant and we are confident that this partnership will only strengthen and prosper existing relationships as well as help to develop new ones.”
Contact Details
Related Glossary Terms
- computer numerical control ( CNC)
computer numerical control ( CNC)
Microprocessor-based controller dedicated to a machine tool that permits the creation or modification of parts. Programmed numerical control activates the machine’s servos and spindle drives and controls the various machining operations. See DNC, direct numerical control; NC, numerical control.
- gang cutting ( milling)
gang cutting ( milling)
Machining with several cutters mounted on a single arbor, generally for simultaneous cutting.
- metalcutting ( material cutting)
metalcutting ( material cutting)
Any machining process used to part metal or other material or give a workpiece a new configuration. Conventionally applies to machining operations in which a cutting tool mechanically removes material in the form of chips; applies to any process in which metal or material is removed to create new shapes. See metalforming.
- metalworking
metalworking
Any manufacturing process in which metal is processed or machined such that the workpiece is given a new shape. Broadly defined, the term includes processes such as design and layout, heat-treating, material handling and inspection.
- milling
milling
Machining operation in which metal or other material is removed by applying power to a rotating cutter. In vertical milling, the cutting tool is mounted vertically on the spindle. In horizontal milling, the cutting tool is mounted horizontally, either directly on the spindle or on an arbor. Horizontal milling is further broken down into conventional milling, where the cutter rotates opposite the direction of feed, or “up” into the workpiece; and climb milling, where the cutter rotates in the direction of feed, or “down” into the workpiece. Milling operations include plane or surface milling, endmilling, facemilling, angle milling, form milling and profiling.
- threading
threading
Process of both external (e.g., thread milling) and internal (e.g., tapping, thread milling) cutting, turning and rolling of threads into particular material. Standardized specifications are available to determine the desired results of the threading process. Numerous thread-series designations are written for specific applications. Threading often is performed on a lathe. Specifications such as thread height are critical in determining the strength of the threads. The material used is taken into consideration in determining the expected results of any particular application for that threaded piece. In external threading, a calculated depth is required as well as a particular angle to the cut. To perform internal threading, the exact diameter to bore the hole is critical before threading. The threads are distinguished from one another by the amount of tolerance and/or allowance that is specified. See turning.
- turning
turning
Workpiece is held in a chuck, mounted on a face plate or secured between centers and rotated while a cutting tool, normally a single-point tool, is fed into it along its periphery or across its end or face. Takes the form of straight turning (cutting along the periphery of the workpiece); taper turning (creating a taper); step turning (turning different-size diameters on the same work); chamfering (beveling an edge or shoulder); facing (cutting on an end); turning threads (usually external but can be internal); roughing (high-volume metal removal); and finishing (final light cuts). Performed on lathes, turning centers, chucking machines, automatic screw machines and similar machines.