Coolants and the systems that apply them require regular maintenance.
Metalworking fluids take a lot of abuse as they cool and lubricate cutting tools and workpieces, but fluids are not the only part of the process subjected to the demanding, and potentially damaging, cutting environment.
The nozzles, hoses, chillers, flumes and other components that help MWFs function are subject to the same dirt, leached oil and debris faced by coolants. Just as fluids need to be cleaned and maintained, these workhorse components should also undergo regular cleaning and inspection.
Often, however, these components are overlooked. Clogged hoses and tubes, damaged seals, gummed-up nozzles, chillers choked in residue and sludge-caked sumps are not typically visible and often escape detection until a problem occurs. Engaging in a fluid management program is one way to help ensure system maintenance is performed as required.
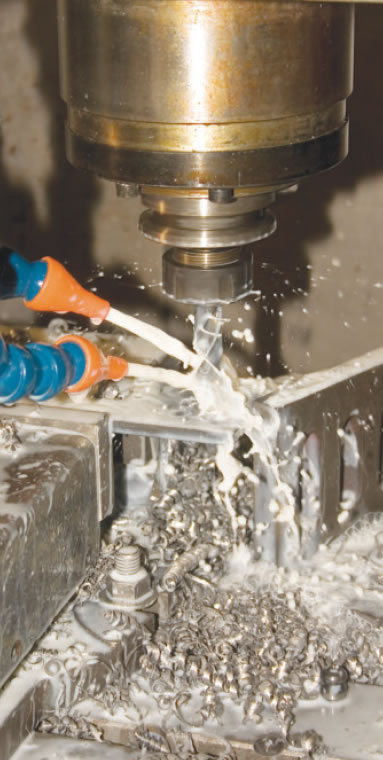
Courtesy of Chemetall
The Tech Cool 35035 coolant from Chemetall is for machining and grinding ferrous, aluminum, copper and brass alloys.
Sumps may have the worst of it. They often experience floating tramp oils, bacteria growing throughout, sludge on the bottom, and chips, fines and swarf hidden in the sump’s corners and stagnant spots—not to mention the food, cigarettes, sweat, saliva and other debris that gets chucked into the tank by machine operators and other workers, said Brett Reynolds, senior applications engineer for Blaser SwissLube Inc., Goshen, N.Y.
It is not just accumulated offal that impedes coolant operations and potentially limits tool life and part quality, it is the extra stress and strain that components endure because they have to work harder to overcome macro and micro messes that can deter efficient cooling and lubrication.
A chiller is a good example. Residue can coat the cooling fins and filters of the chiller, making it work that much harder to keep tools and workpieces cool. If bacteria or fungi are present, the MWF can be consumed, reducing overall coolant volume and making the chiller work even harder.
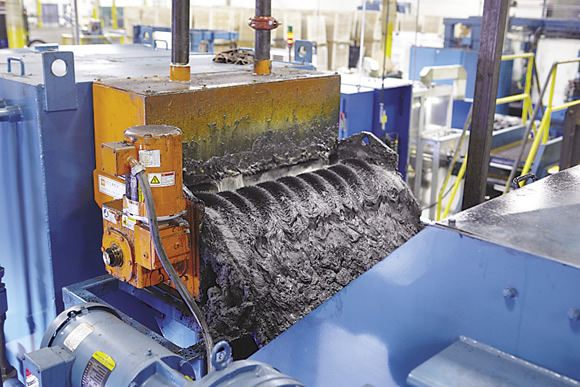
Courtesy of Eriez
Cast iron swarf can be scalped using magnetic rolls, improving the efficiency of the filter and reducing media consumption.
The Occupational Safety and Health Administration identified several areas that negatively impact MWFs and coolant system components. Typical problems include chips and fines that travel through the system, tramp oils floating to the surface of the coolant sump, dirty machines, corrosion, growth of fungi that blocks fluid flow and out-of-specification pH and coolant concentration levels.
“To maintain metalworking fluids, good housekeeping is critical,” said Ken Reindl, business manager, metalworking group, Chemetall, New Providence, N.J.
