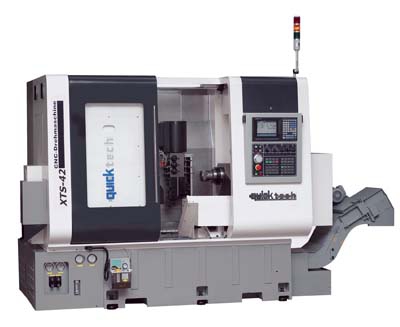
Machine tool importer Absolute Machine Tools Inc. has introduced the Quicktech XTS-42 7-axis twin spindle multi-tasking turning center. The high precision, high production CNC bar processing center enables complete part machining including milling of complex features.
Available in both 42mm and 60mm (1.65" or 2.36") bar capacities as the XTS-42 or XTS-60, the machines feature 7 axes, 2 turning spindles, 1 milling spindle, and a capacity of 27 tools. A 3-axis (X,Y, Z) gang type vertical tool post serves each spindle, with the tool post featuring a full B axis for the live tools. Maximum turning length for the main spindle is 226mm (9.05"), and maximum turning diameter for the subspindle is 98.5mm (3.94"). The main spindle has a 15HP high torque spindle motor, and the sub-spindle is equipped with a 5HP high torque spindle motor for backworking. Both spindles feature a full continuous C axis with braking system and standard 42mm DIN-173-42B collet chucks.
The main spindle has either 42mm or 60mm bar capacity, the sub-spindle has 30mm (1.18") bar capacity, and the spindles are synchronized for fast and accurate part transfer. The cartridge-type spindles employ P4 high precision bearings for stability and heavy cutting ability.
Each spindle is served by a single 3-axis gang tooling system. The tool post features 7 O.D. turning tools (4 front, 3 rear), 1 cut-off toolholder, 10 I.D. turning tools (5 front, 5 rear), 3 radial live tool heads and 6 axial live tool heads (3 front, 3 rear). The live heads are powered by a 2HP spindle motor. The B axis allows the live tools to rotate -45ÌÜÅÁ to +45ÌÜÅÁ and be applied to both the main and the sub spindle. In addition, the tool post has a Y axis for off-center milling operations.
Contact Details
Related Glossary Terms
- collet
collet
Flexible-sided device that secures a tool or workpiece. Similar in function to a chuck, but can accommodate only a narrow size range. Typically provides greater gripping force and precision than a chuck. See chuck.
- computer numerical control ( CNC)
computer numerical control ( CNC)
Microprocessor-based controller dedicated to a machine tool that permits the creation or modification of parts. Programmed numerical control activates the machine’s servos and spindle drives and controls the various machining operations. See DNC, direct numerical control; NC, numerical control.
- gang cutting ( milling)
gang cutting ( milling)
Machining with several cutters mounted on a single arbor, generally for simultaneous cutting.
- milling
milling
Machining operation in which metal or other material is removed by applying power to a rotating cutter. In vertical milling, the cutting tool is mounted vertically on the spindle. In horizontal milling, the cutting tool is mounted horizontally, either directly on the spindle or on an arbor. Horizontal milling is further broken down into conventional milling, where the cutter rotates opposite the direction of feed, or “up” into the workpiece; and climb milling, where the cutter rotates in the direction of feed, or “down” into the workpiece. Milling operations include plane or surface milling, endmilling, facemilling, angle milling, form milling and profiling.
- toolholder
toolholder
Secures a cutting tool during a machining operation. Basic types include block, cartridge, chuck, collet, fixed, modular, quick-change and rotating.
- turning
turning
Workpiece is held in a chuck, mounted on a face plate or secured between centers and rotated while a cutting tool, normally a single-point tool, is fed into it along its periphery or across its end or face. Takes the form of straight turning (cutting along the periphery of the workpiece); taper turning (creating a taper); step turning (turning different-size diameters on the same work); chamfering (beveling an edge or shoulder); facing (cutting on an end); turning threads (usually external but can be internal); roughing (high-volume metal removal); and finishing (final light cuts). Performed on lathes, turning centers, chucking machines, automatic screw machines and similar machines.