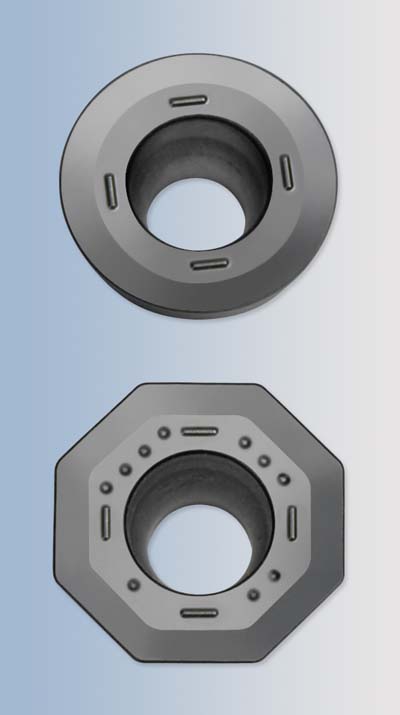
Dapra Corp. has expanded its Toroid Rhino-Carb CNC-pressed insert line with a new cutting edge geometry. Available for round and octagonal inserts, the new neutral ("N") cutting edge provides smoother cutting action for steels, irons and many stainless steels when compared to Dapra's stronger T-Land insert edge, according to the company.
Neutral inserts offer a higher-positive edge preparation and rake angle than their T-Land counterparts, providing enhanced cutting action that creates less heat and pressure while also offering greater strength than the very high-positive dished cutting edge.
Dapra now offers a trio of RHINO-CARB cutting edge options. T-Land ("T") inserts feature the strongest cutting edge and should be used where the heaviest cuts are taken, or where vibration or chatter may be causing edge damage. This geometry is suitable for steels, irons and 400-series stainless. The new Neutral ("N") geometry is intended for typical cutting applications where high-performance milling of steels, irons and 400-series stainless is desired. Dished ("D") inserts are suitable for applications where the lowest tool pressure and higher shear are required. This geometry is best for most stainless steels and high-temperature alloys, but it is also a free-cutting performer in softer steels.
Contact Details
Related Glossary Terms
- alloys
alloys
Substances having metallic properties and being composed of two or more chemical elements of which at least one is a metal.
- chatter
chatter
Condition of vibration involving the machine, workpiece and cutting tool. Once this condition arises, it is often self-sustaining until the problem is corrected. Chatter can be identified when lines or grooves appear at regular intervals in the workpiece. These lines or grooves are caused by the teeth of the cutter as they vibrate in and out of the workpiece and their spacing depends on the frequency of vibration.
- edge preparation
edge preparation
Conditioning of the cutting edge, such as a honing or chamfering, to make it stronger and less susceptible to chipping. A chamfer is a bevel on the tool’s cutting edge; the angle is measured from the cutting face downward and generally varies from 25° to 45°. Honing is the process of rounding or blunting the cutting edge with abrasives, either manually or mechanically.
- gang cutting ( milling)
gang cutting ( milling)
Machining with several cutters mounted on a single arbor, generally for simultaneous cutting.
- milling
milling
Machining operation in which metal or other material is removed by applying power to a rotating cutter. In vertical milling, the cutting tool is mounted vertically on the spindle. In horizontal milling, the cutting tool is mounted horizontally, either directly on the spindle or on an arbor. Horizontal milling is further broken down into conventional milling, where the cutter rotates opposite the direction of feed, or “up” into the workpiece; and climb milling, where the cutter rotates in the direction of feed, or “down” into the workpiece. Milling operations include plane or surface milling, endmilling, facemilling, angle milling, form milling and profiling.
- rake
rake
Angle of inclination between the face of the cutting tool and the workpiece. If the face of the tool lies in a plane through the axis of the workpiece, the tool is said to have a neutral, or zero, rake. If the inclination of the tool face makes the cutting edge more acute than when the rake angle is zero, the rake is positive. If the inclination of the tool face makes the cutting edge less acute or more blunt than when the rake angle is zero, the rake is negative.
- stainless steels
stainless steels
Stainless steels possess high strength, heat resistance, excellent workability and erosion resistance. Four general classes have been developed to cover a range of mechanical and physical properties for particular applications. The four classes are: the austenitic types of the chromium-nickel-manganese 200 series and the chromium-nickel 300 series; the martensitic types of the chromium, hardenable 400 series; the chromium, nonhardenable 400-series ferritic types; and the precipitation-hardening type of chromium-nickel alloys with additional elements that are hardenable by solution treating and aging.