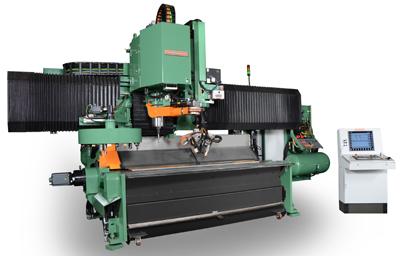
In today's market, it can be difficult for fabricators to compete when steel can be bought and sold at close to the same price as competitors. If a fabricator is currently using a burn table they have already experienced how much labor, floor space, and cost is involved with processing plate using older technology. Peddinghaus' solution to the burn table question is its newest plate processor, the HSFDB-C.
Capable of drilling, scribing, countersinking, tapping, milling, oxy-fuel and plasma cutting, the HSFDB-C is changing the way the world processes plate with its latest features including:
A unique bevel torch that is the only beveling system available on a true CNC plate processor. With the ability to feed material to the operating area of the machine as opposed to bringing the operating area of the machine to the material, the HSFDB-C benefits its users with less material handling, lower scrap due to tighter nesting, and a smaller footprint. The optional bevel cutting assembly maintains a single bevel cutting design for both the oxy-fuel and plasma cutting torch.
A SignoMat hard stamp part marking system of the HSFBD-C utilizes a single disc with 36 different characters for part numbering or layout requirements. The innovative design rotates 360 degrees to accommodate mirrored nesting. This allows any part to be oriented properly within a nest to yield the lowest amount of scrap possible.
A 12-station rotary tool changer that eliminates the need to manually change tooling during production. The efficient design of the HSFDB-C accompanies the spindle throughout the entire range of motion to ensure that no time is wasted when a new tool must be retrieved. Each drilling unit is immediately available as needed upon program command.
Using the latest technology, the HSFDB-C processes plate up to 4" (100mm) thick and is available in 6 ft. (1.8 M), 8 ft. (2.5 M) and 10 ft. (3.2 M) widths.
Contact Details
Related Glossary Terms
- computer numerical control ( CNC)
computer numerical control ( CNC)
Microprocessor-based controller dedicated to a machine tool that permits the creation or modification of parts. Programmed numerical control activates the machine’s servos and spindle drives and controls the various machining operations. See DNC, direct numerical control; NC, numerical control.
- countersinking
countersinking
Cutting a beveled edge at the entrance of a hole so a screw head sits flush with the workpiece surface.
- feed
feed
Rate of change of position of the tool as a whole, relative to the workpiece while cutting.
- gang cutting ( milling)
gang cutting ( milling)
Machining with several cutters mounted on a single arbor, generally for simultaneous cutting.
- milling
milling
Machining operation in which metal or other material is removed by applying power to a rotating cutter. In vertical milling, the cutting tool is mounted vertically on the spindle. In horizontal milling, the cutting tool is mounted horizontally, either directly on the spindle or on an arbor. Horizontal milling is further broken down into conventional milling, where the cutter rotates opposite the direction of feed, or “up” into the workpiece; and climb milling, where the cutter rotates in the direction of feed, or “down” into the workpiece. Milling operations include plane or surface milling, endmilling, facemilling, angle milling, form milling and profiling.
- tapping
tapping
Machining operation in which a tap, with teeth on its periphery, cuts internal threads in a predrilled hole having a smaller diameter than the tap diameter. Threads are formed by a combined rotary and axial-relative motion between tap and workpiece. See tap.