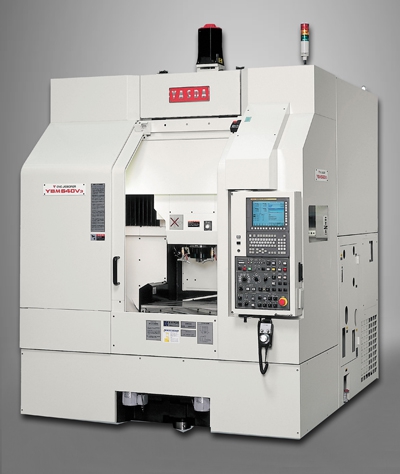
Methods Machine Tools Inc. has announced the introduction of the new Yasda YBM 640V3 3-Axis CNC vertical jig borer, which provides high-speed, precision boring and milling operations for high accuracy mold, die and complex component manufacturing. The new YBM 640V3 simplifies moldmaking in industries such as aerospace, automotive, medical, defense and more, as well as the production of electronic, optical and other extremely complex components, according to the company. The accuracy and rigidity of the YBM 640V3 jig borer virtually eliminates the need for hand polishing.
"Yasda jig borers consistently achieve outstanding performance in heavy duty machining, something conventional jig borers have traditionally not been known for," said David Lucius, Vice President of Sales for Methods Machine Tools. "A very innovative, unique design fully optimizes the rigidity, repeatability and thermal stability of the Yasda YBM 640V3 for the utmost in accuracy, precision and throughput."
To minimize vibration during acceleration and deceleration, a reinforcement rib under the bridge provides great rigidity. Machining efficiency is optimized by keeping the weight of the spindle head and saddle as low as possible. Meticulous hand scraped alignment of through-hardened 60 RC boxed ways provides outstanding mechanical accuracy. An exclusive spindle bearing preload self-adjusting technology provides optimum preload at the full range of spindle speeds. A rugged spindle enables a full range of machining from heavy duty roughing to delicate fine finishing, all while providing a long tool and spindle bearing life.
To reduce thermal distortion, a bridge cooling system is located under the X-Axis guide, and a jacket cooling system for X and Y-Axis ball nuts prevents loss of ball screw pre-tension. Productivity is further increased by improved chip disposal and large coolant and lubrication tank capacities.
The 3-Axis Yasda YBM 640V3 has a standard spindle speed of up to 24,000 RPM (30,000 RPM optional) and a 7/24 taper, No. 40 spindle taper hole. The table size is 27.5 inches (700mm) x 17.7 inches (450mm) with a table loading capacity of 661 lbs (300 kg). X-axis travel is 23.6 inches (600mm), Y-Axis travel is 15.7 inches (400mm) and Z-Axis travel is13.8 inches (350mm). The automatic tool changer has a maximum storage of up to 100 tools. The YBM 640V3 is equipped with a FANUC 31i-Model 5 controller. The Yasda YBM 640V3 is the smallest of a complete vertical line-up of Yasda CNC Jig Borers with the largest 1218V model reaching travels of 71 inches (1,800mm) x 47 inches (1,200mm) x 23.6 inches 600mm.
Contact Details
Related Glossary Terms
- boring
boring
Enlarging a hole that already has been drilled or cored. Generally, it is an operation of truing the previously drilled hole with a single-point, lathe-type tool. Boring is essentially internal turning, in that usually a single-point cutting tool forms the internal shape. Some tools are available with two cutting edges to balance cutting forces.
- computer numerical control ( CNC)
computer numerical control ( CNC)
Microprocessor-based controller dedicated to a machine tool that permits the creation or modification of parts. Programmed numerical control activates the machine’s servos and spindle drives and controls the various machining operations. See DNC, direct numerical control; NC, numerical control.
- coolant
coolant
Fluid that reduces temperature buildup at the tool/workpiece interface during machining. Normally takes the form of a liquid such as soluble or chemical mixtures (semisynthetic, synthetic) but can be pressurized air or other gas. Because of water’s ability to absorb great quantities of heat, it is widely used as a coolant and vehicle for various cutting compounds, with the water-to-compound ratio varying with the machining task. See cutting fluid; semisynthetic cutting fluid; soluble-oil cutting fluid; synthetic cutting fluid.
- gang cutting ( milling)
gang cutting ( milling)
Machining with several cutters mounted on a single arbor, generally for simultaneous cutting.
- jig
jig
Tooling usually considered to be a stationary apparatus. A jig assists in the assembly or manufacture of a part or device. It holds the workpiece while guiding the cutting tool with a bushing. A jig used in subassembly or final assembly might provide assembly aids such as alignments and adjustments. See fixture.
- milling
milling
Machining operation in which metal or other material is removed by applying power to a rotating cutter. In vertical milling, the cutting tool is mounted vertically on the spindle. In horizontal milling, the cutting tool is mounted horizontally, either directly on the spindle or on an arbor. Horizontal milling is further broken down into conventional milling, where the cutter rotates opposite the direction of feed, or “up” into the workpiece; and climb milling, where the cutter rotates in the direction of feed, or “down” into the workpiece. Milling operations include plane or surface milling, endmilling, facemilling, angle milling, form milling and profiling.
- polishing
polishing
Abrasive process that improves surface finish and blends contours. Abrasive particles attached to a flexible backing abrade the workpiece.