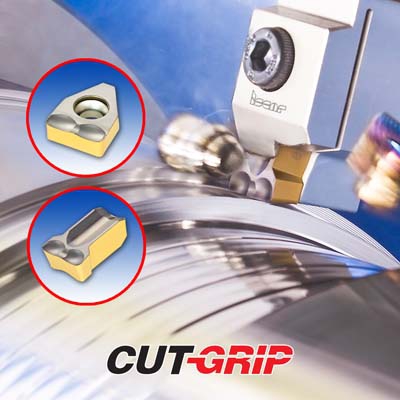
ISCAR TIGERV heavy-duty grooving inserts with a new chipformer design, ensure better tool security, chip control and ejection in difficult grooving operations on carbon and high-alloy steel even at slow speeds. They also can handle a wider range of applications and operating conditions.
Deep grooves in workpieces especially raise the risk of sudden tool failure, as surface cutting speed declines with radius and the deepening groove makes chip expulsion more uncertain. ISCAR's aggressive new CW chipformer is cup-shaped, pressed right into the TIGERV insert's top face behind the cutting edge. They drastically deform the chip coming off and break it into short open segments for optimal expulsion.
For long service in extreme grooving applications, the insert itself is made of the rugged SUMO TEC grade IC808. ISCAR offers the TIGERV-CW insert in 14 and 17mm widths with center-screw clamping, to fit into a V-lock toolholder with an absolutely flat top surface. The flat-top design ensures unobstructed chip flow, even from the bottom of a deep groove. The new TIGERV-CW grooving insert is recommended for carbon steel and high alloy steel and the original TIGER insert for stainless steel.
Contact Details
Related Glossary Terms
- cutting speed
cutting speed
Tangential velocity on the surface of the tool or workpiece at the cutting interface. The formula for cutting speed (sfm) is tool diameter 5 0.26 5 spindle speed (rpm). The formula for feed per tooth (fpt) is table feed (ipm)/number of flutes/spindle speed (rpm). The formula for spindle speed (rpm) is cutting speed (sfm) 5 3.82/tool diameter. The formula for table feed (ipm) is feed per tooth (ftp) 5 number of tool flutes 5 spindle speed (rpm).
- flat ( screw flat)
flat ( screw flat)
Flat surface machined into the shank of a cutting tool for enhanced holding of the tool.
- grooving
grooving
Machining grooves and shallow channels. Example: grooving ball-bearing raceways. Typically performed by tools that are capable of light cuts at high feed rates. Imparts high-quality finish.
- toolholder
toolholder
Secures a cutting tool during a machining operation. Basic types include block, cartridge, chuck, collet, fixed, modular, quick-change and rotating.