Shrink-fit toolholders minimize runout to no more than 0.0002 " and, as a result, extend tool life, provide a consistent chip load and enable the cutting tool to impart a fine surface finish. But if a part manufacturer using thermal-grip holders doesn’t have through-coolant cutting tools and has to use external coolant, the coolant does not effectively reach the tool/workpiece interface where it’s needed, according to Timothy Fara, managing director for Bilz Tool Co. Inc.
Therefore, the manufacturer of tool clamping systems developed the JetSleeve coolant delivery system, which is comprised of a shrink-fit chuck encompassed by an aluminum sleeve, or housing. Coolant pressure is created within the sleeve and delivered to the cutting edge via coolant holes in the face of the gold-colored sleeve.
Initially, Bilz equally spaced 16 coolant channels around the holder face, made all the holes for the channels the same diameter and positioned them on one bolt circle, and directed the coolant at the same angle, Fara noted. This design caused the coolant to be applied at the same point for every tool, regardless of whether the tool, for example, extended 1 " or 6 " from the holder. “Therefore, coolant wasn’t necessarily getting down to the cutting tip,” Fara said, “and centrifugal force was pulling the coolant away.”
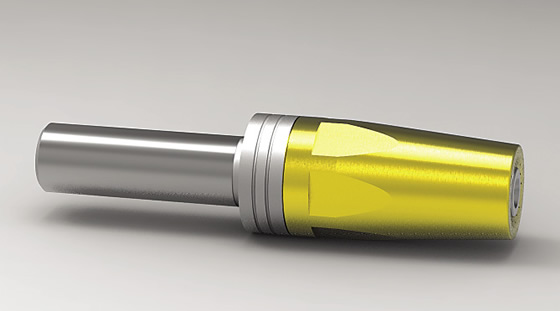
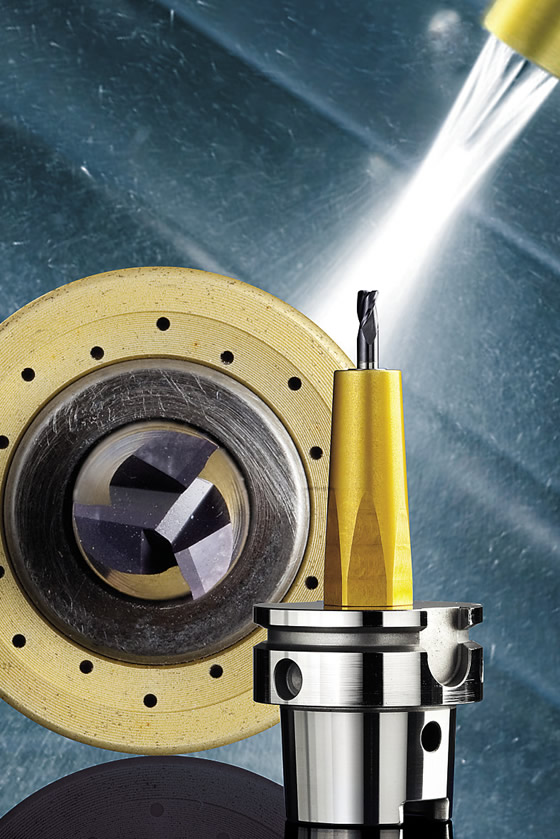
Bilz Tool reports that its JetSleeve through-coolant, shrink-fit chuck reduces coolant consumption by up to 70 percent.
In addition, putting coolant holes through the holder body or coolant grooves along its ID changes the concentric expansion and contraction of the bore, Fara pointed out. “Those holes or grooves create voids and change the heat path, so the holder tends to open and close elliptically,” he said. “That means you’re not gripping your tool with the full force 360° around the shank.”
Fara explained that the company corrected those issues by having the coolant channels unequally spaced on the front of the sleeve, positioning the channels so they are not all on the same bolt circle and varying the hole diameters and coolant delivery angles so each one is different. “We designed it so we could create a tornadic flow of coolant around the cutting tool,” he said. “By doing that, similar to the center of a tornado, you have zero pressure down the center, meaning the coolant or air is actually being sucked into the cutting tool.”
Coolant cannot be applied when machining with PCBN-tipped tools, so air is used instead, Fara added. JetSleeve is also suitable for applying minimum-quantity lubrication.
Bilz reports that JetSleeve increases tool life up to 28 percent and improves surface finish up to 25 percent. It also reduces air usage up to 80 percent and coolant consumption up to 70 percent because the air or coolant is pinpointed directly to the cutting edge and isn’t wasted in areas where it’s not needed.
In addition to preventing chips from being recut and, therefore, edge chipping by not letting chips build up under the cutting edge, the hydraulic design of the holder enhances surface finish by reducing vibration, Fara noted. As the coolant flows through the holder, it creates a slight backpressure and absorbs any vibration.
To prevent clogging of the coolant holes, Fara said users must have a coolant filtration system to remove particles as small as 5µm, but “2µm filtration is better.”
For more information, contact Bilz Tool Co. Inc., Lombard, Ill., at (847) 734-9390 or www.bilzusa.com.
Related Glossary Terms
- chuck
chuck
Workholding device that affixes to a mill, lathe or drill-press spindle. It holds a tool or workpiece by one end, allowing it to be rotated. May also be fitted to the machine table to hold a workpiece. Two or more adjustable jaws actually hold the tool or part. May be actuated manually, pneumatically, hydraulically or electrically. See collet.
- coolant
coolant
Fluid that reduces temperature buildup at the tool/workpiece interface during machining. Normally takes the form of a liquid such as soluble or chemical mixtures (semisynthetic, synthetic) but can be pressurized air or other gas. Because of water’s ability to absorb great quantities of heat, it is widely used as a coolant and vehicle for various cutting compounds, with the water-to-compound ratio varying with the machining task. See cutting fluid; semisynthetic cutting fluid; soluble-oil cutting fluid; synthetic cutting fluid.
- inner diameter ( ID)
inner diameter ( ID)
Dimension that defines the inside diameter of a cavity or hole. See OD, outer diameter.
- minimum-quantity lubrication
minimum-quantity lubrication
Use of cutting fluids of only a minute amount—typically at a flow rate of 50 to 500 ml/hr.—which is about three to four orders of magnitude lower than the amount commonly used in flood cooling. The concept addresses the issues of environmental intrusiveness and occupational hazards associated with the airborne cutting fluid particles on factory shop floors. The minimization of cutting fluid also saves lubricant costs and the cleaning cycle time for workpieces, tooling and machines. Sometimes referred to as “near-dry lubrication” or “microlubrication.”
- shank
shank
Main body of a tool; the portion of a drill or similar end-held tool that fits into a collet, chuck or similar mounting device.