A “nano-onion” sounds like a topping for the world’s smallest pizza. In reality, it’s the core constituent of the Tool-X nanofluid that’s added to oil- and water-based metalworking fluids, noted Jim English, president of Nano Synthetics, which makes the additive that also contains deionized water.
According to the company, the nano-onions are particulates that measure about 10nm in diameter and are created through detonation synthesis, a process that transforms explosives into carbon-based nano-onions, which can absorb lubricants. The structure consists of a hard diamond-like core and an outer shell of amorphous carbon and graphene.
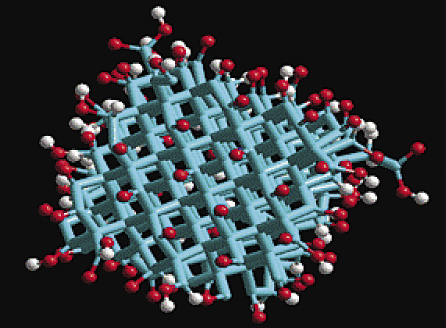
The Tool-X nanofluid additive from Nano Synthetics contains trillions of carbon nano-onions.
English explained that nano-onions are excellent lubricants because they remove heat from the cutting tool and don’t break down in the high temperatures found at the cutting surface. “Graphene is the most thermally conductive material known to man, and Tool-X conducts heat from the coolant and tool, minimizing the need for chillers,” he said. “Graphene technology is the future of lubrication.”
English added that, as a result of better lubrication and lower temperatures, the product extends tool life and allows end users to boost machining parameters 10 to 20 percent and impart finer surface finishes, eliminating the need for secondary operations. For instance, Ron Wellington, president of Bernal Products Inc., Romeo, Mich., reported that tool life tripled for the shop after adding Tool-X to its semisynthetic cutting fluid and enabled it to machine unattended without breaking a tool.
And in a high-volume application cutting 4140 steel with a Promax ½ " carbide endmill on a horizontal machining center, spindle loads were reduced up to 75.1 percent by using the nanofluid additive, according to the Nano Synthetics.
Instead of depositing a coating on a cutting tool, the nanofluid additive enables the coolant to coat a tool. According to Nano Synthetics, research it conducted with Drexel University found that the nanoparticles shot peen the surface of a cutting tool, smoothing it and filling surface micropores. The repeated shot peening under the cutting process’ high pressure and high temperature impinges the lubricious nanoparticles into the tool surface, thereby reducing friction during cutting.
In addition to using Tool-X in wet machining and through-coolant applications, English noted the company is working on minimum-quantity lubrication applications, as well as developing an additive for synthetic fluids.
For more information about Nano Synthetics, Rochester, Mich., call (248) 495-4367 or visit www.tool-x.net.
Related Glossary Terms
- amorphous
amorphous
Not having a crystal structure; noncrystalline.
- coolant
coolant
Fluid that reduces temperature buildup at the tool/workpiece interface during machining. Normally takes the form of a liquid such as soluble or chemical mixtures (semisynthetic, synthetic) but can be pressurized air or other gas. Because of water’s ability to absorb great quantities of heat, it is widely used as a coolant and vehicle for various cutting compounds, with the water-to-compound ratio varying with the machining task. See cutting fluid; semisynthetic cutting fluid; soluble-oil cutting fluid; synthetic cutting fluid.
- cutting fluid
cutting fluid
Liquid used to improve workpiece machinability, enhance tool life, flush out chips and machining debris, and cool the workpiece and tool. Three basic types are: straight oils; soluble oils, which emulsify in water; and synthetic fluids, which are water-based chemical solutions having no oil. See coolant; semisynthetic cutting fluid; soluble-oil cutting fluid; synthetic cutting fluid.
- endmill
endmill
Milling cutter held by its shank that cuts on its periphery and, if so configured, on its free end. Takes a variety of shapes (single- and double-end, roughing, ballnose and cup-end) and sizes (stub, medium, long and extra-long). Also comes with differing numbers of flutes.
- machining center
machining center
CNC machine tool capable of drilling, reaming, tapping, milling and boring. Normally comes with an automatic toolchanger. See automatic toolchanger.
- metalworking
metalworking
Any manufacturing process in which metal is processed or machined such that the workpiece is given a new shape. Broadly defined, the term includes processes such as design and layout, heat-treating, material handling and inspection.
- minimum-quantity lubrication
minimum-quantity lubrication
Use of cutting fluids of only a minute amount—typically at a flow rate of 50 to 500 ml/hr.—which is about three to four orders of magnitude lower than the amount commonly used in flood cooling. The concept addresses the issues of environmental intrusiveness and occupational hazards associated with the airborne cutting fluid particles on factory shop floors. The minimization of cutting fluid also saves lubricant costs and the cleaning cycle time for workpieces, tooling and machines. Sometimes referred to as “near-dry lubrication” or “microlubrication.”
- peening
peening
Mechanical working of a metal by hammer blows or shot impingement.
- semisynthetic cutting fluid
semisynthetic cutting fluid
Water-based chemical solution that contains some oil. See synthetic cutting fluid.
- shot peening
shot peening
Cold working a metal’s surface by metal-shot impingement.