Chips and Fines
As chips are created and MWFs recirculate through the system, the chips and fines are carried along, clogging and potentially damaging hoses and creating dams in flumes. In a worst-case scenario, coolant-borne chips can strike and damage workpieces and tooling, said Ron Wendt, product manager, fluid recycling equipment for Eriez, Erie, Pa.
Damage can occur anywhere on the machine tool, added Jamey Pietrowiak, a former field-service technician and current owner of machine tool parts distributor CNC Specialty Store LLC, Watertown, Wis. Pietrowiak has plenty of horror stories of poorly maintained coolant systems, from eaten O-rings that let coolants flood machine ways to chips forming piles under machine heads and causing them to crash into the chips.
“The worst machines are the ones in which coolant is not taken care of,” Pietrowiak said. “When you walk in you can see the coolants basically eating away the paint and residue is sticking to everything. Slime is building up, and tramp oils are floating, and, by the end of the day, you can feel it in your eyes.”
He cited one instance in which a machine tool was designed to drain in one direction, and the chips clogged the drain hole, causing coolant to back up and overflow. The chip-laden MWFs floated into ballscrew bearings, flushing out grease and damaging the ballscrew.
Microscopic Activity
Tramp oils pollute the coolant and are typically a sign of fluid management problems. These oils are not originally found in the coolant concentrate, but instead are machine tool lubricants, hydraulic and way oils and other oils that have leached into MWFs, said John Logar, sales manager for Abanaki Corp., Chagrin Falls, Ohio.
If tramp oils are not removed, they will form an oxygen-depleted zone and bacteria will turn the tramp layer into a biomass layer that is hard to skim, according to Logar. Anaerobic bacteria, those that do not need oxygen to flourish, will also grow as the tramp oil will inhibit oxygen transfer to the MWF below it. Removal of tramp oil on a regular basis is critical to controlling bacteria levels, he added.

Courtesy of CNC Specialty Store
This machine likely had a chip buildup problem. The threaded part on the lube line is gone, and the fitting on top of the bearing block is damaged.
Microscopic growth also occurs when chips and swarf accumulate on the tank’s bottom, creating a sheltered environment for bacteria to grow and colonize into a slimy, mucous biofilm. To combat this, coolant systems should undergo routine and periodic cleaning, Chemetall’s Reindl said. The coolants can be pumped into the flumes during the cleaning process or pumped into holding tanks to allow for the removal of chips with magnetic separators or other devices.
Many machines use a drag-out conveyor to remove chips, but some chips that settle to the bottom are too minute to be removed with a drag-out system, according to Reindl.
Filtering will aid in reducing the frequency of the cleaning process. Filtration, whether using settling tanks or a filter media to remove solid matter from fluid, can extend the MWFs life. Still, if a cleaning regiment is not kept up, a buildup of chips or biomass can plug filters.
Steven Friedman, general manager for Sanborn Technologies, Walpole, Mass., said by removing solids and tramp oils on a consistent basis, the whole system will work more efficiently.
Sanborn Technologies offers a variety of sump cleaners. Sanborn’s mobile version works at 35 gpm and filters particles down to 10µm. The unit maintains the fluid level so that machining can continue without interruption.
However, many cooling components cannot be cleaned using this in-situ method. A full clean, colloquially called a “sump dump,” allows for the cleaning of all components and surrounding areas.
While there is no criterion for how often a full cleaning is required, the time between full cleanings can be extended through sustained maintenance, as well as the use of higher quality MWFs.
