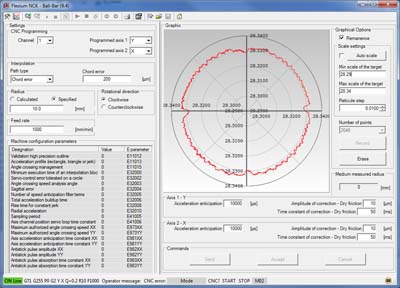
NUM Corp. has launched a new generation of its CNC platform, providing machine tool manufacturers with an exceptionally flexible and scalable solution for safe control of machine tools. Known as Flexium+, the modular safety-equipped platform enables OEMs to standardize on a single cost- and performance-optimized CNC architecture for a vast spectrum of machine types, from small machines with a few axes to large multi-cell manufacturing equipment with over 200 axes and spindles. In this way, the open architecture of the CNC platform can dramatically lower development and support costs, and speed time to market.
Flexium+ builds on the architecture of NUM's Flexium CNC. To provide even greater versatility, dynamic performance and accuracy, the platform's hardware includes new digital servodrive modules with integrated safety, a safety PLC module, safe input and output modules, and a multi-processor operator panel with touch-sensitive screen. New support software includes a precision operating system and soft automation PLC, complete with a fully customizable human-machine interface (HMI) that recognizes touch gestures, an extensive suite of optional machining functions, and a powerful 3D simulator for part program verification and visualization of machining processes.
A choice of three CNC kernels, Flexium+ 6, Flexium+ 8 and Flexium+ 68, enables machine designers to deploy technically and economically optimized solutions for different machine tool applications. Flexium+ 6 and Flexium+ 8 will control up to four interpolated axes and a spindle, where Flexium+ 8 is dedicated to machines which need a higher degree of flexibility. Flexium+ 68 supports larger and more complex machine control applications and provides up to eight CNC channels, each accommodating up to nine interpolated axes and as many as 32 spindles. In total, a single Flexium+ 68 CNC kernel can accommodate 32 connected devices, any of which can be interpolated axes or spindles. This universal control approach simplifies spindle/C-axis commutation and provides an excellent foundation for multi-spindle applications such as transfer machines.
"Being able to use one CNC architecture across a complete range of machines gives a very large payback, especially for the many small to medium sized machine tool builders that support a broad range of applications using limited design resources," says NUM's CEO Peter von Rueti.
An enhanced part program structure enables machine designers to take full advantage of the new CNC hardware's versatility. Each channel runs its own part program asynchronously and operates autonomously, much as if it had a dedicated CNC kernel, or it can be synchronized to other channels. Control of one or more axes or spindles can be passed from one channel to another on-the-fly to maximize use of available hardware resources.
In each channel, four spindles can be operated in a master/auxiliary arrangement, with real-time control of their speed, direction and indexing. This simplifies implementation of complex machining operations. The master handles advanced CNC functions such as maintaining CSS (constant surface speed) while the workpiece changes diameter during processing, or continuously tracking angular position during thread cutting, with the three auxiliary spindles handling associated higher speed machining.
Multiple Flexium+ 68 CNC kernels can be interconnected via real-time Ethernet, which enables the realization of control systems with more than 200 interpolating axes. The ability to drive multiple CNC kernels and control this number of axes with a single automation PLC is a unique advantage of NUM's CNC architecture.
To help OEMs implement rigorous machine safety schemes, Flexium+ introduces a comprehensive system-wide safety architecture known as NUMSafe. All critical system operations are overseen by a new safety PLC module. In conjunction with new NUM safe I/O modules and servodrives – which incorporate safe motion monitoring circuitry, the safety PLC enables machine designers to implement high integrity safety functions with very few additional components. NUMSafe is inherently scalable, requires minimal extra wiring and uses a Fail Safe over EtherCAT (FSoE) protocol to ensure integrity of all safety-related data.
The architecture complies with the EN ISO 13849-1 machinery safety standard up to PLe, and with the EN 61800-5-2 functional safety standard for variable speed drives, up to SIL 3. Available in single- and dual-axis versions, the new digital servodrives, NUMDrive X – offer a choice of two performance levels, with outputs from a few amps to 200 Arms. Their high degree of functional integration makes them one of the smallest drives of their type on the market. To further simplify design-in, the drives' safe motion monitoring board is available in a basic version with Safe Torque Off functionality, and in an extended version which adds Safe Operating Stop, Safe Stop 1, Safe Stop 2, Safely, Limited Speed and Safely-Limited Position functions. NUMDrive X servodrives are significantly faster than NUM's earlier-generation NUMDrive C products.
Advanced DSP control increases CNC-drive servobus speed by 100 percent. Together with improvements to the drives' bandwidth, by as much as 25 percent, and enhanced acceleration algorithms, this means machine designers do not need to sacrifice resolution during extended axis travel, or trade traverse rate against positioning accuracy. Overall CNC resolution and accuracy are further improved by a numerical processor in the CNC kernel; the software has been enhanced to utilize high precision format, allowing for finer interpolation and speed control.
