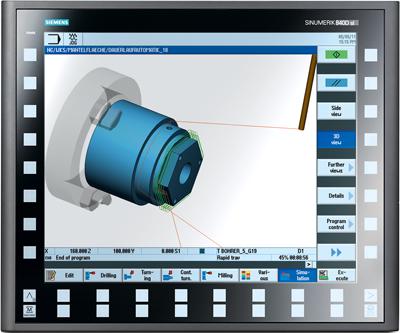
Siemens OP 019 is a new CNC operator panel with advanced technology, enabling seamless design integration to the Sinumerik Operate graphical user interface and Sinumerik 840D sl CNC for use on high-end milling, turning, grinding, laser-cutting and other machine tools.
With the benefit of modern touchscreen operation, this new Sinumerik operator panel OP 019, now extended to include the new Power Control Unit (PCU) 50.5, allows high-speed key actuation at the large 19-inch glass front, which conforms to the IP66 protection rating. Another new feature of the OP 019 design is the wide LEDs, which allow the operator to clearly visualize every key actuation, no matter what the angle of vision plus an integrated key lock that helps safeguard against operating errors. The newoperator panel is able to provide a basic machine display with three or four channels showing up to 13 axes. An operator gets the best overview with maximum detail on digitized drawings, owing to the 19-inch display with 1280 x 1024 pixel resolution.
The result of an advanced capacitive sensory system, glass contact buttons located on the perimeter of the display panel allow easy and reliable functionality, even when the operator is wearing gloves. With a compact yet powerful design, the OP 019 operator panel has a height of just 15.75". Parallel display of dual-channel or axis machine data is provided, as well.
OP 019 panels are designed to quickly and easily replace existing Sinumerik display panels in the field.
Contact Details
Related Glossary Terms
- computer numerical control ( CNC)
computer numerical control ( CNC)
Microprocessor-based controller dedicated to a machine tool that permits the creation or modification of parts. Programmed numerical control activates the machine’s servos and spindle drives and controls the various machining operations. See DNC, direct numerical control; NC, numerical control.
- gang cutting ( milling)
gang cutting ( milling)
Machining with several cutters mounted on a single arbor, generally for simultaneous cutting.
- grinding
grinding
Machining operation in which material is removed from the workpiece by a powered abrasive wheel, stone, belt, paste, sheet, compound, slurry, etc. Takes various forms: surface grinding (creates flat and/or squared surfaces); cylindrical grinding (for external cylindrical and tapered shapes, fillets, undercuts, etc.); centerless grinding; chamfering; thread and form grinding; tool and cutter grinding; offhand grinding; lapping and polishing (grinding with extremely fine grits to create ultrasmooth surfaces); honing; and disc grinding.
- milling
milling
Machining operation in which metal or other material is removed by applying power to a rotating cutter. In vertical milling, the cutting tool is mounted vertically on the spindle. In horizontal milling, the cutting tool is mounted horizontally, either directly on the spindle or on an arbor. Horizontal milling is further broken down into conventional milling, where the cutter rotates opposite the direction of feed, or “up” into the workpiece; and climb milling, where the cutter rotates in the direction of feed, or “down” into the workpiece. Milling operations include plane or surface milling, endmilling, facemilling, angle milling, form milling and profiling.
- parallel
parallel
Strip or block of precision-ground stock used to elevate a workpiece, while keeping it parallel to the worktable, to prevent cutter/table contact.
- turning
turning
Workpiece is held in a chuck, mounted on a face plate or secured between centers and rotated while a cutting tool, normally a single-point tool, is fed into it along its periphery or across its end or face. Takes the form of straight turning (cutting along the periphery of the workpiece); taper turning (creating a taper); step turning (turning different-size diameters on the same work); chamfering (beveling an edge or shoulder); facing (cutting on an end); turning threads (usually external but can be internal); roughing (high-volume metal removal); and finishing (final light cuts). Performed on lathes, turning centers, chucking machines, automatic screw machines and similar machines.