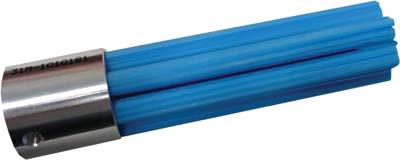
Xebec Deburring Technologies LLC has added a new brush to its lineup of surface deburring brushes. The new "blue" brush is the most aggressive in the lineup and can tackle burrs in today's toughest materials: it is a proven problem solver in titanium castings for the aerospace and defense industries. The brush gets its enhanced deburring action as a result of thicker and stiffer ceramic fiber bristles, making it 3 times more aggressive. The unique self-sharpening ceramic fiber bristles of the Xebec product provide a continuous cutting edge and consistent grinding performance. Each bristle contains 1000 alumina fiber filaments, with no fillers or binders, providing end to end abrasive material in each bristle.
Recently, a customer approached Deburring Technologies because they were having zero success deburring a cast titanium engine housing on their CNC machines. The parts were being processed offline by hand and operator fatigue and injuries were a frequent problem. This, in turn, led to poor part quality and scrap. The part had 2 milled surfaces with burr sizes of .030 that were very sharp. Our Xebec 40mm blue surface brush with sleeve was programmed to run around a 30" diameter flange using a 5 degree ramp in to break up the initial depth of cut. We were highly successful in both removing the sharp .030 burrs and achieving the desired .015 edge break running at 1125 RPM; feeding at 15 IPM; with a .090 depth of cut. After running 10 parts there was only .020 wear on the brush, which translates to less than $50 per part based on the 5 minute cycle time and tool cost. The previous method by hand took an operator 6-8 hours to complete with high scrap rates. Today, the customer continues to deburr the parts directly on the machine with the Xebec blue brush and achieves consistently high quality parts each time.
Xebec's current surface brush lineup consists of 4 colors which denote the level of cutting aggressiveness. Pink is the softest and most flexible and is well suited for intricate parts and softer materials. Red is a little stiffer and more aggressive, being well suited for materials less than 45HRC. More rigid and aggressive still is white which can handle larger burrs followed by blue which can handle burrs up to 1mm in tough materials. The pink brush is available only in 15mm while the other 3 colors are available in 6mm, 15mm, 25mm, 40mm, 60mm, and 100mm diameters. A corresponding Xebec sleeve in each size serves as a holder. In addition, a floating holder is available for brushes up to 40mm. The floating holder maintains even pressure thereby improving brush life and surface finish while reducing time needed to adjust projection length of the ceramic fibers. In addition to deburring, the brushes have the ability to achieve surface finishes as low as 10ra in some materials.
Contact Details
Related Glossary Terms
- abrasive
abrasive
Substance used for grinding, honing, lapping, superfinishing and polishing. Examples include garnet, emery, corundum, silicon carbide, cubic boron nitride and diamond in various grit sizes.
- burr
burr
Stringy portions of material formed on workpiece edges during machining. Often sharp. Can be removed with hand files, abrasive wheels or belts, wire wheels, abrasive-fiber brushes, waterjet equipment or other methods.
- computer numerical control ( CNC)
computer numerical control ( CNC)
Microprocessor-based controller dedicated to a machine tool that permits the creation or modification of parts. Programmed numerical control activates the machine’s servos and spindle drives and controls the various machining operations. See DNC, direct numerical control; NC, numerical control.
- depth of cut
depth of cut
Distance between the bottom of the cut and the uncut surface of the workpiece, measured in a direction at right angles to the machined surface of the workpiece.
- fatigue
fatigue
Phenomenon leading to fracture under repeated or fluctuating stresses having a maximum value less than the tensile strength of the material. Fatigue fractures are progressive, beginning as minute cracks that grow under the action of the fluctuating stress.
- grinding
grinding
Machining operation in which material is removed from the workpiece by a powered abrasive wheel, stone, belt, paste, sheet, compound, slurry, etc. Takes various forms: surface grinding (creates flat and/or squared surfaces); cylindrical grinding (for external cylindrical and tapered shapes, fillets, undercuts, etc.); centerless grinding; chamfering; thread and form grinding; tool and cutter grinding; offhand grinding; lapping and polishing (grinding with extremely fine grits to create ultrasmooth surfaces); honing; and disc grinding.