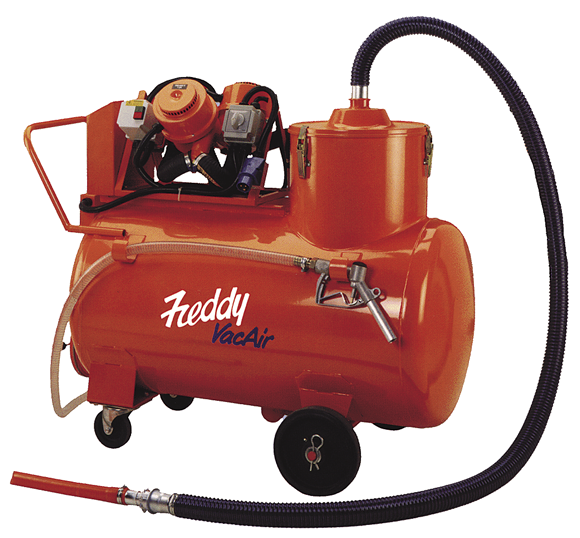
Courtesy of Sanborn Technologies
Sanborn Technologies’ Freddy Ecovac is a sump cleaner that can suck dirty coolant from a sump, filter it to 10µm and discharge the filtered coolant back into the sump.
The time between cleanings can also depend on the type of work being performed at the shop. Full dumps are done much more frequently at shops where a variety of materials are machined, Chemetall’s Reindl noted.
Chips and metal swarf, if allowed to remain in a machine sump will leach the corrosion inhibitor and cause changes in pH, he said. Many small shops do not have filtration on their smallest machines. When they have mixed metals running on the same machine, ferrous and nonferrous materials, for example, these shops will typically decide that it is cheaper and easier to just dump these small systems when they see conductivity increasing or see changes in pH or bacteria.
If machining only aluminum or steel, Reindl said, a company can decide to remove the coolant and chips, filter the chips and put the coolant back into the sump. However, if machining mixed metals, there may be an increase in conductivity as galvanic reaction begins to take place with the dissimilar metals. In shops that have multiple metals, most try to segregate their chips and even add chip hoppers to maintain chip recycling and recovery and prevent autoxidation.
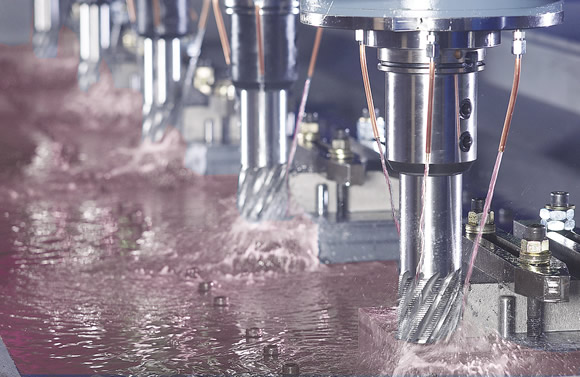
Courtesy of Cimcool
Metalworking fluids can last for years, as opposed to months, if properly maintained.
The time between full cleanings can be extended by using a better quality metalworking fluid. Higher grade MWFs typically have better pH buffering, a stronger emulsion package, better detergency or better resistance to biological degradation. “If the shop maintains concentration, filters the material and controls tramp oil, all metalworking fluids will last longer,” Reindl said. “If you start with a more robust product, you typically get even better results.”
The old fluid must be pumped out and disposed of, and delivery lines should be drained, according to Reindl. Hoses should be purged because bacteria-infused coolants may have pooled in the lines. When the sumps are emptied, cleaned and refilled, the remaining bacteria in the lines can infect the new MWF mix.
During the full cleaning, all chips and swarf should be removed from flumes, trenches, lines and sumps. Covers and guards can be removed to access hidden areas for cleaning.
Dirt and oils often accumulate in stagnant pockets in individual pumps. If not removed, these accumulations can also cause dirt recirculation in a fresh charge, and provide a breeding ground for bacteria, according to Sanborn’s Friedman.
Sludge buildup on any surface can be removed. Coolant flumes can be cleaned of swarf and chip buildups, and walls and piping can be power washed to remove residue and sludge.
Concentration Control
Knowing when to clean can be aided by measuring pH levels and coolant concentration ratios. The need for checking concentration levels on a frequent basis cannot be overlooked. According to Reindl, many plants run daily concentration checks on central systems.
All water-based MWFs operate at a given concentration ratio of water to oil. Out-of-specification concentration levels are the biggest problem observed in machine shops, according to Eriez’ Wendt.
Operating a system at a low concentration ratio may result in decreased tool life, bacteria and fungus problems, corrosion and eventual downtime because of the lack of proper lubrication, according to Wendt. Operating a system at too high a concentration may result in workers suffering from dermatitis caused by airborne lubricant, as well as foaming and oily residue deposited on parts.
