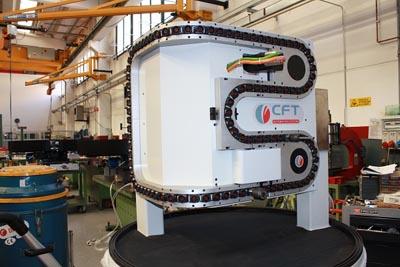
Automatic tool changers, type CTA — HSL from ITI Tooling Co. Inc. are suitable for applications on CNC milling machines, vertical and horizontal machining centers, CNC lathes and multi-tasking machines. CTA-HSL tool exchanger with a compact tool magazine are designed and manufactured to accommodate a high quantity of tool holders in a restricted area and are particularly suitable for use on smaller machine tools.
Each tool changer consists of:
A CTA dual-motion, cam-operated exchanger that performs the high speed and mechanically synchronized movements for grasping, extracting, exchanging and inserting the tools simultaneously between the spindle and the magazine, plus the release of the tool grippers. This entire high speed cycle is operated by one 3-phase, self-braking motor.
A mechanical exchange arm with dual "rapid-release" gripper hands and built-in safety interlocks.
The compact HSL series tool storage magazine, on which all toolholder pockets are hinged to enable a 90 deg. tilt during a tool exchange, are assembled in a moveable track within a support structure designed to gain the optimal utility from the available allotted space on smaller machine tools and is driven via a servo motor. The toolholder tilt unit is pneumatically operated as is the tool taper cleaning head actuated as the used tool is reinserted back into the magazine. A built-in switch system guarantees precise toolholder identification and is used for management of the migrating tools. In addition, a dedicated toolholder to tool pocket identification management system is available upon request.
The main characteristics of these self-contained CTA — HSL tool changers besides the simplicity, reliability and the cleanliness is the high capacity of tools that can be stored in the magazines and the ultra high speed tool exchange cycle itself.
This exchange time varies from 0.6 to 1.2 seconds, depending upon the frame size of unit, the tool weights and the length of the exchange arm.
Contact Details
Related Glossary Terms
- centers
centers
Cone-shaped pins that support a workpiece by one or two ends during machining. The centers fit into holes drilled in the workpiece ends. Centers that turn with the workpiece are called “live” centers; those that do not are called “dead” centers.
- computer numerical control ( CNC)
computer numerical control ( CNC)
Microprocessor-based controller dedicated to a machine tool that permits the creation or modification of parts. Programmed numerical control activates the machine’s servos and spindle drives and controls the various machining operations. See DNC, direct numerical control; NC, numerical control.
- gang cutting ( milling)
gang cutting ( milling)
Machining with several cutters mounted on a single arbor, generally for simultaneous cutting.
- milling
milling
Machining operation in which metal or other material is removed by applying power to a rotating cutter. In vertical milling, the cutting tool is mounted vertically on the spindle. In horizontal milling, the cutting tool is mounted horizontally, either directly on the spindle or on an arbor. Horizontal milling is further broken down into conventional milling, where the cutter rotates opposite the direction of feed, or “up” into the workpiece; and climb milling, where the cutter rotates in the direction of feed, or “down” into the workpiece. Milling operations include plane or surface milling, endmilling, facemilling, angle milling, form milling and profiling.
- toolholder
toolholder
Secures a cutting tool during a machining operation. Basic types include block, cartridge, chuck, collet, fixed, modular, quick-change and rotating.