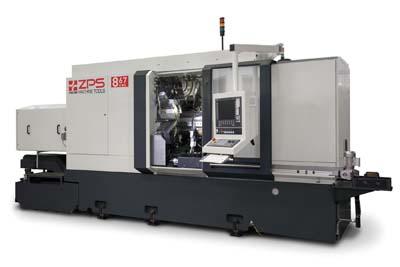
ZPS America announces the new 8-spindle ZPS 867 CNC multispindle production center. The 867 can accommodate stock to 72mm diameter. Provided with a double Siemens 840 D CNC control, the European-built machine offers up to 72 CNC axes and can perform nearly any metalcutting operation on precision parts from drilling and tapping to milling, spline gears, broaching and hobbing. With a cast iron base and total weight of more than 20 tons, the 867 is extremely rigid. Combined with the highest spindle torque in the industry (191 NM), the stable 867 can handle difficult materials with great precision.
"This new multispindle offers for the first time high-precision CNC production capability with its 16+1 tool carriers to a range of part sizes that until now have been processed on transfer machines," said Olaf Tessarzyk, Managing Partner and President of ZPS America.
The ZPS CNC Multi line offers very high processing flexibility and fast changeover with the ability to drop a variety of complex precision parts complete as either a bar-fed or chucker operation. The machine's versatility is provided through its standard features: 8 independent AC-driven CNC horizontal spindles, 8 independent compound slides (X and Z), 8 independent tool carriers with 8 12,000-rpm driven tools, 5 backworking tools (3 driven), and a wide range of standard presettable VDI tooling for quick changeover to increase flexibility. However, it is the patented state-of-the-art designed spindle drive system that sets the ZPS machines apart. It is the key to the machine's precision, thermal stability, and high reliability.
According to tests performed at a technical university in Europe, the ZPS spindle drive system proved to be superior to other multispindle drive systems due to its mechanical precision and genuine simplicity. Each of the machine's eight spindles is linked by a composite shaft to its own motor into the spindle drum, which employs a precise Hirth coupling. This makes it unnecessary to reverse-index the drum at the end of each 360°Cycle, connect, and disconnect the motors to the spindles with each indexing and cool the drum to dissipate the heat generated by the spindle motors. The result is greater precision and reliability across high duty cycles.
Spindle indexing takes only 1 second, not only saving time, but reduces energy and cost. In addition, this system allows for the strongest and most adjustable clamping power in the industry. The mechanical rigidity and thermal stability are the reason for the built-in accuracy of the machine. Therefore, the use of refrigerant is not needed, which is what makes the ZPS machine so interesting to users. Even without spindle compensation this machine tops the precision of its competitors. Using the built-in mechanical compensation allows for a new dimension of accuracy in CNC multispindle machines. Because hydraulics and refrigeration are eliminated through innovative design in the spindle drum, the machine has a significantly higher uptime, has greater thermal stability, and as a result provides higher precision and efficiency than other CNC multispindles on the market.
The innovative, patented technical solution developed by ZPS allows the independent control of the speed and C-Axis of each spindle and the power of each AC spindle motor according to the requirements of specific machining operations performed by each customer. The machine is provided complete with all options and includes capabilities that make it effective on today's precision machining floors: quick changeover; simple, intuitive programming; single-point presettable driven tooling; and teaching software as well as a standard CAM programming software.
A range of optional equipment includes a CNC pick-up spindle with up to 5 tools (3 driven) for backworking, attachments for radial and axial drilling and milling operations from cut-off slide, parts handling gripper or ejection slide, parts conveyor, bar stock feeding and high-pressure tool coolant system.
Contact Details
Related Glossary Terms
- broaching
broaching
Operation in which a cutter progressively enlarges a slot or hole or shapes a workpiece exterior. Low teeth start the cut, intermediate teeth remove the majority of the material and high teeth finish the task. Broaching can be a one-step operation, as opposed to milling and slotting, which require repeated passes. Typically, however, broaching also involves multiple passes.
- computer numerical control ( CNC)
computer numerical control ( CNC)
Microprocessor-based controller dedicated to a machine tool that permits the creation or modification of parts. Programmed numerical control activates the machine’s servos and spindle drives and controls the various machining operations. See DNC, direct numerical control; NC, numerical control.
- computer-aided manufacturing ( CAM)
computer-aided manufacturing ( CAM)
Use of computers to control machining and manufacturing processes.
- coolant
coolant
Fluid that reduces temperature buildup at the tool/workpiece interface during machining. Normally takes the form of a liquid such as soluble or chemical mixtures (semisynthetic, synthetic) but can be pressurized air or other gas. Because of water’s ability to absorb great quantities of heat, it is widely used as a coolant and vehicle for various cutting compounds, with the water-to-compound ratio varying with the machining task. See cutting fluid; semisynthetic cutting fluid; soluble-oil cutting fluid; synthetic cutting fluid.
- gang cutting ( milling)
gang cutting ( milling)
Machining with several cutters mounted on a single arbor, generally for simultaneous cutting.
- metalcutting ( material cutting)
metalcutting ( material cutting)
Any machining process used to part metal or other material or give a workpiece a new configuration. Conventionally applies to machining operations in which a cutting tool mechanically removes material in the form of chips; applies to any process in which metal or material is removed to create new shapes. See metalforming.
- milling
milling
Machining operation in which metal or other material is removed by applying power to a rotating cutter. In vertical milling, the cutting tool is mounted vertically on the spindle. In horizontal milling, the cutting tool is mounted horizontally, either directly on the spindle or on an arbor. Horizontal milling is further broken down into conventional milling, where the cutter rotates opposite the direction of feed, or “up” into the workpiece; and climb milling, where the cutter rotates in the direction of feed, or “down” into the workpiece. Milling operations include plane or surface milling, endmilling, facemilling, angle milling, form milling and profiling.
- precision machining ( precision measurement)
precision machining ( precision measurement)
Machining and measuring to exacting standards. Four basic considerations are: dimensions, or geometrical characteristics such as lengths, angles and diameters of which the sizes are numerically specified; limits, or the maximum and minimum sizes permissible for a specified dimension; tolerances, or the total permissible variations in size; and allowances, or the prescribed differences in dimensions between mating parts.
- tapping
tapping
Machining operation in which a tap, with teeth on its periphery, cuts internal threads in a predrilled hole having a smaller diameter than the tap diameter. Threads are formed by a combined rotary and axial-relative motion between tap and workpiece. See tap.