To speed development of part programs, Flexium+ provides a unified suite of software tools with a consistent look and feel. All CNC, servodrive, I/O, automation PLC and safety PLC functions are set up and programmed using a single tool; the automation PLC offers a choice of IEC 61131-3 compliant graphical and textual programming languages, while the safety PLC is programmed using simple function blocks and Boolean operators. Unlike competitive CNC platforms, Flexium+ also offers a fully customizable HMI, allowing OEMs to add value to their machines through improved ergonomics. Dual touch gestures such as "wipe," "expand" and "rotate" can be incorporated to capitalize on NUM's new touch-sensitive operator panel, while virtual keys can replace physical keys to further simplify machine operation and reduce build costs. Manually-written or CAM-generated part programs can be verified and optimized easily and quickly using NUM's powerful Flexium 3D graphical simulation software on an offline PC.
Alternatively, the software runs on the new operator panel, taking full advantage of its multi-core processor PC and 19-inch screen, and interacting with the machine's CNC unit, to simulate part programs either before they are run, or simultaneously with part processing. Users can visualize the path of the tool centre point, simulate material removal and check for collisions. As standard, the software can simulate a wide variety of machining functions including grooving, thread cutting and tapping on 3- to 5-axis turning machines, milling and drilling on 3-axis machines, and contour cutting.
An exceptionally diverse range of application support software covers machining functions such as grinding, turning, milling and cutting, as well as gear hobbing, shaping and finishing. The latest additions include new functions for water-jet and plasma cutting machines, using innovative "tilted nozzle management" algorithms to prevent under- or over-cut edges by automatically compensating for the conical shape of the beam.
Related Glossary Terms
- computer numerical control ( CNC)
computer numerical control ( CNC)
Microprocessor-based controller dedicated to a machine tool that permits the creation or modification of parts. Programmed numerical control activates the machine’s servos and spindle drives and controls the various machining operations. See DNC, direct numerical control; NC, numerical control.
- gang cutting ( milling)
gang cutting ( milling)
Machining with several cutters mounted on a single arbor, generally for simultaneous cutting.
- grinding
grinding
Machining operation in which material is removed from the workpiece by a powered abrasive wheel, stone, belt, paste, sheet, compound, slurry, etc. Takes various forms: surface grinding (creates flat and/or squared surfaces); cylindrical grinding (for external cylindrical and tapered shapes, fillets, undercuts, etc.); centerless grinding; chamfering; thread and form grinding; tool and cutter grinding; offhand grinding; lapping and polishing (grinding with extremely fine grits to create ultrasmooth surfaces); honing; and disc grinding.
- grooving
grooving
Machining grooves and shallow channels. Example: grooving ball-bearing raceways. Typically performed by tools that are capable of light cuts at high feed rates. Imparts high-quality finish.
- interpolation
interpolation
Process of generating a sufficient number of positioning commands for the servomotors driving the machine tool so the path of the tool closely approximates the ideal path. See CNC, computer numerical control; NC, numerical control.
- milling
milling
Machining operation in which metal or other material is removed by applying power to a rotating cutter. In vertical milling, the cutting tool is mounted vertically on the spindle. In horizontal milling, the cutting tool is mounted horizontally, either directly on the spindle or on an arbor. Horizontal milling is further broken down into conventional milling, where the cutter rotates opposite the direction of feed, or “up” into the workpiece; and climb milling, where the cutter rotates in the direction of feed, or “down” into the workpiece. Milling operations include plane or surface milling, endmilling, facemilling, angle milling, form milling and profiling.
- shaping
shaping
Using a shaper primarily to produce flat surfaces in horizontal, vertical or angular planes. It can also include the machining of curved surfaces, helixes, serrations and special work involving odd and irregular shapes. Often used for prototype or short-run manufacturing to eliminate the need for expensive special tooling or processes.
- tapping
tapping
Machining operation in which a tap, with teeth on its periphery, cuts internal threads in a predrilled hole having a smaller diameter than the tap diameter. Threads are formed by a combined rotary and axial-relative motion between tap and workpiece. See tap.
- turning
turning
Workpiece is held in a chuck, mounted on a face plate or secured between centers and rotated while a cutting tool, normally a single-point tool, is fed into it along its periphery or across its end or face. Takes the form of straight turning (cutting along the periphery of the workpiece); taper turning (creating a taper); step turning (turning different-size diameters on the same work); chamfering (beveling an edge or shoulder); facing (cutting on an end); turning threads (usually external but can be internal); roughing (high-volume metal removal); and finishing (final light cuts). Performed on lathes, turning centers, chucking machines, automatic screw machines and similar machines.