There comes a time when some chipmaking shops add wire EDMing to their repertoire. This is often done to reduce costs, because bringing what were once subcontracted, secondary EDMing operations in-house often makes good financial and logistical sense. It can also be due to demands from medical and aerospace customers, who ask their suppliers to control the entire manufacturing process under one roof. In either case, merging these disparate machining operations can be a workholding challenge.
Substantial differences exist between workholders for conventional CNC machines and those for wire EDMs, starting with the material. Pull a cast iron vise off a machining center and submerge it in a tank of deionized water dielectric and you’ll soon have a rusty mess. For this reason, virtually all EDM workholders are made from hardened 400 series stainless steel.
Premachining fixture locations on workpiece blanks can be eliminated with the right EDM workholder. In the example shown, saw-cut blanks are clamped once and gripped until machining is complete. This setup provides a common interface for automated handling while reducing prep time. Image courtesy Erowa.
There are exceptions. For example, some high-end wire machines use oil dielectric, so it might be possible to use a conventional vise in these instances. However, dedicated EDM workholding is often a necessity due to machine considerations.
EDM tooling can seem like alien Tinker Toys to those familiar only with conventional machine tools. Much of the confusion about what to order can be avoided by understanding the terminology.
For example, reference elements are rails that mount on pedestals inside the EDM work area. Together with reference stops, they provide a zero point to locate fixtures and other workholding components. Chucks are available in pneumatic and manually actuated versions and accept pallets that in turn accept workpieces and fixtures. Mounting heads are used as the "middleman " between the chuck and a vise or universal holder. Add to that a plethora of adapters, f rames, blocks and clamping heads, and a phone call to an EDM workholding expert might be in order.
Some of these experts work at System 3R USA LLC, Elk Grove Village, Ill. John Roskos, vice president of sales, said many shops ease into EDM workholding with a starter kit. For example, a basic system containing a vise, mounting head and adapter might cost $2,000, whereas a full-blown package with reference rails and pneumatic clamps could easily cost 10 times that amount.
This might seem expensive to shops that 've used only homegrown fixtures and commodity vises. Before yelling at the salesman, however, consider the accuracy of these systems, which often provide repeatability and positional accuracy to within a few microns.
As Roskos explained, this accuracy greatly exceeds that of traditional zero-point clamping systems (ZPS), which are often used when milling and turning. For shops that clamp workpieces once for multiple machining operations that now include wire EDMing, ZPS are available to survive EDM’s watery rigors, while still providing the high clamping forces needed for conventional machining, he said.
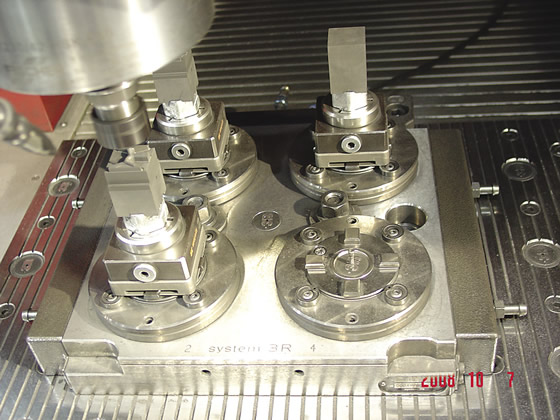
Graphite electrodes are machined while held with quick-change chucks from System 3R. Image courtesy System 3R.
Just because the option exists to palletize workpieces in this manner doesn’t mean shops are using it. Mike Stevens, applications and technical support manager for tooling manufacturer Erowa Technology Inc., Arlington Heights, Ill., said palletizing EDM electrodes—which reduces handling and increases locating accuracy—is widely accepted in mold and die shops, but that few companies use the same technology with their workpieces.
“For most shops, picking the right tooling system is a basic concept, but how you attach the workpiece to the pallet or carrier can take some thought,” he said. Methods include using bolts, magnets, vises and custom fixtures.
The Nano Precision clamping system from System3R
offers pneumatic clamping, accuracy within 0.001mm
and workpiece weight capacity of up to 50kg.
Image courtesy System 3R.
Stevens pointed out another benefit to workholding standardization and palletization: a common interface to automated part handling systems. When shops get overloaded, he explained, the knee-jerk reaction is to buy and staff another machine. Implementing a workholding system like Erowa 's in combination with a robot allows shops to maximize the productivity of the machines they already own, for a fraction of the cost, Stevens said.
Automation, however, takes a shopwide workholding strategy and substantial tooling investment. Shops willing to embrace such a strategy can realize productivity gains of 80 percent or more, Stevens noted.
Before reaching that level, shops new to wire EDMing must adopt unfamiliar workholding methods. Existing fixtures must be adapted for EDM-style clamping or replaced entirely. Before buying an EDM, budget accordingly. Because of their accuracy and technical sophistication, EDM workholders might cost 10 to 20 percent of the machine purchase price. Despite the costs, wire EDMing can help an old chipmaking dog learn new tricks.
Related Glossary Terms
- chuck
chuck
Workholding device that affixes to a mill, lathe or drill-press spindle. It holds a tool or workpiece by one end, allowing it to be rotated. May also be fitted to the machine table to hold a workpiece. Two or more adjustable jaws actually hold the tool or part. May be actuated manually, pneumatically, hydraulically or electrically. See collet.
- computer numerical control ( CNC)
computer numerical control ( CNC)
Microprocessor-based controller dedicated to a machine tool that permits the creation or modification of parts. Programmed numerical control activates the machine’s servos and spindle drives and controls the various machining operations. See DNC, direct numerical control; NC, numerical control.
- electrical-discharge machining ( EDM)
electrical-discharge machining ( EDM)
Process that vaporizes conductive materials by controlled application of pulsed electrical current that flows between a workpiece and electrode (tool) in a dielectric fluid. Permits machining shapes to tight accuracies without the internal stresses conventional machining often generates. Useful in diemaking.
- fixture
fixture
Device, often made in-house, that holds a specific workpiece. See jig; modular fixturing.
- gang cutting ( milling)
gang cutting ( milling)
Machining with several cutters mounted on a single arbor, generally for simultaneous cutting.
- machining center
machining center
CNC machine tool capable of drilling, reaming, tapping, milling and boring. Normally comes with an automatic toolchanger. See automatic toolchanger.
- milling
milling
Machining operation in which metal or other material is removed by applying power to a rotating cutter. In vertical milling, the cutting tool is mounted vertically on the spindle. In horizontal milling, the cutting tool is mounted horizontally, either directly on the spindle or on an arbor. Horizontal milling is further broken down into conventional milling, where the cutter rotates opposite the direction of feed, or “up” into the workpiece; and climb milling, where the cutter rotates in the direction of feed, or “down” into the workpiece. Milling operations include plane or surface milling, endmilling, facemilling, angle milling, form milling and profiling.
- turning
turning
Workpiece is held in a chuck, mounted on a face plate or secured between centers and rotated while a cutting tool, normally a single-point tool, is fed into it along its periphery or across its end or face. Takes the form of straight turning (cutting along the periphery of the workpiece); taper turning (creating a taper); step turning (turning different-size diameters on the same work); chamfering (beveling an edge or shoulder); facing (cutting on an end); turning threads (usually external but can be internal); roughing (high-volume metal removal); and finishing (final light cuts). Performed on lathes, turning centers, chucking machines, automatic screw machines and similar machines.