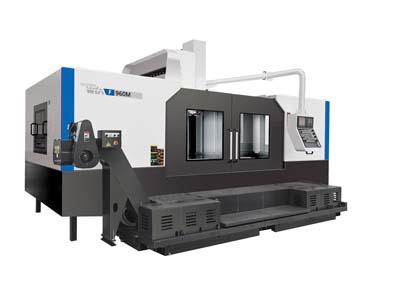
Hyundai WIA introduces two all new large capacity CNC vertical machining centers developed for machining industrial molds and dies, the F750M (travels: 61" X-axis, 29.5" Y-axis, 28.5" Z-axis) and F960M (travels: 96." X-axis, 37.4" Y-axis, 33.5" Z-axis). Standard features found on both M-Series (M=Mold) machining centers include 12,000 RPM built-in spindle with Big Plus 50 taper spindle nose, thru spindle coolant with chiller, hardened and ground box guideways and HW MP II CNC Mold Package included in the control.
Both the F750M and 960M feature a 12,000 rpm built-in cartridge type spindle, which is reportedly idea for mold makers. Ultra precision class angular bearings provide high speed accel/decel for smooth machining at high rpm. The main spindle delivers minimal noise and vibration even at the highest cutting speeds, guaranteeing extremely stable machining and minimizing thermal transmission to the main spindle, and with the use of a hydraulic tool lock system machining stability has been increased.
The standard Big Plus spindle system (BBT #50) provides dual contact between the spindle face and the flange face of the tool holder. This greatly increases tool rigidity, reduces run out and adds significant productivity to any machining application. Spindle motor is 16 to 25 hp with spindle torque rated at 893/732 Nm. The Big Plus spindle offers users fast material removal rates, high accuracy and excellent rigidity. It guarantees stability when run at high spindle speeds for high rpm precision machining.
Through-spindle coolant is standard on the F750M/960M Series. This feature is particularly useful for deep hole drilling where it's necessary to keep chip flow clear of the cutting surface. Thru spindle coolant also helps to increase tool life and decrease cycle time.
All guideways are hardened and ground, wide box type for unsurpassed long-term rigidity and accuracy. By adapting the "semi-rising sliding ways" system the load on the X- and Y-axis slide way is decreased dramatically enabling the M-Series VMC's to hold tolerance and repeatability over longer cycle times. The F960M table is further supported at all times by the use of four box ways and two supplemental ways. This allows for a maximum table load of 4,500 kg without any table distortion.
The bed, column and saddle of this VMC Series are designed using finite element analysis (FEA) to ensure powerful cutting and agility. In order to eliminate thermal growth during machining, all axes are driven by high precision double-nut ballscrews connected directly to the servo drive motors without gears or belts, eliminating backlash. Hyundai WIA's F750M/960M VMC's are outfitted with 20-tool (40-tool optional on F750M), side mount swing arm type tool changers.
This technology offers optimal performance with impressive tool change times of 3.5 seconds tool-to-tool. With a capacity up to 40 tools (plus one in the spindle) setup time is reduced and run times can be made longer, especially if loaded with redundant tools. The 20 (40 optional) tool swing arm
Contact Details
Related Glossary Terms
- backlash
backlash
Reaction in dynamic motion systems where potential energy that was created while the object was in motion is released when the object stops. Release of this potential energy or inertia causes the device to quickly snap backward relative to the last direction of motion. Backlash can cause a system’s final resting position to be different from what was intended and from where the control system intended to stop the device.
- centers
centers
Cone-shaped pins that support a workpiece by one or two ends during machining. The centers fit into holes drilled in the workpiece ends. Centers that turn with the workpiece are called “live” centers; those that do not are called “dead” centers.
- computer numerical control ( CNC)
computer numerical control ( CNC)
Microprocessor-based controller dedicated to a machine tool that permits the creation or modification of parts. Programmed numerical control activates the machine’s servos and spindle drives and controls the various machining operations. See DNC, direct numerical control; NC, numerical control.
- coolant
coolant
Fluid that reduces temperature buildup at the tool/workpiece interface during machining. Normally takes the form of a liquid such as soluble or chemical mixtures (semisynthetic, synthetic) but can be pressurized air or other gas. Because of water’s ability to absorb great quantities of heat, it is widely used as a coolant and vehicle for various cutting compounds, with the water-to-compound ratio varying with the machining task. See cutting fluid; semisynthetic cutting fluid; soluble-oil cutting fluid; synthetic cutting fluid.
- precision machining ( precision measurement)
precision machining ( precision measurement)
Machining and measuring to exacting standards. Four basic considerations are: dimensions, or geometrical characteristics such as lengths, angles and diameters of which the sizes are numerically specified; limits, or the maximum and minimum sizes permissible for a specified dimension; tolerances, or the total permissible variations in size; and allowances, or the prescribed differences in dimensions between mating parts.
- tolerance
tolerance
Minimum and maximum amount a workpiece dimension is allowed to vary from a set standard and still be acceptable.