Testing pH levels, i.e., the measurement of hydrogen ions contained within a given solution, can be instructive. For instance, tracking pH levels provides an understanding of microscopic activity, according to a technical paper from Cimcool Fluid Technology, Cincinnati. According to the report, “Metalworking Fluid Controls,” even low levels of bacteria, if left untreated, can cause a drop in pH, because of the bacteria’s production of acidic waste compounds. If pH falls below 8.5, it can result in the MWF becoming acidic, or “splitting,” in the case of a soluble or semisynthetic oil. Levels greater than 8.7 indicate the presence of mold.
Fluid Management Programs
Recording pH numbers can be a good way to track problems, but it can be a daunting task for some shops. To promote MWF maintenance, organizations, such as OSHA and the Society of Tribologists and Lubrication Engineers, have developed maintenance program guidelines. The STLE offers certificate programs in the field. In addition, some fluid and equipment suppliers offer these services at varying levels.
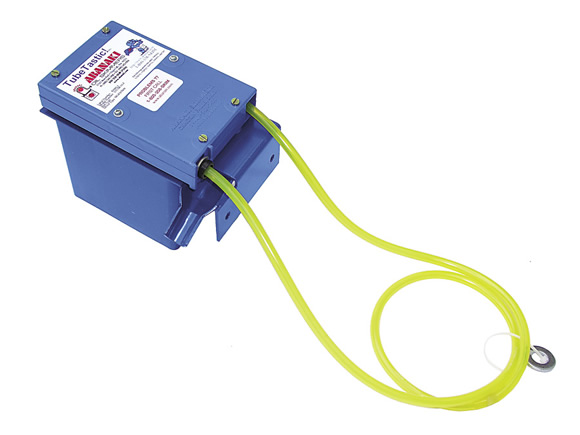
Courtesy of Abanaki
The TubeTastic oil skimmer from Abanaki can skim oil from chip conveyors or even enclosed machining centers.
These programs take an all-inclusive view of coolant systems. OSHA’s “Metalworking Fluids Safety and Health Best Practices Manual,” states: “… an approach that takes the entire system into account will be the most effective. Addressing only one or a few of the issues will probably be ineffective, while dealing with all the issues in a systematic way will be beneficial.”
These programs can be tailored to fit a shop’s specific needs. For instance, a facility using water-miscible MWFs on older machining equipment, with heavy tramp oil leaks and poor microbiological control, might include a list of priorities to track, such as concentration levels, emulsified oils, tramp oils, corrosion resistance and biological contamination.
Companies that offer fluid management programs to metalworking shops include PRAB, Kalamazoo, Mich., a manufacturer of coolant recycling equipment. The company’s Managed Maintenance Program starts with a top-to-bottom equipment inspection, said Thomas Tripepi, technical director for PRAB. The program includes a detailed report with yearly warnings of part wear or impending component failures. “The initial inspection puts a company on track,” he said, “but it must be maintained to reap savings.”
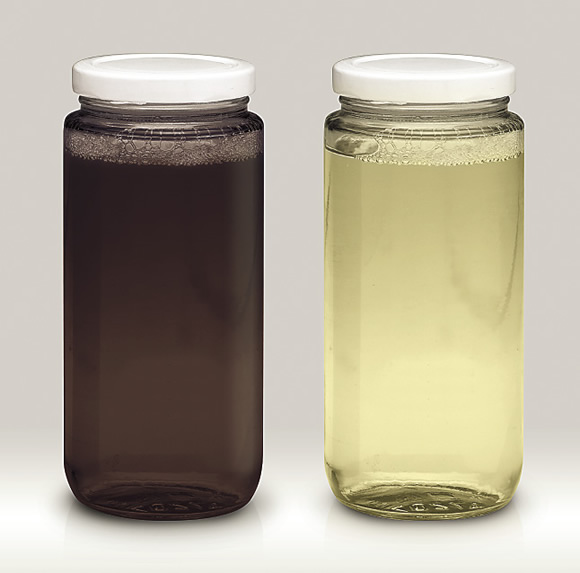
Courtesy of PRAB
Filters can remove fines down to 1µm.
