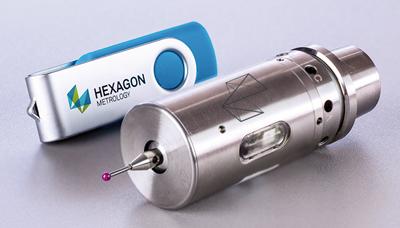
Hexagon Metrology announced the availability of the m&h IRP40.50 infrared touch probe for the North American market. The IRP40.50 is ideal for inspection in tight spaces, and was designed to address the needs of miniature machining centers. The m&h IRP40.50 is a small self-contained wireless CNC probe with a diameter of 25 millimeters, a length of 44.2 millimeters without shank and stylus, and a probing force of 0.7N (XY). The probe's small dimensions enable measurement of small and delicate workpieces. With the shank and stylus included, the IRP40.50 is slightly larger than a standard USB stick. Typical applications for the probe include micro-manufacturing in the firearms, medical, dental, additive manufacturing and electronic industries or any manufacturing which involves small parts with complex geometries and tight tolerances.
Small parts with tight tolerances are difficult, if not impossible, to measure because there is little room in the Z-axis direction and the tool magazine. The IRP40.50 eliminates this concern and leaves enough room to measure in the Z-axis without the danger of collision. The stylus threading is M2 but allows fast probe cycles at speeds up to 2,000mm/min.
"The IRP40.50 works with PC-DMIS NC-Gage v2.1, the revolutionary software that simplifies CNC probe operations into simple, user-friendly instructions that any operator can understand. The probe was designed to inspect and correct the machining process before a bad part can be made," states Adrian Johnson, Business Manager of In-process Inspection. "The IRP40.50 is able to inspect parts that were once considered too difficult or too small to inspect on machine tools. The miniature touch probe enables in-process measurement to drastically reduce scrap and rework."
Even with its small profile, the IRP40.50 has proven high data rate (HDR) infrared transmission. This feature guarantees that only the system's own signals are processed, and disturbances caused by extraneous light are ignored. Newly developed electronics in this mini-probe enables them to use less energy, providing 400 hours of continuous run time.
Contact Details
Related Glossary Terms
- centers
centers
Cone-shaped pins that support a workpiece by one or two ends during machining. The centers fit into holes drilled in the workpiece ends. Centers that turn with the workpiece are called “live” centers; those that do not are called “dead” centers.
- computer numerical control ( CNC)
computer numerical control ( CNC)
Microprocessor-based controller dedicated to a machine tool that permits the creation or modification of parts. Programmed numerical control activates the machine’s servos and spindle drives and controls the various machining operations. See DNC, direct numerical control; NC, numerical control.
- in-process gaging ( in-process inspection)
in-process gaging ( in-process inspection)
Quality-control approach that monitors work in progress, rather than inspecting parts after the run has been completed. May be done manually on a spot-check basis but often involves automatic sensors that provide 100 percent inspection.
- metrology
metrology
Science of measurement; the principles on which precision machining, quality control and inspection are based. See precision machining, measurement.
- shank
shank
Main body of a tool; the portion of a drill or similar end-held tool that fits into a collet, chuck or similar mounting device.
- threading
threading
Process of both external (e.g., thread milling) and internal (e.g., tapping, thread milling) cutting, turning and rolling of threads into particular material. Standardized specifications are available to determine the desired results of the threading process. Numerous thread-series designations are written for specific applications. Threading often is performed on a lathe. Specifications such as thread height are critical in determining the strength of the threads. The material used is taken into consideration in determining the expected results of any particular application for that threaded piece. In external threading, a calculated depth is required as well as a particular angle to the cut. To perform internal threading, the exact diameter to bore the hole is critical before threading. The threads are distinguished from one another by the amount of tolerance and/or allowance that is specified. See turning.