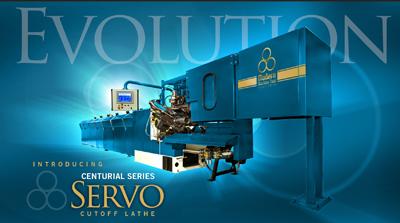
Fast-indexing Centurial CNC cutoff lathes from Modern Machine Tool Co., which is celebrating its 100th anniversary, can automatically load, cut off, chamfer, turn, bore, thread, drill and unload in one quick cycle. This versatile family of cutoff lathe machines combines CNC technology with many of Modern Machine Tool's most popular, production-proven design features.
Features:
EASY SET-UP AND FAST CHANGEOVER – Programmable setting of tools, feed rates and spindle speeds.
STANDARD CARBIDE INSERT TOOLING for turning and boring, in place of expensive form tools.
GE-FANUC CONTROLLED with CRT monitor and operator control panel. (Allen-Bradley CNC is available as an option.)
TWO CROSS SLIDES are fed by independent servo drives and ball screws. The single-axis cutoff slide moves perpendicular to the spindle, while the second slide has two axes of motion for turning, boring and threading. The X axis moves perpendicular to the spindle, the Z axis parallel.
COMPLEX FORMS can be turned by coordinating the movement of X and Z axes using the CNC control, eliminating the need for form tools.
PART LENGTH STOP is power clamped on an overhead beam and moved by a ball screw and hand crank. The stop travels on linear bearings and is positioned using a digital readout with a linear scale.
THE STOP RETRACTS clear of the stock after the collet closes, permitting easy automated unloading of machined parts.
SPINDLE DRIVE – 30 HP digital servo spindle drive. Standard CNC assures uniform surface speed. A 40 HP spindle drive is optional.
AUTOMATIC FEEDER holds large bundles of tube, pipe and bar stock.
STANDARD EQUIPMENT includes a roller feed assembly, circulating oil lubrication of main spindle bearings, high volume coolant pump and piping, fused disconnect and cycle counter.
OPTIONAL DISC-STYLE TOOL TURRET can be supplied for multiple operation tooling.
OPTIONAL SERVO-POSITIONED STOP allows precise positioning of the part length stop using the CNC, with offset control.
Contact Details
Related Glossary Terms
- boring
boring
Enlarging a hole that already has been drilled or cored. Generally, it is an operation of truing the previously drilled hole with a single-point, lathe-type tool. Boring is essentially internal turning, in that usually a single-point cutting tool forms the internal shape. Some tools are available with two cutting edges to balance cutting forces.
- collet
collet
Flexible-sided device that secures a tool or workpiece. Similar in function to a chuck, but can accommodate only a narrow size range. Typically provides greater gripping force and precision than a chuck. See chuck.
- computer numerical control ( CNC)
computer numerical control ( CNC)
Microprocessor-based controller dedicated to a machine tool that permits the creation or modification of parts. Programmed numerical control activates the machine’s servos and spindle drives and controls the various machining operations. See DNC, direct numerical control; NC, numerical control.
- coolant
coolant
Fluid that reduces temperature buildup at the tool/workpiece interface during machining. Normally takes the form of a liquid such as soluble or chemical mixtures (semisynthetic, synthetic) but can be pressurized air or other gas. Because of water’s ability to absorb great quantities of heat, it is widely used as a coolant and vehicle for various cutting compounds, with the water-to-compound ratio varying with the machining task. See cutting fluid; semisynthetic cutting fluid; soluble-oil cutting fluid; synthetic cutting fluid.
- cutoff
cutoff
Step that prepares a slug, blank or other workpiece for machining or other processing by separating it from the original stock. Performed on lathes, chucking machines, automatic screw machines and other turning machines. Also performed on milling machines, machining centers with slitting saws and sawing machines with cold (circular) saws, hacksaws, bandsaws or abrasive cutoff saws. See saw, sawing machine; turning.
- feed
feed
Rate of change of position of the tool as a whole, relative to the workpiece while cutting.
- lathe
lathe
Turning machine capable of sawing, milling, grinding, gear-cutting, drilling, reaming, boring, threading, facing, chamfering, grooving, knurling, spinning, parting, necking, taper-cutting, and cam- and eccentric-cutting, as well as step- and straight-turning. Comes in a variety of forms, ranging from manual to semiautomatic to fully automatic, with major types being engine lathes, turning and contouring lathes, turret lathes and numerical-control lathes. The engine lathe consists of a headstock and spindle, tailstock, bed, carriage (complete with apron) and cross slides. Features include gear- (speed) and feed-selector levers, toolpost, compound rest, lead screw and reversing lead screw, threading dial and rapid-traverse lever. Special lathe types include through-the-spindle, camshaft and crankshaft, brake drum and rotor, spinning and gun-barrel machines. Toolroom and bench lathes are used for precision work; the former for tool-and-die work and similar tasks, the latter for small workpieces (instruments, watches), normally without a power feed. Models are typically designated according to their “swing,” or the largest-diameter workpiece that can be rotated; bed length, or the distance between centers; and horsepower generated. See turning machine.
- parallel
parallel
Strip or block of precision-ground stock used to elevate a workpiece, while keeping it parallel to the worktable, to prevent cutter/table contact.
- threading
threading
Process of both external (e.g., thread milling) and internal (e.g., tapping, thread milling) cutting, turning and rolling of threads into particular material. Standardized specifications are available to determine the desired results of the threading process. Numerous thread-series designations are written for specific applications. Threading often is performed on a lathe. Specifications such as thread height are critical in determining the strength of the threads. The material used is taken into consideration in determining the expected results of any particular application for that threaded piece. In external threading, a calculated depth is required as well as a particular angle to the cut. To perform internal threading, the exact diameter to bore the hole is critical before threading. The threads are distinguished from one another by the amount of tolerance and/or allowance that is specified. See turning.
- turning
turning
Workpiece is held in a chuck, mounted on a face plate or secured between centers and rotated while a cutting tool, normally a single-point tool, is fed into it along its periphery or across its end or face. Takes the form of straight turning (cutting along the periphery of the workpiece); taper turning (creating a taper); step turning (turning different-size diameters on the same work); chamfering (beveling an edge or shoulder); facing (cutting on an end); turning threads (usually external but can be internal); roughing (high-volume metal removal); and finishing (final light cuts). Performed on lathes, turning centers, chucking machines, automatic screw machines and similar machines.