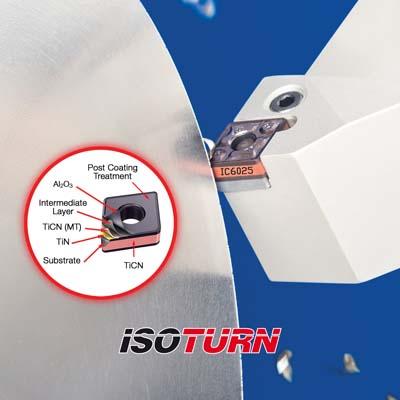
Following the introduction of grade IC6015, ISCAR is introducing an additional new, SUMO TEC CVD coated grade, IC6025, which was developed for machining stainless steel at moderate cutting speeds for stable or unstable conditions. The new grade IC6025 covers the application range of ISO (M20-35), used for roughing and interrupted cuts as well as applications at medium to low cutting speeds. It is composed of a cobalt enriched outer layer substrate, with MT TiCN and alpha aluminum-oxide coating with a special post coating treatment.
Although the coating process of the IC6025 is similar to that of IC6015, it differs with a tougher substrate, featuring a combination of high toughness and deformation resistance. The SUMO TEC MTCVD coating adds toughness, flaking and chipping resistance and thus provides very reliable performance.
The two new grades (IC6015 and IC6025) combined with the new chipformer configuration M3M provide a completely new standard for machining stainless steel. IC6015 covers the high speed machining area for continuous machining of stainless steel and high temperature alloys, while IC6025 is recommended for the interrupted cut applications.
ISCAR's new and innovative chipformer under the designation of M3M was designed especially for machining stainless and low carbon steel. In addition, it was designed with geometric features that improve the tool's life due to a reinforced cutting edge at the area where VG (notch wear) wear tends to occur when machining stainless steel, causing poor surface finish and risk of edge breakage. Additional geometric elements such as optimal positive rake angle feature a smooth cutting process and reduced cutting forces (by 5 to 10 percent), thus reducing the wear and dramatically increasing tool life. The M3M has a wide chipbreaking range.
Contact Details
Related Glossary Terms
- alloys
alloys
Substances having metallic properties and being composed of two or more chemical elements of which at least one is a metal.
- chemical vapor deposition ( CVD)
chemical vapor deposition ( CVD)
High-temperature (1,000° C or higher), atmosphere-controlled process in which a chemical reaction is induced for the purpose of depositing a coating 2µm to 12µm thick on a tool’s surface. See coated tools; PVD, physical vapor deposition.
- interrupted cut
interrupted cut
Cutting tool repeatedly enters and exits the work. Subjects tool to shock loading, making tool toughness, impact strength and flexibility vital. Closely associated with milling operations. See shock loading.
- rake
rake
Angle of inclination between the face of the cutting tool and the workpiece. If the face of the tool lies in a plane through the axis of the workpiece, the tool is said to have a neutral, or zero, rake. If the inclination of the tool face makes the cutting edge more acute than when the rake angle is zero, the rake is positive. If the inclination of the tool face makes the cutting edge less acute or more blunt than when the rake angle is zero, the rake is negative.
- titanium carbonitride ( TiCN)
titanium carbonitride ( TiCN)
Often used as a tool coating. See coated tools.