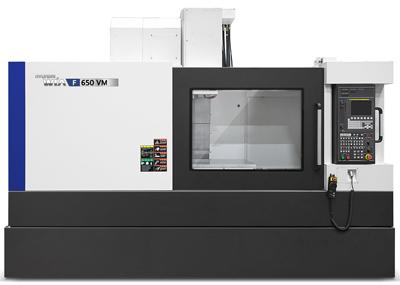
Hyundai WIA announces its latest addition to the wildly popular Value Master range of CNC vertical machining centers, the F650VM. Developed to offer premium performance at an affordable price, the F650VM is bundled with an impressive list of high-performance options as standard. Standard features include: a 30-tool swing arm tool changer, Thru Spindle Coolant, Big Plus Spindle, Rigid Tapping and a 10.4" color LCD. More significant, Value Master machining centers are built upon the same ridged foundation, leveraging Hyundai WIA's knowledge and expertise as a leading designer and builder of high-production machines tools.
The bed, column and saddle of Hyundai WIA's Value Master Series are designed using finite element analysis (FEA) to ensure powerful cutting and agility and are composed of meehanite cast iron to minimize deformation when performing heavy-duty cuts. The rigid bed is designed to absorb vibration for stable machining.
To eliminate thermal growth during machining, all axes are driven by high precision double-nut ballscrews. The double pretension design provides outstanding positioning and repeatability with virtually no thermal growth. All ballscrews are connected directly to the servo drive motors without gears or belts, eliminating backlash. Rapid high speed axis movement is achieved by the use of linear motion guide ways in all three axes. This reduces non-cutting time and decreases machining time for greater productivity. Rapid traverse: 1,418 ipm (36 m/min) in X- and Y-axis and 1,182 ipm (30 m/min) in Z-axis.
The standard Big Plus spindle system provides dual contact between the spindle face and the flange face of the tool holder. This greatly increases tool rigidity, reduces run out and adds significant productivity to any machining applications. The F650 Value Master is configured with a 25 hp, 10,000 rpm spindle for taking deep cuts at high speeds. Ultra precision angular bearings provide high speed accel/decel for smooth machining at high rpms.The main spindle delivers minimal noise and vibration even at the highest cutting speeds, guaranteeing extremely stable machining and minimizing thermal transmission to the main spindle.
To make the Value Master F650VM a true performer, Hyundai WIA included Thru Spindle Coolant as a standard feature. This feature is particularly useful for deep hole drilling where it's necessary to keep chip flow clear of the cutting surface. Thru Spindle Coolant also helps to increase tool life and decrease cycle time. Hyundai WIA's Value Master VMCs are outfitted with 30-tool, side mount swing-arm type tool changers. This technology offers optimal performance with impressive tool change times of 1.5 second, tool-to-tool. With a capacity of 30 tools (plus one in the spindle) setup time is reduced and run times can be longer, especially if loaded with redundant tools.
Contact Details
Related Glossary Terms
- backlash
backlash
Reaction in dynamic motion systems where potential energy that was created while the object was in motion is released when the object stops. Release of this potential energy or inertia causes the device to quickly snap backward relative to the last direction of motion. Backlash can cause a system’s final resting position to be different from what was intended and from where the control system intended to stop the device.
- centers
centers
Cone-shaped pins that support a workpiece by one or two ends during machining. The centers fit into holes drilled in the workpiece ends. Centers that turn with the workpiece are called “live” centers; those that do not are called “dead” centers.
- computer numerical control ( CNC)
computer numerical control ( CNC)
Microprocessor-based controller dedicated to a machine tool that permits the creation or modification of parts. Programmed numerical control activates the machine’s servos and spindle drives and controls the various machining operations. See DNC, direct numerical control; NC, numerical control.
- coolant
coolant
Fluid that reduces temperature buildup at the tool/workpiece interface during machining. Normally takes the form of a liquid such as soluble or chemical mixtures (semisynthetic, synthetic) but can be pressurized air or other gas. Because of water’s ability to absorb great quantities of heat, it is widely used as a coolant and vehicle for various cutting compounds, with the water-to-compound ratio varying with the machining task. See cutting fluid; semisynthetic cutting fluid; soluble-oil cutting fluid; synthetic cutting fluid.
- inches per minute ( ipm)
inches per minute ( ipm)
Value that refers to how far the workpiece or cutter advances linearly in 1 minute, defined as: ipm = ipt 5 number of effective teeth 5 rpm. Also known as the table feed or machine feed.
- tapping
tapping
Machining operation in which a tap, with teeth on its periphery, cuts internal threads in a predrilled hole having a smaller diameter than the tap diameter. Threads are formed by a combined rotary and axial-relative motion between tap and workpiece. See tap.