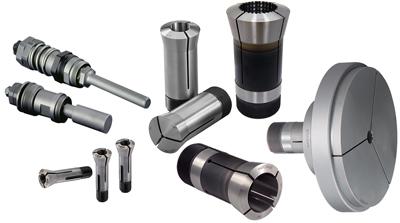
Hardinge Inc. began production of collets in the 1890s for use on bench lathes making parts for the watchmaking and lens industries. It is believed that the "C" designation for their first 5C collets came from the name of the Cataract waterfalls that could be viewed from the factory grounds of the Hardinge Brothers Co. in Chicago, where they manufactured precision Cataract bench lathes. Incredibly, the Hardinge C-series design has not changed since the early use in the 1890s, even in light of the rapidly changing technology in machine tool design.
A collet has the capability to accurately grip a workpiece or a tool, resisting both rotational forces and multidirectional cutting loads with the ability to rapidly release the workpiece or the tool. A collet has the capability to amplify the actuation force, converting it into workpiece gripping or tool gripping with the ability to operate at high repetition levels without loss of accuracy or material failure. It also has the ability to operate at a wide range of rotational speeds with minimal loss of gripping force.
Hardinge C-Series collets, in sizes ranging from 1C up to 25C, are used in manual and CNC lathes, mills, grinding machines, collet blocks and closers, indexers, rotary tables and tool holders. The Hardinge collet is manufactured to exacting standards from special alloy steel. Threads are heat treated and the body is spring tempered to assure accuracy and durability. Hardinge C-series collets are available in fractional sizes of round, hexagon and square to capacity. In addition, many round collets are stocked in metric, decimal, letter and number sizes. Most of the popular sizes of round serrated, taper hole and regular collets are available from stock. Special accuracy 5C collets with a guaranteed maximum TIR of .0002" are available. Collet variations include emergency collets, step collets, extended-nose collets, step chucks (stepped out collets that hold larger diameters), and Dead-Length collet systems for controlling workpiece lengths.
The standard Hardinge 5C-series collet, with an order hole of .9843" or less includes precision internal threads to permit the use of Hardinge positive solid and ejector stops. The Hardinge stops are threaded into and positively locked against the end of the collet and are adjustable and machineable for the desired part length to accommodate a wide variety of chucking work. Once locked in place, the stop cannot move even under heavy drilling or other end-working pressures. Universal stops are available for 5C collets and 16C spindles.
Contact Details
Related Glossary Terms
- collet
collet
Flexible-sided device that secures a tool or workpiece. Similar in function to a chuck, but can accommodate only a narrow size range. Typically provides greater gripping force and precision than a chuck. See chuck.
- computer numerical control ( CNC)
computer numerical control ( CNC)
Microprocessor-based controller dedicated to a machine tool that permits the creation or modification of parts. Programmed numerical control activates the machine’s servos and spindle drives and controls the various machining operations. See DNC, direct numerical control; NC, numerical control.
- grinding
grinding
Machining operation in which material is removed from the workpiece by a powered abrasive wheel, stone, belt, paste, sheet, compound, slurry, etc. Takes various forms: surface grinding (creates flat and/or squared surfaces); cylindrical grinding (for external cylindrical and tapered shapes, fillets, undercuts, etc.); centerless grinding; chamfering; thread and form grinding; tool and cutter grinding; offhand grinding; lapping and polishing (grinding with extremely fine grits to create ultrasmooth surfaces); honing; and disc grinding.
- total indicator runout ( TIR)
total indicator runout ( TIR)
Combined variations of all dimensions of a workpiece, measured with an indicator, determined by rotating the part 360°.