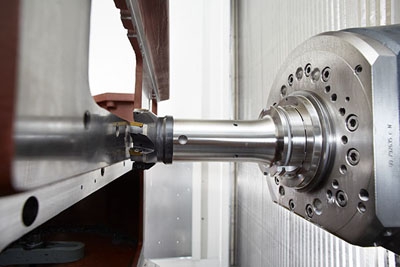
HELLER Machine Tools introduces the top range of its 4-axis H Series horizontal machining centers, the H 14000. This large capacity machine combines a super-robust machine design with the structural stiffness and high torque required for making the deepest cuts in the toughest alloy steels and irons. Developed and perfected over many years as the number one machine provider for large diesel engine component machining solutions Heller's H series is for machining large pumps and housings for power and fluid transmission.
The capacity of the H Series machines to make roughing cuts while still providing finishing accuracies for XYZ positioning of 0.010mm (according to VDI/GDQ 3441) make them ideal for large, difficult to machine alloy steel and iron components, according to the company. Feed forces of 20,000 N make it capable of making demanding cuts.
The Heller H 14000 is the top of the H-series, featuring a work area of 2400x1600x1600mm in X/Y/Z over a 1000mm pallet capable of handling a 4000kg workpiece load. HELLER has also minimized positioning times by focusing on realistic dynamic rates of 40 M/min in all axes.
Heller's NC out-facing head is available on the H 14000 for performing feed out operations on the machine such as taper boring, generating pockets, as well as compensating diameters. A measuring probe for on-machine part checking, and instant tool breakage monitoring are integrated. The machines, consistent with efficient cell operation are designed for manual or can be easily adapted to FMS systems or other automated loading systems.
With a high power cutting (HPC) gear-driven head stock, the H 14000 offers maximum torque of 2292 NM and generating 60 kW of power at low rpm with options available for rigid face clamping for right angle milling heads. HSK 100 spindle taper is standard with a choice of chain type tool magazines for tools up to 800mm length or rack type magazines with tool lengths up to 1000mm. The precision provided by all machine sizes in the H range is ensured through reduced table deformation and high precision due to internally arranged drives and linear scales. This provides high productivity and minimal axes positioning times resulting in reductions in machining times between 20 and 50 percent in practical application compared to competitive machines.
The H 14000 is designed with three chip augers that rapidly move chips out of the work area and into the chip conveyor, delivering the chips to the chip hopper. To support its global customers, Heller machines are equiped with either Siemens Sinumerik 840D or FANUC 31i-B CNC.
Contact Details
Related Glossary Terms
- alloy steels
alloy steels
Steel containing specified quantities of alloying elements (other than carbon and the commonly accepted amounts of manganese, sulfur and phosphorus) added to cause changes in the metal’s mechanical and/or physical properties. Principal alloying elements are nickel, chromium, molybdenum and silicon. Some grades of alloy steels contain one or more of these elements: vanadium, boron, lead and copper.
- boring
boring
Enlarging a hole that already has been drilled or cored. Generally, it is an operation of truing the previously drilled hole with a single-point, lathe-type tool. Boring is essentially internal turning, in that usually a single-point cutting tool forms the internal shape. Some tools are available with two cutting edges to balance cutting forces.
- centers
centers
Cone-shaped pins that support a workpiece by one or two ends during machining. The centers fit into holes drilled in the workpiece ends. Centers that turn with the workpiece are called “live” centers; those that do not are called “dead” centers.
- computer numerical control ( CNC)
computer numerical control ( CNC)
Microprocessor-based controller dedicated to a machine tool that permits the creation or modification of parts. Programmed numerical control activates the machine’s servos and spindle drives and controls the various machining operations. See DNC, direct numerical control; NC, numerical control.
- feed
feed
Rate of change of position of the tool as a whole, relative to the workpiece while cutting.
- flexible manufacturing system ( FMS)
flexible manufacturing system ( FMS)
Automated manufacturing system designed to machine a variety of similar parts. System is designed to minimize production changeover time. Computers link machine tools with the workhandling system and peripherals. Also associated with machine tools grouped in cells for efficient production. See cell manufacturing.
- gang cutting ( milling)
gang cutting ( milling)
Machining with several cutters mounted on a single arbor, generally for simultaneous cutting.
- milling
milling
Machining operation in which metal or other material is removed by applying power to a rotating cutter. In vertical milling, the cutting tool is mounted vertically on the spindle. In horizontal milling, the cutting tool is mounted horizontally, either directly on the spindle or on an arbor. Horizontal milling is further broken down into conventional milling, where the cutter rotates opposite the direction of feed, or “up” into the workpiece; and climb milling, where the cutter rotates in the direction of feed, or “down” into the workpiece. Milling operations include plane or surface milling, endmilling, facemilling, angle milling, form milling and profiling.
- numerical control ( NC)
numerical control ( NC)
Any controlled equipment that allows an operator to program its movement by entering a series of coded numbers and symbols. See CNC, computer numerical control; DNC, direct numerical control.
- stiffness
stiffness
1. Ability of a material or part to resist elastic deflection. 2. The rate of stress with respect to strain; the greater the stress required to produce a given strain, the stiffer the material is said to be. See dynamic stiffness; static stiffness.