The heart of any coolant management program includes detailed information on each machine tool’s operation. The data should include physical observations of the MWF’s condition and its supporting components. The data should be tabulated so relationships and trends can be spotted and used to improve fluid management techniques.
According to Tripepi, the record-keeping process begins with the initial mixing of the machine coolant. Then, the pH and coolant concentration are measured and recorded. This provides a baseline from which to work and compare against future results.
For fluid maintenance, a shop should first identify a person responsible for filtration and make sure he has the proper training and instruction. “However, some companies do not have a person on staff that can accomplish the record keeping and operate the cleaning equipment,” Tripepi said. “Or, if a person can do it, is his time better spent machining parts?”
According to Tripepi, there is no rule of thumb on when to outsource coolant system maintenance. Often, medium-sized shops are likely to outsource this type of program, but even this comes in fits and starts, where some shops choose to run the program in-house for a couple years, find it is too much trouble or too costly and then outsource it. Another option is to contract with a company such as PRAB to do shared maintenance. For instance, tracking concentration levels can be done in-house, and equipment cleaning can be outsourced.
Whatever the decision, well-maintained coolants can provide significant benefits—despite the daily challenges they face. CTE
About the Author: Larry Adams is a senior editor for CTE. Contact him at (847) 714-0182 or ladams@jwr.com.
Maintaining the same-old grind
Filtering solids, fines and other debris from coolants can be difficult in any scenario, but in grinding operations the task is more daunting, considering the speeds at which modern grinding machines operate, the heat they produce and the minute fines they generate.
Most machine tool coolant, whether straight oil or water based, is filtered to remove particles down to 20µm. However, grinding operations for cutting tools, and especially carbide grinding, should filter coolant to 5µm to ensure metals and particulates are removed, said Randal Armstrong, owner of Filter Technology, Livonia, Mich. “While finer than 5µm clarities can be achieved, it is normally not required for most grinding applications,” he added.
Incorporating filtration into a grinding systems requires a total systems approach. “Too many people go out and buy a filter and forget about the other ancillary equipment that is involved in the process,” Armstrong said. In addition to filters, users should consider properly designed tanks, dirty returns and energy-efficient clean pumps to name a few.
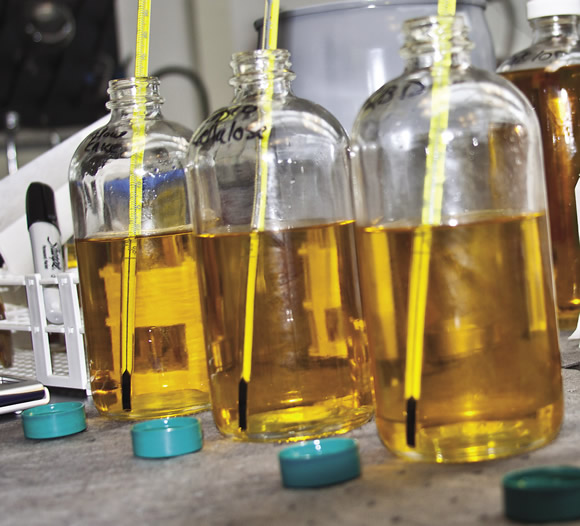
Courtesy of Filter Technology
In grinding operations, coolant should be filtered to 5µm to ensure metals and particulates are removed.
The filters, whether for grinding operations or other large “dirt-load conditions,” must be capable of handling heavy loads. A filter should have enough volume to contain all of the swarf present, so cleaning cycles have a minimal impact on production. The filter needs to be sized to hold the maximum amount of metal that a shop can expect to remove in 24 hours, according to Armstrong. The filters, he added, are normally sized to flow from 0.5 to 0.7 gpm per sq. ft. of filtering area.
