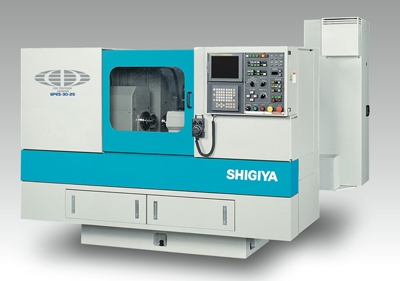
Shigiya (USA) Ltd. introduces its efficient and high-accuracy GPES-30 Series of CNC eccentric pin/polygon grinders. Featuring a rigid base and thermal expansion control, the GPES-30 is designed for accuracy.
The GPES-30's process of grinding two different eccentric areas within the same chucking eliminates or drastically reduces setup time. Journal grinding and face grinding options are available. An innovative polygon grinding method also eliminates or reduces training and adjusting. Plunge, oscillation and traverse grinding are also available.
For smooth and stable movement, the GPES-30 features closed hydrostatic slideways for the wheelhead feed, which automatically adjust to maintain the position of the wheelhead. As a result, eccentric grinding can be performed to an accuracy of less than 1µm.
A high-speed non-circular wedge-type hydrodynamic spindle bearing further contributes to high accuracy and high efficiency grinding. The direct drive spindle features a high precision angular contact bearing with no backlash on movement. Located behind the workhead, the rotary diamond dresser's spindle is supported by an ultra precise angular contact bearing and lubricated with Micro-fog. An AE sensor and wheel flatness sensor are also included as standard. The GPES-30's tailstock is mounted with a large diameter spindle to further ensure high precision heavy grinding.
The GPES-30 is controlled with Shigiya's easy-to-use conversational programming system. With this system, eccentric pin grinding offset direction can be quickly measured with the OD gauge, and operators can choose from 13 polygon pre-programmed shapes. Other features of the system include shape compensation, automatic workhead speed override, automatic grinding conditions, a new wheel dressing cycle and an indicator for X-axis speed and acceleration.
The GPES-30 features a 300mm swing over table, and 250mm or 630mm distance between centers. Wheel size is 350 (OD) x 25 (W) x 127 (ID)mm.
Contact Details
Related Glossary Terms
- backlash
backlash
Reaction in dynamic motion systems where potential energy that was created while the object was in motion is released when the object stops. Release of this potential energy or inertia causes the device to quickly snap backward relative to the last direction of motion. Backlash can cause a system’s final resting position to be different from what was intended and from where the control system intended to stop the device.
- centers
centers
Cone-shaped pins that support a workpiece by one or two ends during machining. The centers fit into holes drilled in the workpiece ends. Centers that turn with the workpiece are called “live” centers; those that do not are called “dead” centers.
- computer numerical control ( CNC)
computer numerical control ( CNC)
Microprocessor-based controller dedicated to a machine tool that permits the creation or modification of parts. Programmed numerical control activates the machine’s servos and spindle drives and controls the various machining operations. See DNC, direct numerical control; NC, numerical control.
- conversational programming
conversational programming
Method for using plain English to produce G-code file without knowing G-code in order to program CNC machines.
- dressing
dressing
Removal of undesirable materials from “loaded” grinding wheels using a single- or multi-point diamond or other tool. The process also exposes unused, sharp abrasive points. See loading; truing.
- feed
feed
Rate of change of position of the tool as a whole, relative to the workpiece while cutting.
- grinding
grinding
Machining operation in which material is removed from the workpiece by a powered abrasive wheel, stone, belt, paste, sheet, compound, slurry, etc. Takes various forms: surface grinding (creates flat and/or squared surfaces); cylindrical grinding (for external cylindrical and tapered shapes, fillets, undercuts, etc.); centerless grinding; chamfering; thread and form grinding; tool and cutter grinding; offhand grinding; lapping and polishing (grinding with extremely fine grits to create ultrasmooth surfaces); honing; and disc grinding.
- outer diameter ( OD)
outer diameter ( OD)
Dimension that defines the exterior diameter of a cylindrical or round part. See ID, inner diameter.