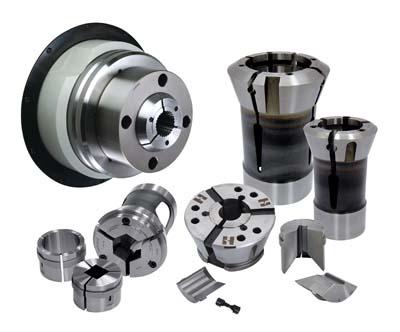
What tooling does a multi-spindle automatic, a CNC lathe and a vertical machining center have in common? The answer is S-pads. S-pads can be shared between many brands of machines whether the master collet is mounted directly in a machine spindle (single or multiple), in a collet adaptation chuck, or in a collet block. If you work in a multi-spindle shop, you already know how much faster it is to change pads, rather than collets, from job-to-job.
The style-S master collet, although originally designed for multi-spindle automatic screw machines, offers many benefits to the CNC lathe and vertical machining center operator as well. The collet pads can be changed much quicker than a standard collet, the cost is lower, and the pads require much less storage space. Standard S-pads from Hardinge are hardened and ground for a long life. Semi-hard and soft emergency pads can be bored-to-size on the machine for the best possible concentricity. Hardinge, the inventor of the S-pad concept, has a dedicated S-pad manufacturing cell enabling them to maintain stock availability on more than 1000 sizes of S-pads, in a variety of styles.
Hardinge's patented style-S pads can be changed without removing the master collet from the spindle, thus reducing changeover time. For example, on an eight-spindle automatic, all the pads can be changed in 15-30 minutes as compared to 2-3 hours that it would take to change the solid collets. Hardinge's dovetail anchor design securely holds the pad in place, and cannot be dislodged under normal use. No other front-loading pad can make this claim. The Hardinge design eliminates any pressure on the clamp. There are no holes in the OD of the master collet, or on the ID of the pads, resulting in maximum bearing on the workpiece and the spindle collet seat.
Hardinge S-pads are available in S10 through S50 sizes to fit Hardinge style-S master collets used in screw machines and CNC lathes. Style-S master collets designed for Hardinge collet-ready CNC lathes are available in 16C, 20C, 25C, B42 and B65. Hardinge HCAC collet adaptation chucks are available for chuck-style lathes to accept style-S master collet and pads. S-pads can also be used in the Hardinge FlexC™ collet blocks, as well as 16C collet blocks, for 3- and 4-axis milling applications. Hardinge provides stock delivery of most popular sizes, and quick turnaround for decimal sizes and specials. Pads are available in round, hexagon and square with smooth or serrated order holes, and special shapes.
Contact Details
Related Glossary Terms
- chuck
chuck
Workholding device that affixes to a mill, lathe or drill-press spindle. It holds a tool or workpiece by one end, allowing it to be rotated. May also be fitted to the machine table to hold a workpiece. Two or more adjustable jaws actually hold the tool or part. May be actuated manually, pneumatically, hydraulically or electrically. See collet.
- collet
collet
Flexible-sided device that secures a tool or workpiece. Similar in function to a chuck, but can accommodate only a narrow size range. Typically provides greater gripping force and precision than a chuck. See chuck.
- computer numerical control ( CNC)
computer numerical control ( CNC)
Microprocessor-based controller dedicated to a machine tool that permits the creation or modification of parts. Programmed numerical control activates the machine’s servos and spindle drives and controls the various machining operations. See DNC, direct numerical control; NC, numerical control.
- gang cutting ( milling)
gang cutting ( milling)
Machining with several cutters mounted on a single arbor, generally for simultaneous cutting.
- inner diameter ( ID)
inner diameter ( ID)
Dimension that defines the inside diameter of a cavity or hole. See OD, outer diameter.
- lathe
lathe
Turning machine capable of sawing, milling, grinding, gear-cutting, drilling, reaming, boring, threading, facing, chamfering, grooving, knurling, spinning, parting, necking, taper-cutting, and cam- and eccentric-cutting, as well as step- and straight-turning. Comes in a variety of forms, ranging from manual to semiautomatic to fully automatic, with major types being engine lathes, turning and contouring lathes, turret lathes and numerical-control lathes. The engine lathe consists of a headstock and spindle, tailstock, bed, carriage (complete with apron) and cross slides. Features include gear- (speed) and feed-selector levers, toolpost, compound rest, lead screw and reversing lead screw, threading dial and rapid-traverse lever. Special lathe types include through-the-spindle, camshaft and crankshaft, brake drum and rotor, spinning and gun-barrel machines. Toolroom and bench lathes are used for precision work; the former for tool-and-die work and similar tasks, the latter for small workpieces (instruments, watches), normally without a power feed. Models are typically designated according to their “swing,” or the largest-diameter workpiece that can be rotated; bed length, or the distance between centers; and horsepower generated. See turning machine.
- machining center
machining center
CNC machine tool capable of drilling, reaming, tapping, milling and boring. Normally comes with an automatic toolchanger. See automatic toolchanger.
- milling
milling
Machining operation in which metal or other material is removed by applying power to a rotating cutter. In vertical milling, the cutting tool is mounted vertically on the spindle. In horizontal milling, the cutting tool is mounted horizontally, either directly on the spindle or on an arbor. Horizontal milling is further broken down into conventional milling, where the cutter rotates opposite the direction of feed, or “up” into the workpiece; and climb milling, where the cutter rotates in the direction of feed, or “down” into the workpiece. Milling operations include plane or surface milling, endmilling, facemilling, angle milling, form milling and profiling.
- outer diameter ( OD)
outer diameter ( OD)
Dimension that defines the exterior diameter of a cylindrical or round part. See ID, inner diameter.