The tank not only needs a sufficient operating volume, but it also needs to contain the freeboard, which is the total volume of fluids from the pumping system, sumps, return systems, filters, sludge receivers and piping. For a grinding system, the operating volume of the tank should be sized for approximately 13 minutes times the total flow rate, with the clean tank having 3 minutes times the flowrate and the dirty tank having 10 minutes times the flow rate. A 400-gpm system would require a clean tank volume of 1,200 gal. (400 x 3 minutes) and a dirty tank operating volume of 4,000 gal. (400 x 10 minutes).
Returns can be gravity-fed pipes or individual sumps with pumps and level controls. These will need to return dirty coolant and grinding swarf back to the main tank. While a gravity system is the most forgiving, sumps offer the flexibility to easily relocate or add additional sumps.
These are just some of the issues that need to be considered when filtering fluid for a grinding operation. While many will be tempted to purchase an “out-of-the-box” filter system, Armstrong said there are so many variables specific to each application that, to have a successful operation, each item should be individually addressed.
– L. Adams
Contributors
Abanaki Corp.
(800) 358-7546
www.abanaki.com
Blaser Swisslube Inc.
(845) 294-3200
www.blaser.com
Chemetall
(800) 526-4473
www.chemetallamericas.com
Cimcool Fluid Technology
(888) 246-2665
www.cimcool.com
CNC Specialty Store LLC
(414) 881-4493
www.cnc-specialty-store.com
Eriez
(800) 345-4946
www.eriez.com
Filter Technology
(734) 744-6446
www.filtertechno.com
PRAB
(800) 968-7722
www.prab.com
Sanborn Technologies
(508) 660-9150
www.sanborntechnologies.com
Related Glossary Terms
- alloys
alloys
Substances having metallic properties and being composed of two or more chemical elements of which at least one is a metal.
- centers
centers
Cone-shaped pins that support a workpiece by one or two ends during machining. The centers fit into holes drilled in the workpiece ends. Centers that turn with the workpiece are called “live” centers; those that do not are called “dead” centers.
- computer numerical control ( CNC)
computer numerical control ( CNC)
Microprocessor-based controller dedicated to a machine tool that permits the creation or modification of parts. Programmed numerical control activates the machine’s servos and spindle drives and controls the various machining operations. See DNC, direct numerical control; NC, numerical control.
- coolant
coolant
Fluid that reduces temperature buildup at the tool/workpiece interface during machining. Normally takes the form of a liquid such as soluble or chemical mixtures (semisynthetic, synthetic) but can be pressurized air or other gas. Because of water’s ability to absorb great quantities of heat, it is widely used as a coolant and vehicle for various cutting compounds, with the water-to-compound ratio varying with the machining task. See cutting fluid; semisynthetic cutting fluid; soluble-oil cutting fluid; synthetic cutting fluid.
- corrosion resistance
corrosion resistance
Ability of an alloy or material to withstand rust and corrosion. These are properties fostered by nickel and chromium in alloys such as stainless steel.
- emulsion
emulsion
Suspension of one liquid in another, such as oil in water.
- grinding
grinding
Machining operation in which material is removed from the workpiece by a powered abrasive wheel, stone, belt, paste, sheet, compound, slurry, etc. Takes various forms: surface grinding (creates flat and/or squared surfaces); cylindrical grinding (for external cylindrical and tapered shapes, fillets, undercuts, etc.); centerless grinding; chamfering; thread and form grinding; tool and cutter grinding; offhand grinding; lapping and polishing (grinding with extremely fine grits to create ultrasmooth surfaces); honing; and disc grinding.
- metalworking
metalworking
Any manufacturing process in which metal is processed or machined such that the workpiece is given a new shape. Broadly defined, the term includes processes such as design and layout, heat-treating, material handling and inspection.
- recovery
recovery
Reduction or removal of workhardening effects, without motion of large-angle grain boundaries.
- straight oil
straight oil
Cutting fluid that contains no water. Produced from mineral, vegetable, marine or petroleum oils, or combinations of these oils.
- swarf
swarf
Metal fines and grinding wheel particles generated during grinding.
- tramp oil
tramp oil
Oil that is present in a metalworking fluid mix that is not from the product concentrate. The usual sources are machine tool lubrication system leaks.